ГОСТ 27580-88 Дуговая сварка алюминия и алюминиевых сплавов в инертных газах. Соединения сварные под острыми и тупыми углами. Основные типы, конструктивные элементы и размеры
Текст ГОСТ 27580-88 Дуговая сварка алюминия и алюминиевых сплавов в инертных газах. Соединения сварные под острыми и тупыми углами. Основные типы, конструктивные элементы и размеры
Цена 10 коп.
ГОСУДАРСТВЕННЫЙ СТАНДАРТ
СОЮЗА ССР
ДУГОВАЯ СВАРКА АЛЮМИНИЯ И АЛЮМИНИЕВЫХ СПЛАВОВ В ИНЕРТНЫХ ГАЗАХ. СОЕДИНЕНИЯ СВАРНЫЕ ПОД ОСТРЫМИ И ТУПЫМИ УГЛАМИ.
ОСНОВНЫЕ ТИПЫ, КОНСТРУКТИВНЫЕ ЭЛЕМЕНТЫ
И РАЗМЕРЫ
ГОСТ 27580—88
Издание официальное
ГОСУДАРСТВЕННЫЙ КОМИТЕТ СССР ПО СТАНДАРТАМ
Москва
УДК 621.791.75:006.354 Группа В05
ГОСУДАРСТВЕННЫЙ СТАНДАРТ СОЮЗА ССР
ДУГОВАЯ СВАРКА АЛЮМИНИЯ И АЛЮМИНИЕВЫХ СПЛАВОВ В ИНЕРТНЫХ ГАЗАХ.
СОЕДИНЕНИЯ СВАРНЫЕ ПОД-ОСТРЫМИ
И ТУПЫМИ УГЛАМИ. ГОСТ
Основные типы, конструктивные элементы и размеры
27580—88
Arc welding of aluminium and aluminium alloys in inert gases. Acute and blunt weld joints.
Main types, design elements and dimensions
ОКСТУ 0072
Срок действия с 0l.0t.89
до 01.01.94
Несоблюдение стандарта преследуется по закону
1. Настоящий стандарт распространяется на сварные соединения из алюминия и алюминиевых сплавов при толщине кромок свариваемых деталей от 0,8 до 60,0 мм включительно и устанавливает основные типы сварных соединений, конструктивные элементы и размеры разделки кромок и сварного шва, выполненных дуговой сваркой в инертных газах.
Стандарт не распространяется на сварные соединения трубопроводов.
2. В стандарте приняты следующие условные обозначения способов дуговой сварки в инертных газах:
РИНП — ручная неплавящнмся электродом с присадочным металлом;
АИНП — автоматическая неплавящнмся электродом с присадочным металлом;
АИНПЗ— автоматическая неплавящнмся электродом с присадочным металлом — трехфазная;
АИП — автоматическая плавящимся электродом — однодуговая;
ПИП — полуавтоматическая плавящимся электродом.
3. Основные типы сварных соединений должны соответствовать указанным в табл. 1.
4. Конструктивные элементы и их размеры должны соответствовать указанным в табл. 2—19.
Издание официальное
★
Перепечатка воспрещена
© Издательство стандартов, 1988
Таблица 1
№
S
X
OJ
X
fs
s
о
о
с
я
и
О)
о
D3
О
ч
с-
Форма
подготов
ленных
кромок
Характер
сварного
шва
Форма поперечного сечения подготовленных кромок и выполненного шва
Без скоса кромок
Односто
ронний
Односторонний на подкладке
Толщина свариваемых деталей, мм, для способов сварки
а X S D, | И X 5 < | » и X X < | ПИП | АИП |
1 О О | I о °^со о | — | 4—12 | 4—12 |
0. | 0.8— 20,0 | — | 4—12 | 4-12 |
0,8— 12,0 | 0,8- 12,0 | 4—12 | 4—12 | |
0.8— 5.0 | 0,8— 16,0 | 5-25 | 3-12 | 3—12 |
Угол соединения деталей 6
<У
X «
Л1 я К
Я <и я О QJ
2» СВ X
Я я к
ц о 3 о
>5 О О
179°—
122°
У1
Г21°—
91°;
89°—31° 30°~5°
179°—
136°
У2
С. 2 ГОСТ 27580—88
Тип соединения
Форма
подготов
ленных
кромок
Характер
сварного
шва
Форма поперечного сечения подготовленных кромок и выполненного шва
си
о
я
о
к
(—I >>
Без скоса
кромок
Со скосом одной кромки
Односто
ронний
Двусто
ронний
Толщина свариваемых деталей, мм, для способов сварки | Угол со | <и я № | ||||
н PC Я а | и X 5 < | п Н PC 5 < | С Я с | Я я < | единения деталей В | я Я К ф я О р* 4> * Я Я Я я я 2 « е( Ч О (U tJO о ЛОО |
2,0— 6,0 | 2,0— 10,0 | 10— 30 | 4-8 | 4-12 | 179°- 91° | УЗ |
2,0- 6,0 | 2,0— 6,0 | 4-12 | 4-12 | 89°—60° | ||
4,0- 20,0 | — | — | 6,0— 20,0 | — | 179°— 1;22° | У4 |
4,0- 20,0 | 4,0— 20,0 | 4,0- 20,0 | 4,0- 20,0 | 89°—32° | ||
4—20 | 6-20 | 179°- 122° | У5 | |||
4—20 | 4—20 | 4-20 | 4—20 | 89°—60° |
ГОСТ 27580—88 С.
Тип соединения
Форма
подготов
ленных
кромок
Характер
сварного
шва
Форма поперечною сечения подготовленных кромок и выполненного шва
Толщина свариваемых детален мм для способов сварки
к X | Н X | ю п X | а | X |
X | X | X | X | X |
а | < | < | X | < |
Угол со единения деталей 6
<L>
Я К Я S
2 ЕГ (О
«55
ё 2 **
ЙОц|
о
Л О У
о
о
m
о
ч
Е-.
С двумя скосами одной кромки
Со скосом одной кромки
С двумя скосами одной кромки и одним скосом второй кромки
Двусто
ронний
Односторонний на подкладке
Двусто
ронний
12—
35
4-20
12—
30
12-
30
32-
60
12-
35
6-20
12—
30
12-
30
179°-165°; 89°—75е
179°-
136°
179°-
136°
У6
У7
У8
С. 4 ГОСТ 27580—88
ьэ
*
к к X си я | Форма | Характер |
я к | ПОДГОТОВ | |
3 | ленных | сварного |
о о | кромок | шва |
а к Н |
Форма поперечного сечения подготовленных кромок и выполненного шва
Со скосом Одностодвух кромок ронний
а>
о
ей
о
с*.
>>
Двусто
ронний
Толщина свариваемых деталей мм для способов сварки
и X | и X | » в X | X | £ |
£ | X | £ | £ | h—1 Л |
о, | < | < | £ | < |
Угол со
единения
деталей
в
4-20
8-20
10
30
10-
30
179°—
122°
12- 12—
30 30
12—
30
12-
30
89°—61°
4—20
4-40
20-
40
12-
30
10-
30
12—
30
10-
30
12—
30
179°—
122°
89°—61°
<У
S W
к к
X (У ЕЙ о 3* О
я (0 X “MS
g « к
R О ф о
>> О у
У9
У10
tn
ГОСТ 27580—88 С.
1 Тип соединения Г | Форма ПОДГОТОВ’ ленных кромок | Характер сварного шва | Форма поперечного сечения подготовленных кромок и выполненного шва | 1 Толщина свариваемых деталей, мм, Для способов сварки | Угол соединения деталей В | Условное обозначение 1 соединения | ||||
н X X а | н X X < | а а X X < | X X X | X X <! | ||||||
Тавровое 1 | Без скоса кромок | Односто ронний | 1—20 | 2—20 | 3-20 | 3-20 | 3-20 | 91°— 179° | Т1 | |
Двусто ронний | р | 1—20 | 2-30 | 3-20 | 3-20 | 3-20 | 91°— 120° 89°—60° | Т2 | ||
Со скосом одной кромки | Односто ронний | р VV? | 4—20 | 4—20 | 4-20 | 4—20 | 91°— 149° | ТЗ |
6 ГОСТ 27580—88
Тавровое *тип соединения
Форма
подготов
ленных
КРОМОК
Характер
сварного
шва
Со скосом Двусто-одной кром- ронний ки
Односто
ронний
Двусто
ронний
Толщина свариваемых деталей, мм, для способов
Форма поперечного сечения подготовленных кромок и выполненного шва
сварки
в X | в X | « в X | С | £ : |
£ | £ | £ | £ | £ |
а, | С | £ | С |
Угол соединения деталей
в
4—20 4—20
4-20
4-20
91°—
Т4
149°
ГОСТ 27580—88 С.
Тип соединения
Форма
подготов
ленных
кромок
Характер
сварного
шва
Толщина свариваемых деталей, мм, для способов сварки
Форма поперечного сечения подготовленных кромок и выполненного шва
а | н | » а | |
X | X | X | X |
X | S | X | X |
Он | С | < | с |
С
S
<
С двумя скосами одной кромки
Угол соединения деталей
е
91°—
100°
89°—80°
<и
К «
„ я и
£ 0 tq 2 S’ <D
И л щ S я з:
О СП н
ч о 3
«О о о о
Т7
С двумя криволинейными скосами одной кромки
к
и
Е
о
а,
о
t-
о
>,
д
*=(
9 Г— 105°
89°—75°
T9
8 ГОСТ 27580—88
Обозначение
соединения
Конструктивные элементы | |
П0ДГ0Т0ВЛ01ПП 1\ кромок свариваемых деталей | сварного шва |
Способ
Сварки
РИНП; | От | 0,8 |
АИН„ | до | 2,5 |
Сй. | 2,5 | |
до | 6,0 | |
Св. | 6,0 | |
до | 10,0 | |
Св. | 10,0 | |
до | 12,0 | |
Св. | 12,0 | |
до | 20,0 | |
АИП; | От | 4,0 |
ПИП | до | 10,0 |
Св. | 10,0 | |
до | 12,0 |
сё
е, не более при Ц
о | |||||
СМ | о | Л | |||
СМ | о | ||||
* | СТ) 1 | О | ж | ||
1 | со | ю | я | ||
о1 | 1 о | 1 | 1 | S | |
<т> | о | о | о | ||
СМ | СТ) | о | PC | ||
ю | со |
Я
5§
ёё
У1
9
О
+0,5
+1,0
+2,0
+1,0
+2,0
2s+5
2s+5
29+6
2s+5
29+4
2s+4
От 0 до 0,5s
0,8
1,0
2,0
±0,5
±1,0
+2. 0
ГОСТ 27580—88 С.
I. 10 ГОСТ 27580—88
Обозначение
соединения
ГОСТ 27580—88 С. II
Обозначение
соединения
подготовленных кромок свариваемых деталей
сварного шва
Способ
сварки
12 ГОСТ 27580—88
Обозначе! не соединение
Конструктивные элементы
подготовленных кромок свариваемых деталей
СиосиП
сварного шва
сварки
51 ? 0,5s
От | 4 |
ДО | б |
Св | 6 |
ДО | 8 |
Св | 8 |
до | 10 |
Св | 10 |
до | 12 |
Св. | 12 |
до | 20 |
От | 4 |
до | 6 |
От 6 до 10
г пе более
<\±2
при б
С-1
<м
о
с-
о
<о
ф
со
о
О)
о
ч
1. 5S + 6
1.55+8
1.6s 4 10
1,4s 4 6
l,5s+8
l.Cs I 5
1.4S+6
10
13
10
о
£
0 | Ь | ||
н | и | ||
о | о | ||
X | X | ||
X | я | fc{ | |
2 | <У | 2 | <и |
о | а | о | а |
X | С | X | X |
СО.
8~Si
ffi
я
s
о
X
X
H
о
tt
0)
a
К
+i
tt
+i
±2
о
+1
+2
+i
60!
+1
ГОСТ 27580—88 C. 13
Обозначение
соединения
14 ГОСТ 27580—88
<и
Я h»
И й <и Й!
« 5
2 к
* s
о ч
п ® О о
Конструктивные элементы | |
подготовленных кромок свариваемых деталей | сварного шва |
Способ
сварки
не более
ПОИ 3
»л h- | О | fe | о | О Ю СО | о | о £ | о | о iC ю | 9 | |
1C | О | ю | о | 1Л | ||||||
J <л | 7 | оТ -‘t- | 00 1 g | т о СП | к 1 О | т 0 | 00 1 о | 1 о 05 | ь- 1 о | о? (0 О |
t- | 3 | г- | со | СГз | г^ | ю | О) | |||
00 | оо | Г’- | со | г- |
8
О
Ч
g=gi
пои В
СВ. 90° I до 90°
к
я
£
о
X
£ f-
С о
я
я
£
О
X
&£
X о
О | |
я | |
я | ч |
£ | о |
о | (i |
X | С |
+1
-н
л:
■н
ь
От | m |
до | 14 |
Св. | и |
до | 16 |
Св. | 16 |
до | 18 |
Св. | 18 |
до | 20 |
Св. | 20 |
ДО | 22 |
Св. | 22 |
до | 24 |
У6
Si*0,ns
РИН,
СО
+
со
05
»
О
LO
+
со
00
*
О
о
+
со
05
оо
+
со
сч
о
02.
о
5а
о
5а
о
Q2.
I
Ф
Ф
+
е
±1
10
±2
О
+2
±3
60е
8
10
ГОСТ 27580—88 С. 1&
5 к * к
Конструктивные элементы
подготовленных кромок свариваемых деталей
сварного шва
Способ
сварки
Св. | 24 |
ДО | 26 |
С в. | 26 |
до | 28 |
Св. | 28 |
ДО | 30 |
Св. | 30 |
ДО | 32 |
Св. | 32 |
ДО | 35 |
От | 12 |
до | И |
р—ег | е | е\ |
не более |
а,
при В
v
£
0 Ю (D | О | О О | о | О Ю ю | о | <Ь СП |
Ю | 1—1 | О | fH | Ю | ||
| | *г | 1 | 00 1 | | | 1 | |
0 О) | о | о | 1 о | О 05 | 1 о | Св. |
CD | СП | Г- | Ю | а | ||
Г» | 1—1 | 00 | 1-Н |
о
О)
5
8
при В
СВ
90° I до 90°
Я
Я
%
о
а» 5
Со
х
К
Е
о
Е
а* Е о
h-
о
<и
а
К
У6
РИНд
пип
ю
+
to
00
о
о
+
to
О
00
+
со
(N
СО.
о
£
о
оа
еа
о
О)
+
в
±1
+1
—2
10
±3
О
+2
11
12
13
14
60(
16 ГОСТ 27580—88
ГОСТ 27580—88 С. 1>
Обозначение
соединения
Конструктивные элементы
подготовленных кромок свариваемых деталей
сварного шва
Способ
сварки
е=ех | | е | ||||
не более | >i | а2 | ах |
а 1
g=g 1
g
при В
при В
ю | ь | О 1C | о О | о Л | ||||||
h- | с Ю | 0 О | (О *** | ю | г- | ь | СО | 2a | ь | |
т | 00 | т | 00 | 1 | к | 7 | 00 | 7 | h- I | о |
о 03 | о’ | 1 0 | J | о О | 1 О | 0 ■чГ | 1: 0 | % | l 0 | в |
О) 00 | S | со | 79 | г- *■* | 84 | CD | 79 | и |
св. 90° I До 90°
О
Ч
X
S
Е
о
X
$ к
ак
С о
х
%
Е
о
X
а * СЗ о
н
о
«
аз
о
С
■н
в
пип
Св. 26 до 28
11
У6
Св, 28 до 30
Св, 30 до 32
со
+
<0
О
Ю
+
SO
00
о»
+
to
СП
00
+
to
о
£
о
GQ.
о
СО.
со
I
о
+
в
Св. 32 до 35
+i
—2
10
±4
О
+2
12
13
60′
18 ГОСТ 27580—88
Обозначение
соединения
ГОСТ 27580—88 С. 19
ф
3 « 3 я
X
СО
ф
rt к £2 oS
Конструктивные элементы | |
подготовленных кромок свариваемых деталей | сварного шва |
Способ
сварки
hf=h\
±1,5
е=ех
±3
а1
а2=а3
при Й 179е—13)6°
х
S
*
о
К
х
о
Ф
U
С
с
±1
+1
У8
5, г 0. 75
РИН„;
АИНд
ЛИП
11А
От 10 до 14
Св. 14 до 17
Св. 17 до 20
Св. 20 до 23
Св. 23 до 26
Св. 26 до 30
Or 32 до 36
От 36 до 40
10
11
13
11
13
0+5
0,9s+5
0,8s+5
0,60 + 3
о
00
I
о
qClI (N
I
JL
V
8 1 СМ
±1
±2
70‘
12
. 20 ГОСТ 27580—88
Обо:
си
33 Я
sg
0) о и
Конструктивные элементы | |
подготовленных кромок свариваемых деталей | сварного шва |
Способ
сварки
h=h}
±1,5
e=ei
±3
CXi
ПРИ В 179е—136°
ё=ё\
х
я
S
о
X
н
о
«
0)
о
с
с
±1
+1
У8
АИН
пз
АИП;
ПИП
Св. | 15 | 0,6s+3 | |
Св. 44 до 48 | 17 | ||
С в, 48 до 52 | 19 | 0,65 + 5 | |
Св. 52 до 56 | 21 | ||
Св. 56 до 60 | 23 | О | |
От 12 до 14 | 4 | (180—f | |
Св. 14 до 17 | 6 | 0,8s+3 | |
Св. 17 до 20 | 8 | £ | |
Св. 20 до 23 | 9 | ||
Св. 23 до 26 | 10 | 0,7s+4 | |
Св. 126 до 30 | 12 |
аа.
+
в сч
+1
—2
12
70‘
ГОСТ 27580—88 С. 21
. 22 ГОСТ 27580—88
Обозначение
соединения
У10
Конструктивные элементы | |
подготовленных кромок свариваемых деталей | сварного шва |
*5/ ^ Gt7$
к
х
р
а
<а
о
\о
о
о
о
в
О
РИН„
АИНц
От 4 до 8
Св 8 до 10
Св | 10 | ДО | 12 | |
Св | 12 | до | 14 | |
Св | 14 | до | 20 | |
Св. | 20 | до | о со | |
АИНП; | От | 20 | до | 24 |
АИНпз | Св | 24, | до 26 | |
Св | 26 | ДО | 40 | |
АИП; | От | 10 | ДО | 12 |
пип | ||||
Св | 12 | ДО | 14 | |
Св | 14 | до | 24 | |
Св | 24 | ДО | 26 | |
Св. | 26 | ДО | 30 |
е. не более
oti=as
при 3
и
01
(D
О)
оо
1.45 + 5
1.5S + 7
1.

1,5s
+4
1,5s
+2
1,5s
+2
I,4s+2
1,5s
+6
1,5s +4
1,5s
+2
1,5s
+3
о
<31
Ю
U
о
05
о
tr
ex
±2
о
05
в
U
аа_
О
00
04
Ю
СО
QQ-
о
о
04
S3
10
14
15
Н
о
и
flj
о
П
о
+1
+2
,44
я | |
3 | |
н | |
о | |
X | |
S | ы |
£ | о |
о | о |
X | X |
12
8
+1
О
«•н
35′
ГОСТ 27580—88 С. 28
Обо
а
24 ГОСТ 27580
Конструктивные элементы | |||
<и | Способ | ||
сварки | |||
(подготовленных | |||
s* | кромок свариваемых | сварного шва | |
о « | деталей | ||
О о |
РИНп
ГОСТ 27580—88 С. 25
Обозначение
соединения
Конструктивные элементы | |||
Способ | S | ||
подготовленных кромок свариваемых деталей | сварного шва | сварки |
РИН„
От 4 до 10
Св. 10 до 20
тз
От 4 до 10
Св, 10 до 14
Св. 1А до 20
С. 26 ГОСТ 27580—88
Обозначение
соединения
ГОСТ 27580—88 С. 27
Обо
. 28 ГОСТ 27580—88
<и
« ж
я £ о ч
18
О о
Конструктивные элементы
подготовленных кромок свариваемых деталей
сварного шва
Способ
сварки
e=g
Номин.
Пред откл
а.
при 15
о | о | о | О |
Ф | CS | ф | (N |
7 | LO 1 | 1 | |
о1 | 1 □ | 0 | о |
Ф | *■1 | ф | 1—f |
СО | <У> | 00 | О) |
V
8
И
О
v
8
о
Ч
X
X
S
о
К
9
<и
а
Е
Тб
57 £ (7,75
РИНП;
АИНп
АИП;
ПИП
От | 4 до | 6 |
Св. | 4 до | 10 |
Св. | 10 до | 12 |
Св. | 12 до | 18 |
Св. | 18 до | 20 |
От | 4 до | 6 |
От | 6 до | 8 |
От | 8 до | 10 |
Св. | 10 до | 12 |
Св. | 12 до | 18 |
Св. | 18 до | 20 |
10
13
9
10
+3
±2
+4
±3
+5
+3
±2
+4
+5
±3
о
ел
«а.
со.
I
о
О)
О
+1
+2
+1
+2
ГОСТ 27580—88 С. 29
си
** X to*
™ Я
Е ф 2 к
§§
So О о
Конструктивные элементы
подготовленных кромок свариваемых деталей
сварного шва
s
*
а
л
я
о
ю
о
о
о
в
а
е=е, | е | ел |
не более |
От | 12 |
до | 14 |
Св. | 14 |
до | 17 |
Св. | 17 |
до | 20 |
Св. | 20 |
до | 23 |
Св. | 23 |
до | 26 |
Св. | 26 |
до | 30 |
Св. | 30 |
до | 35 |
«1
при В
о Ю | О Ю | О О | О | |
05 I | 00 I | 1 | о® | |
! о | 1 о | 1 о | о | <5 |
1-Н | 05 | СО | со | |
05 | 00 | 05 | СО | ф |
о
00
Tf
00
Св 90(
До 90е
ь | |
0 | |
К | |
X | п |
s | ф |
о | а |
X | ь* top* |
с
±1
а
±1°
Ъс
II
he
РИНП;
АИПп
И
12
13
15
l,4s+5
1Л 5 4-4
1,15 + 2
s+3
1Л5 + 5
1. 25 + 6
1,25+4
l,2s + 6
о
0>
СО.
О
а>
GO.
+
в
о
£
о
О)
СО.
I
О
о>
+
е
О
+2
5±3
60°
. 30 ГОСТ 27580—88
Обозначение
соединения
Конструктивные элементы
подготовленных кромок свариваемых деталей
сварного шва
х
X
а
са m v
О
о
о
о
с
О
От | 12 |
до | 14 |
Св, | 14 |
до | 17 |
Св, | 17 |
до | 20 |
Св. | 20 |
до | 23 |
Св. | 23 |
до | 26 |
Св. | 26 |
до | 30 |
Св. | 30 |
ДО | 35 |
е=е\
е\
не более
пои В
0 | о | |||
о Ю | о ю | о о | ь | О О |
СТ) 1 | 00 1 | т | ОО 1 | Т |
1 о | 1 & | 1 о | 1 О | 1 0 |
05 | СП СО | 96 | 84 | 96 |
Ь
00
00
Св 90й
До 90е
Ъ | |
X | |
ь* | |
О | |
X | |
X | п |
Z | <и |
О | о |
X | С |
€
±1
Ьо
It
Ьс
а
±Г
Т7
АИП;
ПИП
6
8
10
12
14
16
1,4s+ 3
1,15 + 3
Us
s+2
1,2s + 3
his
s + 4
о
O)
CO.
о
О)
СО.
+
о
£
о
05
о
S
I
О
05
+
8
О
+2
5±3
60
ГОСТ 27580—88 С. 31
Обозначение
соединения
. 32 ГОСТ 27580—88
d)
Si
х
QJ
V
Й
В
m
О
\D
О
Конструктивные элементы | ||||
Способ сварки | S | h ±1,5 | ||
подготовленных кромок свариваемых деталей | сварного шва |
T9
ПИП
От 32
до 36
Св 36 до 40
Св. 40 до 44
С в. 44 до 48
Св. 48 до 52
Св. 52 до 56
Св 56 до 60
14
16
18
20
22
24
26
ГОСТ 27580—88 С. 33
5. Кромки свариваемых деталей должны быть обработаны механическим способом, при этом шероховатость обработанной поверхности должна быть не более Rz 40 мкм по ГОСТ 2789—73.
6. Сварка соединений деталей неодинаковой толщины при разнице, не превышающей значений, указанных в табл. 20, должна производиться так же, как для деталей одинаковой толщины. Конструктивные элементы подготовленных кромок и размеры сварного шва следует выбирать по большей толщине.
Таблица /20
мм
Толщина тонкой детали | Разность толщины деталей |
От 0,8 до 3,0 | 0,5 |
Св. 3,0 » 5,0 | 1,0 |
» 5,0 » 12.0 | 1.2 |
» 12,0 » 25,0 | 1.5 |
» 25,0 > 60,0 | 3,0 |
При разнице в толщине свариваемых деталей свыше значений, указанных в табл. 20 на детали, имеющей большую толщину su должен быть сделан скос с одной или двух сторон до толщины тонкой детали s, как указано на черт. 1 и 2.
5
Черт. 1 Черт. 2
При этом конструктивные элементы подготовленных кромок и размеры сварного шва следует выбирать по меньшей толщине. 8 мм;
+4,0 мм при /С>8 мм.
12. Размеры выполненных швов на участке перекрытия для замкнутых соединений, а также в местах, исправленных подваркой, могут отличаться от установленных настоящим стандартом. В этом случае они должны соответствовать нормативно-технической документации.
13. При сварке технического алюминия допускается увеличение размеров швов до 20%.
14. При выполнении двустороннего шва с полным проплавлением перед сваркой с обратной стороны корень шва должен быть расчищен до чистого металла. Расчистка абразивными кругами не допускается.
15. При переменном угле сопряжения деталей р шов делится на участки. Каждый участок сопрягаемых элементов выполняется в соответствии с требованиями настоящего стандарта.
ИНФОРМАЦИОННЫЕ ДАННЫЕ
1. УТВЕРЖДЕН И ВВЕДЕН В ДЕЙСТВИЕ Постановлением Государственного комитета СССР по стандартам от 18.01.88 № 67
2. Введен впервые
3. ССЫЛОЧНЫЕ НОРМАТИВНО-ТЕХНИЧЕСКИЕ ДОКУМЕН-
ТЫ: | |
Обозначение НТД. | Номер пункта |
на который дана ссылка | |
ГОСТ 2789—73 | 5 |
Редактор Р. Г. Говердовская Технический редактор В Н Мальков Корректор В И Баренцева
Сдано в на/б. 10 02 88 Подп к печ 26 04 88 2,5 уел п л 2,68 уел к.р отт 1,59 уч -изд л. Тираж 25 000 экз Цена 10 коп.
Ордена «Знак Почета» Издательство стандартов, 123840, Москва, ГСП, Новопресненский пео . 3 Тип «Московский печатник». Москва. Лялин пер, 6 Зак 1887
ГОСТы по сварке. Все ГОСТы по сварочным технологиям.
В этом разделе Вы можете просмотреть ГОСТы по сварке: способам сварки, сварочному оборудованию и материалам, дефектам и т.д.
Внимание : для Вашего удобства на сайте работает поиск по ГОСТам !
“У человека должен быть здравый смысл, для всего остального есть ГОСТ.”
№ п/п | Название стандарта | Описание |
---|---|---|
1 | ГОСТ EN 1011-6-2017 Сварка. ![]() | Область применения: Настоящий стандарт устанавливает требования для лазерной сварки и связанных с ней процессов обработки металлических материалов для всех видов изделий (например, литых, штампованных, экструдированных, кованых). |
2 | ГОСТ 2246-70 Проволока стальная сварочная. Технические условия. (112 Загрузок) | Настоящий стандарт распространяется на холоднотянутую сварочную проволоку из низкоуглеродистой, легированной и высоколегированной стали. |
3 | ГОСТ 2601-84 Сварка металлов. Термины и определения основных понятий. (183 Загрузки) | Настоящий стандарт устанавливает применяемые в науке, технике и производстве термины и определения основных понятий в области сварки металлов. Термины, установленные стандартом, обязательны для применения в документации всех видов, научно-технической, учебной и справочной литературе. ![]() |
4 | ГОСТ 5264-80 Ручная дуговая сварка. Соединения сварные. Основные типы, конструктивные элементы и размеры. (258 Загрузок) | Настоящий стандарт устанавливает основные типы, конструктивные элементы и размеры сварных соединений из сталей, а также сплавов ни жилезоникелевой и никелевой основах, выполняемых ручной дуговой сваркой. Стандарт не распространяется на сварные соединения стальных трубопроводов по ГОСТ 16037-80. |
5 | ГОСТ 8713-79 Сварка под флюсом. Соединения сварные. Основные типы, конструктивные элементы и размеры. (113 Загрузок) | Название англ.: Flux welding. Welded joints. Main types design elements and dimensions. Область применения: Настоящий стандарт распространяется на соединения из сталей, а также сплавов на железоникелевой и никелевой основах, выполняемых сваркой под флюсом, и устанавливает основные типы, конструктивные элементы и размеры сварных соединений. Стандарт не распространяется на сварные соединения стальных трубопроводов по ГОСТ 16037. |
6 | ГОСТ 10594-80 Оборудование для дуговой, контактной, ультразвуковой сварки и для плазменной обработки. Ряды параметров. (290 Загрузок) | Настоящий стандарт распространяется на оборудование для дуговой, контактной, ультразвуковой сварки и для плазменной обработки (резка, сварка) металлов. Стандарт не распространяется на оборудование бытового назначения. |
7 | ГОСТ 11533-75 Автоматическая и полуавтоматическая дуговая сварка под флюсом. Соединения сварные под острыми и тупыми углами. Основные типы, конструктивные элементы и размеры. (166 Загрузок) | Настоящий стандарт устанавливает основные типы, конструктивные элементы и размеры соединений конструкций из углеродистых и низколегированных сталей, выполняемых автоматической и полуавтоматической дуговой сваркой под флюсом с расположением свариваемых деталей под острыми и тупыми углами. |
8 | ГОСТ 11534-75 Ручная дуговая сварка. ![]() | Настоящий стандарт устанавливает основные типы, конструктивные элементы и размеры сварных соединений конструкций из углеродистых и низколегированных сталей, выполняемых ручной дуговой сваркой плавящимся электродом во всех пространственных положениях при толщине свариваемого металла до 60 мм включительно с расположением свариваемых деталей под острыми и тупыми углами. |
9 | ГОСТ 11969-79 Сварка плавлением. Основные положения и их обозначения. (112 Загрузок) | Настоящий стандарт распространяется на сварные швы, выполняемые сваркой плавлением как в один, так и в несколько слоев, и устанавливает основные положения сварки и их обозначения. |
10 | ГОСТ 14771-76 Дуговая сварка в защитном газе. Соединения сварные. Основные типы, конструктивные элементы и размеры. (208 Загрузок) | Настоящий стандарт устанавливает основные типы, конструктивные элементы и размеры сварных соединений из сталей, а также сплавов на железоникелевой и никелевой основах, выполняемых дуговой сваркой в защитном газе.![]() Стандарт не устанавливает основные типы, конструктивные элементы и размеры сварных соединений стальных трубопроводов по ГОСТ 16037-80. |
11 | ГОСТ 14776-79 Дуговая сварка. Соединения сварные точечные. Основные типы, конструктивные элементы и размеры. (128 Загрузок) | Настоящий стандарт устанавливает основные типы, конструктивные элементы и размеры точечных сварных соединений из сталей, медных, алюминиевых и никелевых сплавов, выполняемых дуговой сваркой. |
12 | ГОСТ 14806-80 Дуговая сварка алюминия и алюминиевых сплавов в инертных газах. Соединения сварные. Основные типы, конструктивные элементы и размеры. (103 Загрузки) | Настоящий стандарт распространяется на сварные соединения из алюминия и алюминиевых сплавов при толщине кромок свариваемых деталей от 0,8 до 60,0 мм включительно. Стандарт не распространяется на сварные соединения трубопроводов. Стандарт устанавливает основные типы сварных соединений, конструктивные элементы и размеры разделки кромок и сварного шва. ![]() |
13 | ГОСТ 15164-78 Электрошлаковая сварка. Соединения сварные. Основные типы, конструктивные элементы и размеры. (74 Загрузки) | Настоящий стандарт устанавливает основные типы, конструктивные элементы и размеры сварных соединений из сталей. Стандарт не устанавливает размер зазора между свариваемыми деталями перед сваркой. Стандарт не распространяется на сварные соединения из коррозионно-стойких сталей. |
14 | ГОСТ 15878-79 Контактная сварка. Соединения сварные. Конструктивные элементы и размеры. (102 Загрузки) | Настоящий стандарт устанавливает конструктивные элементы и размеры расчетных сварных соединений из сталей, сплавов на железоникелевой и никелевой основах, титановых, алюминиевых, магниевых и медных сплавов, выполняемых контактной точечной, рельефной и шовной сваркой. Стандарт не распространяется на сварные соединения, выполняемые контактной сваркой без расплавления металла. |
15 | ГОСТ 16037-80 Соединения сварные стальных трубопроводов. ![]() | Настоящий стандарт распространяется на сварные соединения трубопроводов из сталей и устанавливает основные типы, конструктивные элементы и размеры сварных соединений труб с трубами и арматурой. Стандарт не распространяется на сварные соединения, применяемые для изготовления самих труб из листового или полосового материала. Требования настоящего стандарта являются обязательными. |
16 | ГОСТ 16038-80 Сварка дуговая. Соединения сварные трубопроводов из меди и медно-никелевого сплава. Основные типы, конструктивные элементы и размеры. (62 Загрузки) | Настоящий стандарт устанавливает основные типы, конструктивные элементы и размеры сварных соединений труб с трубами из меди марок М1р, М2р, М3р по ГОСТ 859 и медно-никелевого сплава марки МНЖ 5-1 по ГОСТ 492, с фланцами из латуни марки Л90 по ГОСТ 15527 и со штуцерами и ниппелями из бронзы марок БрАМц 9-2 по ГОСТ 18175 или БрАЖНМц 9-4-4-1.![]() Стандарт не распространяется на сварные соединения, применяемые для изготовления самих труб из листового или полосового материала. |
17 | ГОСТ 19521-74 Сварка металлов. Классификация. (156 Загрузок) | Настоящий стандарт устанавливает классификацию сварки металлов по основным физическим, техническим и технологическим призракам. |
18 | ГОСТ 20549-75 Диффузионная сварка в вакууме рабочих элементов разделительных и формообразующих штампов. Типовой технологический процесс. (52 Загрузки) | Настоящий стандарт устанавливает типовой технологический процесс диффузионной сварки в вакууме вставок из твердых металлокерамических сплавов марок ВК15, ВК20 и ВК25 по ГОСТ 3882-74 с основаниями рабочих элементов разделительных и формообразующих штампов из сталей марок 5ХНВ, 5ХНМ, 5ХНСВ по ГОСТ 5950-73 и марок 38ХН3МФА и 18Х2Н4ВА по ГОСТ 4543-71. |
19 | ГОСТ 23055-78 Контроль неразрушающий. ![]() | Название англ.: Non-destructive testing. Fusion welding of metals. Welds classification by radiography testing results. Настоящий стандарт распространяется на сварные соединения, выполненные сваркой плавлением изделий из металлов и их сплавов с толщиной свариваемых элементов от 1 до 400 мм и устанавливает семь классов сварных соединений по максимальным допустимым размерам пор, шлаковых, вольфрамовых и окисных включений, выявляемых при радиографическом контроле. |
20 | ГОСТ 23338-91 Сварка металлов. Методы определения содержания диффузионного водорода в наплавленном металле и металле шва. (64 Загрузки) | Название англ.: Welding of metals. Methods for determination of diffusible hydrogen in deposited weld metal and fused metal.![]() Настоящий стандарт устанавливает хроматографический и вакуумный методы определения содержания диффузного водорода в наплавленном металле и металле шва и распространяется на покрытые электроды, порошковую проволоку, стальную сварочную проволоку, предназначенные для сварки низкоуглеродистых и низколегированных сталей. |
21 | ГОСТ 23518-79 Дуговая сварка в защитных газах. Соединения сварные под острыми и тупыми углами. Основные типы, конструктивные элементы и размеры. (111 Загрузок) | Название англ.: Gas-shielded arc welding. Welded joints. Main types, design elements and dimensions. Область применения: Настоящий стандарт устанавливает основные типы, конструктивные элементы и размеры сварных соединений из сталей, а также сплавов на железоникелевой и никелевой основах, выполняемых дуговой сваркой в защитных газах. |
22 | ГОСТ 25997-83 Сварка металлов плавлением. Статистическая оценка качества по результатам неразрушающего контроля. ![]() | Название англ.: Fusion welding of metals. Statistical quality evaluation by nondestructive testing results. Область применения: Настоящий стандарт устанавливает правила статистической оценки стабильности статистически управляемых технологических процессов сварки соединений из металлов и их сплавов для изделий массового или серийного производства по результатам неразрушающего контроля. |
23 | ГОСТ 27580-88 Дуговая сварка алюминия и алюминиевых сплавов в инертных газах. Соединения сварные под острыми и тупыми углами. Основные типы, конструктивные элементы и размеры. (68 Загрузок) | Название англ.: Arc welding of aluminium and aluminim alloys in inert gases. Acute and blunt weld joints. Main types, design elements and dimensions. Область применения: Настоящий стандарт распространяется на сварные соединения из алюминия и алюминиевых сплавов при толщине кромок свариваемых деталей от 0,8 до 60,0 мм включительно и устанавливает основные типы сварных соединений, конструктивные элементы и размеры разделки кромок и сварного шва, выполненных дуговой сваркой в инетрных газах. |
24 | ГОСТ 28915-91 Сварка лазерная импульсная. Соединения сварные точечные. Основные типы, конструктивные элементы и размеры. (63 Загрузки) | Название англ.: Laser beam impulse welding. Button welds. Main types, design elements and dimensions. Область применения: Настоящий стандарт устанавливает основные типы, конструктивные элементы и размеры точечных сварных швов соединений из сталей, железоникелевых, никелевых и титановых сплавов, выполняемых импульсной лазерной сваркой твердотельными лазерами. |
25 | ГОСТ 30430-96 Сварка дуговая конструкционных чугунов. Требования к технологическому процессу. (76 Загрузок) | Название англ.: Arc welding of structural cast irons. Requirements for technological process. Область применения: Настоящий стандарт распространяется на технологические процессы ручной и механизированной дуговой сварки, применяемые при исправлении дефектов чугунного литья, восстановлении поврежденных чугунных деталей и создании литосварных изделий из чугуна. |
26 | ГОСТ 30482-97 Сварка сталей электрошлаковая. Требования к технологическому процессу. (60 Загрузок) | Название англ.: Electroslag welding of steels. Requirements for technological process. Область применения: Настоящий стандарт устанавливает требования к технологическому процессу электрошлаковой сварки проволочным электродом или плавящимся мундштуком углеродистых и низколегированных сталей с содержанием легирующих элементов не более 2,5%. Стандарт не распространяется на электрошлаковую сварку пластинчатым электродом. |
27 | ГОСТ 33857-2016 Арматура трубопроводная. Сварка и контроль качества сварных соединений. Технические требования. (90 Загрузок) | Название англ.: Pipeline valves. Welding and quality control of welded joints. Technical requirements. Область применения: Настоящий стандарт распространяется на сварку узлов и конструкций трубопроводной арматуры из стали и железоникелевых сплавов для опасных производственных объектов (ОПО), атомных станций 4-го класса безопасности и других областей применения. |
28 | ГОСТ 34061-2017 Сварка и родственные процессы. Определение содержания водорода в наплавленном металле и металле шва дуговой сварки. (58 Загрузок) | Название англ.: Welding and allied processes. Determination of hydrogen content in deposited metal and arc weld metal. Область применения: Настоящий стандарт устанавливает отбор образцов и аналитическую процедуру определения диффузионного водорода в наплавленном металле и металле шва дуговой сварки с присадочным материалом для сталей мартенситного, бейнитного и ферритного классов |
ГОСТ 14806-80 Дуговая сварка алюминия и алюминиевых сплавов в инертных газах, соединения сварные.
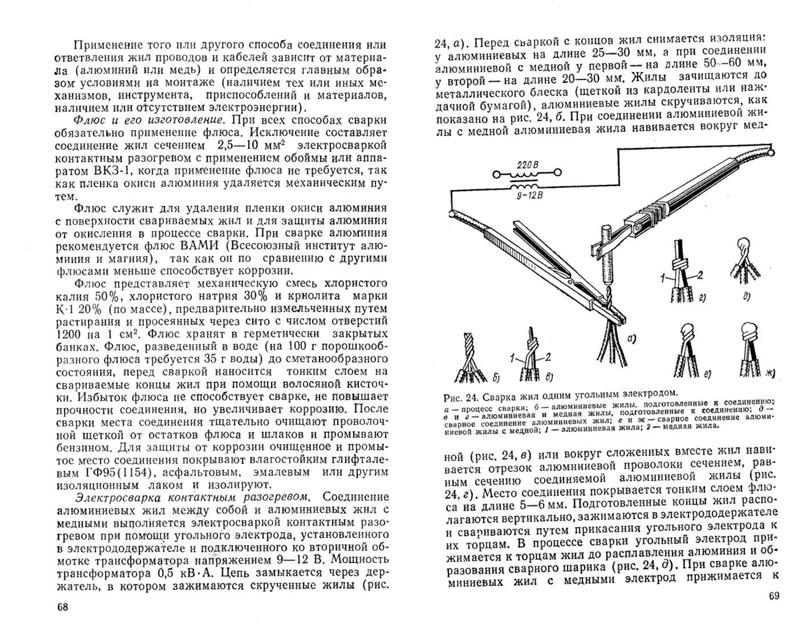
ГОСТ (сокращенное название от Государственный стандарт, Государственный стандарт, ГОСТ) – это одна из важных категорий системы сварочных стандартов в СССР, которая и сейчас является стандартом в современных странах СНГ. Принимается таки органом, как МГС (межгос. советом по стандартизации, метрологии и сертификации.
В период социализма все гос. Стандарты по сварке сохранялись для производства продукции, и имели обязательный характер для использования в тех областях техники, которые определялись сферой возможного использования ГОСТа.
ГОСТы: процессы сварки
ГОСТ 19521-74 Сварка металлов. Классификация
ГОСТ 3.1705-81 Единая система технологической документации. Правила записи операций и переходов. Сварка
ГОСТ 2601-84 Сварка металлов. Термины и определения основных понятий
ГОСТ 11969-79 Сварка плавлением. Основные положения и их обозначения
ГОСТ 29273-92 Свариваемость. Определение
ГОСТ 23870-79 Свариваемость сталей. Метод оценки влияния сварки плавлением на основной металл
ГОСТ 30430-96 Сварка дуговая конструкционных чугунов. Требования к технологическому процессу
ГОСТ 30482-97 Сварка сталей электрошлаковая. Требования к технологическому процессу
ГОСТ 29297-92 Сварка, высокотемпературная и низкотемператупная пайка, пайкосварка металлов. Перечень и условные обозначения процессов
ГОСТ 2.312-72 Единая система конструкторской документации. Условные изображения и обозначения швов сварных соединений.
ГОСТ 20549-75 Диффузионная сварка в вакууме рабочих элементов разделительных и формообразующих штампов. Типовой технологический процесс
ГОСТ Р ИСО 17659-2009 Сварка. Термины многоязычные для сварных соединений.
ГОСТ Р ИСО 857-1-2009 Сварка и родственные процессы. Словарь. Часть 1. Процессы сварки металлов. Термины и определения.
Особенности работы с металлом
Следует знать, что сварка может проводится в ручном, автоматическом либо полуавтоматическом режиме. Работу делают и не применяя присадку, пользуясь только расплавленным металлом с кончиков элементов для сварных швов, что значительно сокращает рабочие затраты. Необходимо учитывать ряд моментов:
пайка вольфрама возможна даже в тех случаях, если толщина элементов менее 0,1 мм;- во время работы воздушные массы должны устраняться с действующей зоны, расход газа зависит от показателя толщины изделия, скорости пайки, типа соединений;
- дуга может поджигаться, не касаясь металла, в таком случае понадобится осциллятор;
- нужно тщательно следить за выбором полярности тока, что позволит уменьшать трату электродов за счет сокращения нагревания металла;
- аргон создает защитный шар, предотвращая окисление и уменьшая использование материалов.
Существует ряд требований относительно работы. Их следует обязательно придерживаться для сохранения высокого качества изделий, в частности:
- следить за точным соблюдением размеров для получения швов высочайшего качества;
- пользоваться определенными приспособлениями, упрощающими сборку;
- обезжирить кончики электродов и обрабатываемые поверхности;
- правильно подбирать силу тока для экономии электродов и сохранения формы их заточек;
- не забывать вытеснять воздух из зоны работ;
- если используются инертные защитные газы, нужно постоянно следить, чтобы газовое облако закрывало не только сварную ванну, но и электрод с кончиком разогретой проволоки;
- при ускорении сваривания должна возрасти и скорость подачи инертных газов.
Ручная методика имеет ряд особенностей. Работы выполняются справа налево. Если сваривают самые тонкие компоненты, то горелку нужно держать под углом 60 градусов, если более толстые — 90 градусов. При выборе методики установки присадки учитывают толщину изделий.
У автоматического и полуавтоматического режимов также имеются особенности. Так, направление работы должно помогать перемещению присадочного прутка в передней части дуги. Электроды размещают в перпендикулярном положении к сварочным поверхностям, а присадка и проволока — под углом 90 градусов.
Сварка вольфрамовыми электродами
Трансформаторы выступают главными источниками питания, когда используется переменный ток, генераторы и выпрямители — если постоянный. У всех источников должна быть крутопадающая характеристика, которая поддержит постоянную величину напряжения, если нарушена длина дуги из-за перепадов.
Относительно того, что варят вольфрамовыми электродами. Такой тип сваривания используют при работе с молибденом, никелем, титаном и высоколегированными сталями. Источник высокой температуры — ток.
Компоненты — специальный электрод и газ аргон, то есть процесс происходит уже в защищенной среде, что приводит к улучшению характеристик сварочных швов, упрощая саму работу и делая ее более эффективной.
ГОСТ: сварка под флюсом
ГОСТ 8713-79 Сварка под флюсом. Соединения сварные. Основные типы, конструктивные элементы и размеры
ГОСТ 11533-75 Автоматическая и полуавтоматическая дуговая сварка под флюсом. Соединения сварные под острыми и тупыми углами. Основные типы, конструктивные элементы и размеры
гост сварка +в среде защитных газов
ГОСТ 14771-76 Дуговая сварка в защитном газе. Соединения сварные. Основные типы, конструктивные элементы и размеры
ГОСТ 23518-79 Дуговая сварка в защитных газах. Соединения сварные под острыми и тупыми углами. Основные типы, конструктивные элементы и размеры
Способы газоэлектрической сварки алюминия
Газоэлектрическую сварку алюминия и его сплавов выполняют неплавящимся (вольфрамовым) или плавящимся электродом.
При сварке неплавящимся электродом источником тепла является дуга, возбуждаемая между электродом и изделием.
Конец электрода, дуга и ванна расплавленного металла защищены инертным газом. Основным рабочим инструментом является специальная сварочная горелка, которая служит для крепления электрода и подвода сварочного тока к нему. Поток защитного газа формируется и направляется в сторону сварочной ванны наконечником горелки.
Сварку алюминия и его сплавов неплавящимся электродом в среде защитных газов производят переменным током. Для повышения устойчивости горения дуги используют специальные вспомогательные аппараты (осцилляторы и импульсные возбудители). Осцилляторы применяют также для облегчения возбуждения дуги. Сварку неплавящимся электродом можно выполнять без присадки, когда шов формируется путем расплавления свариваемых кромок, и с присадкой, когда в формировании шва участвует присадочный металл, подаваемый со стороны в зону дуги.
Дуговую сварку в среде защитных газов неплавящимся электродом можно выполнять вручную, полуавтоматом или автоматом. При ручной сварке перемещение горелки и подачу присадочной проволоки в зону дуги выполняет сварщик. При полуавтоматической сварке перемещение горелки вдоль шва осуществляется вручную, а подача присадочной проволоки — специальным механизмом. При автоматической сварке перемещение горелки и подача присадочной проволоки осуществляются механически.
Сварка неплавящимся электродом алюминия и его сплавов применяется преимущественно для соединения изделий малых и средних толщин.
Дуговая сварка неплавящимся вольфрамовым электродом в среде защитных газов является наиболее универсальным способом сварки. Этим способом можно выполнять сварку в различных пространственных положениях и в труднодоступных местах.
Формирование шва наилучшее. При сварке алюминия вольфрамовым электродом можно получать металл шва плотным, мало насыщенным газами. При этом достигается высокая прочность и пластичность сварных соединений, близкие к прочности и пластичности основного металла. Сварку неплавящимся электродом в среде защитных газов рекомендуется применять для ответственных соединений, требующих высокого качества, герметичности и прочности. Сварка неплавящимся электродом может производиться одной, двумя и. тремя дугами.
При двухдуговой сварке с растянутой ванной создаются благоприятные условия для предупреждения образования пор и обеспечиваются необходимые качества сварных соединений.
Этот способ сварки отличается стабильностью режимов.
Трехфазная дуга является одним из наиболее мощных концентрированных источников тепла, ее мощность более чем в 2 раза превышает мощность однофазной дуги при том же токе и напряжении. Важным преимуществом трехфазной дуги по сравнению с однофазной является ее высокая устойчивость.
При сварке трехфазной дугой постоянно горит, по крайней мере, одна дуга, поэтому на осциллограмме не наблюдается значительных пиков зажигания и нулевых площадок тока.
Применение сварки трехфазной дугой дает увеличение производительности труда и позволяет снизить расход электроэнергии на 25—40%. При сварке трехфазной дугой обеспечивается равномерность загрузки фаз питающей сети, что дает возможность во много раз повысить мощность сварочного поста. Коэффициент мощности достигает 0,8.
Однако сварку трехфазной дугой применяют мало из-за сложности оборудования и неудобства в работе.
При сварке плавящимся электродом источником тепла является дуга, возбуждаемая между свариваемым изделием и электродной проволокой, непрерывно подаваемой в зону дуги с заданной скоростью. Электродная проволока подается механизмом подачи с постоянной или переменной скоростью.
Для направления электродной проволоки, подведения к ней тока и подачи в зону сварки защитного газа применяют специальные сварочные горелки.
Дуговую сварку в среде защитных газов плавящимся электродом можно выполнять с помощью полуавтоматов и автоматов. Полуавтоматическая и автоматическая сварка плавящимся электродом в защитных газах осуществляется на постоянном токе обратной полярности. Источники питания сварочной дуги должны иметь жесткую, полого возрастающую или полого падающую внешнюю характеристику. Сварку плавящимся электродом алюминия и его сплавов применяют для соединения изделий средних и больших толщин.
Основными преимуществами механизированной сварки плавящимся электродом являются высокая производительность и простота ведения процесса. При сварке плавящимся электродом в среде защитных газов благодаря высокой степени концентрации источника тепла обеспечиваются наименьшие сварочные деформации, а также более глубокое проплавление основного металла по сравнению со сваркой неплавящимся электродом. Плавящийся электрод позволяет получить хорошее проплавление корня шва при сварке тавровых и нахлесточных соединений.
К недостаткам этого способа относятся большая вероятность получения непровара по глубине в начале сварки, когда невозможно применить выводные пластины; трудность предотвращения образования пор в сварных швах. Последний недостаток устраняется при использовании способа импульсно-дуговой сварки плавящимся электродом в среде защитных газов. Этот способ разработан в ИЭС им. Е. О. Патона.
При импульсно-дуговой сварке обеспечивается струйный перенос металла в широком диапазоне режимов сварки.
Управление переносом электродного металла позволяет выполнять сварку плавящимся электродом во всех пространственных положениях без разбрызгивания с хорошим формированием сварного шва. При этом универсальность полуавтоматической сварки плавящимся электродом приближается к универсальности ручной дуговой сварки неплавящимся электродом. Импульсно-дуговой сваркой можно успешно сваривать детали небольшой толщины. При сварке импульсной дугой по сравнению со сваркой стационарной дугой значительно уменьшается пористость металла шва, несколько возрастает прочность сварных соединений. Схема включения импульсного генератора в сварочную цепь приведена на рис. 1.
Рис. 1. Схема включения в сварочную цепь импульсного генератора: СГ — сварочный генератор; ГИ — генератор импульсов; В — полупроводниковый вентиль.
В последнее время разрабатывается и уже находит применение в промышленности способ плазменной сварки сжатой дугой алюминия на переменном токе. По сравнению с обычной дуговой сваркой неплавящимся электродом сварка сжатой дугой производится на повышенных скоростях, при этом снижается расход защитного газа, электроэнергии и присадочной проволоки. При этом способе сварки обеспечивается высокая стабильность горения и устойчивость дуги, снижается величина тепловложения, сужается зона термического влияния и уменьшаются деформации.
В ИЭС им. Е. О Патона разработан способ микроплазменной сварки, позволяющий сваривать алюминиевые листы толщиной 0,05—0,8 мм. Обычная аргоно-дуговая сварка неплавящимся электродом для соединения такого материала непригодна из-за прожогов и провисания металла шва. При микроплазменной сварке в качестве плазмообразующего газа используется аргон, в качестве защитного — гелий.
Микроплазменную сварку можно выполнять вручную и автоматически, с присадочной проволокой и без нее. При сварке тонколистового алюминия наилучшие результаты получены в стыковых соединениях с отбортовкой кромок и бортовых.
Гост: сварка алюминия
ГОСТ 14806-80 Дуговая сварка алюминия и алюминиевых сплавов в инертных газах. Соединения сварные. Основные типы, конструктивные элементы и размеры
ГОСТ 27580-88 Дуговая сварка алюминия и алюминиевых сплавов в инертных газах. Соединения сварные под острыми и тупыми углами. Основные типы, конструктивные элементы и размеры
гост точечная сварка
ГОСТ 14776-79 Дуговая сварка. Соединения сварные точечные. Основные типы, конструктивные элементы и размеры
ГОСТ 28915-91 Сварка лазерная импульсная. Соединения сварные точечные. Основные типы, конструктивные элементы и размеры
Отклонение от размеров швов
В случае проведения сварных работ в положении, которое отличается от нижнего, то величина шва может быть увеличена. Но допустимые отклонения по ГОСТу не могут превышать 2 мм для деталей до 25 мм и 3 мм – свыше 25 мм.
В случае если в качестве инертного газа используется гелий, а работы производятся на постоянном токе, то размеры шва могут быть уменьшены до 15%.
Для стыковых соединений допустимо уменьшение размера до 1-2 мм, тавровых и угловых соединений – до 1 мм. При нахлесточных соединениях сварной шов не может выступать над поверхностью более, чем на 1 мм.
В случае сварки технического алюминия швы могут быть увеличены до 20%.
Если выполняется двухсторонний шов с полным проплавлением перед сварочными работами с обратной стороны, то корень шва расчищается до чистого металла. Не допускается использование абразивных кругов.
Таким образом, применение ГОСТ 14806-80 является обязательным при выполнении работ по сварке алюминия и его сплавов с толщиной 0,8-60 мм, если сварочный процесс производится методом дуговой сварки в среде инертных газов. Здесь приведены типы швов, конструктивные элементы, допустимые отклонения швов от заданных параметров и пр.
ГОСТ: cварка трубопроводов
ГОСТ 16037-80 Соединения сварные стальных трубопроводов. Основные типы, конструктивные элементы и размеры
ГОСТ 16038-80 Сварка дуговая. Соединения сварные трубопроводов из меди и медно-никелевого сплава. Основные типы, конструктивные элементы и размеры
ГОСТ 16310-80 Соединения сварные из полиэтилена, полипропилена и винипласта. Основные типы, конструктивные элементы и размеры
ГОСТ 15164-78 Электрошлаковая сварка. Соединения сварные. Основные типы, конструктивные элементы и размеры
ГОСТ 15878-79 Контактная сварка. Соединения сварные. Конструктивные элементы и размеры
ГОСТ 16098-80 Соединения сварные из двухслойной коррозионностойкой стали. Основные типы, конструктивные элементы и размеры
ГОСТ 16310-80 Соединения сварные из полиэтилена, полипропилена и винипласта. Основные типы, конструктивные элементы и размеры.
ГОСТ 16130-90 Проволока и прутки из меди и сплавов на медной основе сварочные. Технические условия
Советы
Наилучшим вариантом для вольфрамовых электродов аргонодуговой сварки является работа на постоянном токе прямой полярности. Особое внимание необходимо уделить заточке кончика прутка. Рекомендуется уделить внимание другим моментам:
- В процессе заточки не стоит усердствовать. Материал может перегреться и стать хрупким. Дальнейшее его использование будет вряд ли возможно, он просто раскрошится;
- Важно следить за качеством подаваемого газа.
Объемная доля качественного аргона достигает 99,9 %. Если его качество низкое, это сразу станет заметно по потемневшему шву. Необходимо будет провести регулировку с помощью оборудования на баллоне;
- Важно наладить оптимальную силу тока, чтобы избежать эрозии наконечника прутка. Затупление или образование большой капли приведет к недолговечности электрода, пропуску участков расплавления, сквозным прожогам материала;
- Для получения качественного шва сварку проводят справа налево. Горелка удерживается в правой руке, а присадочная проволока — в левой.
В ряде случаев может применяться переменный ток. Сварка аргоном на переменном токе не столь требовательна к форме кончика прутка. Здесь важно просто подготовить электрод к сварке, придав кончику полукруглую форму. А вот к поверхностям, которые потребуется сварить, сварка на переменном токе очень чувствительна. Особенно это касается алюминия. Основное условие получения ровных сварных швов без непроваренных участков — очистка и тщательное удаление жировых следов с поверхности.
Используемая литература и источники:
- ГОСТ 23949-80 Электроды вольфрамовые сварочные неплавящиеся. Технические условия
- Cary, Howard B. & Helzer, Scott C. (2005), Modern welding technology, Upper Saddle River, New Jersey: Pearson Education
- Watkins, Arthur D. & Mizia, Ronald E, Optimizing long-term stainless steel closure weld integrity in DOE standard spent nuclear canisters, ASM International
ГОСТы: сварочные материалы
ГОСТ Р ЕН 13479-2010 Материалы сварочные. Общие требования к присадочным материалам и флюсам для сварки металлов плавлением
ГОСТ Р 53689-2009 Материалы сварочные. Технические условия поставки присадочных материалов. Вид продукции, размеры, допуски и маркировка
ГОСТ 7871-75 Проволока сварочная из алюминия и алюминиевых сплавов. Технические условия
ГОСТ 9466-75 Электроды покрытые металлические для ручной дуговой сварки сталей и наплавки. Классификация и общие технические условия
ГОСТ Р ИСО 2560-2009 Материалы сварочные. Электроды покрытые для ручной дуговой сварки нелегированных и мелкозернистых сталей. Классификация
ГОСТ Р ИСО 3580-2009 Материалы сварочные. Электроды покрытые для ручной дуговой сварки жаропрочных сталей. Классификация
ГОСТ Р ИСО 3581-2009 Материалы сварочные. Электроды покрытые для ручной дуговой сварки коррозионно-стойких и жаростойких сталей. Классификация
ГОСТ 2246-70 Проволока стальная сварочная. Технические условия
Процесс сварки вольфрамовым электродом
При выполнении сварочных работ в качестве электрода применяется вольфрамовый стержень, температура плавления которого выше температуры, до которой он нагревает свариваемые детали. Работы ведутся в среде ограждающего газа для защиты шва и электрода от воздействий внешней среды, чаще всего применяют аргон, гелий и некоторые их смеси. Вольфрамовые электроды используют для сварки цветных металлов (Вольфрамовые электроды WT-20) и высоколегированных сталей. Необходимо отметить, что при задействовании вольфрамового электрода можно достичь получения отличного сверхпрочного сварного шва, причем свариваемые модули могут быть неоднородного химического состава.
Сам процесс сварки происходит следующим образом: вольфрамовый электрод заключен в токопроводящем устройстве горелки и окружен керамическим соплом. Благодаря электрической дуге на стыке свариваемых металлических деталей образуется цельная расплавленная ванна. Аргон подается по токопроводящему приспособлению, вытесняя кислород. Электрическая дуга при этом сжата и собрана на очень небольшой поверхности, благодаря чему в зоне плавления достигается температура от 4000 до 6000 °C. Подобный вид сварки предусматривает подачу в дугу присадочного материала — присадочной поволоки для усиления шва.
Сварной шов получается целостным со свариваемыми элементами, это залог гарантии высокого уровня надежности и длительной эксплуатации продукта (вольфрамовые электроды WL-20). При дуговой сварке чаще всего применяется аргон, но при сварке алюминия, толщина которого меньше 1/4 дюйма, применяется смесь с гелием. Делается это для того, чтобы добиться необходимой теплопроводности. В редких случаях при помощи аргонно-гелиевых смесей зажигают дугу, после чего сварку проводят исключительно с гелием. Подобный прием используют, когда нужно сварить толстолистовой алюминий при постоянном токе. Стыкуя для сварки металл толщиной до 10 мм, работы ведутся справа налево. Если толщина меньше 10 мм, то угол между соплом аппарата и рабочим материалом должен быть 60 градусов. Металлы с большей толщиной сваривают под углом 90 градусов. При работе с автоматической и полуавтоматической сваркой вольфрамовый электрод должен находиться под углом 90 градусов, при этом присадочный пруток располагается впереди дуги.
Несмотря на относительно низкую степень износчивости, на вольфрамовом электроде со временем появляются наросты окислов, которые еще называют коронками. Эти наслоения ведут к тому, что электрическая дуга начинает блуждать по сварочной поверхности. Образования наростов можно предотвратить, если интенсивно охлаждать электрод, и вероятность образования «коронки» уменьшается, если максимально повысить газовую защиту.
Если вы выбрали правильный режим сварки, то боковая поверхность и конец электрода должны блестеть. Мутная поверхность говорит о том, что тепловая нагрузка на электрод превышает рекомендуемую.
Проверить надлежащий расход аргона достаточно просто: если после сварочных работ электрод имеет зеленоватый, сизый или черный налет, это означает, что расход аргона небольшой, или после отключения дуги затрачено мало времени для продувки аргона.
Вольфрамовые стержни следует затачивать твердыми мелкозернистыми дисками для того, чтобы не допустить образования бороздок и выступов на электроде.
Получить более полную информацию о сварочных материалах и особенностях всех типов сварочных работ вы можете в Инженерно-техническом . Мы долго и упорно изучали сварочное дело для того, чтобы помочь вам в возведении самых смелых строительных конструкций.
Подобрать нужный вольфрам можно вот тут
Технология аргонодуговой сварки неплавящимся электродом
Дуга горит между свариваемым изделием и неплавящимся электродом (как правило, для электрода используется вольфрам). Электрод расположен в горелке, через сопло которой вдувается защитный газ (как правило, аргон). Присадочный материал в электрическую цепь не включён и подаётся в зону дуги со стороны.
Сварка может быть ручной, когда горелка и присадочный пруток находятся в руках сварщика, и автоматической, когда горелка и присадочная проволока перемещаются без непосредственного участия сварщика.
При способе сварки неплавящимся электродом зажигание дуги не может быть выполнено путём касания электродом изделия по двум причинам.
Во-первых, аргон обладает достаточно высоким потенциалом ионизации, поэтому ионизировать дуговой промежуток за счёт искры между изделием и электродом достаточно сложно. При аргонодуговой сварке плавящимся электродом после того, как проволока коснётся изделия, в зоне дуги появляются пары железа, которые имеют потенциал ионизации в 2,5 раза ниже, чем аргона, что позволяет зажечь дугу.
Во-вторых, касание изделия вольфрамовым электродом приводит к его загрязнению и интенсивному оплавлению. Поэтому при аргонодуговой сварке неплавящимся электродом для зажигания дуги параллельно источнику питания подключается устройство, которое называется «осциллятор».
Осциллятор — устройство, предназначенное для бесконтактного возбуждения электрической дуги и стабилизации горения дуги при сварке малыми токами.
Для зажигания дуги осциллятор подаёт на электрод высокочастотные высоковольтные импульсы, которые ионизируют дуговой промежуток и обеспечивают зажигание дуги после включения сварочного тока. Если сварка производится на переменном токе, осциллятор после зажигания дуги переходит в режим стабилизатора и обеспечивает подачу импульсов на дугу в момент смены полярности, чтобы предотвратить деионизацию дугового промежутка и обеспечить устойчивое горение дуги.
Деионизация — процесс исчезновения положительных и/или отрицательных ионов, а также электронов из занимаемого газом объёма. Является обратным процессу ионизации и обычно происходит после прекращения электрического разряда в газе.
При сварке на постоянном токе на аноде и катоде выделяется неодинаковое количество тепла. При токах до 300А 70% тепла выделяется на аноде и 30% на катоде, поэтому практически всегда используется прямая полярность, чтобы максимально проплавлять изделие и минимально разогревать электрод. Все стали, титан и другие материалы, за исключением алюминия, свариваются на прямой полярности. Алюминий обычно сваривается на переменном токе для улучшения разрушения оксидной пленки.
Для улучшения борьбы с пористостью к аргону иногда добавляют кислород в количестве 3-5%. При этом защита металла становится более активной. Чистый аргон не защищает металл от загрязнений, влаги и других включений, попавших в зону сварки из свариваемых кромок или присадочного металла. Кислород же, вступая в химические реакции с вредными примесями, обеспечивает их выгорание или превращение в соединения, всплывающие на поверхность сварочной ванны, что предотвращает пористость шва.
Сварщик по классификации алюминиевых сплавов
Промышленные деформируемые алюминиевые сплавы делятся на семь серий. Есть еще восемь — сплавов, не попавших в первую семерку и девятую — резервную. Разница между партиями заключается в разных основных легирующих элементах. Различные легирующие элементы придают различные свойства алюминиевым сплавам.
Сварка чистого алюминия
Серия сплавов 1ххх называется «Сплав» весьма условно. Это высокочистые варианты технически чистого алюминия. ГОСТ 4784 так и называет их: «алюминиевые марки». Однако железо часто является не только примесью, но и легирующим элементом — оно повышает прочность алюминия. Предел прочности сплавов этой серии составляет от 70 до 150 МПа. Они сварные, хотя из-за узкого интервала затвердевания требуют особой технологии сварки. Их высокая коррозионная стойкость делает их пригодными для использования в химических резервуарах и трубопроводах. Из-за их высокой электропроводности используется для изготовления шинопроводов. Эти алюминиевые сплавы обладают относительно низкими прочностными характеристиками и поэтому редко используются для конструкционных элементов. Чаще всего это сварка сварочных материалов с одинаковым химическим составом или сварка алюминиевых сплавов серии 4ххх в зависимости от назначения изделия и условий его эксплуатации.
сварка дюралюминия
серия 2ххх. Это серия термически упрочняемых алюминиевых сплавов. Их предел прочности при растяжении от 190 до 430 МПа. Они содержат меди от 0,7 до 6,8 %. Эти высокопрочные сплавы часто используются в аэрокосмической и авиационной технике. Они сохраняют высокую прочность в широком диапазоне температур.
Большинство из них не считаются свариваемыми дуговой сваркой из-за их склонности к горячему растрескиванию и коррозии под напряжением. Однако в этой серии есть специально разработанные хорошо свариваемые дугой алюминиевые сплавы 2219.(наш Д20) и 2519. К ним часто приваривают свариваемый высокопрочный сплав 2319. Иногда, в зависимости от условий эксплуатации сварного шва, применяют для сварки алюминиевые сплавы из серии 4ххх, содержащие кремний или кремний в сочетании с медью.
Сварка алюминиево-марганцевых сплавов
серия 3ххх. Сплавы алюминиевые серии — нетермоупрочненные до предела прочности при растяжении от 110 до 280 МПа. Основной легирующий элемент — марганец, от 0,05 до 1,8 %. Они обладают умеренной прочностью, хорошей коррозионной стойкостью, хорошей формуемостью и пригодны для эксплуатации при повышенных температурах. В последние годы нам нравилось делать посуду. Сейчас они являются основным материалом для изготовления теплообменников автомобилей, химических заводов и электростанций. Их скромные прочностные характеристики делают их непригодными для конструкционных применений. Алюминиевые сплавы серии 3ххх сваривают сварочными сплавами серий 1ххх, 4ххх и 5ххх в зависимости от их химического состава, условий применения и эксплуатации.
Сварка алюминиевых сплавов
серия 4XXX. Эта серия состоит из как термически упрочняемых, так и термически неупрочняемых алюминиевых сплавов. Прочность на растяжение – от 170 до 380 МПа. Они содержат кремния от 0,6 до 21,5 %. Кремний снижает температуру плавления и увеличивает текучесть материала при плавлении. Эти свойства весьма благоприятны для них как материалов для сварки плавлением и пайки. Кремний, когда он сам по себе, делает алюминий термически неупрочняемым, однако добавки магния или меди делают его термически упрочняемым сплавом. Обычно эти термически упрочняемые сплавы применяют только для сварки, когда сварную конструкцию после сварки необходимо подвергнуть термической обработке.
Сварка алюминиево-магниевых сплавов
Серия 5ххх. Термически неупрочняемые алюминиевые сплавы этой серии имеют предел прочности при растяжении от 125 до 350 МПа. Они содержат магния от 0,2 до 6,2 %. Эти сплавы обладают самой высокой прочностью среди неупрочняемых сплавов и хорошо свариваются термически. Они широко применяются в виде листов и плит для судостроения, транспортного машиностроения, при изготовлении сосудов высокого давления, строительстве мостов и зданий. Алюминиевые сплавы с содержанием магния до 2,5 % чаще всего успешно свариваются сваркой алюминиевых сплавов серий 5ххх и 4ххх. Сплав 5052 (сплав АМг2,5 по ГОСТ 4784) обычно считается предельным по содержанию магния, когда можно сваривать сварочный сплав серии 4ххх. Это связано со снижением механических свойств сварных швов вследствие эвтектического подплавления. Поэтому сплавы с повышенным содержанием магния не свариваются сплавами серии 4ххх, а сплавами серии 5ххх с близким химическим составом.
Сварочные сплавы магний-алюминий-кремний
серия 6ххх. Эти термически упрочняемые алюминиевые сплавы имеют предел прочности при растяжении от 125 до 400 МПа. Они содержат небольшое количество магния и кремния – около 1 % каждого. Сплавы серии 6ххх широко применяются в сварных строительных конструкциях, преимущественно в виде штампованных профилей. Эти алюминиевые сплавы склонны к горячему растрескиванию во время затвердевания сварного шва. Поэтому их не сваривают без присадочной проволоки или сварочной проволоки. Сварочный сплав смешивается в сварочной ванне со свариваемым сплавом и предотвращает горячее растрескивание сварного шва. Сплавы 6ххх сваривают как при сварке сплавов 4ххх, так и при сварке сплавов 5ххх в зависимости от назначения свариваемого изделия и условий его применения.
Сварка высокопрочных алюминиевых сплавов
серия 7ххх. Данная серия включает термически упрочняемые алюминиевые сплавы с пределом прочности от 220 до 610 МПа. Основным легирующим элементом является цинк в количестве от 0,8 до 12,0 %. К этому ряду относятся самые прочные алюминиевые сплавы. Сплавы серии 7ххх применяются в авиационной, космической технике, спортивном инвентаре. Как и в серии 2ххх, большинство сплавов этой серии не считаются свариваемыми дуговой сваркой. Однако он имеет и хорошо свариваемые сплавы, как, например, сплав 7005 (сплав 1915 ГОСТ 4784), который приваривается к основным сварочным сплавам серии 5ххх.
Источник: Т. Андерсон, www.thefabricator. com
Какие алюминиевые сплавы лучше всего подходят для сварки?
Алюминий и его сплавы чрезвычайно популярны для широкого спектра применений. Тем не менее, существует распространенное заблуждение, что алюминий не может быть эффективно соединен с помощью обычных процессов сварки, как стальные сплавы.
Многие люди думают, что у них нет другого выбора, кроме как соединить алюминиевые детали с помощью механических застежек, таких как заклепки, но на самом деле все сложнее. Есть некоторые нюансы, когда речь идет о сварке алюминия.
В этой статье вы получите общее представление о том, насколько поддаются сварке алюминий и его сплавы. Вы также узнаете о методах сварки и о шести лучших алюминиевых сплавах для сварки. Эта информация поможет вам определить, можно ли сваривать алюминиевое изделие.
Содержание
Насколько алюминий поддается сварке?
Квадратные алюминиевые профили, вваренные в раму
Вообще говоря, способность алюминия к сварке (свариваемость) варьируется в зависимости от серии сплавов. Он может варьироваться от «очень хорошо» до «не поддается сварке обычными методами дуговой сварки». Тем не менее, большинство алюминиевых сплавов можно сваривать в правильных условиях и при соблюдении надлежащих мер предосторожности.
Из-за его физических и химических свойств методы сварки алюминия отличаются от других металлов. Таким образом, эту практику должны выполнять только профессионалы, специально обученные сварке алюминия.
В частности, сварка алюминия усложняется двумя свойствами.
- Оксидный слой на его поверхности
- Теплопроводность алюминия
Давайте поговорим о каждом из этих свойств.
Оксидный слой
Одной из мер предосторожности, которую должны соблюдать сварщики при работе с алюминием, является подготовка или очистка поверхности, которую они собираются сваривать. Алюминий естественным образом образует на своей поверхности слой оксида, что вызывает проблемы.
Этот оксидный слой устойчив к коррозии — желательное качество в большинстве случаев — но материал твердый. Его температура плавления почти в три раза выше, чем у алюминия. Таким образом, если оксид алюминия не будет полностью удален, он может создать загрязнения в соединении, что приведет к пористости и трещинам.
Теплопроводность
Следует также помнить, что алюминий имеет гораздо более высокую теплопроводность, чем сталь. И хотя его температура плавления ниже, чем у стали, вам нужно приложить больше тепловой энергии к сварному шву.
Одним из способов борьбы с высокой теплопроводностью в некоторых соединениях является предварительный нагрев алюминия. Опытные сварщики делают это, чтобы предотвратить прожоги на более тонких алюминиевых участках и на более толстых материалах, чтобы обеспечить достаточное проплавление сварного шва.
Методы сварки алюминия
Человек, использующий сварочный аппарат TIG для изготовления алюминиевой рамы
Лучший метод сварки конкретного алюминиевого изделия зависит от различных факторов. Это может быть толщина материала, назначение детали и свариваемые сплавы.
Вообще говоря, двумя наиболее распространенными методами сварки алюминия являются сварка в среде инертного газа (MIG) и сварка вольфрамовым электродом в среде инертного газа (TIG). Для этих процедур обученный специалист должен подобрать соответствующий состав присадочного металла. Они будут принимать во внимание различные факторы, такие как:
- Свариваемость основного металла
- Требования к механическим свойствам
- Коррозионная стойкость
- Анодирующие покрытия
Существуют таблицы, помогающие выбрать соответствующие присадочные металлы для многих алюминиевых сплавов.
Сварка трением с перемешиванием (FSW) — это еще один тип сварки, который можно использовать в некоторых случаях для создания очень высокопрочных сварных швов. В отличие от методов дуговой сварки, которые мы упоминали, он включает использование высокоскоростного вращающегося цилиндрического инструмента для размягчения и смешивания алюминия.
К сожалению, СТП может не подходить для всех случаев, так как требует специальной настройки оборудования и позволяет сваривать только стыковые соединения.
Для сварки алюминия можно использовать несколько других методов сварки, например лазерную сварку (LBW). Однако в большинстве отраслей они менее распространены.
Свариваемость различных серий сплавов
Квадратные экструдированные алюминиевые трубы
Хотя свариваемость различных алюминиевых сплавов различается, вы можете определенно увидеть закономерности в их свариваемости, которые различаются в зависимости от их основных легирующих элементов или серий марок.
Сплавы серий 2XXX и 7XXX обладают очень высокой прочностью и часто используются в аэрокосмической и авиационной промышленности. Но эти сплавы иногда называют «несвариваемыми».
Большинство сплавов этой серии чрезвычайно склонны к горячему растрескиванию из-за содержания в них меди или цинка. Однако термин «несвариваемый» вводит в заблуждение, поскольку некоторые из этих сплавов действительно можно сваривать. Но сварщик должен принять особые меры предосторожности, чтобы обеспечить хорошее качество сварки.
Сплавы, принадлежащие к серии 6XXX, обладают хорошей свариваемостью, если используются соответствующие методы для предотвращения их склонности к растрескиванию. Они не такие прочные, как сплавы 2ХХХ и 7ХХХ, но обладают другими превосходными физическими свойствами. Сплавы серии 6XXX часто используются в сварочных работах, несмотря на трудности.
Сплавы серии 4XXX обычно используются в качестве присадочного материала для сварки других алюминиевых сплавов, включая сплавы серии 6XXX. Содержание в них кремния значительно снижает их температуру плавления и позволяет им улавливать некоторые легирующие компоненты других термообрабатываемых сплавов.
Наконец, оставшиеся сплавы серий 1XXX, 3XXX и 5XXX обычно демонстрируют свариваемость от хорошей до отличной, хотя только сплавы серии 5XXX обычно используются для применений, требующих структурной целостности.
6 Распространенные алюминиевые сплавы для сварки
В следующей таблице показаны некоторые наиболее часто свариваемые алюминиевые сплавы.
Обозначение сплава | Преимущества | Недостатки | Общие приложения |
---|---|---|---|
3003 | Очень популярный сплав общего назначения. Отличная формуемость и свариваемость | Не особенно сильный. | Обработка листового металла, штамповка, топливные баки, кухонная утварь, электроника. |
5052 | Прочнее, чем 3003. Хорошая свариваемость и отличная коррозионная стойкость. | Не подлежит термообработке. | Сосуды под давлением, резервуары, гидравлические трубки, приборы, морское оборудование. |
5083 | Высокая эффективность сварки и очень высокая прочность соединения. Хорошая коррозионная стойкость. | Не подлежит термообработке. | Буровые установки, резервуары и морские компоненты, криогенные установки.![]() |
5454 | Прочность от умеренной до высокой, отличная свариваемость. | Не рекомендуется для облицовки. | Применения в условиях высоких температур, например, для перевозки автоцистерн с горячим асфальтом и самосвальных кузовов, а также для некоторых емкостей для хранения химикатов, таких как перекись водорода. |
6061 | Хороший универсальный сплав. | Не лучший рейтинг в какой-либо конкретной области. | Конструкционные и сварные узлы, вагоны, трубопроводы, самолеты, автозапчасти. |
6063 | Средняя прочность и хорошая коррозионная стойкость, свариваемость и обрабатываемость. | Плохая обрабатываемость. | Прессованные детали, такие как перила из труб, мебель, архитектурное, медицинское оборудование. |
Вывод: можно ли сваривать мой алюминиевый продукт?
Роботизированный сварочный аппарат
Если процесс формирования требует сварки вашего алюминиевого изделия, есть большая вероятность, что вы сможете это сделать! За некоторыми исключениями, такими как многие представители серий 2XXX и 7XXX, алюминиевые изделия можно соединять с помощью соответствующих методов сварки.
В дополнение к ручной сварке вы также можете использовать роботизированную сварку для своего проекта. Роботизированная сварка обеспечивает более высокую точность сварки, согласованность и большую производительность. В Gabrian мы используем роботизированные сварочные установки для некоторых наших клиентов, занимающихся экструзией алюминия.
Если вам нужна помощь в изготовлении вашего следующего изделия из алюминия или требуется помощь в обработке, свяжитесь с нашей командой специалистов по обслуживанию. Вы также можете ознакомиться с нашими линиями алюминиевого проката и изделий из экструдированного алюминия, чтобы узнать, как мы можем удовлетворить ваши производственные потребности.
алюминиевый фланец с патрубком ГОСТ
Алюминий Алюминиевый лист/плита Алюминий Алюминиевая труба/трубка Алюминий Алюминиевый стержень/пруток Медь Медный лист/плита Медь Медная труба/трубкаМуфта для шланга Википедия
Муфта для шланга — это соединитель на конце шланга для соединения или соединения его с другим шлангом, краном или устройством для шланга, таким как спринклер для орошения. Обычно это …
ТоварыAcero Tubos,Tuberias,Tubi,Gost 8732,API 5L,API 5CT …
Алюминий Латунь SS Guillemin Coupling middot CRA CLAD Труба middot Grayloc Clamp Connector Glok middot Алюминиевый сплав Venne Perolo middot SCM444 Сталь 42CrMo. ..
Фланцевые фитинги для трубных усилителей Сантехника The Home Depot
Результаты 1 24 из 58 … Получите бесплатную доставку квалифицированных фланцевых фитингов для трубных усилителей или купите онлайн … Фланец для туалета с втулкой из ПВХ с тестовой крышкой и нержавеющей сталью Звенеть.
Алюминиевые фланцы и фланцы из нержавеющей стали Купить Перила
Купите 1000 шт. коммерческих фитингов из алюминия или оцинкованной стали и получите скидку 25 на трубы из алюминия и оцинкованной стали. Скидка составит…
Алюминиевые фланцы MSC Industrial Supply
Труба 8 кв.