Корпус для блока питания своими руками
Когда в наличии имеется станок с ЧПУ и современные электроинструменты, изготовить прозрачный корпус из дерева и оргстекла для блока питания (и прочих изделий) своими руками не так уж и сложно. Но как выходить из ситуации, если подобного оборудования нет, а желание поработать именно с этими материалами есть.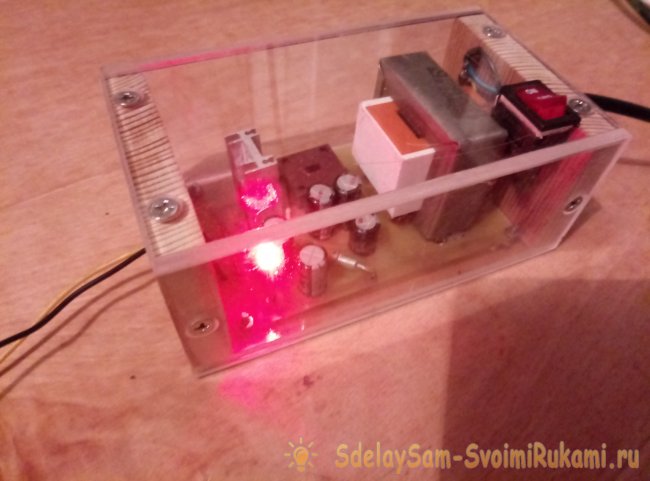
Ниже описан процесс изготовления самодельного прозрачного корпуса для блока питания с применением только простых и доступных инструментов. Также приведено много полезных рекомендаций относительно обработки оргстекла. Вы узнаете, как можно его разрезать, подогнать детали по размеру, просверлить в них отверстия, в том числе, прямоугольные. Наглядно показан один из самых простых способов соединения дерева и оргстекла. Дополнительно есть информация о том, как еще можно скреплять эти материалы между собой.
Инструменты и материалы
Для изготовления самодельного прозрачного корпуса понадобятся следующие расходные материалы:
- прозрачное оргстекло толщиной около 5 мм;
- деревянная доска или фанера толщиной не менее 10 мм;
- саморезы с потайной головкой – 12 шт;
- мелкие болты с гайками – 4 шт;
- прямоугольная кнопка на 250 В и не менее 2 А;
- наждачная бумага зернистостью P100 и P240;
- минеральное или синтетическое моторное масло;
- собранная печатная плата с монтажными отверстиями.
Чтобы из всего вышеперечисленного получилось готовое изделие, следует подготовить такие инструменты и приспособления (специально взяты только доступные и дешевые):
- электродрель;
- сверла по дереву диаметром 3 мм и 10 мм;
- зенкер;
- ножовка по дереву;
- струбцина;
- ножовка по металлу с полотном;
- крестовая отвертка;
- линейка;
- черный маркер.
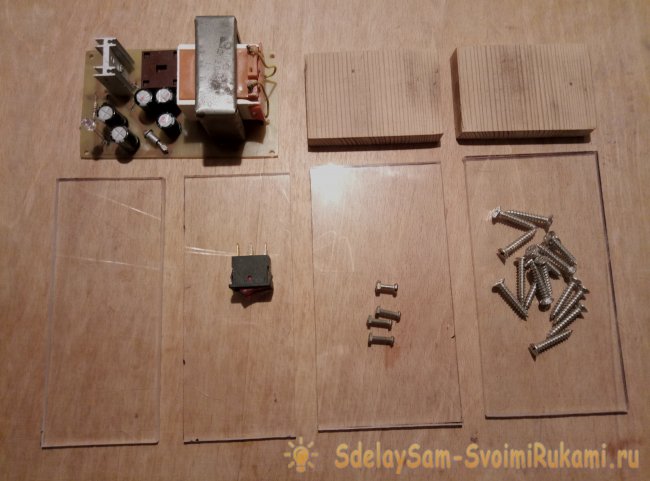
Если в вашем распоряжении есть электрический лобзик, фрезер, шуруповерт и шлифовальная машинка – то все это значительно ускорит процесс изготовления. Однако вполне легко можно обойтись и без этих, довольно дорогих инструментов. Ведь одна из ключевых задач материала заключается в том, чтобы показать, как изготовить прозрачный корпус с применением только бюджетных инструментов.
Изготовление деревянных стенок корпуса
Начнем с самой простой операции, то есть, с изготовления деталей корпуса из дерева, то есть его торцевых стенок. Для этих целей можно взять либо деревянные планки толщиной не менее 10 мм, либо такого же размера фанеру. Подойдут даже остатки какого-либо наличника или же обрезки вагонки. Не рекомендуется использовать ДСП или ОСБ, так эти материалы не очень подходят для изготовления мелких изделий.
Размеры деталей в представленном примере составляют 70x50x10 мм. Естественно, если вы делаете корпус под какое-либо свое изделие, то ширина и высота торцевых стенок подбирается индивидуально. Неизменной желательно оставить только толщину древесины, так как в более тонких заготовках вручную будет затруднительно сделать правильные отверстия.
Выпилить такие простые детали дешевле всего при помощи обычной ножовки по дереву. Для более точной результата рекомендуется использовать стусло и обушковую пилу. На самом деле такие небольшие заготовки можно изготовить даже при помощи ножовки по металлу. Опять же, если у вас есть электрический лобзик – задача только упрощается.
Намного важнее раскройки деревянных заготовок является их подгонка. Они обязательно должны быть абсолютно одинаковыми и, при этом, иметь форму прямоугольного параллелепипеда. Без профессионального столярного инструмента решить такую задачу можно при помощи всего одной струбцины и наждачной бумаги зернистостью P100. Абразив закрепляется на ровной поверхности, а детали соединяются одна с другой и шлифуются до полного сопряжения граней.
Изготовление деталей корпуса из оргстекла
Работа с оргстеклом без всяких там станков с ЧПУ немного сложнее, чем с древесиной. Хоть это довольно податливый, на первый взгляд, материал, но при неправильной обработке он постоянно плавится, пузырится, растрескивается и царапается. Однако и с этими сложностями вполне можно справится, вооружившись информацией, представленной ниже.
В первую очередь, определяемся с размерами деталей. Они подбираются в зависимости от длины и ширины изготовленных из дерева торцевых стенок. Сначала делаются какие-либо две противоположные стороны, затем пара оставшихся. Если кому будет интересно, в примере размеры боковых стенок составляют 140×70 мм, а верхней и нижней — 140×50 мм.
Теперь о резке оргстекла. Самый дешевый и надежный способ раскроя этого материала – использование обычной ножовки по металлу. Также можно выполнить нарезку при помощи специального ножа, самодельных приспособлений, граверов, электрических лобзиков, фрезеров и так далее.
Если, все же, решено использовать ножовку по металлу, то перед выполнением работы нужно усвоить всего пару хитростей, чтобы избежать известных проблем. Во-первых, при таком пилении оргстекло может плавиться из-за трения. Во-вторых, сделанную маркером разметку бывает сложно смыть, особенно, если он перманентный. В-третьих, оргстекло очень легко царапается, что изрядно портит внешний вид готового изделия (как на фотографиях в примере).
Итак, рассмотрим методы решения вышеописанных проблем. Чтобы оргстекло не плавилось при резке полотном по металлу, его необходимо предварительно обработать обычным моторным маслом. Причем, смазывать можно как само полотно, так и линию реза. Если нанести масло на оргстекло, то его будет возможно без проблем разрезать даже электрическим лобзиком, и материал, при этом, не будет расплавляться.
Первое, что приходит в голову по поводу смывки перманентного маркера – это обычный медицинский спирт. Да. Он прекрасно справляется со следами маркера, но тут есть одна неприятность. Дело в том, что, когда спирт попадает на кромку органического стекла, она дает заметные трещины. Чтобы избежать подобных проблем, для нанесения разметки лучше использовать обычный фломастер. Еще лучшим вариантом будет гвоздь, которым легко нацарапать линию реза на оргстекле.
И последний момент. Чтобы защитить акриловое стекло от случайных царапин, перед раскроем и обработкой его стоит заклеить обычным малярным скотчем. В представленном на фото примере этого сделано не было, и результат отчетливо можно увидеть. Хотя все работы выполнялись очень осторожно. Малярный скотч не будет мешать ни распиловке, ни шлифовке, ни сверлению, ни сборке. Да и проблема со следами от маркера исчезает автоматически.
После нарезки деталей из оргстекла их необходимо подогнать по размеру. Делать это тоже можно на наждачной бумаге, закрепленной на ровном основании. Материал, при этом, тоже будет плавиться, но в данном случае маслом лучше не пользоваться. Гораздо эффективнее использовать обычную воду – она отлично охладит оргстекло при шлифовке, не давая ему плавиться.
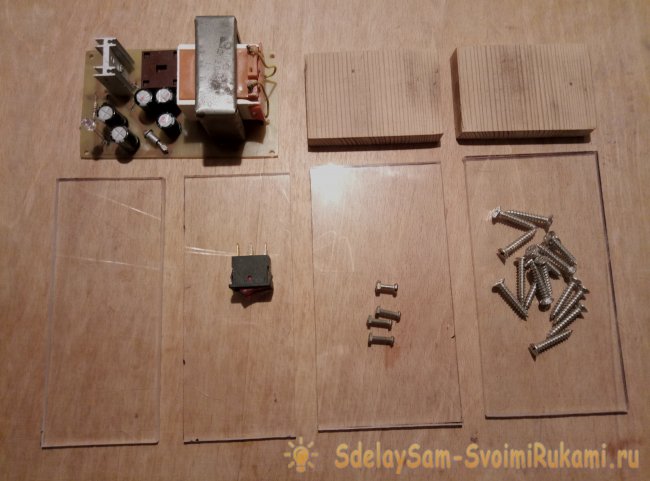
Прямоугольное отверстие в оргстекле
Если с круглыми отверстиями все более или менее понятно, то без специальных инструментов проделать прямоугольное посадочное гнездо для того же выключателя не так просто. Для решения этой задачи есть два способа. Оба простые.
Если есть тот же электрический лобзик (или ручной), то просто сверлим небольшие отверстия по углам будущего гнезда, заводим в одно из них пилочку, и работаем по периметру. Не забываем о смазке. Если лобзиков нету, то берем обычное сверло, диаметр которого максимально приближен к ширине посадочного гнезда на корпусе. Сверлим одно или два отверстия, а затем дорабатываем до прямоугольной формы при помощи обычного дешевого надфиля.
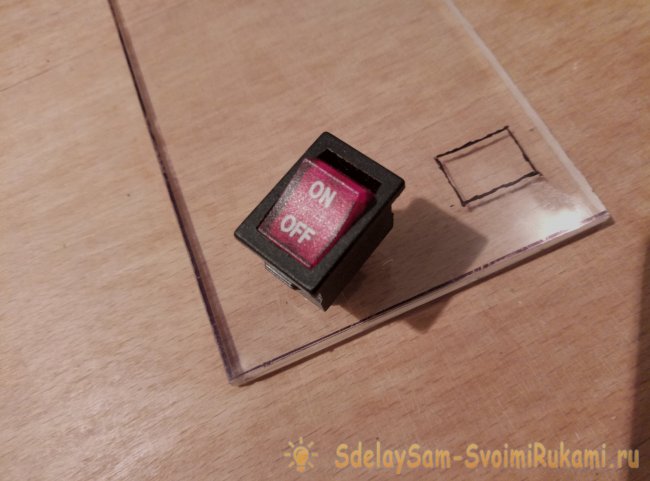
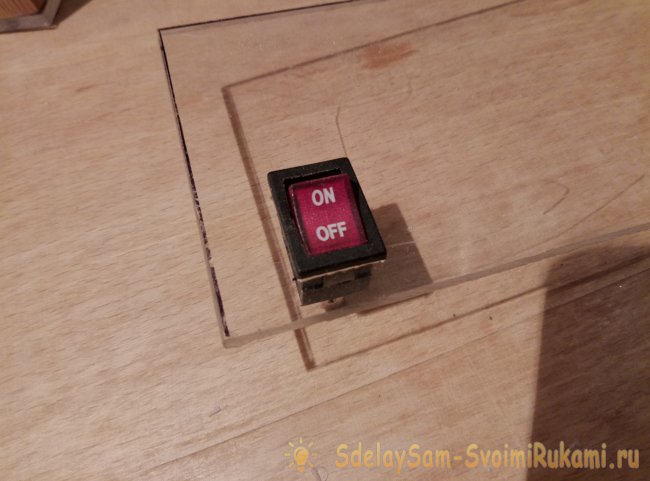
В последнем случае обработка пройдет гораздо быстрее и легче, если оргстекло предварительно неподвижно закрепить. Также стоит сначала работать надфилем под углом 45 градусов с обеих сторон заготовки, а уже потом выравнивать грань под прямой угол.
Сборка корпуса из дерева и оргстекла
Когда все заготовки сделаны, остается только собрать их в одно изделие. Для начала разберем варианты, как прикрепить оргстекло к дереву. Клей в данном случае не совсем подойдет, так как его следы будут видны через прозрачный материал. Смотреться, в итоге, все это будет не очень.
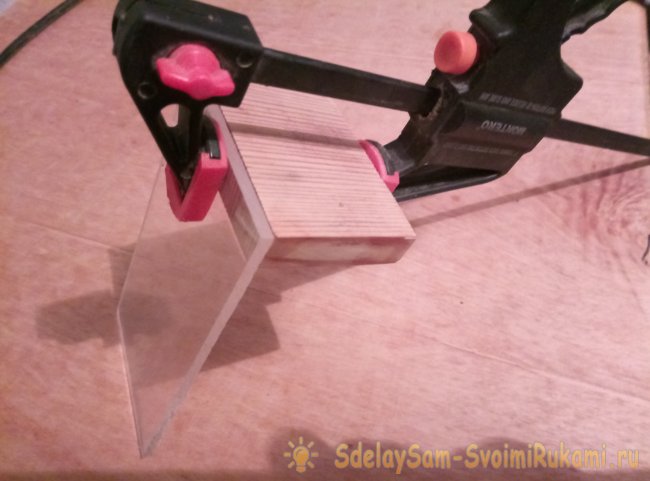
Самый простой подход – саморезы с потайной головкой. Если их распределить симметрично, то внешний вид изделия они не испортят. Для сборки таким способом понадобится дрель, сверло с диаметром, меньшим, чем сами метизы, а также зенкер.
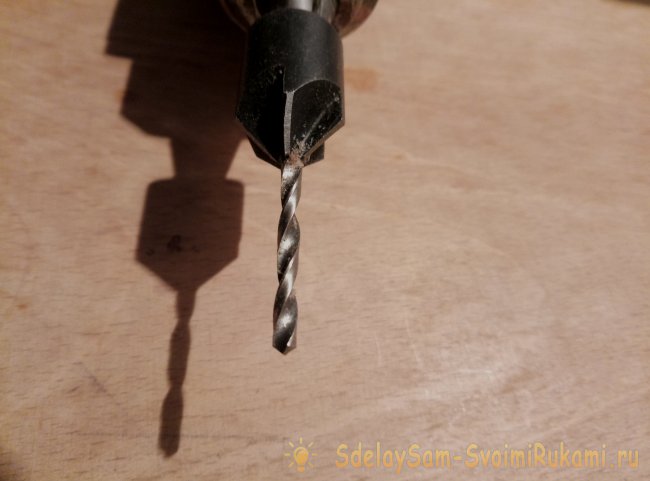
Две смежные заготовки сопрягаются и фиксируются между собой при помощи струбцины. Лучше использовать две маленьких, так как сила сжатия здесь играет большую роль. Дело в том, что при проходе сверла через оргстекло в дерево при слабой фиксации деталей они обязательно смещаются, что недопустимо. Когда отверстия готовы, делаем посадочное место под головку и вкручиваем саморезы. Аналогично поступаем со всеми стенками корпуса.
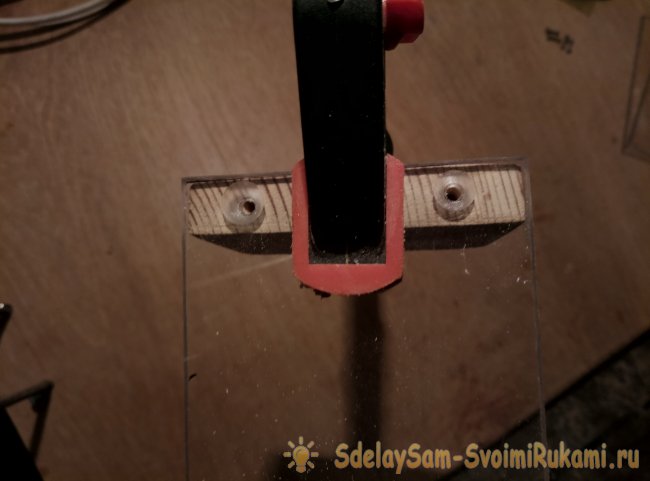
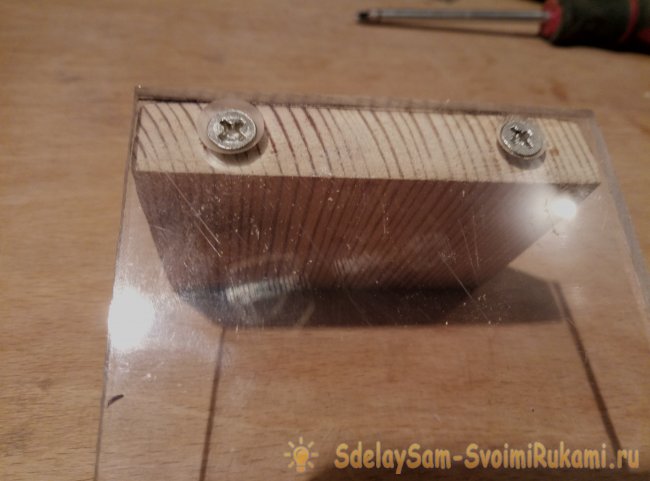
Стоит также отметить, что использование саморезов не всегда является лучшим подходом к решению подобных задач. Такое соединение после нескольких сборок и разборок потеряет прочность. Потому его стоит использовать только в тех случаях, если ваш прибор не будет часто вскрываться.
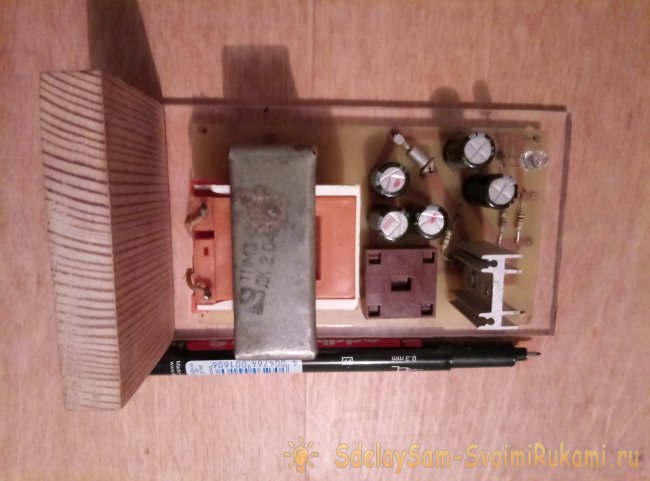
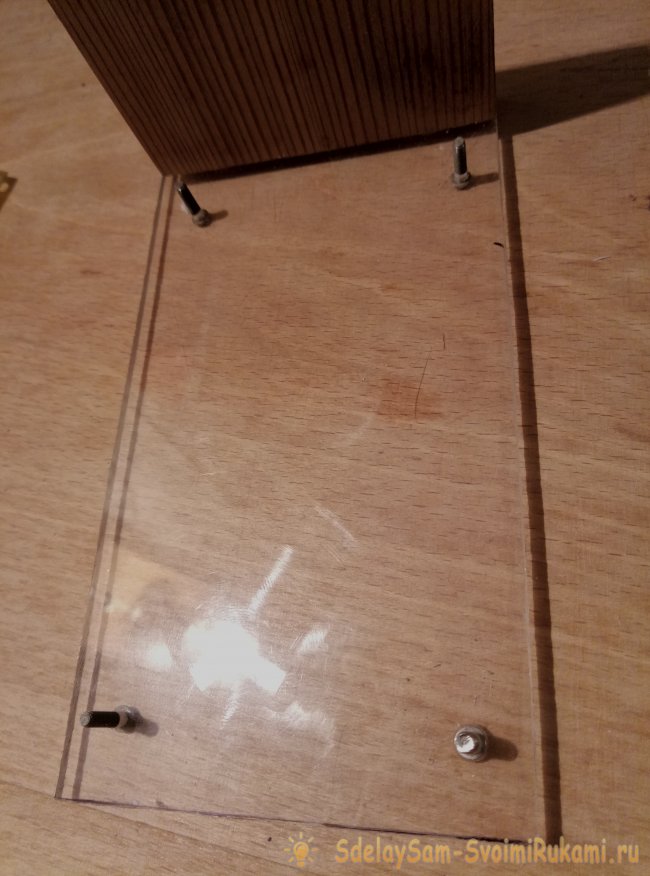
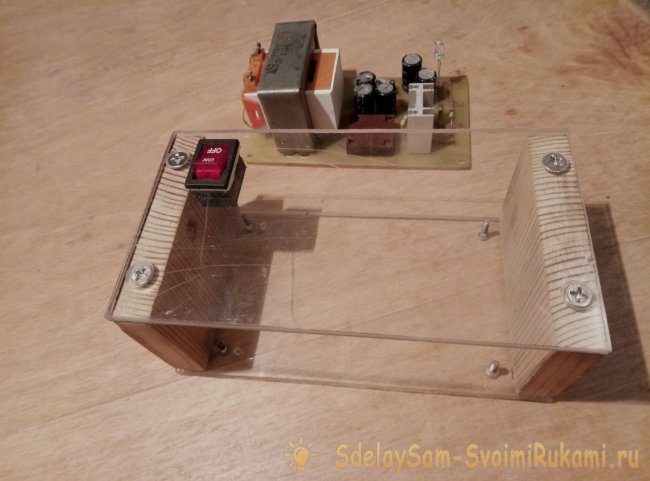
Если же нужен прозрачный корпус с возможностью бесконечной разборки, то вместо саморезов применяйте специальные резьбовые втулки и винты с потайной головкой. В таком случае сначала в дерево вкручиваются втулки, а уже в них ввинчиваются винты. Такое соединение абсолютно не уступает саморезам по прочности, а вот по функциональности выигрывает в разы.
После пробной сборки корпуса остается только интегрировать в него начинку. Для крепления печатной платы в дне делаются отверстия, а для ее фиксации используются болты с гайками. Если есть специальные радиомонтажные стойки с соответствующими резьбами, то предпочтительнее использовать их. Показанная в примере кнопка фиксируется сама. Дополнительно предусматриваем выходы под провода или отверстия для разъемов, и собираем все согласно схемы. Если есть желание, то добавляем резиновые или пластиковые ножки.
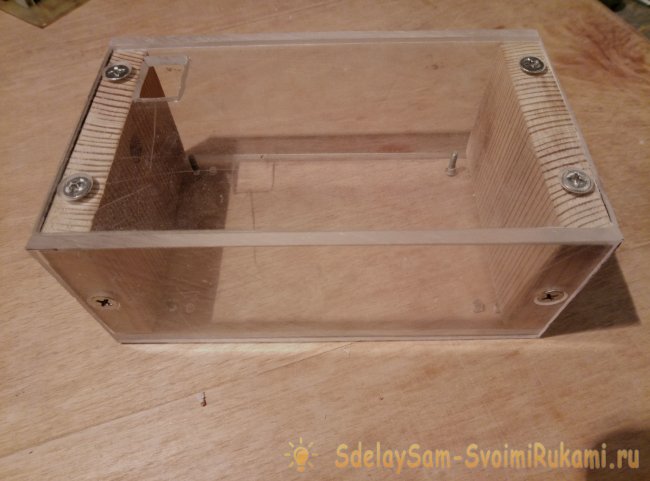
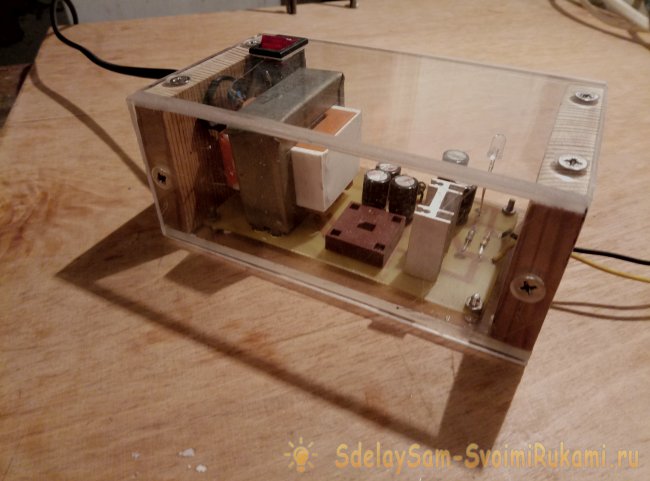
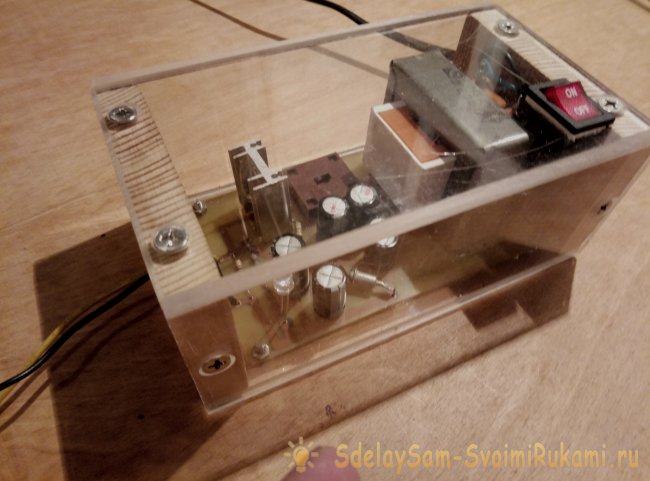
Посмотрите, насколько просто изготовить самодельный корпус для электронной самоделки своими руками
Перевёл alexlevchenko для mozgochiny.ru
У каждого радиолюбителя, который погружается в мир электроники, рано или поздно возникает желание оформить свои электронные поделки в красивые корпуса. При этом возникает проблема выбора. Обычно их размеры очень ограничены, а качество оставляет желать лучшего. Корпуса же хорошего качества стоят очень дорого. Поэтому у меня появилась мысль, а почему бы не начать
Порывшись в интернете, к большому сожалению, не нашёл ничего толкового. Все мануалы сводились к тому, что если у вас есть лазерный резак, сделать элегантные коробки из плексигласа не составит большого труда.
Но так как у меня, как и у большинства читателей, нет лазерного резака, принял решение разработать технологию изготовления самодельных корпусов, используя для этого доступные ручные инструменты.
Они получились не такими уже и элегантными, как если бы я использовал лазерный резак, но зато достаточно крепкими.
- Акриловый клей, но если нет возможности «достать» его, можно использовать супер-клей;
- Нож-резак для оргстекла;
- Наждачная бумага и надфиль;
- Металлическая линейка;
- Тонкий маркер.
Прежде всего, нужно определить размеры изготавливаемого корпуса (в моём случае 10 х 6,35 х 6,35 см).
Разметим плексиглас в соответствии со схемой.
В качестве направляющей будем использовать старое ножовочное полотно. Резак должен идти перпендикулярно поверхности оргстекла. Процарапаем (прорезаем) примерно половину от общей толщины. Затем доломываем его осторожным движением. Зачистим край среза наждачной бумагой или надфилем.
Вырежем все шесть сторон. Лучше сделать их немного больше, уменьшить их мы всегда успеем.
Отшлифуем заготовки. Они должны быть с прямыми углами и перпендикулярными сторонами.
Воспользуемся изолентой, чтобы собрать детали корпуса воедино. Проклеим все стыки клеем, но без фанатизма, пролитый лишней клей в дальнейшем может «вылезти боком».
Из-за того, что не учёл толщину оргстекла, торцевые стеночки получились меньшего размера.
Примечание: во избежание трудностей при монтаже, учитывайте толщину материала.
Независимо от того, насколько сильно вы будете стараться, у вас все равно не будет идеальных кромок. Поэтому хорошенько обработаем края, сделав их, как можно более ровными.
В случае, если клей попадёт на внешние поверхности, придётся приложить достаточно усилий, чтобы сошлифовать остатки клеевого состава.
Для того, чтобы закрепить крышку на корпусе необходимо изготовить опоры. Возьмём кусок толстого оргстекла, вырежем четыре кубика, а затем отшлифуем их края. Вклеим их ниже уровня верхней кромки, чтобы она располагалась заподлицо со сторонами короба. Установим крышку, просверлим четыре отверстия, а затем вкрутим в них шурупы.
БлагоДарю вас за просмотр и искренне надеюсь, что эта статья поможет вам при изготовлении собственных поделок. МозгоЧины, а какие вы корпуса используете для своих электронных самоделок?
(A-z Source)
ПОДЕЛИТЕСЬ С ДРУЗЬЯМИ!
About alexlevchenko
Ценю в людях честность и открытость. Люблю мастерить разные самоделки. Нравится переводить статьи, ведь кроме того, что узнаешь что-то новое — ещё и даришь другим возможность окунуться в мир самоделок.Оформление корпуса в домашних условиях. — Технологии — Практика
Евгений Князев
Привет ВСЕМ! Многие радиолюбители, после того как сделали очередную свою поделку, встают перед дилеммой – куда всё это «впихнуть», да и так, чтобы потом людям не стыдно было показать. Ну с корпусами допустим в настоящее время, это не такая уж и большая проблема. Сейчас можно встретить в продаже много готовых корпусов, или использовать для своих конструкций подходящие корпуса от какой либо вышедшей из строя и разобранной на детали радиоаппаратуры, так же применять в своих поделках строй материалы или вообще, что под руку попадет.
Я постараюсь здесь коротко описать, как делаю передние панели к своим поделкам в домашних условиях.
Для разработки и отрисовки передней панели, я пользуюсь бесплатной программой FrontDesigner_3.0. Программа в пользовании очень простая, всё становится понятно сразу, в процессе работы с ней. В ней имеется большая библиотека спрайтов (рисунков), она — это что то наподобие Sprint Layout 6.0.
Как я делаю свои панели:
1 — Предварительно продумываю и расставляю по местам то, что будет у меня установлено на передней панели в моей конструкции. Так как передняя панель представляет из себя своеобразный «бутерброд» (оргстекло – бумага – металл или пластик) и этот бутерброд необходимо между собой как-то скрепить, то пользуюсь принципом — чем всё это будет держаться и в каких местах. Если крепёжные винты на панели не предусмотрены, то для этой цели остаются только гайки крепления разъёмов, переменных сопротивлений, выключателей и других крепёжных элементов.
Все эти элементы стараюсь распределить на панели равномерно, для надёжного крепления всех её составных частей между собой и крепления самой панели на корпусе будущей конструкции.
Как пример — на первом фото крепёжные места будущего блока питания, обвел красными прямоугольниками — это у меня сопротивления переменные, гнезда типа «банан», выключатель.
На втором фото, второго варианта исполнения блока питания – все аналогично. На третьей фотографии следующего варианта передней панели – это держатели LED, энкондер, гнезда, выключатель.
2 — Потом рисую в программе FrontDesigner_3.0 переднюю панель и распечатываю на принтере (дома имеется ч/б принтер) так сказать черновой вариант.
3 — Из оргстекла (еще его называют акриловое стекло или просто акрил) вырезаю заготовку для будущей панели. Беру оргстекло в основном у рекламщиков. Иногда они его и так отдают, а иногда приходится брать и за деньги.
4 — Дальше на распечатанном черновом рисунке платы, размечаю центры всех будущих отверстий и шилом делаю проколы в в них.
5 — Потом через эти проколы, маркером делаю разметку на акриле (оргстекле) и на корпусе своей будущей конструкции.
6 — Также на корпусе делаю разметку под все другие имеющиеся отверстия на панели, на индикаторы, выключатели и прочее…
7 — А как же закрепить на передней панели, или корпусе конструкции индикатор или дисплей?? Если корпус конструкции изготовлен из пластика, то это не проблема – просверлил отверстие, раззенковал, поставил винты с потайной головкой, опорные шайбы под дисплей (или трубочки) и всё, проблема решена. А если металл, да ещё тонкий? То тут так не прокатит, идеально ровную поверхность под передней панелью таким способом не получить и внешний вид уже будет не тот.
Можно конечно попробовать посадить винты с обратной стороны корпуса и на термо клей или приклеить «эпоксидкой», кому как нравится. Но мне так не нравится, как то уж слишком по-китайски, для себя же любимого делаю. Поэтому здесь я поступаю немного иначе.
Беру подходящие по длине винты с потайной головкой (такие легче паять). Места крепления винтов и сами винты залуживаю припоем (и флюс для пайки металлов), и припаиваю винты. С обратной стороны получается может не очень эстетично, зато дешево, надёжно и практично.
8 — Потом, когда всё готово и все отверстия просверлены, вырезаны и обработаны, распечатывается рисунок панели на цветном принтере у себя дома (или у соседа). Можно распечатать рисунок там, где печатают фотографии, предварительно нужно экспортировать файл в графический формат и подогнать его размеры под предполагаемую панель.
Далее собираю весь этот «бутерброд» воедино. Иногда, чтоб не было видно гайки от переменного сопротивления, приходится чуть спиливать его шток (стачивать вал). Тогда колпачок садится глубже и гайки из под колпачка практически не видно.
9 — Вот посмотрите некоторые экземпляры передних панелей моих конструкций, часть из которых изображена ещё и в начале статьи под заголовком. Может конечно не «супер-пупер», но вполне прилично, и показать друзьям будет не стыдно.
P.S. Можно сделать немного проще и обойтись без оргстекла. Если не предусмотрены цветные надписи, то можно распечатать рисунок будущей панели на чёрно белом принтере, на цветной или белой бумаге, или, если рисунок и надписи в цвете — то распечатать на цветном принтере, потом всё это дело заламинировать (для того, чтобы не так быстро залапывалась бумага) и приклеить её на тонкий двухсторонний скотч. Потом уже всё это дело крепится (приклеивается) на корпус устройства на место предполагаемой панели.
Пример:
Была использована для передней панели старая печатная плата. На фотографиях видно, каким был начальный вариант конструкции, и каким он стал в конце.
Или вот ещё пара конструкций, где передняя панель изготавливалась по такой же технологии
Ну вот, в принципе и всё, что я хотел Вам рассказать!
Конечно, каждый сам для себя выбирает доступные ему пути в своём творчестве, и ни в коем случае я не навязываю Вам принимать мою технологию за основу. Просто может быть кто то возьмёт её, или какие то её моменты себе на вооружение и просто скажет мне спасибо, и мне будет приятно, что мои труды кому то пригодились.
С уважением к Вам! (Tyzik)
Корпус домашнего лабораторного блока питания из старого компьютерного корпуса
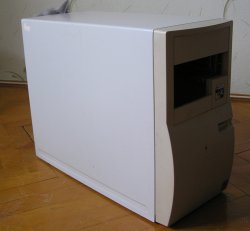
Давно хотел поменять свой морально и физически устаревший лабораторный блок питания. Рыскал в Интернете в поисках схемы. Схема была найдена, все детали куплены. Встал вопрос корпуса, для меня проблема корпусов, всегда была проблемой номер один.
Но решение пришло неожиданно, оно (решение) уныло стояло в подъезде в ожидании своей участи. Это был старый компьютерный корпус формата АТ.
В отсутствии супруги корпус был принесен домой, отмыт и пропылесосен.Вся начинка была вытащена и сложена на полку. Далее наступил момент определиться с размерами будущего корпуса. Предполагается, что блок питания будет однополярным и размеры были выбраны с оглядкой на заводские аппараты. В результате готовый корпус получился следующих размеров 255×176×152. В нем свободно разместится 100 ватный трансформатор и все платы. Далее привожу фото-отчет о проделанной работе.
Техника безопасности: использовать х/б перчатки, т. к. края штамповки с заусеницами, возможны порезы.
Высверлил соединительные заклепки сверлом на 4. Разобрал корпус на составляющие части.
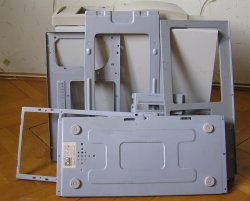
Раскройка заготовок. Красная линия — линия разреза, крестом отмечены не используемые части. Дно с ножками. Вторая пара ножек уже перенесена на рабочую часть.
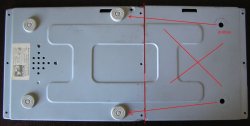
Задняя стенка. Было решено использовать верхнюю часть заготовки.

Передняя стенка.
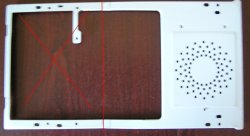
Верхняя часть для придания жесткости конструкции.
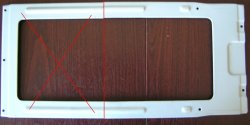
Вставка в заднюю стенку, вырезается из блока питания. Сразу убиваем двух зайцев, есть гнездо для подключения сетевого шнура с заземляющим контактом и вентилятор.
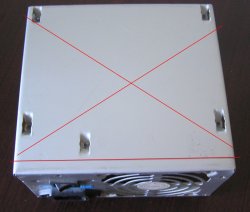
Лишнее отверстие в задней стенке закроем боковой частью корпуса блока питания, вырезав ее по контуру нашего отверстия.
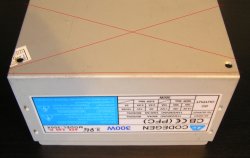
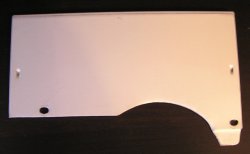
Верхняя крышка корпуса вырезана ножницами по металлу и крепится 4-мя штатными саморезами. Задние кромки подогнуты для скрытия щелей. Ровно согнуть не получилось, посему присутствуют косяки.
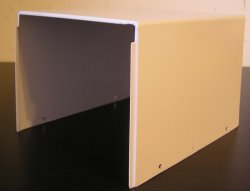
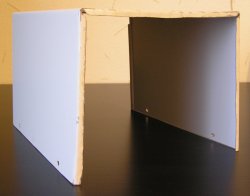
Все элементы каркаса скреплены между собой с помощью болтов М3 и гаек. В идеале хорошо бы использовать заклепки, но чего нет — того нет. Для крепления верхней части использованы 4 уголка 25×25, купленные в строительном магазине.
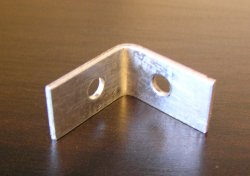
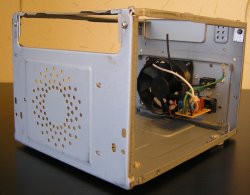
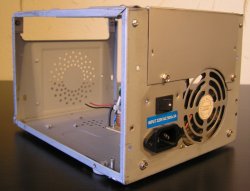
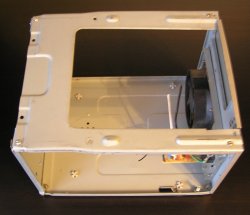
Заготовка лицевой панели, вырезана из штатной панели корпуса. Нижняя кромка приклеена дихлорэтаном.
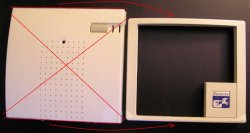
Дизайн лицевой панели еще не придуман, но скорее всего будет похожа на панели в заводских моделях.
В результате сборки получилось следующее:
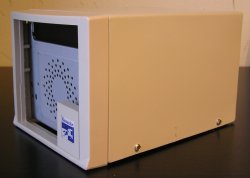
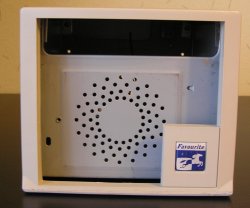
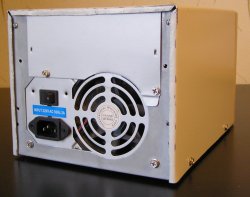
В итоге имеем корпус, сделанный по своему вкусу и фактически без финансовых затрат.
Надеюсь, что моя идея пригодится кому-либо в ваших самоделках.
Спасибо за внимание!
Камрад, смотри полезняхи!

Михаил (Dust112)
Россия
О себе автор ничего не сообщил.
Простой лабораторный блок питания
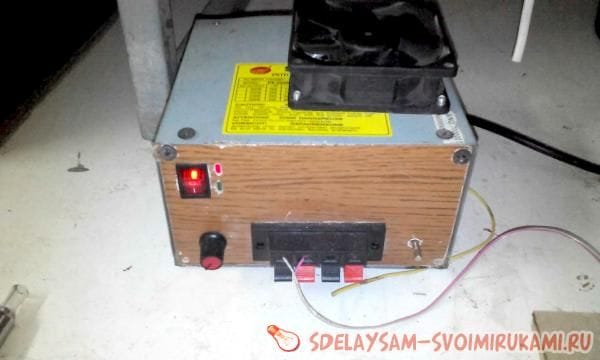
В этой статье будет детально разобрано и показано на примере как и из каких деталей можно собрать простенький лабораторный блок питания. Довольно часто радиолюбители сталкиваются проблемой получения определенного напряжения для запитывания различных самодельных устройств, с такой же проблемой столкнулся и автор данной самоделки, которая как раз и позволяет решить проблемы подобного рода.
Материалы и инструменты, которые использовались автором для создания простейшего лабораторного блока питания:
1) Для плат блока питания необходим корпус, его можно приобрести в магазинах электроники, либо как и автор взять от ненужного компьютерного блока питания.
2) Так же необходим трансформатор с напряжением на выходе до 30 В и силой тока 1.5 А. Мощность трансформатора стоит рассчитывать из того, какие именно границы напряжения вы хотите сделать для данного блока питания.
3) Диодный мост на 3 А
4) конденсатор электролитический 50 В 2200 мкф
5) конденсатор керамический на 0.1 мкф, он будет нужен, чтобы сгладить пульсации.
6) Микросхема LM317 (автор использовал 2 таких микросхемы в своем блоке питания)
7) Резистор переменный на 4.7кОм.
8) Резистор на 200ом 0.5Ват.
9) Конденсатор керамический на 1мкф.
10) В качестве вольтметра автор использовал имеющийся у него старый аналоговый тестер.
11) Текстолит и хлор железа, который будет нужен для травления платы.
12) Клеммы
13) Провода
14) Паяльная лампа и паяльные принадлежности.
15) ДВП либо пластик
16) дрель
Рассмотрим основные этапы создания и конструктивные особенности лабораторного блока питания собранного автором.
Первым делом автор взял корпус от ненужного блока питания компьютера и занялся подготовкой его к использованию в качестве корпуса для своей самоделки. Для этого корпус был разобран и из него были вытащены внутренности. Затем автор отпилил переднюю панель, с которой выходят провода.
Все это показано на фотографиях приведенных ниже:
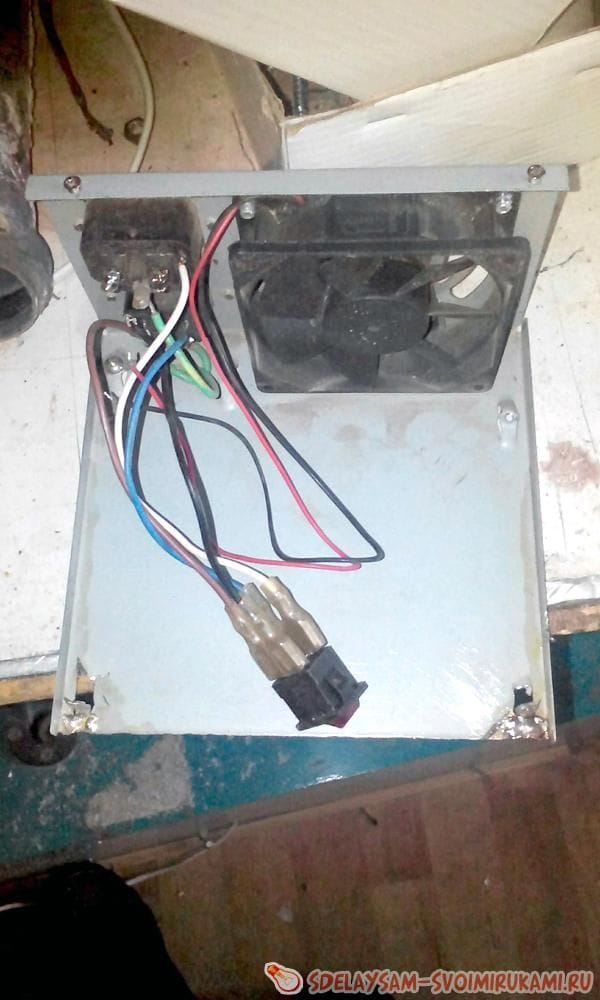
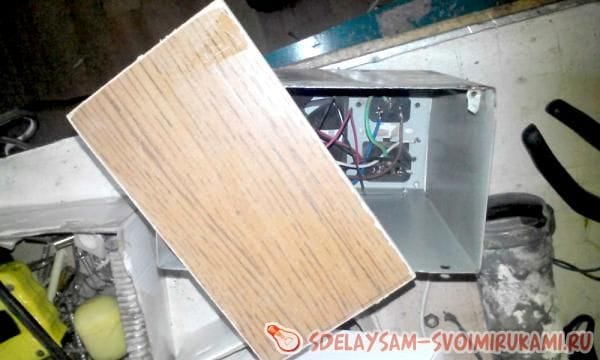
После этого корпус блока питания был собран обратно. Чтобы сделать переднюю панель для лабораторного блока питания автор использовал ДВП, из которого вырезал небольшую дощечку, которая была подогнана по размерам для корпуса. При желании панель можно так же сделать и из пластика, что может положительно сказаться на внешнем виде устройства.
Далее автор отрезал крепления платы с одной из сторон и выгнул их так, чтобы имелась возможность в последующем закрепить на них подготовленную переднюю панель.
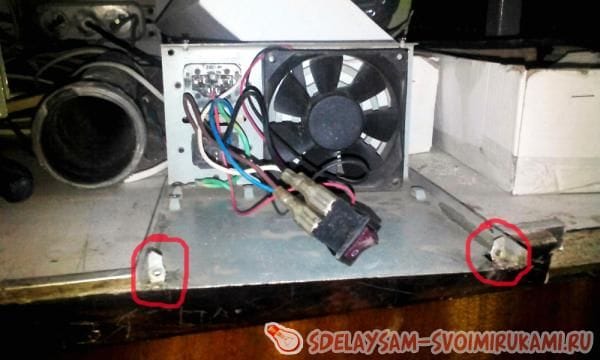
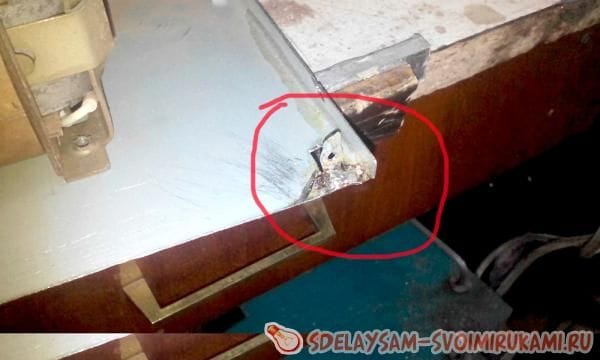
Затем автор приступил к созданию места под трансформатор. Для этого при помощи дрели были просверлены отверстия в нижней части корпуса, через которые и будет крепиться трансформатор.
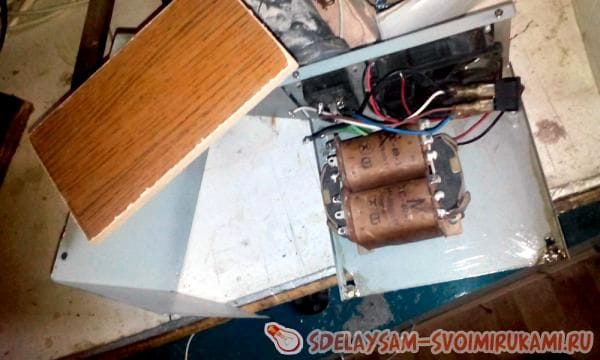
После этого автор приступил к созданию платы для устройства. Для начала ее было необходимо вытравить. Для этого заранее распечатанная плата была перенесена на текстолит, после чего она была кинута в хлорное на 15 минут. После того как плата была вытравлена, автор приступил к сверлению отверстий и лужению платы.
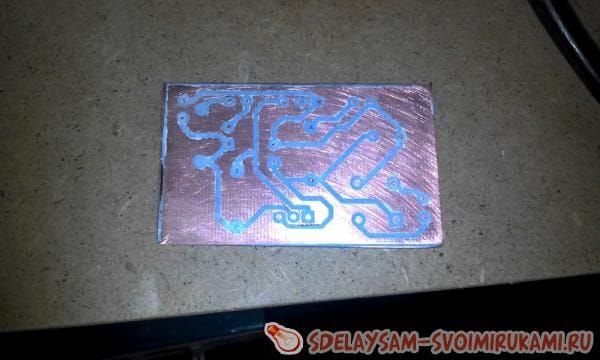
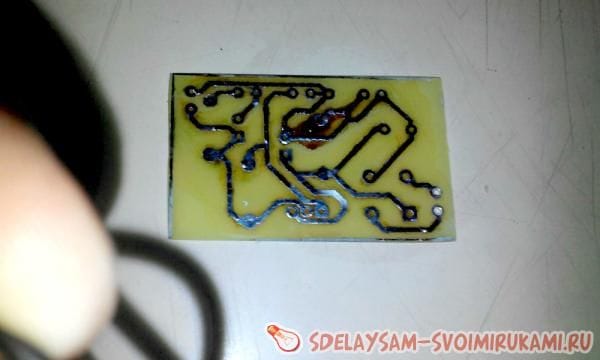
Далее автор приступил к пайке элементов согласно схеме устройства, которая приведена ниже.
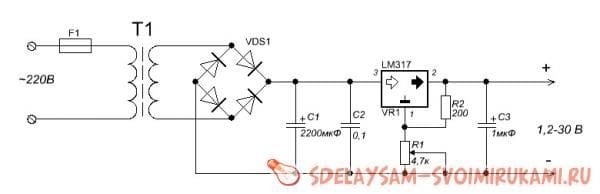
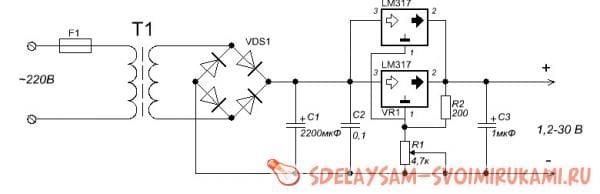
Далее припаивались провода и производилась сборка всей схемы в единый корпус. Очень важно внутреннее расположение сделать таким образом, чтобы микросхема была установлена на радиатор, так как при сильных нагрузках она может прилично нагреваться и без должного охлаждения быстро придет в негодность.
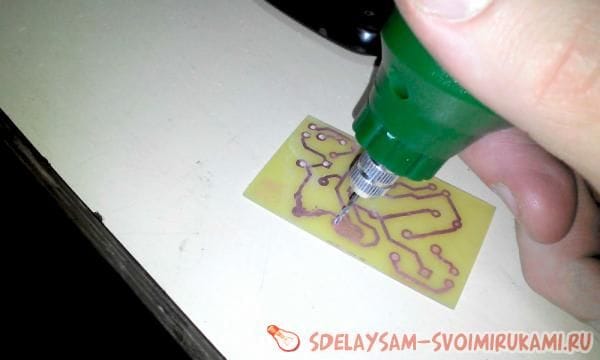
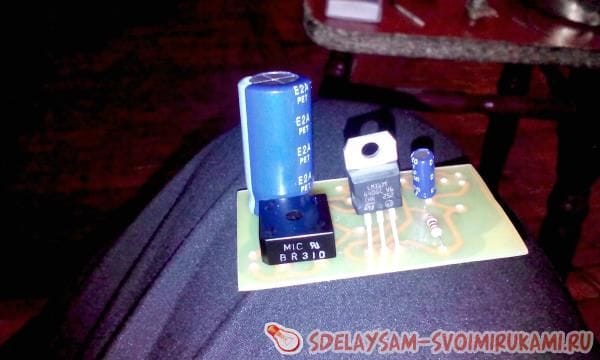
По сути прибор полностью собран и готов к использованию, но для начала необходимо провести испытания, чтобы убедиться в правильной работе блока питания и при необходимости устранить его недостатки.
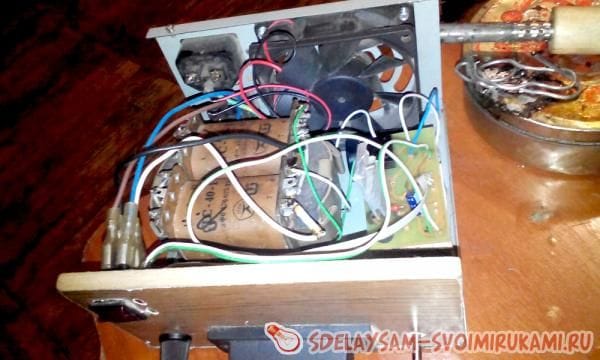
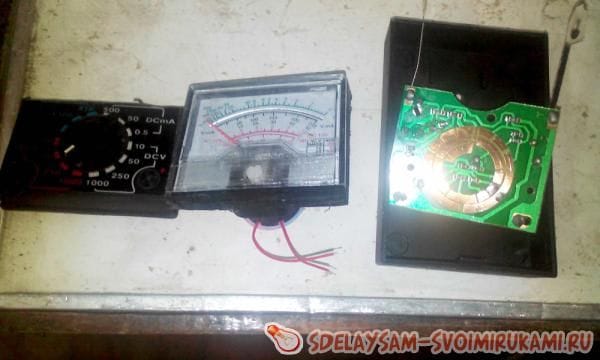
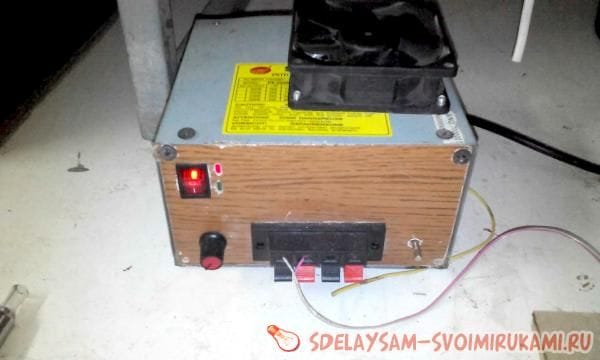
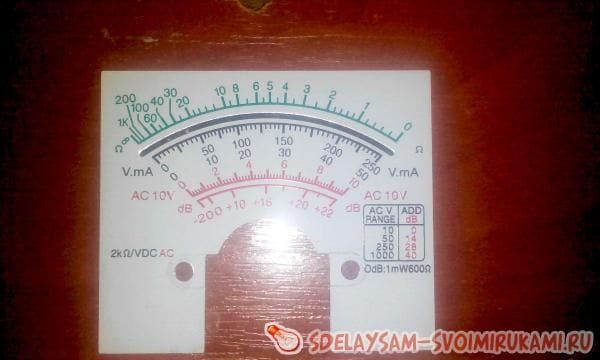
Далее автор занялся переделкой старого тестера в вольтметр. Чтобы это сделать автор просто отрезал сам индикатор от пластикового корпуса, после чего
установил перемычку на плате тестера в диапазоне 50 В. Затем автор вырезал в передней панели устройства отверстие под получившийся вольтметр и подключил все необходимые провода. После чего плата была изолирована.
После окончательной сборки корпуса автор решил установить вентилятор сверху устройства, чтобы осуществлять обдув радиатора и охлаждать микросхему закрепленную на нем.
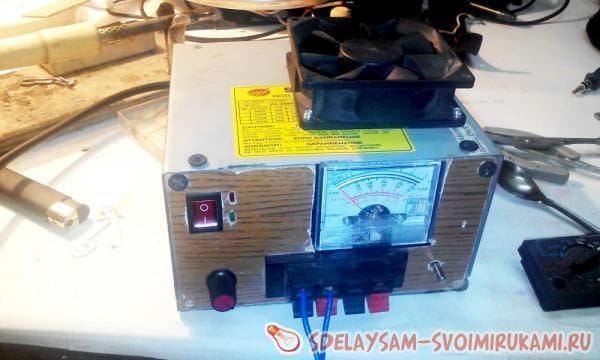
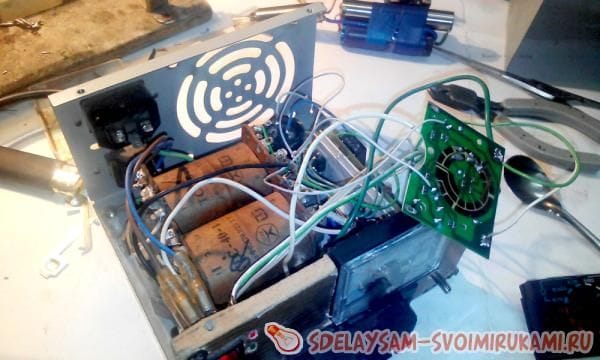
После всех этих действий получился неплохой лабораторный блок питания с довольно простой конструкцией и сборкой.
Источник
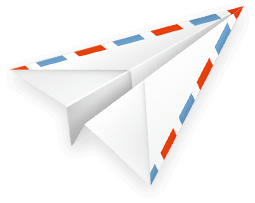
Получайте на почту подборку новых самоделок. Никакого спама, только полезные идеи!
*Заполняя форму вы соглашаетесь на обработку персональных данных
Становитесь автором сайта, публикуйте собственные статьи, описания самоделок с оплатой за текст. Подробнее здесь.Как разобрать корпус блока питания от ноутбука
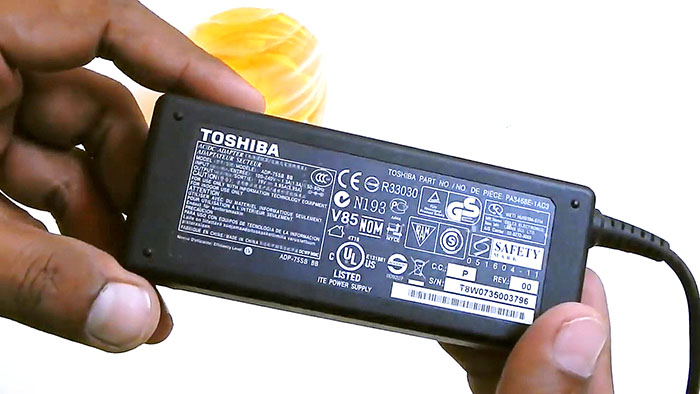
Корпус адаптера питания ноутбука склеивается из двух частей специальным клеем и не имеет никакого другого крепежа. Если случилось несчастье, и блок питания сломался, то для его ремонта его необходимо прежде всего разобрать. А как это сделать если он не разборный? Долгое время при разборке я просто ломал корпуса, но оказывается все гораздо проще, чем может показаться. И открыть такой блок без повреждения не так уж и трудно.
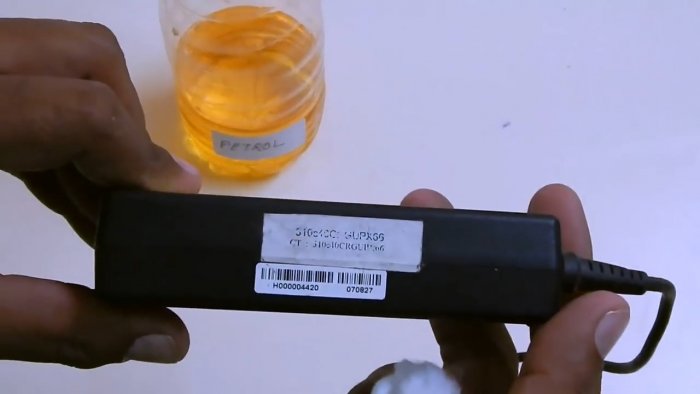
Как видите оболочка полностью почти герметична. Никаких каналов или углублений нет. Такие блоки часто разбираю не только для ремонта, но и для пополнения радиоэлектронных запасов своей мастерской, ведь там есть что взять.
Понадобится
- Вата или ватный тампон.
- Обычный бензин любого октанового числа. Также неплохо себя зарекомендовал 646 растворитель.
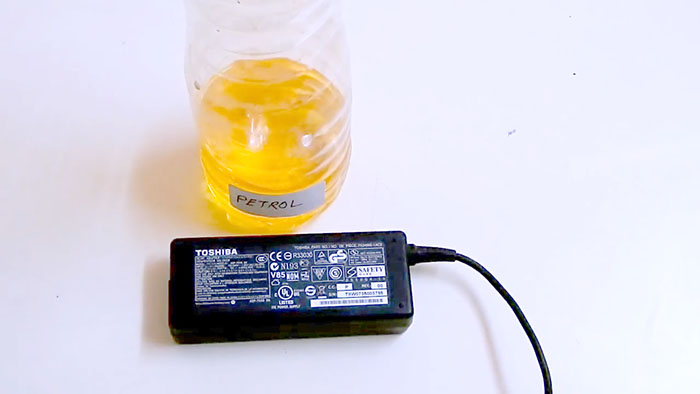
Разбираем склеенный корпус блока питания
Суть данного метода заключается в отмачивании соединительного клея растворителем. Для этого смачиваем вату в бензине и протираем шов между частями корпуса.
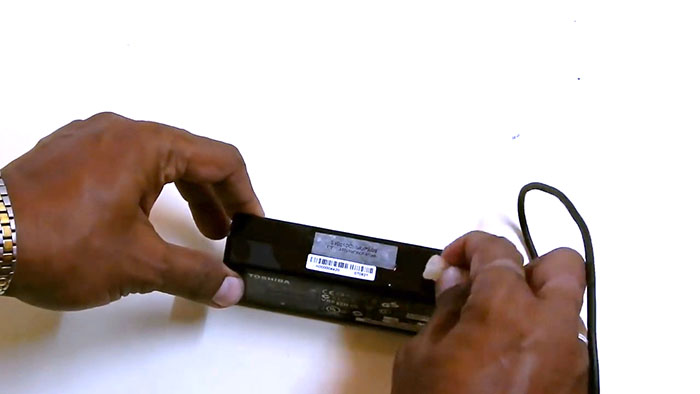
Смачиваем обязательно обильно, чтобы растворитель проник во все поры. Переворачиваем блок на другую сторону и повторяем процедуру с другой стороной.
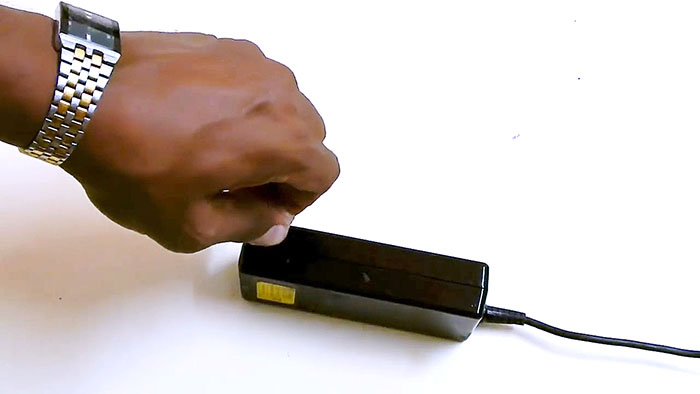
Необходимо пройти весь корпус по периметру.
Затем оставляем отмыкать клей минут на 10-15. А затем обмазываем швы повторно и также ждем отмыкания.
По истечении времени, очень аккуратно, пробуем раскрыть блок.
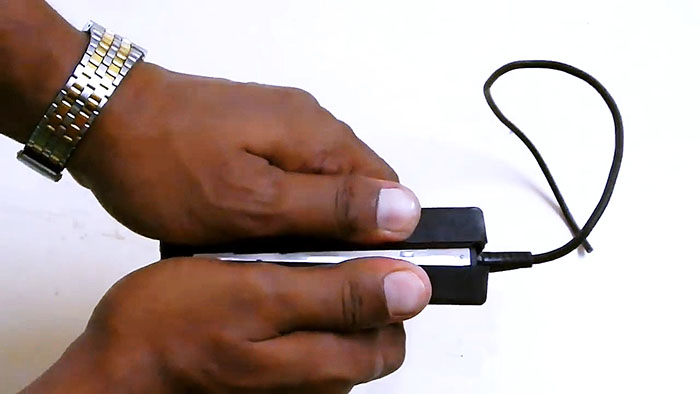
Торопиться не нужно, не на всех участках клей успел отойти. Если вдруг, случилось так, что движения никакого нет, будьте особо осторожны — подковырните скальпелем.
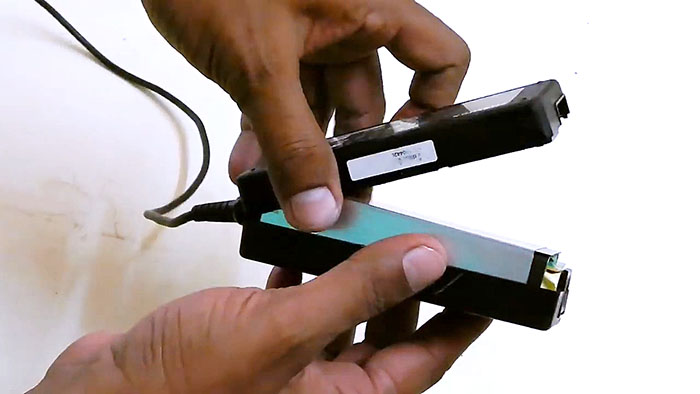
И вот наконец-то все открылось без повреждений.
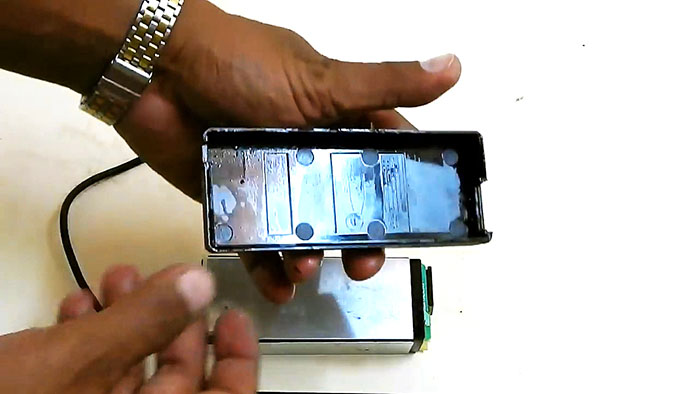
Теперь можно производить ремонт или просто извлекать нужные детали про запас.
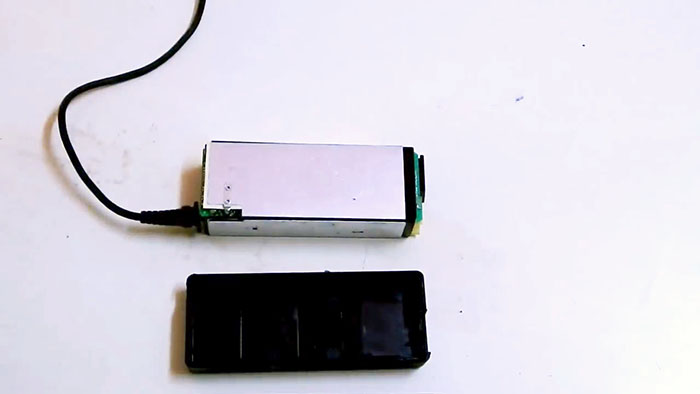
Обязательно все процедуры с бензином (растворителем) проводите в хорошо проветриваемом помещении, иначе можно получить отравление.
Заключение
Такие корпуса так же используются для блоков питания мониторов, принтеров, видеокамеры и т.д. Этот несложный метод поможет вам добраться до внутренностей без лишних сложностей.
Смотрите видео
Печатаем простейший корпус для самодельного устройства / Habr
Напечатать подходящий корпус для своего устройства — это наверно самая популярная мысль при знакомстве любого изобретателя с технологией 3д печати. Но на практике всё оказывается не так просто как в рекламе 3д-принтера и под катом я немного подробней расскажу к каким выводам я пришёл в попытках сочинить удобную конструкцию корпуса.
С 3д-печатью прекрасно всё — это просто волшебная палочка для мастера, за исключением того, что большинство смогут позволить себе только модели принтеров нижнего ценового диапазона. И после завладения 3д принтером большинство, как и я, столкнутся с несовершенством технологии бюджетной 3д печати, а именно технологии FDM(послойное наплавление – использует большинство доступных принтеров), вне зависимости от того собрали вы принтер сами или купили в магазине. Основные проблемы заключаются в усадке материала после остывания, что является причиной деформаций и не точных линейных размеров напечатанных деталей. Если вы придумали какой- то раскрутейший дизайн по подобию корпусов серийной техники, то корпус вашего устройства будет щедро насыщен аккуратными фасочками, дырочками или защёлками точно в размер для удобства сборки… даже будучи профессионалом в моделировании и учитывая перечисленные выше проблемы при печати, вы устанете сводить все эти размеры и придумывать в каком положении лучше печатать каждую деталь, чтобы ничего не выгнуло при усадке, как это часто бывает. Усадка зло, особенно это расстраивает и отнимет время, когда в вашей конструкции оказывается много размеров, которые нужно точно выдержать для сборки и красивого вида. Но не всё так плохо и это не повод отступать).
На основе своего опыта печати, я придумал простую конструкцию коробочки для прототипов устройств, которая будет удобна в печати на любом фдм принтере и подойдёт для многих проектов.
Конструкция состоит из двух частей: шасси — на котором будем монтировать детали, и собственно кожуха – который спрячет весь тот срам что мы напаяли) Одно легко вставляется в другое и для надёжности закрепляется единственным шурупом сзади корпуса.
Шасси печатается в горизонтальном положении, чтобы легко выдержать горизонтальные размеры посадочных мест под установку компонентов. Потом я их просто подклеиваю по углам капельками горячего клея, так быстрее и проще потом разбирать в случае необходимости.
Шасси я рекомендую щедро издырявить снизу и боков для экономии материала, меньшей деформации при усадке и упрощения отдирания от стола. Просто выдавливаю круги, помните что такое баблинг?)
А кожух я печатаю вертикально. В таком положении можно делать тонкие ровные стенки и текстура почти на всей видимой части корпуса получается в одном направлении, выглядит аккуратно. По необходимости можно дорисовать ушки крепления или ножки.
Даже если вы не сможете с первого раза точно выдержать размер и вам придётся немного сточить грани шасси напильником, следов обработки совершенно не будет видно с наружи устройства.
Конические ножки на нижней части корпуса печатаются без поддержек, что избавляет от последующей обработки и экономит материал/время.
Если вы печатаете на скотч или клей, поверхность которая прилипает к столу как правило получается не ровной и требует обработки. При таком подходе она окажется с задней стороны корпуса(со стороны интерфейсных разъёмов), которую один фиг никто обычно не видит.
Этот корпус я печатал из PLA пластика соплом 0,3мм на принтере российского производства MZ3D-256 со следующими настройками структуры: толщина стенок 0,6мм, заполнение 23%, без печати подложки.
Размер корпуса в моём примере позволяет разместить внутри ардуину уно, пару реле, драйвер шагового двигателя, преобразователь напряжения, различные коммуникационные разъёмы и элементы управления/индикации.
Вы конечно нарисуете шасси необходимого размера под свои модули, лишь бы хватило области печати принтера, чтобы напечатать кожух цельным. На мой взгляд наиболее простой и удобной будет именно такая конструкция.
Выгода от корпуса очевидна) Конструкция не разваливается, из устройства не торчат провода, оно не похоже на бомбу, никто не знает, что оно работает на ардуине и его не стыдно показать на выставке или отдать программистам для написания прошивки.
Надеюсь эта информация оказалась кому-то полезна, спасибо за внимание.
P.S. На картинках не аудиоусилитель, а контроллер полива, просто аудиоразъёмы очень удобны для подключения слаботочных нагрузок.
UPD. Спасибо НЛО за то что приняло на борт сообщества и всем участникам за тёплый приём:)
И конечно файлики, экономлю время изобретателям)