Советы по проектированию реперных знаков для печатных плат
Следующие пункты призваны осветить общие вопросы по проектированию и размещению специальных
поверочных меток на поверхности печатной платы, более известных как реперные знаки. Советы
придерживаются правил проектирования, стандартизированных Ассоциацией производителей, использующих
технологию поверхностного монтажа плат ( Surface Mount Equipment Manufacturers Association ) и
поддерживаемых IPC.
Реперные знаки являются одним из элементов разводки печатной платы, создаваемых одновременно с разводкой самой платы.
(Структура платы и реперных знаков должны вытравливаться в одно и то же время)
Реперные знаки обеспечивают общие точки, которые могут быть распознаны и обмеряны на всех этапах процесса сборки печатной платы. Это позволяет любому сборочному оборудованию точно распознавать расположение рисунка печатной платы.
Реперные знаки разбиты по следующим типам:
- Общие реперные знаки:
Реперные знаки, используемые для обнаружения всех элементов на конкретной печатной плате. Когда мультиплицированные платы обрабатываются как единая панель, общие реперные знаки могут также располагаться вместе с реперных знаками цельной панели. В таком случае они используются для обнаружения конкретных плат на данной панели.(См. Рис. 1 и 2)
- Локальные ( местные ) реперные знаки:
Реперный знак (или знаки) используемый для обнаружения позиции конкретной группы контактных площадок на плате или компонента, что бывает необходимо для более точной установки таких компонентов, как QFP с шагом от 0,5 мм.
- Реперные знаки, содержащиеся в изображении печатной платы:
Общие реперные знаки на мультиплицированной панели печатных плат, расположенные в пределах периметра конечных печатных плат ( т.е. плат, получаемых после разрезки панели ).
- Реперные знаки панели печатных плат:
Общие реперные знаки на мультиплицированной панели печатных плат, расположенные по внешней стороне периметра конечных печатных плат. (См. Рис.2 )
Обрезаемые краевые реперные знаки.
Общие реперные знаки
Общие и/или панельные реперные знаки должны, в идеале, быть расположены в узлах трех-точечной сеточной системы, левый нижний угол которой имеет координаты точки 0,0, а остальные две точки которой находятся на положительных осях в X и Y направлениях.
Общие реперные знаки должны располагаться на всех слоях печатной платы, которые содержат
компоненты, монтируемые автоматическим оборудованием.
Это остается верным и тогда, когда печатная плата не содержит компонентов с мелким шагом (
менее 0,5 мм.), так как большая часть современного оборудования для монтажа использует распознавание
реперных знаков для выравнивания печатных плат в процессе производства. Использование других
объектов на печатной плате ( сквозные отверстия , и.т.д.) вместо реперных знаков может снизить
точность установки компонентов.
Сдвиги:
Минимум два общих реперных знака смогут обеспечить при необходимости корректировку печатной платы при сдвиге ( оси X и Y ) и повороте ( ось Тета ). Такие общие реперные знаки должны быть расположены диагонально, на максимально возможном удалении друг от друга.на печатной плате или панели.
Нелинейные искажения:
Минимум три реперных знака смогут обеспечить при необходимости корректировку нелинейных
искажений, таких как нарушение масштаба, вытягивание или сдвиг рисунка печатной платы.
Подобные реперные знаки должны быть расположены по треугольной схеме и располагаться как можно
дальше друг от друга на печатной плате или панели.
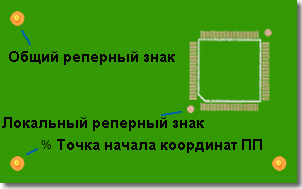
Рис.1 Общие и локальные реперные знаки
Локальные (местные) реперные знакиРеперный знак ( или знаки ) используемые для обнаружения позиции конкретной группы контактных площадок или компонента, что может быть необходимо при точной установке таких компонентов как QFP с шагом от 0,5 мм.
Поступательные сдвиги:
Один или более реперных знаков смогут обеспечить при необходимости корректировку поступательных сдвигов ( по осям X и Y). Подобные реперные знаки располагаются внутри периметра группы контактных площадок, преимущественно в ее центре.
Если имеются ограничения по месту на печатной плате, можно использовать как минимум один локальный реперный знак для корректировки поступательных сдвигов. В таком случае он располагается в центре группы контактных площадок.
Реперные знаки панели:
Три реперных знака смогут обеспечить при необходимости корректировку поступательных и вращательных
сдвигов для всей панели мультиплицированных печатных плат.
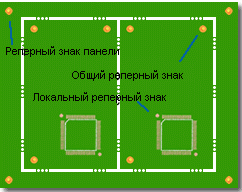
Рис. 2 Реперные знаки панели
Минимальный рекомендуемый размер для реперного знака это 1 мм.
Признак хорошего тона делать реперные знаки одного размера, поскольку некоторое сборочное
оборудование не настолько гибко способно перенастраиваться для распознавания реперных знаков
различного размера.на одной и той же печатной плате.
Форма:
Существует несколько общепринятых форм. Некоторые говорят, что оптимальным реперным знаком является сплошной залитый круг.

Рис.3 Общепринятые формы реперных знаков
Размер:
Минимальный диаметр реперного знака должен быть 1мм (0.040 дюйма).
Максимальный диаметр реперного знака должен быть 3мм (0.120 дюйма).
Реперные знаки на одной печатной плате не должны отличаться в размерах более чем на 25 микрон
(0.001 дюйма).
Свободная область вокруг реперного знака:
Вокруг реперных знаков должна быть обеспечена область, свободная от любых других элементов
печатной платы или каких-либо маркировок.
Размер свободной области должен быть эквивалентен радиусу реперного знака. Предпочтительно
делать свободную область вокруг реперного знака равным диаметру знака.

Рис.4 Свободная зона, вокруг реперного знака
Свободная область на краю печатной платы:
Расстояние от реперного знака, до края печатной платы или панели не должно быть менее чем сумма значений 4.75 мм [0.187 дюймов] ( ширина области на краю печатной платы для транспортировки ее в устройствах, оборудованных конвейерами по стандарту SMEMA) и радиусом свободной области вокруг реперного знака.
Базовый материал:
Предпочтительный базовым материалом является неизолированный или неизолированный, покрытый
медью материал, защищенный анти-окислительным покрытием..
Это также может быть материал, покрытый никелем или оловом или с нанесенным паяльным припоем
(HASL).
Для оптимальной проиводительности оборудования должна быть обеспечена высокая степень контрастности между поверхностью реперного знака и соседней областью базового материала печатной платы.
Толщина покрытия:
Для нормального использования толщина покрытия неизолированного, покрытого медью материала,
должна быть от 5 до 10 микрон [0.0002 до 0.0004 дюймов].
Толщина паяльного покрытия никогда не должна превышать 25 микрон [0.001 дюйма].
Плоскостность:
Плоскостность поверхности реперного знака должна быть в пределах 15 микрон (0.0006 дюйма).
Контактные площадки компонентов:
Реперные знаки должны использоваться совместно с контактными площадками компонентов, которые проектируются с учетом требований IPC-SM-782.
Правильная подготовка проекта под автоматический монтаж печатных плат
Применяемое оборудование позволяет размещать компоненты с минимальным расстоянием друг от друга 0,2 мм, а от края платы — 1 мм (при условии наличия технологических полей на заготовке). Но использование максимальных технических возможностей не всегда оправдано. Например, слишком близкое размещение компонентов очень сильно снижает ремонтопригодность изделия, оптическую инспекцию компонентов, проверку паяных соединений. Близкое расположение компонентов, разных по размерам и теплоемкости может сказываться на качестве пайки.
Кроме того, важно учитывать, что размеры корпусов многих компонентов выходят за размеры контактных площадок, поэтому при создании графики компонентов желательно прорисовывать их реальные габариты или зону, занимаемую компонентом, с учетом пространства, необходимого для инспекции и ремонта. Это поможет правильному размещению компонентов и позволит избежать ошибок.
Рекомендуемые зазоры: 0,6…0,8 мм между чип-компонентами; 1 мм — между чип-компонентами и крупными элементами платы и 1,2…1,5 мм — между микросхемами и крупными компонентами, и 1,5 мм между SMD и выводными компонентами (см. рис.1).
Ориентация компонентов не имеет значения, т. к. на нашем предприятии метод пайки волной припоя не применяется.
Располагать SMD-компоненты на обеих сторонах печатной платы стоит только в том случае, если габариты самой платы, всевозможные ограничения на зазоры между проводниками, контактными площадками и другими элементами платы и прочие требования не оставляют выбора. В этом случае увеличивается затраты и время на подготовку и монтаж (изделие дважды проходит стадию монтажа, для него дважды пишутся программы на оборудование, дважды происходит его переналадка, изготавливается два трафарета, стоимость монтажа каждой стороны платы рассчитывается как за отдельное изделие). Кроме того, значительно возрастает стоимость тестового оборудования для проверки таких печатных плат.
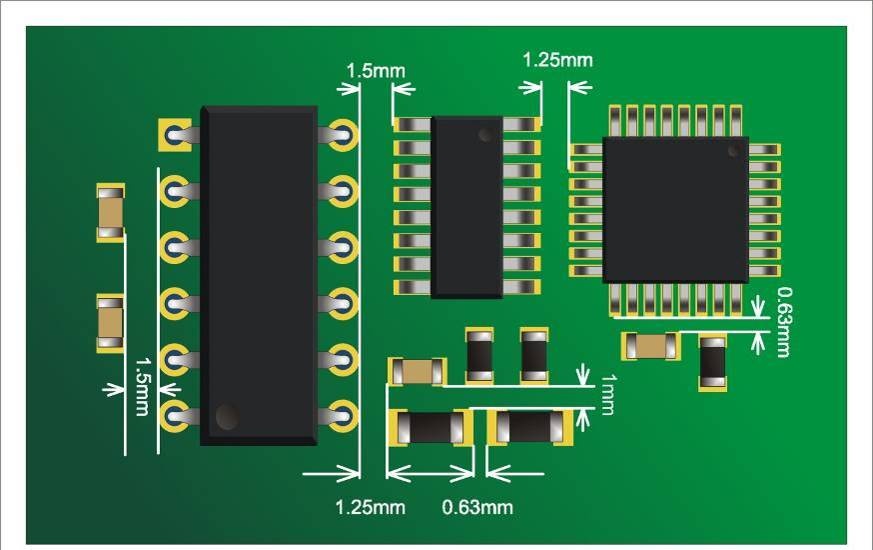
Рис. 1. Расстояние между компонентами
В том случае, если одностороннее размещение компонентов невозможно, рекомендуется небольшие, например, пассивные, компоненты разместить на одной стороне платы, а микросхемы и другие «тяжелые» компоненты — на другой стороне.
На рисунке ниже приведена классификация размещения элементов на сторонах печатной платы по IPC.
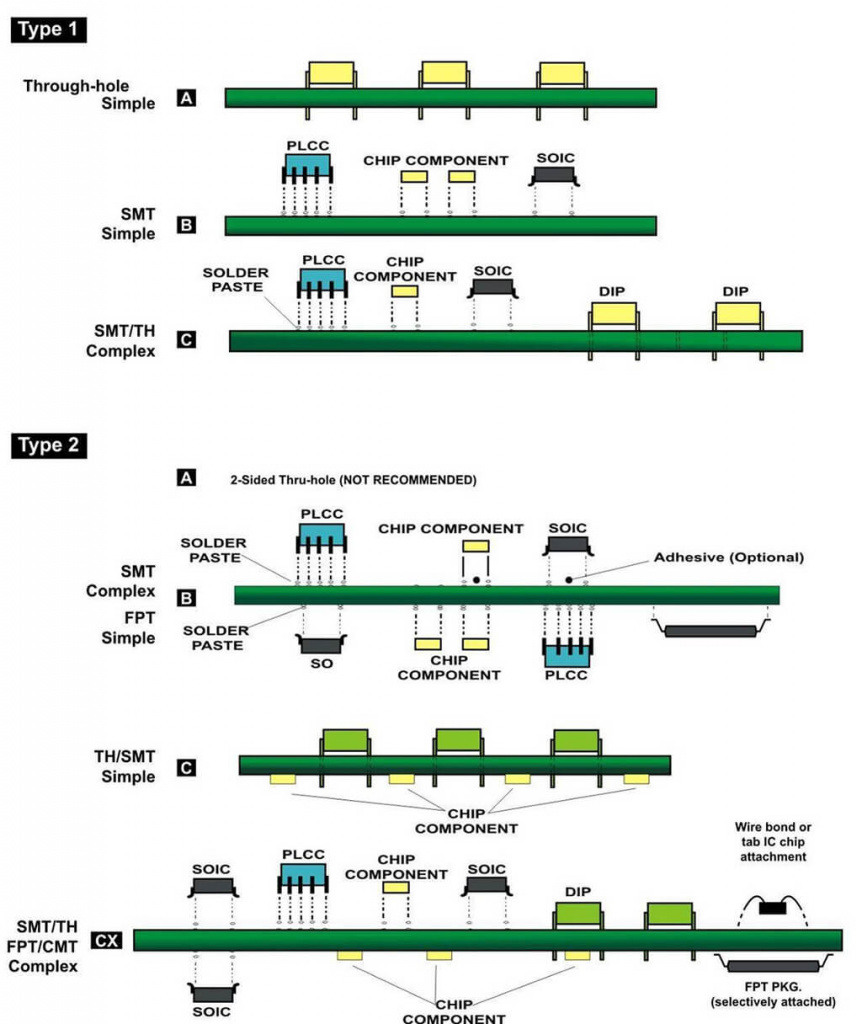
Рис. 2. Расположение типов элементов по сторонам
Проектирование печатных плат — часто задаваемые вопросы
Во многом качество SMD-монтажа обеспечивается ещё на этапе проектирования печатного узла. Для того, чтобы снизить вероятность возникновения каких-либо проблем при монтаже, и, как следствие, вероятность брака, и, соответственно, уменьшить себестоимость изделия за счет стоимости монтажа, необходимо учитывать требования предприятия производящего монтаж. Их соблюдение позволит получить наиболее полную отдачу от тех преимуществ, которые заключает в себе технология поверхностного монтажа.
В этом разделе размещена информация, посвященная тем вопросам разработки, которые непосредственно отражаются на качестве и процессе монтажа. Некоторые из приведенных здесь сведений носят общий характер, и применимы к любому производству. Они основаны на рекомендациях и стандартах таких организаций как IPC или JEDEC. Некоторые были получены нашими специалистами на основе собственного опыта работы с нашим оборудованием. В любом случае, применение изложенной здесь информации на практике поможет сделать процесс монтажа Ваших изделий на нашем предприятии более качественным, быстрым и эффективным.
Общая конструкция плат и мультиплицированных заготовок
Одно- и двусторонние платы
Некоторые разработчики, не раздумывая, спешат располагать SMD компоненты на обеих сторонах печатной платы. В этом случае изделие дважды проходит стадию монтажа, для него дважды пишутся программы на оборудование, дважды происходит его переналадка, изготавливается два трафарета и т.д. Это стоит делать только в том случае, если габариты самой платы, всевозможные ограничения на зазоры между проводниками, контактными площадками и другими элементами платы, и прочие требования не оставляют выбора. Помните, что стоимость монтажа каждой стороны платы рассчитывается как за отдельное изделие, а во-вторых, на монтаж двусторонних плат существует коэффициент наценки. И это относится к абсолютному большинству предприятий, занимающихся монтажом. Кроме того, значительно возрастает стоимость тестового оборудования для проверки самих печатных плат.
Размеры плат и групповых заготовок
Допустимые размеры печатного узла или мультиплицированной заготовки, состоящей из нескольких одинаковых плат, зависят от параметров оборудования, на котором будет производиться сборка. Для оборудования, которое применяет наша фирма, эти размеры должны находиться в диапазоне от 50Х50мм до 320X250мм (в отдельных случаях максимальный размер может превышать указанные параметры, но это необходимо согласовать с нашими технологами). При этом желательно выдержать соотношение длины к ширине групповой заготовки примерно 3 к 2.
Технологические поля
Наше оборудование позволяет производить монтаж отдельных плат или групповых заготовок, не имеющих специальных технологических отверстий и полей для фиксации платы на сборочном оборудовании. Но при этом необходимо учитывать, что хотя бы по одной из длинных сторон платы компоненты должны быть расположены не ближе, чем 3 мм от края как минимум! Причем, если поверхностно-монтируемые элементы размещены с обеих сторон платы, это правило должно соблюдаться и для второй стороны. В противном случае, по длинным сторонам платы или мультизаготовки необходимо разместить технологические поля, шириной 3-5мм.
Разделение заготовок на платы
Для разделения плат между собой и технологическими полями существует два метода: скрабирование и фрезеровка по контуру платы. В первом случае по прямым линиям раздела плат и полей наносятся надрезы, которые оставляют в этих местах перемычку, размер которой определяет как жесткость всей заготовки в целом, так и легкость ее последующего разделения.
Реперные метки
На каждой плате необходимо предусмотреть наличие желательно 4-х (минимум 2-х) реперных меток, необходимых для системы технического зрения установщиков. Они должны располагаться по углам платы и быть максимально удалены друг от друга.
Реперные метки должны представлять собой круглые площадки, диаметром 1мм, вскрытые от маски в диаметре 3,5-4 мм. Желательно, что бы проводники, контактные площадки, переходные, крепежные отверстия и другие элементы печатной платы располагались не ближе 5 мм к реперным меткам.
Контактные площадки
Чтобы избежать перетекание припоя, произвольное смещение компонентов и другие нежелательные эффекты во время пайки, нельзя допускать расположение переходных отверстий на контактных площадках элементов или в непосредственной близости от них. Необходимо, чтобы контактные площадки компонентов были отделены от переходных отверстий, других контактных площадок и т.д. паяльной маской. Подобное правило очень важно для микросхем с малым шагом выводов – их контактные площадки обязательно должны быть разделены маской.
Элементы, расположенные внутри полигонов, должны быть отделены от них термобарьерами. Это позволит избежать неравномерного прогрева разных контактных площадок одного и того же компонента во время пайки и, как следствие, смещение этого компонента, эффекта «надгробного камня» и т. д.
Одним из наиболее важных моментов при проектировании печатных узлов является соблюдение форм и размеров контактных площадок. Именно несоответствие этих параметров зачастую приводит к возникновению таких нежелательных явлений как эффект «надгробного камня», непропаи одного из выводов компонента, слишком большое смещение элемента и т. д.
Опять же, здесь невозможно привести параметры контактных площадок для всех типов корпусов. Поэтому мы рекомендуем сверять эти параметры с данными производителей компонентов и стандартами IPC (IPC-7351A – «Общие требования по конструированию контактных площадок и печатных плат с применением технологии поверхностного монтажа»), а так же обращаться к специалистам нашей фирмы, перед тем, как отправить проект печатной платы на изготовление.
Установщик SMD-деталей на платы (Pick and Place) TVM802B-X, часть 2
¥25300.00 / ≈$3700 / 254189 руб (плюс 37547 руб доставка)Это вторая и последняя часть обзора. Целиком он не влез в одну публикацию из-за ограничения на объем текста в обзоре 🙂
Первая часть тут — mysku.ru/blog/taobao/66376.html
В этой части я опишу процесс подготовки файлов для станка и работу с программой софта.
Интерфейс я описал в первой части уже с высоты моего опыта работы с этим станком, показал опыт первого запуска, а теперь немного расскажу как я по незнанию промучился несколько часов с настройкой и как поимел очень много геморвозни после того как решил улучшить станок 🙂
Спрячу этот рассказ под спойлер
Наигравшись вдоволь с тестовой платой и потратив метров 5 из ленты резисторов 0603, я решил попробовать скормить станку нормальную плату. Подготовив файл, открыл его в программе станка, настроил параметры компонентов и запустил исполнение программы. А среди прочих там были две микросхемы с шагом выводов 0.5мм, для них я поставил в параметрах «Точная коррекция по камере». То есть станок берет микросхему, несет ее к нижней камере, там по изображению вносит коррекцию по точному положению и углу и потом ставит на плату.И вот тут случилось неприятное — после коррекции станок поставил микросхему под каким-то непонятным углом, да еще и со смещением почти в сантиметр. Пробую еще раз — опять так же. Стал выполнять по шагам и увидел, что во время коррекции по камере эта самая камера видит внизу своего поля зрения какой-то мусор и принимает его за часть микросхемы. В результате микросхема определяется станком вот так:
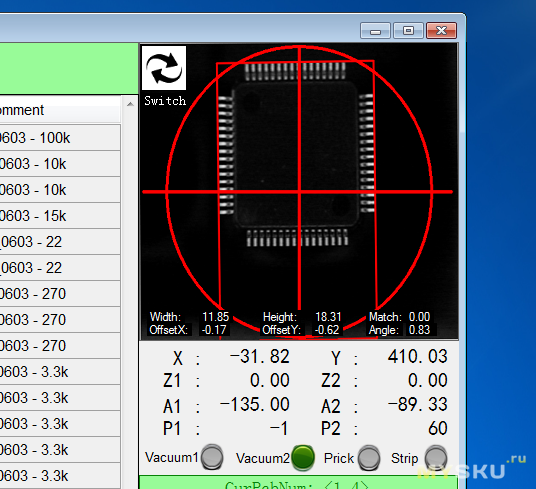
Пробую другую микросхему и вижу то же самое:
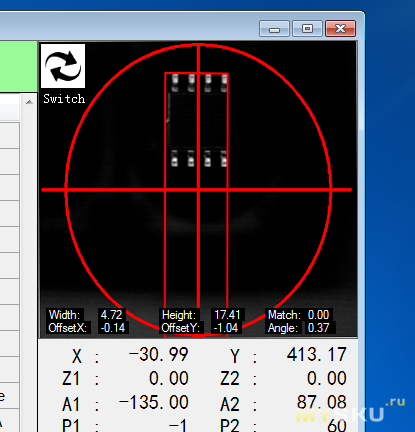
Что за …? Тем более, что мелкие резисторы-транзисторы камера определяет превосходно, никакой мусор ей не мешает.
Не, ну понятно, что какая-то царапина или соринка сбивает камеру с толку, но блин, его же должны были проверять, юстировать?
Часа полтора я пробился с ним, думая, что это что-то программное. Может где-то надо уменьшить яркость подсветки или выдержку камере, но нигде ничего такого в настройках не было. Потом я начал потихоньку разбирать нижнюю камеру, насколько это было возможно малой кровью. Сначала снял защитное стекло, думал на нем царапина или мусор. Не помогло совершенно. Продул, промахнул кисточкой, а потом и протер объектив — ноль изменений. И тогда уже под утро я опять написал гневное письмо в поддержку производителя, приложив скриншоты.
На следующий день, проснувшись в обед я увидел ответ от поддержки, где меня вежливо ткнули носом в нужные настройки. Оказывается за чувствительность определения компонентов нижней камерой отвечает параметр CompThre, который настраивается отдельно для каждой позиции в ленточных питателях и для каждого лотка. Проблема была в том, что для питателей этот параметр уже был по умолчанию настроен на среднее значение 50, а для лотков он по умолчанию стоял в минимальном значении 0. Ну и еще в том, что я просто не знал что это за параметр 🙂
После настройки этого параметра все замечательно заработало 🙂
Второй случай поиметь возни с настройкой станка я создал себе сам. Вздумалось мне подкрутить фокус на верхней камере, чтобы она более четко видела реперные знаки и, соответственно, более точно по ним позиционировалась (хотя, в общем-то, и так все было хорошо, но всегда ведь хочется еще лучше чем есть :)). И не долго думая, я снял с каретки блок с камерой:
Объектив камеры был залит каким-то довольно твердым герметиком, по консистенции как мягкий пластик. Кое-как отковырял его.
Прикрутил обратно блок камеры, подрегулировал фокус и залил объектив по периметру термоклеем, чтобы объектив не болтался и не крутился. Я-то сразу понимал как важно объективу быть зафиксированным, от этого ведь будет зависеть точность определения реперных знаков, а значит и установки компонентов. Но в мою голову не закралось мысли, что после регулировки объектив обязательно встанет не так как он стоял с завода, а значит полетит нафиг вся юстировка сопел, а соответственно и всех позиций в питателях. До меня это дошло только когда я обнаружил несоответствие значений смещения сопел в настройках фактическому положению дел. А после того, как исправил это, отъюстировав смещения сопел, оказалось, что теперь напрочь улетела юстировка всех 46 позиций в обоих питателях 🙂
Приведение всех настроек и калибровок в порядок заняло у меня почти два дня. Дело осложнялось еще и тем, что я тогда не до конца понимал значение всех этих настроечных полей, как они влияют на станок и что будет если изменить какое-то из них, во все пришлось вникать методом проб и ошибок.
Но зато теперь я знаю и понимаю все эти настройки так, как долго бы еще не узнал бы, если бы не пришлось пройти через все это 🙂
Ну и еще одна подстава ждала меня перед уже окончательным приведением установщика в полностью рабочее состояние.
Я вдруг обнаружил, что то одно то другое сопло вдруг начинает брать из питателей (и соответственно ставить на плату) некоторые детали с довольно большим смещением. Первым делом, конечно, полез в юстировку сопел, но все проверки показывали отличный результат — оба сопла попадали точно в центр. Потом попытался заново настроить параметры всех позиций в питателях — вот вроде бы все стало отлично, но при следующей установке опять смещение. Собирался уже писать опять в поддержку производителю, но тут меня посетила дикая мысль — а может сопла кривые? И точно — одно из сопел оказалось кривым 🙂 При его вращении центр сопла не стоял на месте, а выписывал окружность. И так и получалось, что после снятия и установки сопел это кривое попадало то на первую голову то на вторую, соответственно и смещение появлялось то на одной голове то на другой, да еще и его направление зависело от того в каком положении сопло было вставлено. Хорошо, что в комплекте было два мелких сопла, так что кривое я отложил и поставил вместо него другое, ровное 🙂
Уже заказал на Али по паре сопел двух мелких размеров, надеюсь, что их эта проблема минует 🙂
Ну а теперь приступим к работе в софте станка. Сам софт, к сожалению, практически никак не документирован — нет ни нормального мануала (кроме некоего «Быстрого старта»), ни встроенной помощи. Поэтому почти до всего пришлось доходить самому, причем многие моменты я узнал или прояснил для себя в процессе написания этого обзора 🙂
Софт работает с файлами в формате .csv — списки значений, разделенных запятыми. Первая строка в таком файле — названия полей, все последующие строки — значения, по одной записи на строку. Это очень старый и стандартный формат, проблем с ним не должно быть. Кроме как у Excel, который вроде бы и понимает его и экспортировать в него может, только вот почему-то формат «список с разделением запятыми» он экспортирует как «список с разделением точкой с запятой». Победить это можно только зайдя в виндовую Панель управления — Язык и региональные стандарты — Дополнительные параметры и поставив там в поле «Разделитель элементов списка» запятую вместо точки с запятой. После этого можно вполне комфортно работать с файлами .csv в Excel.
В этом файле для программы установщика требуются несколько обязательных полей:
— Designator (можно так же RefDes) — позиционное обозначение компонента, например R12, C6 и т.п.
— MidX (можно так же Center-X или Center-X(mm)) — координата компонента по X.
— MidY (можно так же Center-Y или Center-Y(mm)) — координата компонента по Y.
— Rotation — угол установки компонента.
— Explanation или Footprint — о них ниже
Необязательное поле:
— Layer — сторона установки компонента. Если это поле присутствует в файле, то программа при открытии файла спросит для какой стороны платы взять из файла компоненты. Если указать нижнюю сторону, то станет доступна опция Reverse X для зеркалирования координат по оси X.
— Explanation — описание компонента, это может быть любое значение, например тип корпуса и номинал для резисторов и конденсаторов или название для микросхем и т.д. Служит исключительно для удобства оператора. Если этого поля нет, то в описание программа вставляет значения Footprint и Comment.
— Footprint — название корпуса компонента.
— Comment — любое описание компонента, например его номинал.
По поводу полей Explanation, Footprint и Comment. Если в файле нет одного из двух полей — Explanation или Footprint, программа вылетает с ошибкой при попытке открыть такой файл. Если имеется поле Explanation, то программа берет значение для столбца Comment в выводимой на экран таблице именно из этого поля, игнорируя поля Footprint и Comment. Если поля Explanation в файле нет, то для столбца Comment берется значение поля Footprint плюс значение поля Comment (если оно есть).
Любые другие поля в файле .csv программа станка будет просто игнорировать.
Координаты при импорте округляются до сотых долей миллиметра.
Такие файлы может формировать практически любая программа проектирования печатных плат. Там это так и называется — вывод для Pick and Place (PnP). Это может быть в разделе экспорта или в разделе отчетов. Я буду показывать на примере программы P-CAD 2006.
Подготовка списка для установки из P-CAD 2006
Итак, у нас открыт проект печатной платы и нам нужно вывести список компонентов для установки: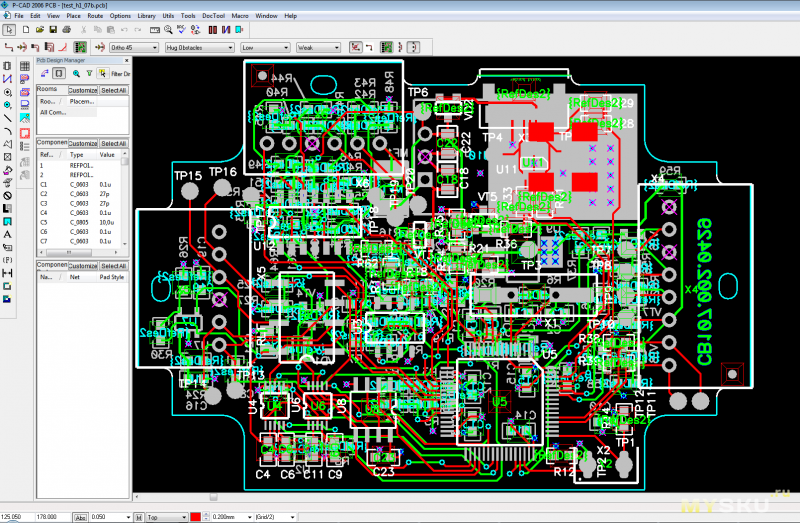
Для удобства работы можно удалить все кроме компонентов и границ платы и сохранить файл с новым именем, например xxxx_pnp.pcb:
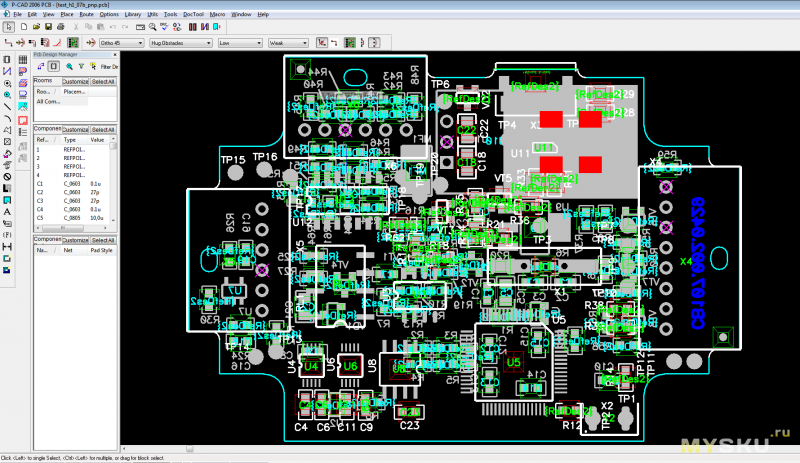
Удалять что-то определенное или все кроме чего-то определенного очень удобно через Options -> Selection Mask. Там выделяем галочками что можно выделять и на каких слоях и потом просто выделяем мышкой всю плату. Выделенными станут только разрешенные элементы.
Дальше можно пойти двумя путями: экспортировать список всех компонентов с обеих сторон и дальше при открытии файла в программе установщика выбирать нужную сторону, или сохранить две стороны в отдельных файлах. Первый вариант проще и быстрее, но в нем координаты X всех компонентов с нижней стороны примут в программе установщика отрицательные значения. В том числе и в настройки платы нужно будет забивать координаты реперных знаков со знаком минус по оси X. Это ни на что особенно не влияет, просто не слишком удобно если придется что-то проверять или подстраивать 🙂
Во втором варианте придется побольше повозиться, но все координаты будут иметь положительное значение X.
Итак, если решили сделать как проще, по первому варианту, то сразу идем в File -> Reports, ставим там галочку на Pick and Place Locations (csv):
и жмем кнопку Customize. В первой вкладке меняем расширение на csv и убираем галочку Include Report Preface:
Во второй вкладке ставим крестики на строках RefDes, Type, Value, LocationX, LocationY, Layer и Rotate:
Значения RefDes, LocationX, LocationY и Rotate необходимы для программы установщика, Layer так же нужен для корректного выбора стороны установки, а Type и Value используем для формирования поля Explanation, которое так же требуется установщику. Жмем Ok, убеждаемся, что выбраны варианты File и Separated List и жмем Generate. Теперь в папке с платой у нас есть файл xxxx_pnp.csv для двух сторон платы.
Можно переходить к обработке файла в Excel 🙂
Второй вариант:
Нужно удалить все компоненты с нижней стороны и сохранить опять под новым именем, например xxxx_top_pnp.pcb:
Верхняя сторона готова к экспорту списка для установки. Идем в File -> Reports и действуем как описано в первом варианте. В папке с платой у нас появляется файл xxxx_top_pnp.csv для верхней стороны платы.
Теперь открываем предыдущий вариант платы xxxx_pnp, в котором удалено все кроме компонентов на обеих сторонах и удаляем все компоненты на верхней стороне:
Сохраняем под новым именем, например xxxx_bottom_pnp.pcb
Теперь выделяем абсолютно все и переворачиваем кнопкой F. Все что было на нижней стороне перейдет с зеркальным переворотом на верхнюю сторону, остальное (например границы платы) просто зеркально отразится:
Это нужно для правильных координат, ведь станок будет «видеть» плату именно в таком виде.
Повторяем File -> Reports и так далее, только теперь сформируется файл xxxx_bottom_pnp.csv
Все, у нас есть файл для установки на верхнюю сторону и файл для установки на нижнюю сторону (или единый для обеих сторон). Но их нужно слегка подправить. Открываем в Екселе файл xxxx_top_pnp.csv:
Для начала меняем формат всех колонок на «Текстовый». Потом удаляем строки с компонентами, которые не нужно ставить. Теперь нужно изменить названия полей координат с LocationX/LocationY на MidX/MidY. И добавить поле Explanation. В него можно скопировать значения из Value или Type, а можно объединить их. Лично я использую для формирования значений этого поля формулу:
=ЕСЛИ(СОВПАД(C3,"Value"), B3, СЦЕПИТЬ(B3, " - ", C3))
То есть если поле Value (номинал) содержит слово «Value» (значит, что номинал не задан, например для микросхем/диодов/транзисторов и т.п.), то подставляем только значение из Type, иначе объединяем через тире с пробелами Type и Value. Размножаем эту формулу по всем строкам:
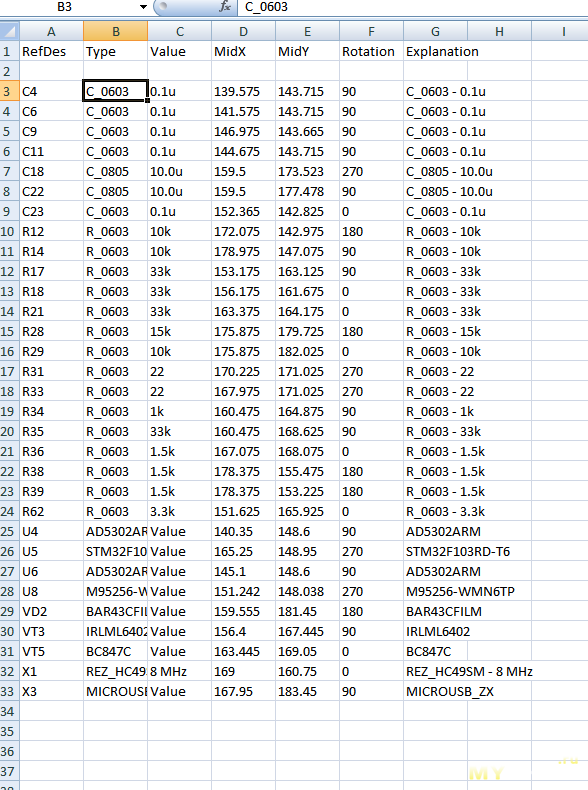
Все, файл готов, сохраняем его в тот же формат .csv.
Кстати, следите за тем, чтобы в значениях полей не было запятых, потому что Ексель при сохранении не обрамляет значения кавычками и запятая в значении будет воспринята как разделитель.
Аналогично поступаем и с .csv для нижней стороны.
Подготовка списка для установки из Altium Designer 17
В Altium Designer все делается гораздо проще. Здесь как и в P-CAD можно пойти двумя путями — сформировать список сразу для обеих сторон или отдельные списки для верхней и нижней. Логика действия при этом такая же как и для P-CAD.Дальше идем в Файл -> Выходные файлы для сборки -> Generates pick and place files:
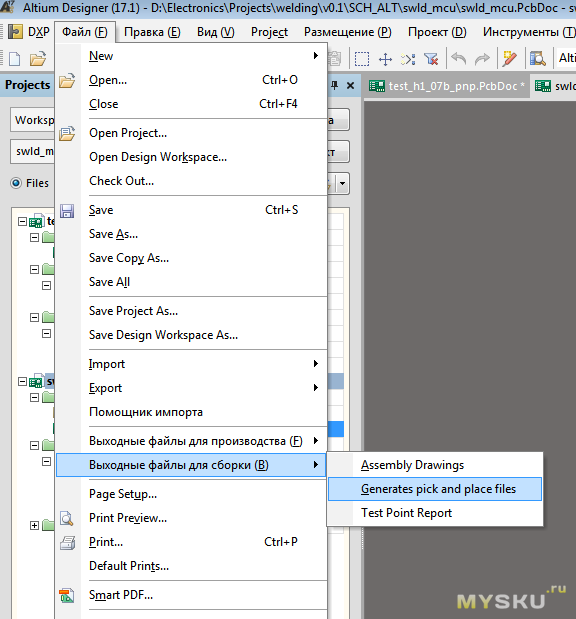
В появившемся окне убеждаемся, что все галочки и переключатели установлены как на скриншоте:
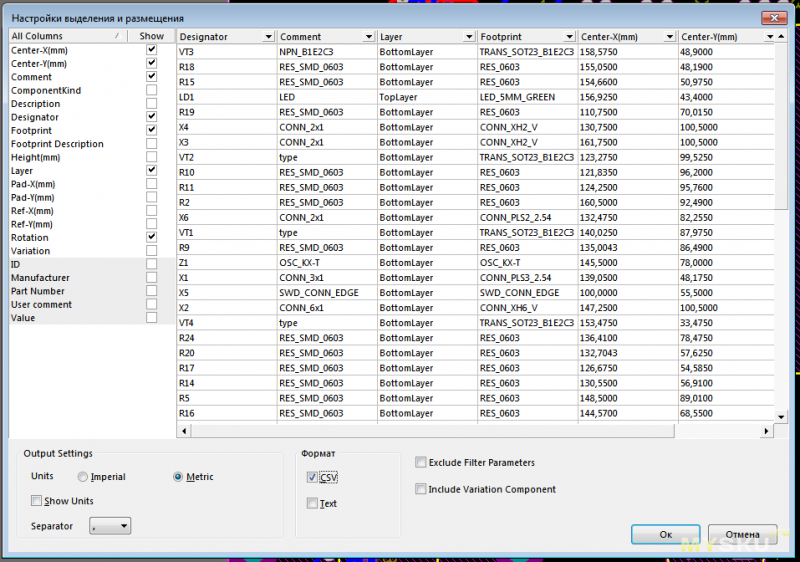
И жмем Ok. В подкаталоге Project Outputs for появляется файл .csv со списком компонентов для установки и этот файл можно сразу скармливать программе установки, она его сожрет без всяких доработок 🙂
Файлы со списками готовы, копируем их на компьютер станка. Если это отдельные файлы для каждой стороны (с перевернутой нижней стороной), то программа установщика открывает эти файлы молча. Если это один файл для обеих сторон, то при открытии программа спросит какую сторону нужно выбрать из файла:
При выборе нижней стороны становится доступна галочка Reverse X и ее нужно отметить.
Зачем реверсировать (зеркалить) нижнюю сторону?
Когда плата проектируется, то на все слои мы смотрим «сверху» — со стороны верхнего слоя, как бы сквозь плату. Например, у нас вот такая плата с микросхемой U1 и резистором C1 на нижней стороне платы: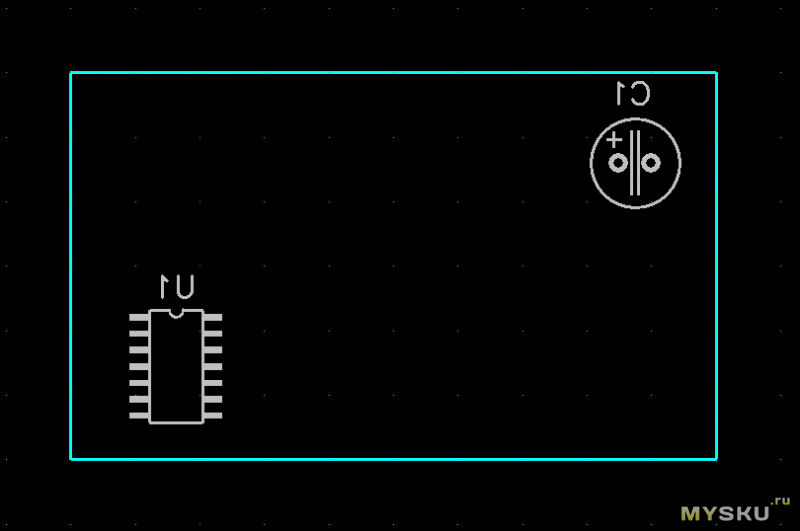
В программе проектирования мы на них смотрим «сквозь» плату, со стороны верхнего слоя, это заметно, например, даже по перевернутым обозначениям. Координаты и у станка и в программах проектирования плат начинаются снизу слева, в данном случае начало координат лежит в нижнем левом углу платы. Таким образом координаты микросхемы X-Y будут 33.0-30.0 (группа Location):
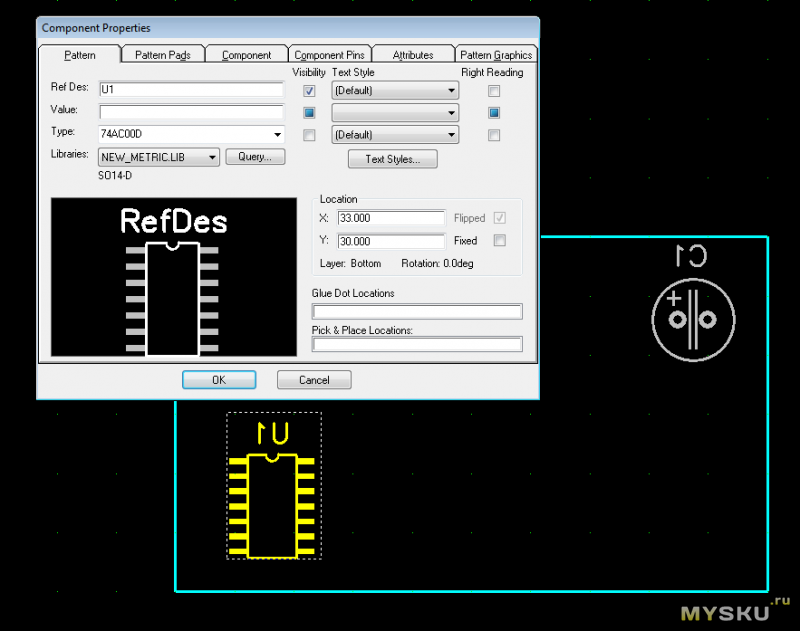
а координаты конденсатора — 67.0-42.0:
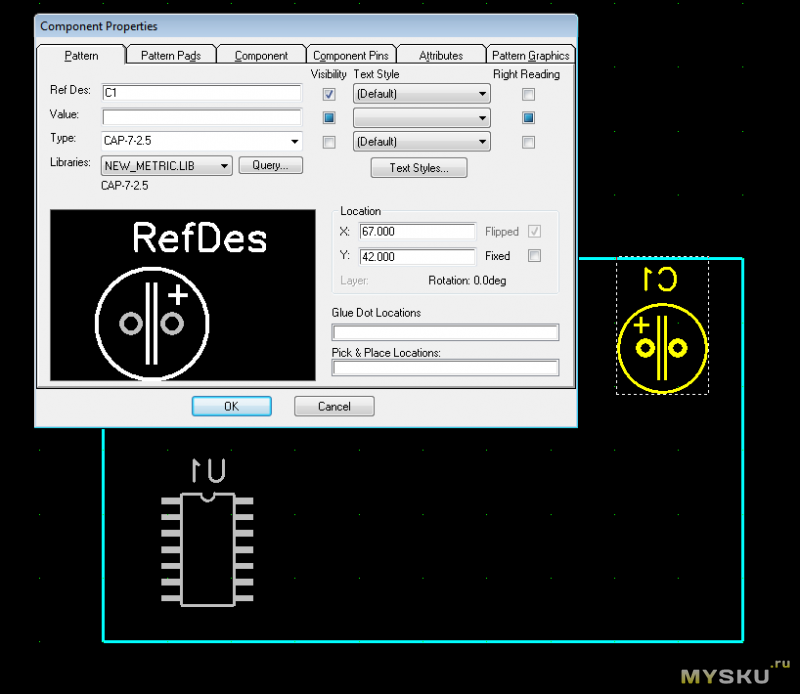
И именно эти координаты и будут выведены в файл PnP.
Но ведь когда нам нужно поработать с реальной платой, мы должны перевернуть ее нижней стороной к себе, и при этом все компоненты отразятся зеркально — которые были слева станут справа, а которые были справа станут слева:
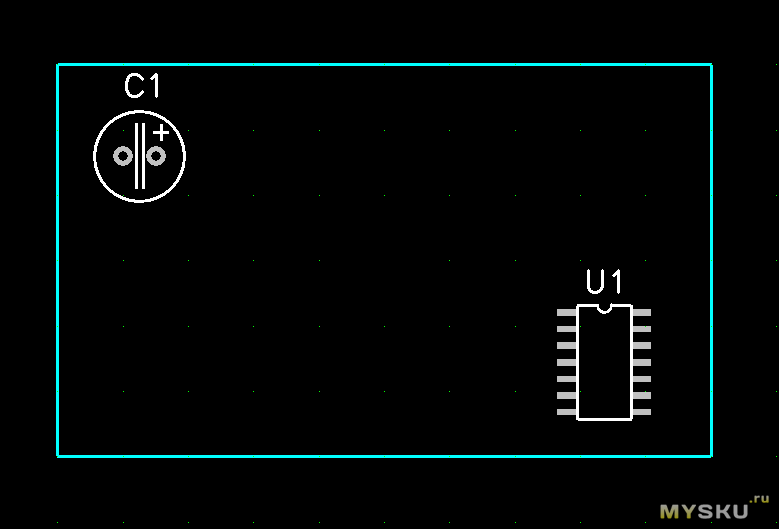
Теперь у микросхемы координаты стали 61.0-30.0:
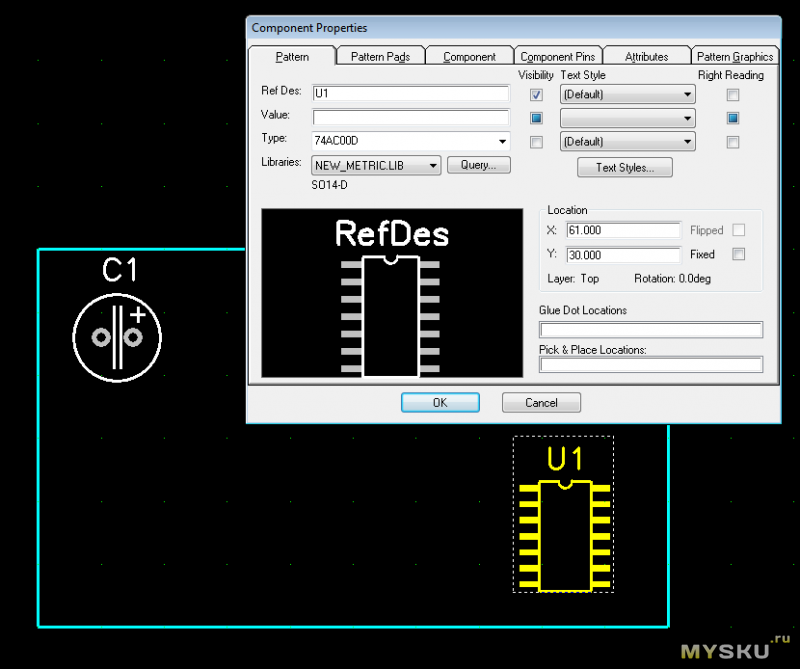
а у конденсатора — 27.0-42.0:

Значит и координаты из файла нужно «перевернуть». Вот это и делает галочка Reverse X — проставляет координатам по X знак «минус» перед значением, то есть фактически зеркально переворачивает их относительно нуля.
Итак, файл открыли:
Как видим, список в основном поле программы почти повторяет список из файла .csv, только с добавлением дополнительных полей. Кстати, эти поля можно выводить и сразу из программы проектирования печатных плат — добавить компонентам свойства с соответствующими названиями и сразу присваивать нужные значения. Только тут есть нюансы. Например, если у какого-то компонента не будет такого свойства, то в файл выведется пустое значение, а программа установщика не принимает файлы с пустыми значениями.
Из дополнительных полей мы можем увидеть:
Nozzle — каким соплом работать с этим компонентом. Доступен выбор из списка — 1 — первым (левым), 2 — вторым, 1/2 — можно и первым и вторым.
Stack — из какой позиции какого питателя брать этот компонент. Так же выбор из списка — левый питатель, задний, и лотки для микросхем:
Height — высота компонента. На эту высоту сопло будет недоопускаться при установке компонента на плату или при взятии его из лотка для микросхем. Задается в миллиметрах.
Speed — скорость опускания сопла с компонентом при его установке. Доступен список в процентах с шагом 10:
Vision — коррекция положения компонента по нижней камере. Доступен список — None (не корректировать), Quick (быстрая коррекция) и Accurate (точная коррекция):
Галочка Pressure — подавать ли в сопло избыточное давление после установки компонента на плату.
Галочка Done — говорит о том, что компонент уже установлен, его ставить не надо. Эти галочки заполняются автоматически по мере установки компонентов, так что остановив выполнение программы потом можно продолжить установку с первого неустановленного компонента. Или можно перед установкой вручную отметить эту галочку у тех компонентов, которые ставить не нужно.
Самая левая часть строк (перед колонкой ID) предназначена для выделения строк. Выделять строки можно для:
— установки только выделенных компонентов. Для этого нужно выделить нужные компоненты, щелкнуть правой клавишей мыши и выбрать из выпавшего меню пункт Place Selected Components.
— задания одинакового значения параметров для всех выделенных строк. Например, выделяем все строки с резисторами 0603 15к и в любой из выделенных строк ставим значение Stack в L14. Автоматически во всех выделенных строках этот параметр поменяется на это значение. Так же можно изменить и любой другой параметр, включая галочки, списки, числовые значения.
— удаления выделенных строк. Выделяем, жмем Del и подтверждаем удаление.
Нажатие правой кнопки мыши на списке вызывает выпадающее меню, в котором можно:
— добавить новый компонент (новую строку) в разных вариантах — с нулевыми координатами, с текущими координатами сопла, с текущими координатами камеры;
— установить текущему компоненту (на котором щелкнули) текущие координаты сопла или текущие координаты камеры;
— передвинуть на координаты текущего компонента сопло или камеру;
— выделить все строки с таким же значением того параметра, который в данный момент выделен. Например, выделяем параметр угла компонента, кликаем на нем правой кнопкой и выбираем Select The Same:
В результате выделяются все строки, в которых параметр угла равен тому, который был выделен:
Все компоненты настроены, для них указаны позиции в питателях, сопла, скорость, режим визуальной коррекции и т.д. Теперь переходим в настройки платы — кнопка PCB Config внизу. Первым делом идем во вкладку Config и настраиваем параметры реперных меток, используемых в нашей плате.
Что такое реперные метки и зачем они
Реперные метки представляют собой специальные знаки на плате, которые хорошо видны камерой и легко определяемы программами. Обычно это просто круглые контактные площадки диаметром 1-2 мм, открытые от маски, расположенные в двух или трех противоположных углах платы (ну или как можно дальше друг от друга по обеим осям). Их координаты точно известны при проектировании и установщик, найдя эти метки на реальной плате и определив их реальные координаты, может сделать поправку на погрешность установки платы как по смещению, так и по углу.
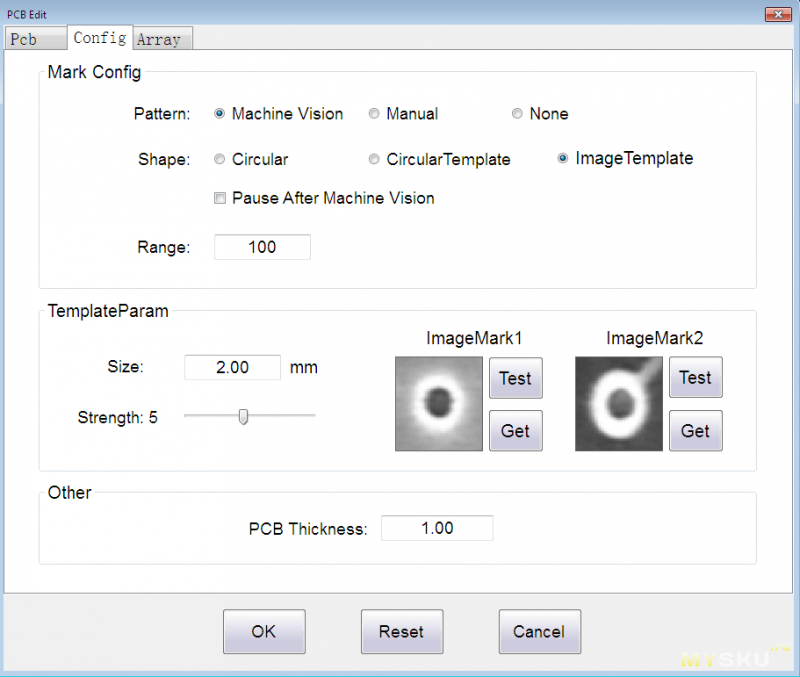
Этот установщик работает с одной или двумя реперными метками на плату. По одной он может определять только смещение плат, по двум — еще и угол их поворота. Желательно всегда использовать две метки.
Выбираем Pattern:
— если хотим, чтобы установщик сам находил, распознавал и центрировался на реперных метках, то выбираем Machine Vision.
— если хотим, чтобы станок оставлял возможность точного центрирования на метках оператору в ручном режиме, ставим Manual.
— и если вообще не собираемся делать коррекцию по реперным меткам, ставим None. В этом случае предполагается, что платы всегда устанавливаются абсолютно одинаково и точно и нет нужды во внесении поправок на погрешность установки платы.
Выбираем Shape:
— Circular или Circular Template — метка представляет собой стандартный кружок. Отличие этих параметров в том, что просто Circular будет искать любой круг в радиусе обнаружения, а Circular Template будет искать круг заданного диаметра.
— ImageTemplate — метка представляет собой что-то нестандартное.
Галочка Pause After Machine Vision ставит установщик на паузу после того как он в автоматическом режиме распознал и определил координаты метки. Оператор может проконтролировать точность распознавания и при необходимости поправить перед тем как продолжить.
Range говорит установщику в каком радиусе от предполагаемых координат искать и пытаться распознать метку. Это ограничение вводится для того, чтобы станок не принял за метку какое-то соседнее отверстие или контактную площадку, попадающие в поле зрения камеры.
Группа TemplateParam отвечает за размер меток и их вид.
Size говорит станку какого размера метку нужно искать. Это или диаметр круга для Circular Template или размер картинки для ImageTemplate.
Strength устанавливает степень соответствия искомого изображения. Если метка имеет высокую контрастность и повторяемость от платы к плате, то это значение можно поставить побольше для бОльшей точности определения центра метки. Если метка видна плохо или ее изображение может слегка варьироваться от платы к плате, то это значение лучше сделать поменьше. При неправильно настроенном этом параметре установщик может вообще не находить метку (при слишком высоком значении) или видеть ее там, где ее нет (при слишком низком значении).
ImageMark1 и ImageMark2 отвечают за нестандартный тип первой и второй реперных меток соответственно — например, квадратные контактные площадки, какие-то знаки или буквы на плате и т.п. Они активны только если выбрана опция ImageTemplate в параметре Shape. При нажатии кнопки Get установщик сохранит область из центра текущего изображения камеры размером, установленным в Size. Этот кусок изображения будет служить эталоном при автоматическом поиске и распознавании меток. Следует обратить внимание, что центром метки будет считаться центр этого куска изображения, так что перед тем как нажать Get следует выставить центр камеры точно в центр метки, это важно. Кнопка Test включает распознавание метки и накладывает на изображение камеры бирюзовый квадрат (или круг) вокруг распознанной метки:
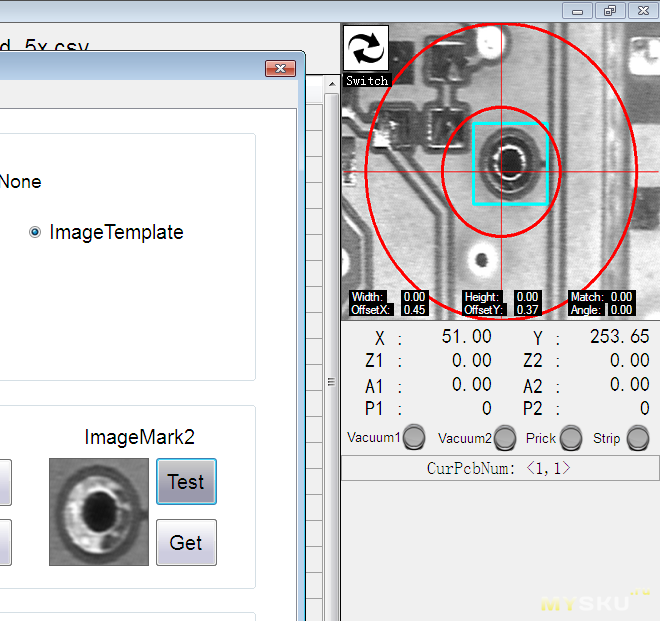
Это помогает проверить насколько правильно были заданы параметры метки.
Теперь переходим во вкладку PCB, где нужно настроить координаты реперных меток. Тут можно настроить до 50 плат — это группы PCB1, PCB2, PCB3 … PCB50. Если Вы ставите в установщик одновременно три платы, значит настраиваете параметры в трех группах, например PCB1, PCB2 и PCB3 , в остальных группах галочки Enable должны быть отключены. При этом можно настроить, скажем, 10 плат PCB1—PCB10, но если в очередной раз нужно будет поставить компоненты только на 3-ю и 5-ю платы, то можно просто снять галочки во всех группах кроме PCB3 и PCB5, а позже опять поставить их.
Mark1 и Mark2 задают координаты первой и второй реперных меток в системе проектирования платы. Эти координаты берутся в программе проектирования и во всех группах имеют одинаковое значение.
Например, тут координаты первой метки равны 139.0-185.0, их и нужно вносить в поля Mark1.
Если из проекта был выведен список компонентов с обеих сторон и при его импорте в программу установщика была выбрана нижняя сторона с зеркалированием координат X, то координаты по X в Mark1 и Mark2 нужно вводить отрицательными. К примеру, если в системе проектирования координата X у реперной метки равна 110.0, то сюда ее нужно вписать как -110.0.
Real1 и Real2 — это координаты этих же меток уже на реальных платах, установленных в станке. Для каждой метки нужно подвести к ее центру верхнюю камеру и нажать Set XY. Эти координаты служат отправной точкой для автоматического поиска реперных меток. При работе установщик подводит к этим координатам камеру и начинает искать здесь реперную метку по настроенным параметрам.
Это не значит, что все эти координаты нужно вводить после каждой установки плат. Нет, они вводятся только один раз, ведь платы в установщик всегда устанавливаются одинаково, так что и реперные метки всегда будут находиться в примерно одинаковых координатах. Может быть только небольшая погрешность, например, из-за неровного края отломанной от панели по скрайбированию платы (скрайбирование — прорезание текстолита по контурам плат примерно на треть толщины сверху и снизу), которую установщик и компенсирует, распознавая метки и точно определяя их центр.
Итак, настроили метки для всех плат, что дальше?
Теперь нужно сохранить файл кнопкой Save внизу главного окна. Если Вы открывали общий файл с компонентами и верхнего и нижнего слоев, то программа в диалоге сохранения автоматически добавит в конце имени файла «_top» или «_bottom», смотря какой слой Вы выбрали при открытии. Иначе имя для сохранения будет таким же, по которым .csv файл был открыт.
Программа сохраняет с тем же расширением — .csv, но это уже не совсем тот самый «comma separated values» формат. Начинается он в правильном формате — списком компонентов со всеми настроенными параметрами (сопла, позиция в питателе, режим визуальной коррекции т.д.) но после этого списка в файл пишутся и все те настройки, которые были внесены в разделе PCB Config — вплоть до образов пользовательских реперных меток, захваченных с камеры. А так же настройки лотков для микросхем, хотя они находятся в системных настройках. И это логично — для каждого вида плат могут понадобиться уникальные лотки под конкретный набор микросхем, так что сохранять настройки лотков в файле конкретных плат — отличная идея. И вот эти дополнительные настройки хранятся в файле уже совершенно не в соответствии с форматом .csv, хотя и в текстовом виде. Так что открыть этот файл в том же Екселе, чтобы что-то подправить, не получится.
И вот теперь можно нажимать Start в программе или на передней панели станка и смотреть как он работает за Вас 🙂
Это если был установлен режим Machine Vision и снята галочка Pause After Machine Vision. Иначе установщику придется помочь с определением реперных меток. В режиме Machine Vision с установленной галочкой Pause After Machine Vision нужно будет просто проконтролировать как он находит центры меток и кнопкой Pause/Cont подтверждать ему после каждой метки. При этом перед продолжением можно подкорректировать положение если станок сам не совсем точно определил центр. В режиме Manual все то же самое, но только станок сам не будет пытаться найти метку и ее центр, так что корректировать руками придется практически каждую метку.
Ниже в видео показаны три режима поиска реперных меток станком. В первом режиме установщик в полностью автоматическом режиме проходит по всем меткам, распознавая их, находя центр и переходя к следующей метке. Во втором режиме (с установленной галочкой Pause After Machine Vision) он так же сам распознает метки, находит их центр, но после этого встает на паузу, ожидая подтверждения оператором (нажатия кнопки Pause/Cont). В третьем режиме (Manual) установщик только подводит камеру к предполагаемым координатам метки (заданным в настройках платы), но не пытается определить ее центр, хотя саму метку распознает — это видно на изображении с камеры (в правом верхнем углу). Обратите внимание, что метки смещены от центра, но станок не пытается скорректировать это смещение, в отличии от двух предыдущих режимов, он оставляет это за оператором.
И еще одно видео — установка компонентов на две одинаковые платы.
Небольшие пояснения к видео — в начале видно, что я отключаю реперные метки с трех плат из пяти, тем самым исключая эти платы из работы. Вообще файл рассчитан на работу с пятью платами, но для более короткого видео я взял только две платы, поэтому остальные три отключил.
Некоторые компоненты я предварительно установил на плату вручную. Это не потому что с ними какие-то проблемы у станка, просто так получилось 🙂 И в начале видео видно, что я для этих компонентов устанавливаю в списке галочку Done, чтобы программа знала, что они установлены. Из-за этого программа при старте работы и спрашивает «Продолжить или начать заново?». Начать заново — программа очистит галочки Done у всех компонентов и будет ставить все что есть в списке. Продолжить — программа не будет устанавливать компоненты с галочкой Done.
На видео видно, что одна большая и одна мелкая микросхемы при установке на плату чуть съехали в сторону — это из-за очень толстого лужения производителем плат. На второй плате эти же микросхемы сели без сползания и отлично попали на свои площадки, в конце видео я привел их фотографии под микроскопом. Так же не попал в отверстия один из разъемов miniUSB, почему- фиг знает 🙂 Где-то один из 20 разъемов не попадает. Может быть при проектировании платы я не точно указал центр разъема как точку установки…
Микросхемы с мелким шагом — TQFP64 и MSOP10 устанавливаются с точной коррекцией по нижней камере. Остальные микросхемы, miniUSB и кварц — устанавливаются с быстрой коррекцией по камере. Остальные компоненты ставятся без визуальной коррекции. Скорость работы — по умолчанию, 50% 🙂 И сорри за звуковой фон и за качество монтажа — мой слабый рабочий комп едва шевелился в видеоредакторе, так что было не до лоска 🙂
И эти платы после печки еще до мытья:
После 12 минут мытья в УЗ-ванне, 5 секунд ополаскивания в дистиллированной воде и 30 минут сушки при температуре 110 градусов не останется ни следов флюса, ни разводов, ни налета — платы будут девственно чисты 🙂
Коротко в целом по станку:
+ есть стандартные китайские огрехи и некоторая экономия, но в целом сделан очень и очень неплохо, я ожидал худшего.
+ работает практически из коробки, хотя для наилучшего результата тщательная настройка требуется.
+ механика достойного качества, работает не очень шумно, как и помпа.
+ встроенный компьютер при всей его слабости легко справляется с управлением станком.
+ цена вполне оправдана возможностями 🙂
+ поддержка производителя отвечает по email довольно оперативно и по делу.
— требует очень много места, на стандартный стол со столешницей глубиной 60 см не встанет — у него между ножками 62 см, к тому же требует наличие доступа с трех сторон (ну или как минимум спереди и сзади).
— вопреки заверениям продавца, не способен точно ставить корпуса размером с TQFP-144 и больше.
— концевики механические, неточные (обычные микрики), хотя от их точности здесь зависит очень многое, очень желательно сразу менять на оптические.
— нет питателей на ленты 24 мм и вибролотка.
Коротко в целом по софту:
+ гораздо более гибкий и мощный, чем я ожидал, предусматривает множество моментов, о которых я даже не задумывался раньше.
+ весьма удобный для работы со списками компонентов.
+ довольно развитые средства работы с несколькими платами.
+ обширные настройки и калибровки.
+ умеет работать с пользовательскими реперными метками.
— нет ни одной горячей клавиши, что бывает весьма неудобно.
— совершенно не документирован.
— нет рисок на линиях поверх изображения с камер для более удобного центрирования, пришлось выкручиваться варварскими методами — матовый скотч на мониторе с нарисованными маркером миллиметровыми рисками :))
Спасибо всем, кто хотя бы попытался прочесть хотя бы половину моей писанины :))))
Если остались любые вопросы задавайте, постараюсь ответить 🙂
UPD (25.09.2018): получил пару катушек с резисторами и конденсаторами типоразмера 0402 (размер такого резистора — 1.0х0.5 мм), установил в питатели и попробовал установку на максимальной скорости без визуальной коррекции. На состояние платы не обращайте внимания — это на ней двухсторонний скотч для удерживания компонентов 🙂 Результат более чем устраивает:
Руководство для проектировщиков печатных плат по Разработке для производства (DFM). Часть 7. Глава 7, продолжение.
Спецификации процесса
Спецификации процесса включают в себя информацию, которая нужна производителю, когда он выполняет определенные процессы, такие как чистка и подготовка вашей платы. Информация о процессах должна включать и информацию о необходимых допусках.
Система матрицы
Система матрицы играет важную роль в создании платы и используется для размещения свойств и деталей, включая компоненты, отверстия и поверхностно монтируемые элементы. Свойства, не размещенные на матрице, должны быть измерены с учетом необходимых допусков.
Производственные характеристики
Производственные характеристики представляют собой дополнительную информацию, которая позволит производителю понять, как ваша плата ориентирована в пространстве для более эффективной обработки.
Реперные точки
Реперная точка — это контрольная точка, расположенная на печатной плате (обычно это отверстие), которая позволяет машине «видеть», как плата ориентирована в пространстве. Для более детальной информации обратитесь к IPC-D-300. 17-21
Опорные метки
Опорные метки – это особый тип реперных точек, обычно используемые для машин «захват-размещение», которые позволяют машине знать, где ПП ориентирована в пространстве. Опорные метки должны быть показаны на всех планах поверхностного монтажа.
Документация к эталонному чертежу
Раздел документации к эталонному чертежу включает в себя все поддерживающие детали для вашей платы, включая примечания, выноски, дополнительные схемы, что поможет прояснить ваши производственные намерения.
Диаграмма контроля конфигураций чертежей
Диаграмма контроля конфигураций чертежей – это таблица, которая указывает и управляет уровнями изменений различных чертежей, включая трафаретное нанесение, паяльная паста, данные по сверлению.
Примечания
Примечания, сопровождающие производственные чертежи, используются для того, чтобы уточнить ваши требования и детали для процесса производства. Ниже приведен список возможных примечаний, которые вы можете включить в вашу документацию:
• Спецификации и класс окончательной платы
• Требования к материалам
• Требования к материалам В-стадии (для многослойных плат)
• Маркировка платы
• Конструкция
• Спецификации паяльной маски
• Материал и толщина паяльной маски
• Требования к сверлению отверстий
• Толщина медного покрытия
• Требования к травлению
• Требования по изгибу платы
• Тип чернил для нанесения
• Требования к тест-купонам
• Требования к электрическому тестированию платы
Завершение подготовки производственной документации
Документация по вашей разработке – это один из наиболее важных аспектов процесса разработки. Даже самый лучший проект печатной платы пропадет, если вы не в состоянии четко сообщить ваши намерения своему производителю. В следующей главе мы изучим последний кусочек паззла под названием «документация» для окончательного монтажа вашей платы.
Устройство для совмещения реперных знаков пленочного фотошаблона печатной платы
Патент 1102063
Устройство для совмещения реперных знаков пленочного фотошаблона печатной платы
УСТРОЙСТВО ДЛЯ СОВМЕЩЕНИЯ РЕПЕРНЫХ ЗНАКОВ ПЛЕНОЧНОГО ФОТОШАБЛОНА ПЕЧАТНОЙ ПЛАТЫ, преимущественно в установках для пробивки базовых а отверстий, содержащее основание и размещенный на нем механизм фиксации фотошаблона с регулировочным винтом, отличающееся тем, что, с целью улучшения эксплуатационных возможностей, механизм фиксации снабжен дополнительными регулировочными винтами и выполнен i виде плиты с фрикционными прокладками , установленными со стороны фотошаблона, и откидными стойками, одна из которых снабжена подпружиненными упорами, причем регулировочные винты и подпружиненные упоры установлены на стойках с возможностью взаимодействия с плитой.
СОЮЗ СОВЕТСНИХ
СОЦИАЛИСТИЧЕСКИХ
РЕСПУБЛИК
ЗсЮН05КЗОО
ОПИСАНИЕ ИЗОБРЕТЕНИЯ
Н АВТОРСКОМУ СВИДЕТЕЛЬСТВУ (21) 3589637/18-21 (22) 27. 04 ° 83 (46) 07.07.84. Бюл. 25 (72) Л.А. Писарева (53) 621.317.729.2(088.8) ГОСУДАРСТВЕННЫЙ КОМИТЕТ СССР
ПО ДЕЛАМ ИЗОБРЕТЕНИЙ И ОТНРЫТИЙ (56) 1. Авторское свидетельство СССР
Р 658795, кл. Н 05 К 3/00, 06.01.77.
2. Авторское свидетельство СССР
Р 924925, кл. Н 05 К 3/00, 07.09.79 (прототип). (54)(57) УСТРОЙСТВО ДЛЯ СОВМЕЩЕНИЯ
РЕПЕРНЫХ ЗНАКОВ ПЛЕНОЧНОГО ФОТОШАБЛОНА ПЕЧАТНОЙ ПЛАТЫ, преимущественно в установках для пробивки базовых
„„SU„„1102063 А отверстий, содержащее основание и размещенный на нем механизм фиксации фотошаблона с регулировочным винтом, о т л и ч а ю щ е е с я тем, что, с целью улучшения эксплуатационных возможностей, механизм фиксации снабжен дополнительными регулировочными винтами и выполнен в. виде плиты с фрикционными прокладками, установленными со стороны фотошаблона, и откидными стойками, одна из которых снабжена подпружиненными упорами, причем регулировочные винты и подпружиненные упоры установлены на стойках с возможностью взаимодействия с плитой.
55
1 110206
Изобретение относится к технологическому оборудованию для производства печатных плат.
Известно устройство для совмещения реперных знаков пленочного
5 фотошаблона печатной платы для пробивки базовых отверстий, содержащее основание, подпружиненные пуансоны и прижимные планки (1 J.
Однако устройство не обеспечи- !0 вает качественного изготовления фотошаблонов, так как при зажиме фотошаблона в устройстве возможен
его сдвиг, а при больших габаритах фотошаблона возможно его коробление и не представляется возможным усреднение погрешности межосевого расстояния между реперными знаками.
Наиболее близким к изобретению по технической сущности является 20 устройство для совмещения реперных знаков пленочного фотошаблона печатной платы в установке для пробивки базовых отверстий, содержащее основание и размещенные на нем 25 механизмы пробивки базовых отверстий и механизмы совмещения реперных знаков и фиксации фотошаблона Ã23.
Однако известное устройство неудобно к эксплуатации, так как совмещение реперных знаков фотошаблона производится очень долго потому,что осуществляется при помощи одного регулировочного винта.
Цель изобретения — улучшение эксплуатационных возможностей.
Поставленная цель достигается тем, что в устройстве для совмещения реперных знаков пленочного фотошаблона печатной платы, преимущественно в установках для пробивки базовых отверстий, содержащем основание и размещенный на нем механизм фиксации фотошабло- 45 на с регулировочным винтом, механизм фиксации снабжен дополнительными регулировочными винтами и выполнен в виде плиты с фрикционными прокладками, установленными со стороны фотошаблона,,и откидными стойками, одна из которых снабжена подпружиненными упорами, причем регулировочные винты и подпружиненные упоры установлены на стойках с возможностью взаимодействия с плитой.
На фиг. 1 изображено устройство, вид сверху; на фиг. 2 — разрез А-А
3 з на фиг. 1; на фиг. 3 — схема воз,можного варианта разделения погрешностей при настройке.
На основании 1 закреплены кронштейны 2, на которых установлены при помощи цанг 3, гаек 4 микроскопы 5, пуансоны 6 с пружинами 7, прижимы 8 с пружинами 9, соединенные тягами 10 с упорами 11 и скобарукоятка 12. На основании 1 устанавливается фотошаблон 13, на него кладется плита 14, снабженная фрик- . ционными прокладками 15, приводимая в движение регулировочными винтами
16 и.17 и подпружиненными упорами
18 и 19, установленными в откидных стойках 20 и 21, представляющими собой механизм фиксации фотошаблона.
В основании 1 выполнены два установочных отверстия 22 и 23, расположенные точно по координатам реперных знаков, отверстия 24, соединяющие рабочую поверхность основания 1 с вакуумной камерой 25. Камера 25 соединяется с вакуумным насосом через дроссель 26,. при помощи которого регулируется усилие поджатия фотошаблона к основанию.
Устройство работает следующим об- . разом.
Откинув стойки 20 и 21, фотошаблон 13 устанавливают ориентировочно на основании 1 так, что реперные знаки 27 совпадают с установочными отверстиями 22 и 23. Включается устройство для вакуумного поджима. При помощи дросселя 26, регулируя усилие поджнма, фотошаблон 13 расправляется и слегка поджимается к рабочей поверхности основания 1. Стойки 20 и
21 с регулировочными винтами 16 и
17 и подпружиненными упорами 18 и 19 устанавливают в рабочее положение.
Между регулировочными винтами 16 и
17 и подпружиненными упорами 18 и !9 на фотошаблон 13 кладут плиту 14, снабженную прокладками 15, которые обеспечивают прочное сцепление плиты
14 с фотошаблоном 13. При помощи регулировочных винтов 16 и 17 и подпружиненных упоров 18 и 19, плиту 14 со сцепленным фотошаблоном 1.3 можно передвигать в нужном направлении для совмещения реперных знаков 27 с отверстиями 22 и 23. Контроль совмещения производится через микроскопы 5.
При наличии погрешности расположений реперных знаков 27 ее необходимо раз1102063 делить поровну (усреднить) за счет равного смещения осей реперных знаков
27 от осей отверстий 22 и 23.
После окончательной выверки фотошаблона его плотно поджимают к основанию 1 увеличением разряжения в вакуумной камере 25 при помощи дросселя 26. Затем, воздействуя на скобырукоятки 12, упоры 11 производят пробивку базовых отверстий пуансонами 6. При движении пуансонов 6 при- жимы 8 идут сначала .вместе с ними, поджатые к тягам 10 пружинами 7, так как пружины 7 сильнее пружин 9.
При дальнейшем движении пуансонов 6 прижимы 8 касаются фотошаблона 13 и дополнительно прижимают его силой пружин 9 в зоне пробиваемых отверстий. Затем происходит пробивка базовых отверстий.
При плавном снятии усилия со скоб-рукояток 12 пуансоны 6 под действием пружин 7 возвращаются в исходное положение. Сначала выходит пуансон 6 из фотошаблона 13, при этом фотошаблон 13 еще зажат прижимами 8, что обеспечивает высокое качество кромок пробитых отверстий.
При дальнейшем движении пуансона 6 вверх избыточным усилием пружин 7.
5 по отношению к пружинам 9 прижимы 8 встают в крайнее верхнее положение.
Устройство для совмещения реперных знаков пленочного фотошаблона позволяет улучшить эксплуатационные
1О возможности и повысить точность расположения базовых отверстий относительно реперных знаков фотошаблона, а следовательно, и точность взащ ного расположения слоев многослойных
1 печатных плат. Экономический эффект от внедрения устройства получается за счет повышения процента выхода годных печатных плат, так как улучшается удобство работы и повышается
20 точность расположения и пробивки базовых отверстий, что позволяет по-высить точность базирования при выполнении операций: экспонирование, нанесение печати, совмещение слоев по рисунку, выполнение контактных отверстий.
1102063
1102063
Ф, %
Составитель В. Жеглов
Редактор Н. Бобкова Техред М.Надь, Корректор О. Тигор
Заказ 4786/45
Тираж 783 Подписное
ВНИИПИ Государственного комитета СССР. по делам изобретений и открытий
113035, Москва, Ж-35, Раушская наб., д. 4/5
Филиал ППП «Патент», r. Ужгород, ул. Проектная, 4
Проектировщики печатных плат должны знать эти рекомендации по панелизации. Часть 4
Важные инструкции для разлома плат с перфорацией и мостиками
Вне зависимости от того, как хорошо вы спроектировали массив печатных плат с перфорацией, возможность разрыва или раскалывания слоя паяльной маски или активного поверхностного слоя печатной платы все же существует, если используется плохой метод депанелизации. Ниже приводится безопасный метод разлома перфорированных массивов, для минимизирования и повреждения печатной платы и стрессов, передающихся через поверхность платы компонентам во время разламывания (Рис. 11 и 12).
Важные моменты силы панели в массивах со многими платами
Главные причины заботы об общей силе панели – это избежание вибрации в захватывающем манипуляторе и провисание во время пайки волной или избирательной пайки. Правила, приведенные ниже, могут быть ослаблены на 50%, если панель не будет подвергаться никакой форме пайки для сквозных отверстий. Они также могут быть ослаблены, если панель будет паяться на поддерживающей паллете.
Соблюдение этих правил обеспечить достаточную силу панели, чтобы выдержать нагрузки от обработки.
V-образные канавки или мостики с прорезями между платами создают значительное снижение силы панели. Количество канавок или прорезей между платами должно быть ограничено в зависимости от:
- Материала платы и ее толщины
- Веса деталей, устанавливаемых на плату
- Будут или нет платы проходить через аппараты пайки с использованием жесткой паяльной паллеты.
Панели с многочисленными платами должны проектироваться таким образом, чтобы обеспечить передний и задний края ребер жесткости. Используйте «надрезы за краями», как было описано выше, если это необходимо. Если тяжелые детали должны быть припаяны вручную, так как они не могут выдержать автоматический процесс пайки или они находятся на нижней стороне платы, они не являются фактором в решении о дизайне панели.
Для FR4 или HTFR4 печатных плат больших или равных 0,06 дюймов (1,5 мм) толщины позволяется не более пяти плат сторона к стороне до 0,5 дюймов ширины платы, четырех плат до 2,5 дюймов ширины платы, трех плат до 4 дюймов ширины платы и двух плат шириной до 7,5 дюймов. Платы до 6,65 дюймов длиной могут быть повернуты на 90° на панели и размещены сторона к стороне вдоль длинной оси массива, чтобы вписаться в стандарт 7,25 дюйма шириной. Это имеет смысл только, если итоговая панель длиннее, чем ее ширина, то есть вы можете добавить платы в массив, чтобы эффективно использовать панель производителя (Рис.13).
Вы также можете попытаться повернуть более длинные платы до 10 дюймов длиной на 90°, чтобы наиболее полно использовать панель производителя. Однако, это обычно приводит к избыточному прогибу массива во время автоматической пайки со сквозными отверстиями. Поворот длинных плат более практичен на более толстых, более жестких платах. Когда вы проектируете стандартные 0,09 дюймовые по толщине платы, количество плат в массиве может быть больше, чем в приведенных рекомендациях.
Для FR4 или HTFR4 печатных плат меньших по толщине 0,06 дюйма (1,5 мм) позволительно не более трех плат сторона к стороне при платах шириной до 1,5 дюймов, и двух плат при ширине плат до 3 дюймов. Обратите внимание, что эти панели будут чрезвычайно хрупкими и их нельзя подвергать пайке волной без поддержки на специальной паллете.
Еще одна забота в процессе разработки массива печатных плат для избежания провисания в обрабатывающих машинах — это вес деталей на плате. Если на плате будет тяжелая электроавтоматика (больше чем 1,1 кг) или другие массивные детали, лучше не делать панель из нескольких плат. Две платы с тяжелыми деталями могут быть размещены сторона к стороне, если ширина итоговой панели не превышает 7,25 дюйма. В этом случае лучше взять более толстую плату, скажем, 0,09 дюйма.
Разные соображения
Платы нестандартной формы: платы нестандартной формы могут поворачиваться относительно друг друга, чтобы сократить использование материала ПП, тем самым снижая затраты на плату. Допустимо чередовать платы, 90° до 180° друг от друга, чтобы реализовать экономию материала ПП, если вы не нарушаете правило о том, что мостики разлома должны находиться на одной линии с каждой осью разлома.
Технологические отверстия: Для упрощения тестирования на матричном контактном поле, нужно обеспечить технологические отверстия рядом с любыми тремя углами массива платы на технологических краях. Технологические отверстия обычно 0,125 дюйма 0,004/-0,00, не металлизируются. Также технологические отверстия обычно размещаются в 5 мм от края плат в массиве.
Реперные знаки: Массивы, которые содержат печатные платы с поверхностно монтируемыми деталями должны иметь реперные знаки, обычно рядом с каждым технологическим отверстием. Есть большой выбор форматов реперных знаков, так что вы можете проконсультироваться со своим монтажником, какой из них предпочесть. Края реперных знаков должны быть по меньшей мере в 0,157 дюйма (4 мм) от краев платы, чтобы они не были затушеваны верхними зажимами конвейера в обрабатывающих машинах с системами фото выравнивания. Реперные знаки на технологических краях массива не исключают необходимости наличия реперных знаков на отдельных платах внутри массива.
Заключение
Ни один проектировщик не может себе позволить игнорировать эти правила панелизации печатных плат. Проекты массивов ПП могут оказать серьезное влияние, как положительное, так и отрицательное, на процесс монтажа печатных плат. Различные правила являются комплексными и зависят от геометрии печатных плат, так же как и от ряда возможностей оборудования бесчисленных поставщиков оборудования для монтажа печатных плат. Стоимость печатной платы также значительно зависит от разработки массива.
Приведенные здесь рекомендации не являются неизменными и полными, но они работают для нас в AMETEK и являются хорошей практикой в производстве устройств. Вы всегда должны пытаться связаться со своей службой монтажа печатных плат, чтобы познакомиться с их возможностями и требованиями оборудования. Но так как это не всегда возможно на стадии разработки печатных плат, старайтесь проектировать максимально надежно, чтобы повысить свои шансы получить эффективный процесс сборки.
Источник: electronicdesign.com