Мастер класс по изготовлению модели механической руки
Знакомство с такой серьезной и загадочной отраслью науки, как робототехника всегда производит на детей сильное впечатление, вызывает у них интерес к науке и жажду своих собственных исследований. Кроме того, у этой игрушки прикладное назначение – знакомство ребенка с законами механики и их применение в реальной жизни. Получается, что это вовсе и не игрушка, а замечательный помощник в учебе!
С удовольствием представляю Вам мастер класс по изготовлению механической руки. По внешнему виду она напоминает экзоскелет, повторяющий естественные движения человеческой руки. Чтобы управлять этим удивительным устройством юному инженеру понадобится изучить строение человеческой руки и перенести его на картонный прототип, а затем «научить» руку двигаться.
Для работы понадобятся следующие материалы и инструменты:
картон; простой карандаш и маркер;ножницы;канцелярский нож;5 пластиковых трубочек; аптечные резинки; нитки средней толщины, иголка; клеящий пистолет.
Ход работы.
Шаг первый. Положите руку на картон, обведите и вырежьте.
Обратите внимание на направление волокон многослойного картона.
Шаг второй. Промаркируйте линии сгибов фаланг на картоне, ориентируясь по своей руке.
Шаг третий. В местах сгибов фаланг пальцев сделайте небольшие надрезы канцелярским ножом на внешней стороне руки. Зафиксируйте сгибы на каждой фаланге.
Пальцы картонной руки должны свободно сгибаться в местах надрезов.
Шаг четвертый. Прикрепите пластиковые трубочки с помощью скотча к «руке» как показано на рисунке.
Шаг пятый. Теперь на местах сгиба фаланг пальцев сделайте надрез на пластиковых трубочках на внутренней стороне. Надрезы должны иметь угол примерно 45 градусов, чтобы «пальцы» могли сгибаться.
Шаг шестой. Удалите скотч и приклейте пластиковые трубочки к картону с помощью клеевого пистолета как показано на рисунке.
Шаг седьмой. Проденьте в трубочки нитки и закрепите их на концах «пальцев». Здесь же прикрепите аптечные резинки.
Шаг восьмой. С помощью клеевого пистолета закрепите резинки на тыльной стороне «руки».
Механическая рука готова! Удерживая нити в руке и потягивая их на себя можно выполнять различные движения рукой: сгибать пальцы, брать легкие предметы и т.п.
Поняв принцип работы механической руки, можно предложить детям сделать собственные проекты по изготовлению собственных вариантов экзоскелетных рук. На детей производит особое впечатление, когда на такую «руку» надета перчатка.
Для более наглядного изучения строения человеческой руки можно с тыльной стороны можно нарисовать скелет реальных костей руки.
Робототехника. Создание механической руки — Паркфлаер
Актуальность данной темы состоит в том, что в настоящее время роботы способны заменить человека в самых различных средах, будь то промышленная, военная, медицинская индустрия и т.д. Роботы могут выполнять за человека различные виды работ, полностью или частично заменить человеческий труд. Эти машины неприхотливы к условиям труда, им не нужно платить заработную плату, они могут работать без перерывов и отпусков, так же способны выполнять рутинную работу.Задачи:
• Ознакомиться с системами управления роботов.
• Самостоятельное изготовление частей механической руки (детали механизма, электрической схемы).
• Найти подходящий материал и опциональные детали для создания робота.
• Обучится программировать на языке С++
• Написать программу для автономного выполнения работы, без участия человека.
• Обучиться технологии создания схем и пайке
СОЗДАНИЕ ПЕРВОЙ МОДЕЛИ РОБОРУКИ
Перед тем, как начать делать своего робота, я озадачился вопросом: а какого именно робота я хочу сделать? Я начал анализировать типы роботов: робота-андройда я не мог создать по нескольким причинам: у этого робота много подвижных деталей, сложно сделать каркас и трудно повторить внешний вид человека. Так же андроид сложен в управлении и потребляет много энергии.
Медицинский робот сложен в создании и очень чувствителен в управлении, тем более, самодельный робот вряд ли сможет кому-нибудь помочь, а может даже наоборот.
Боевого робота и робота для обеспечения безопасности я не стал создавать из-за сложности создания, безнадобности, опасности и отсутствием опциональных деталей.
Идеальным вариантом стал промышленный робот: легок в управлении, легко создать каркас и подобрать опциональные детали, но промышленные роботы обычно крупногабаритные, поэтому я решил сделать уменьшенную копию промышленной роборуки.
Подходящим материалом для создания роборуки был обычный металлический конструктор, который лежал в шкафу многие годы. Плюсы конструктора: легкость, возможность построить практически любую фигуру и деталь. Минусы: конструктор легко гнётся.
В качестве приводов я использовал сервоприводы, которые заказал по интернету.
Сложнее всего было придумать, как же все-таки будет управлятся робот. Я решил пойти по сложному пути и заказал электронную плату arduino uno, которая программируется на языке С++. Встал новый вопрос: а как программировать на языке C++?
Так как плата Ардуино к моменту создания первой модели не успела прийти по почте, я стал искать альтенативные способы управления. Выбор пал на самолетное радиоуправление. Друг, который увлекается авиамоделизмом, одолжил мне приемник и передатчик от своего самолета, и я подсоединил все сервоприводы к приемнику и запитал его своим автомодельным аккомулятором.
Сначала необходимо было сделать основание. Оно должно было быть устойчивым:
Следом, я закончил сборку подвижного основания, с помощью которого рука сможет вращаться вокруг своей оси:
Затем, я начал делать большое плечо.
Потом, настала очередь среднее плечо. Конечный вид большого и среднего плеч:
Затем, я собрал кисть робота и объединил с большим и средними плечами:
После этого я установил сервоприводы:
Однако возникла новая проблема: так как я обеспечил питание от автомодельного аккумулятора, который был более мощным, чем нужно сервоприводам, из-за этого регулятор, рассчитанный на небольшое количество маленьких сервоприводов, не справлялся и сильно грелся, а сервоприводы работали некорректно. Тогда было принято решение избавиться от одного плеча.
После этого я занялся сборкой финальной части – захвата. Сервоприводы способны поднять строго ограниченный вес, которые они способны поднять, поэтому необходимо было установить сервоприводы в строго определенных местах. После объединения всех деталей, за исключением большого плеча, и установки сервоприводов, модель приобрела законченный вид:
В качестве управления использовался авиамодельный пульт управления, который я позаимствовал на время у друга.
В качестве источника питания выступал автомодельный аккумулятор Turnigy nano-tech. Так же в данной модели аккумулятор служил противовесом.
Но сервоприводы способны поднять строго ограниченный вес, которые они способны поднять, поэтому необходимо было установить сервоприводы в строго определенных местах. Подключение сервоприводов к приёмнику не составило особого труда.
Первая модель оказалась не совсем удачной: она была неустойчивой, управление было неудобным, и потенциал сервоприводов был значительно снижен из-за самолетного регулятора напряжения, который был рассчитан только на маленькие сервоприводы, вследствие этого рука могла поднять только небольшой вес.
СОЗДАНИЕ ВТОРОЙ МОДЕЛИ РОБОРУКИ.
• Механическая часть
На создание второй модели механической руки времени было предоставлено крайне мало: чуть больше месяца. Однако роборука была готова в срок.
Сначала я приступил к созданию эскиза:
В качестве основания я решил использовать основу от игрушечного крана, так как оно обладало высокой устойчивостью.
Детали было решено изготовить П-оразной формы. Такого типа детали имели ряд преимуществ: они имели большой запас прочности, на такие детали легко крепить сервоприводы, при сцеплении можно сделать дополнительную ось вращения, что снизит нагрузку на сервопривод и сделает конструкцию более надежной.
Материалом для создания послужила листовая сталь 0.8мм, так как этот материал был легким и легко поддавался обработке. «Клешни» решено было сделать из дюралюминия, так как листовая сталь была слишком тонкой.
Но прежде, чем приступить к работе с металлом, необходимо было сделать точную копию деталей механической руки из картона. На картонных деталях соблюдались все размеры в натуральную величину, были размечены места отверстий для оси вращения в местах сцепления, и отверстия для крепления сервоприводов. Это позволило сделать детали максимально точно и уменьшило шанс совершения ошибок.
Для разрезания металла использовались ножницы по металлу, а для изготовления отверствий использовался сверлильный станок. Для изгиба деталей была применена киянка и тиски, так как железный молоток имеет меньшую площадь контакта и продавливает детали, дела вмятины и сколы.
«Клешни» вырезались с помощью ножовки по металлу и обрабатывались напильником. В них были сделаны отверстия разного диаметра, что облегчило их и сделало более красивыми.
Затем необходимо было сделать механизм захвата. Он представлял собой две шестеренки, надетые на неподвижные оси, на которые крепились «клешни», к одной шестеренке подводилась еще одна, которая связывалась с сервоприводом.
Чтобы соединить шестеренки с «клешнями» было использовано свойство металлов: расширяться при нагревании. Нагревание «клешней» осуществлялось строительным феном. После нагрева, на шестеренки, с помощью молотка, были насажены «клешни», а после охлаждения, конструкция стала монолитной.
Когда все детали были готовы, их необходимо было отшлифовать, убрать с помощью надфиля заусеницы и обработать ацетоном, чтобы избавиться от жира.
Наконец, наступила очередь окраски.
После окраски детали приняли законченный вид.
Затем, из основания бывшего игрушечного крана был удален механизм вращения и установлен новый, который присоединялся к сервоприводу. Так как сервопривод был длиннее, чем доступное место в основании, то в нижней крышке, с помощью сверлильного станка и ножовки, было вырезано место под сервопривод.
Настало время сборки второй модели механической руки. На специальные места были установлены сервоприводы и закреплены с помощью винтов, шайб и гаек. «Плечо», «локоть» и «кисть» крепились к сервоприводам с помощью саморезов, а осями вращения стали винты. Провода сервоприводов и сами сервоприводы крепились к плечам руки с помощью пластиковых хамутиков.
Законченный вид руки:
• Программная часть
Было решено управлять роборукой с помощью платы Arduino Uno. Программирование осуществлялось на достаточно сложном языке С++. Сама программа писалась на компьютере в специальной программе, которую надо было скачать с официального сайта Arduino. Там же находилось драйвера для связи платы Arduino Uno с компьютером.
После изучения принципа программирования и основных команд, я написал первую программу: мигание светодиода. Специальной схемы для этого составлять не надо было, так как на плате уже установлен один светодиод.
Сам код выглядел следующим образом:
Таким образом, светодиод загорается на 5 секунд, а затем гаснет на 5 секунд, и эти действия продолжаются, пока есть питание.
Итак, я убедился, в том, что правильно написал программу и теперь могу приступить к работе с сервоприводами. Для них в программе установлена специальная библиотека для связи сервоприводов с платой. Так же там есть другие библиотеки: чтение и запись в последовательный порт, для работы с шаговыми электродвигателями, для подключения к интернету и много других, но они нам не понадобятся.
Готовая программа выглядела следующим образом:
Выполняя эту программу, сервопривод поворачивается на 20 градусов каждую секунду, пока не сделает оборот в 180 градусов, затем возвращается в исходное положение.
Но прежде, чем приступить к написанию программы для пропорционального управления, нужно было написать программу для мониторинга сопротивления от резистора, которым будет управляться сервопривод. С помощью этого кода можно узнать максимальное и минимальное значение резистора, которые будут применены в конечной программе.
В итоге, изменяя сопротивление резистора, я узнал, что его максимальное значение это 537, а минимальное 0.
Наконец, я приступил к созданию электронной схемы. Сначала я сделал основание 18х8см и крепление переменных резисторов на 10Ком из стеклотекстолита. Затем на основу я установил плату Arduino Uno, схему стабилизатора напряжения, монтажную плату для выхода на сервоприводы, монтажную плату входного делителя напряжения и кронштейны с установленными переменными резисторами.
Конечный вид схемы:
В качестве питания сервоприводов использовался блок питания на 9V, но во дальнейшем было принято решение использовать аккумулятор на 7.4V.
После этого я написал программу для пропорционального управления механической руки.
В итоге, изменяя сопротивление на резисторе, мы изменяем угол поворота сервопривода, и механическая рука совершает действия, которые ей зададут.
Следом, я приступил к написанию кода, при котором роборука будет совершать одни и те же действия бесконечно долго, пока к ней подведено напряжение.
В дальнейшем, 3 резисторы будут заменены на тензодатчики- датчики изгиба, и механическая рука будет управляться с помощью перчатки, повторяя движения моей биологической руки.
Моя рука стала победителем среди проектов по физике на конференции «Шаг в будущее»!!! Ура!!!
Механический таракан своими руками
Механический таракан – это конструкция, которая весьма популярна среди любителей мастерить своими руками. Такие механические тараканы — прекрасный способ вызвать интерес к творчеству среди подрастающего поколения.Его походка очень схожа с настоящим тараканом. При ходьбе немного раскачивается шагая уверенно вперед. Таракан имеет минимум сложных деталей и очень прост в изготовлении.
1.Видеотест
На видео показан механический таракан с разных ракурсов во время его работы и передвижении.
2. Характеристики и особенности.
На фото 1. Показан Механический таракан, вид сбоку. На фото 2. Показан вид сверху.
Фото 1.

Фото2.

КОНСТРУКЦИЯ. В качестве рамы использован профиль ппн-2 30Х20. Крепление двигателя и других соединений произведено с помощью пайки. Лапы таракана крепятся болтами М6. Кнопка включения и отсек для батареек приклеены на двухсторонний скотч. В качестве тяги для привода лап таракана использован медный кабель сечением 2,5мм.
МОТОР И КРИВОШИП. Моторчик и ось кривошипа припаяны к раме на ПОС-61, паяльная кислота ZnCl (Хлористый цинк). Для увеличения крутящего момента и уменьшения габаритов, была использована червячная передача.
ПИТАНИЕ. В качестве питания робота был использован аккумулятор 18650. Источник питания 3,7В.
ДЕТАЛИ КОНСТРУКЦИИ РОБОТА
1. Лапы таракана.
2. Ребро жесткости.
3. Рама.
4. Ось лап таракана.
5. Кривошипный механизм.
6. Червячный привод.
7. Электродвигатель F130 5 В.
8. Втулка оси лап таракана.
9. Аккумулятор типа 18650, 3.7 В.
10. Батарейный отсек.
11. Кнопка включения.
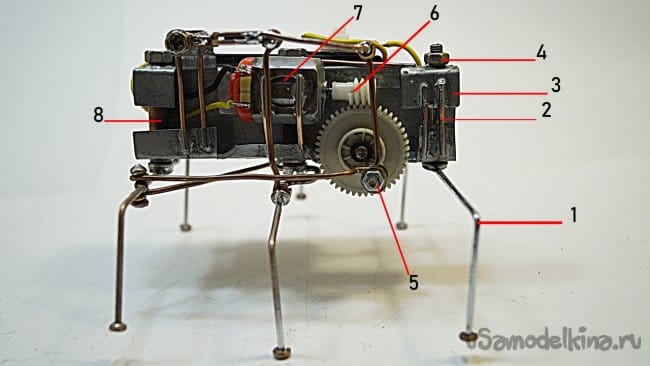

3. Принцип работы.
На фото 3. 4. Показан принцип работы механических частей таракана. Стоит помнить, что передние и задние лапы робота, движутся по горизонтальной плоскости, а средние лапы движутся по вертикальной и горизонтальной плоскости.
На электродвигатель через ключ поступает питание, двигатель вращает кривошипный механизм. Кривошип приводит в движение через тягу переднюю лапу, соответственно от передней лапы тяга толкает заднюю лапу (они движутся синхронно). Средняя пара лап соединена с первой парой, накрест (они движутся в противофазе).
Для движения средней пары лап вертикально, над моторчиком установлен рычаг, который приводится в движение от кривошипного механизма.
Фото.3
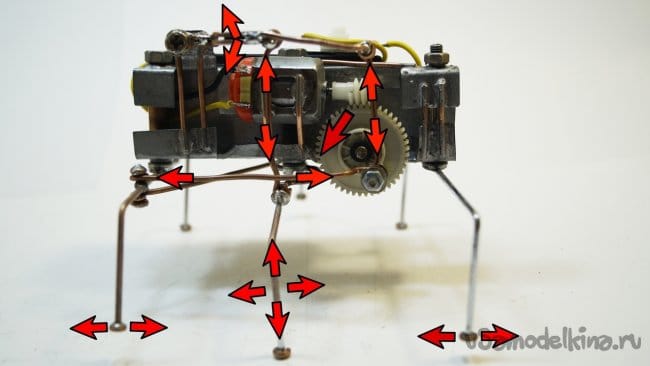
Фото.4

4. Материалы и инструмент.
1.Паяльник 50Вт.
2.Батарейный отсек.
3.Припой ПОС-61.
4.Медный провод сечением 2.5 мм.
5.Паяльная кислота ZnCl (Хлористый цинк)
6 .Электромотор F130 5В.
7.Ножницы по металлу.
8.Червячный привод.
9.Плоскогубцы.
10.Стальная трубка, диаметром 80мм.
11.Аккумуляторная батарея 18650.
12.Профиль ппн-2 30Х20.
А также: (кнопка включения, двухсторонний скотч, провод монтажный)

5. Инструкция по сборке.
1.Изготовление рамы таракана.
Рисуем на профиле разметку как указано на Фото 5.
Фото 5.
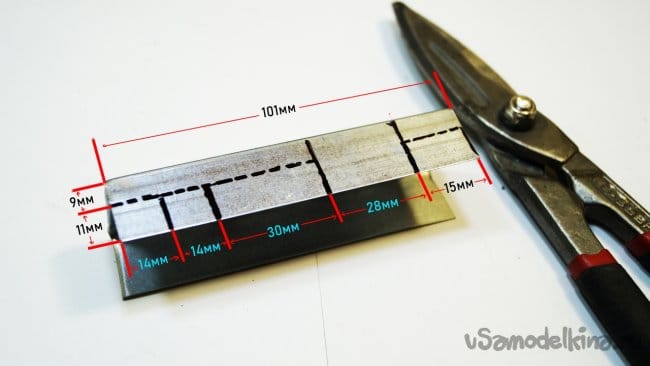
С помощью ножниц по металлу, отрезаем и загибаем заготовку плоскогубцами как указано на фото 6. Размечаем нижнюю часть как указано на фото 6. Загибаем профиль плоскогубцами как на фото 7.
Фото 6.

Фото 7.

2.Электромотор и ось кривошипа.
Следующим этапом нужно припаять электромотор к раме. Электромотор перед пайкой нужно будет разобрать. Лудим корпус мотора и раму паяльником Фото 8.

Спаиваем корпус электромотора и рамы вместе, хорошо прогревая детали паяльником прижав их друг к другу Фото 9.!!! БУДЬТЕ АККУРАТНЫ, ДЕТАЛИ СИЛЬНО НАГРЕВАЮТСЯ!!!
Фото 9.

Собираем электромотор обратно. По месту припаиваем ось кривошипа, это делается экспериментальным путем. Червячная передача должна быть хорошо подогнана между собой, шестерни не должны быть перекошены Фото 10,11.
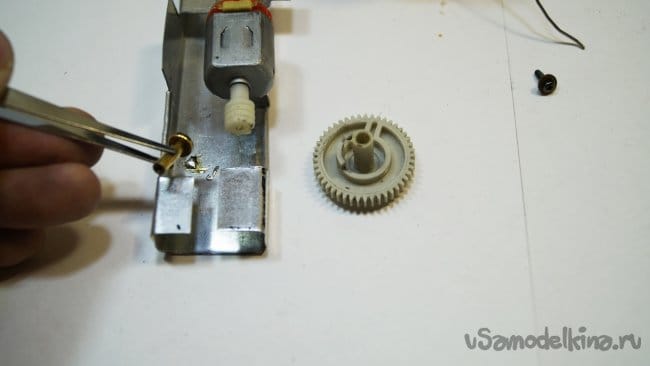

3. Отверстия для лап таракана.
Для крепления лап таракана к раме, нужно просверлить отверстия сверлом 8мм. Сверлим отверстие в ушке за электромотором сверлом 3.2мм


Также припаиваем на ушко за электромотором гайку. На эту гайку будет крепиться рычаг, отвечающий за подъем средних лап по вертикальной оси
Для усиления конструкции рамы, были припаяны ребра жесткости медным проводом сечением 2,5мм.
Также были впаяны втулки 8мм в места крепления лап таракана Фото 15.
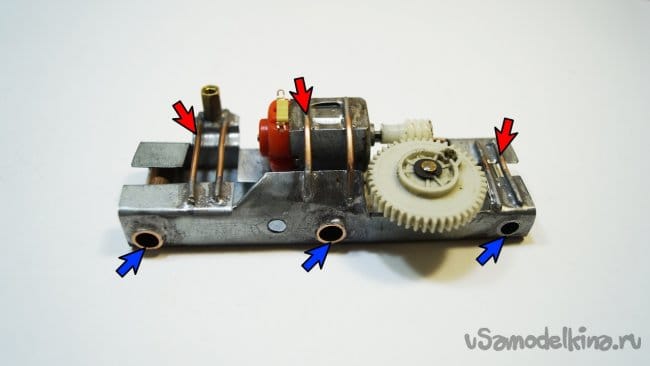
4. Лапы таракана.
В качестве лап таракана использована металлическая проволока диаметром 3мм, она припаяна к головке болта М6 Фото 16. Средняя пара лап таракана выполнена по-другому, в головке болта высверливается отверстие по диаметру проволоки. Проволока загибается в виде буквы “S”, это даст возможность лапам таракана двигаться вертикально Фото 17.
Фото 16.

Фото 17.
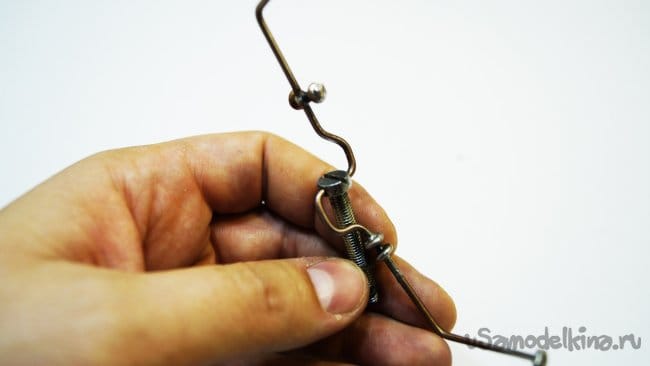
Для крепления тяг, к лапам таракана припаяна медная проволока сечением 2,5мм длиной 12мм, на концы ее припаиваются медные кольца. Тяги сделаны из медной проволоки сечением 2,5мм, размеры указываются приблизительно, проволоку желательно подогнуть, чтобы в дальнейшем была возможность регулировки по длине Фото 18.
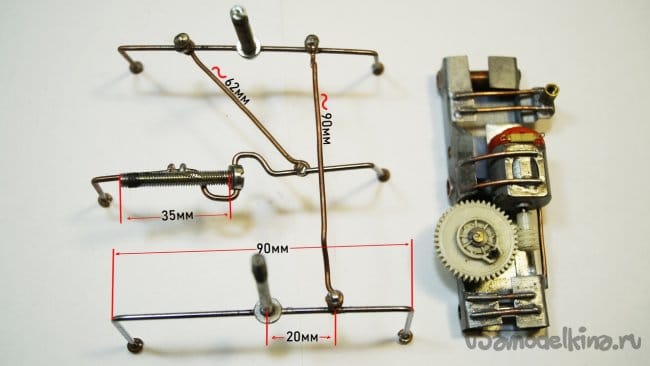
На Фото 19 показан вид снизу, с установленными лапами на раму.

Устанавливаем тягу от кривошипного механизма до передних лап таракана. Тягу делаем с подгибом для возможности её отрегулировать. Радиус кривошипа 8мм Фото 20.

Изготавливаем из медной проволоки рычаг для движения средних лап вертикально Фото 21.22.
На этом механическая часть таракана закончена.
Фото 21.

На Фото 22. Показано расположение лап при нижнем положении вала кривошипного механизма.
Фото 22.

5. Электрическая часть.
Батарейный отсек приклеиваем на двухсторонний скотч к раме таракана. Кнопку включения приклеиваем на батарейный отсек. Спаиваем все элементы Фото 23.

Робот — таракан готов!!!

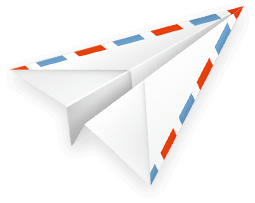
Получайте на почту подборку новых самоделок. Никакого спама, только полезные идеи!
*Заполняя форму вы соглашаетесь на обработку персональных данных
Становитесь автором сайта, публикуйте собственные статьи, описания самоделок с оплатой за текст. Подробнее здесь.Протез своими руками. Механическая рука из 3d принтера.
Это трогательная и поучительная история. Как много человек может обрести настоящее счастье! Посмотрите это видео до конца, посмотрите на этих счастливых детей. А ведь скольким сможем помочь мы с вами, обладая подобными технологиями! Как обычно, для любителей почитать публикуем даже не статью, а скорее историю о потрясающей технологии, меняющей нас с вами: Когда я отрезал себе пальцы — это было в среду, во второй половине дня — я поехал в больницу. Именно там, пока я сидел в кабинете неотложной помощи, я решил сделать себе новые пальцы. Вначале я обращался ко многим людям за помощью, но все они отказывались, даже не обсудив идею как следует. Они говорили мне, что это невозможно Однако, чем больше людей старались убедить меня в том, что это невозможно, тем крепче становилась моя уверенность в обратном. Я начал собирать и изучать информацию в интернет, в частности о всевозможных протезных решениях. Ни одно из них не давало мне возможности вернуться к моему ремеслу. Они не были нацелены на восстановление работоспособности человека. — Впервые о протезных руках и пальцах я начал задумываться когда мне было 12-13 лет. На уроках труда приводные инструменты приводили меня в ужас. — Иван сыграл во всем этом всем важную роль. Его идеи сильно помогли проекту. — У меня есть опыт работы с механическими деталями, в основном я занимался конструированием механических креплений. Однажды я сделал гигантские марионеточные руки. Ричард связался со мной после того, как увидел видео с одним из таких экземпляров механической руки, и предложил мне сотрудничество. Мы стали экспериментировать с трехмерной печатью, и использовать принтеры от Makerbot. — Мы раздобыли принтеры, и затем Иван вернулся в Америку. Я рисовал чертежи, сканировал их, отправлял Ивану по электронной почте. Он делал свои пометки, и отправлял файл назад, затем я распечатывал, и говорил: нет, так не пойдет, и опять начинал менять то и се, и так по кругу. — Makerbot replicator 2 очень сильно повлиял на процесс разработки. Он позволил сильно увеличил скорость, с которой мы могли создавать прототипы и испытывать новые идеи. Он дал нам возможность покрутить в руках физическое воплощение одной и той же модели, несмотря на то, что мы находились на расстоянии в десять тысячи миль. — Изначально, проект не был нацелен на помощь другим людям, и единственной целью было помочь мне. Но с течением времени, наблюдая за тем, как один прототип сменяет другой, я понял, что этот проект может помочь также и многим другим людям. -Лиам родился без пальцев. До него у нас было два полностью здоровых ребенка, так что для нас это было большим шоком. — Мать Лиама послала нам сообщение через Facebook… Дело в том, что мы выложили некоторую информацию на страницу в Facebook. Итак, она вышла с нами на контакт, послав небольшое сообщение, затем мы с ней побеседовали, и она сказала, что готова абсолютно на все ради шанса облегчить жизнь Лиама. На то время я еще даже не задумывался о возможности сделать полный протез кисти. О синдроме амниотических перетяжек… я впервые о таком слышал, я никогда с таким не сталкивался. Я оценил ситуацию, и мы решили сделать полный протез кисти. — Раньше я и не подозревала, что такое возможно… И когда я впервые увидела, как он что-то поднимает, и держит это в своей правой руке… это было поразительно! — Положи мяч, и снова подними его. Теперь подними. Вот так. Умница! — Протез кисти, который мы разработали для детей и взрослых с синдромом амниотических перетяжек, работает благодаря движению запястья. Чаще всего у таких людей пальцы отсутствуют, включая большой палец. У них есть только ладонь. Итак, протез крепится к руке с помощью специальной накладки. К той же накладке крепятся тросики. Когда кисть сгибается, механические пальцы сжимаются, и наоборот: когда кисть разгибается, пальцы разжимаются. Все, кроме трех вещей, сделано на трехмерном принтере Makebot. Все пальцы и суставы, кончики пальцев, большой палец, кистевой шарнир — все это печатается. Все, что остается — это тросики, металлические детали (все они сделаны из нержавеющей стали) и термопластическая пластмасса. Насчет последнего — вы просто вырезаете кусок нужного Вам размера, кладете его в горячую воду, он становится полупрозрачным, затем Вы вынимаете его, и он легко принимает форму руки. Однажды мне позвонила одна из матерей — как раз в то время, когда я занимался столярной работой — она сказала мне, что узнала о нас по телевидению SABC. — Я увидела там информацию, переписала телефонный номер, и позвонила Ричарду. — Мы сделали чертежи, и установили протез. Затем мне пришлось прибегнуть к помощи оккупационального терапевта. Дело в том, что у мальчика были большие проблемы с маневрированием протезом. Ему показали специальные упражнения, и уже ко времени его ухода он уже мог поднимать больше, чем раньше. — Ему очень нравиться носить этот протез. Если бы он мог — он бы и спал с ним. Благодаря ему он чувствует себя … особенным. — Когда ребенок подрастает, используя Makerbot, мы просто увеличиваем модель в размере и печатаем ее заново. При этом металлические детали берутся из старого протеза и вставляются в новый. Поэтому желательно, чтобы устаревшие протезы нам возвращали, чтобы мы могли их приспособить для кого-нибудь другого. — Когда я осознала, что он сможет жить как обычные дети, с обеими руками, на мои глаза навернулись слезы. Он сможет играть с мячом, играть в крикет, регби, кататься на велосипеде, держать стакан обеими руками… в общем, делать все то же, что и обычные дети. А когда я увидела радость в его глазах… я была просто счастлива. — Мне нравится эта рука, она потрясающая, и с ее помощью я могу делать практически все что угодно. — Если во время изготовления одного из этих протезов, вы ошиблись, сломали что-либо, или просверлили деталь не в том месте — ничего страшного: просто запускаете принтер, и заново печатаете новый комплект деталей. — Этот трехмерный принтер сильно упрощает для Ричарда и Robohand задачу создания протезов. — Наличие принтера Makerbot, и возможность обмениваться файлами по интернет, позволили нам сократить время на разработку прототипа с недели до двадцати минут. Невероятно быстро. — Для того, кто впервые пользуется таким протезом, он отлично справляется, и очевидно, что ему доставляет удовольствие экспериментировать с новыми возможностями своей руки. — Со мной связался отец Дилана, и сказал, что он — друг отца Лиама. Он сказал, что наблюдал за всем этим, и хотел бы дать и своему сыну шанс на нормальную жизнь, так что не мог бы я помочь и ему тоже? — Мы — одни из первых людей, которым выпало испробовать это новое приспособление. По результатам я вижу, что мой сын действительно счастлив, и потому я тоже счастлив. — Если у кого-либо есть ребенок с синдромом амниотических перетяжек, и он хочет сделать ему такую руку, мы считаем, что это вполне возможно. На сайте Thingiverse мы выложили все необходимые файлы. Все, что нужно сделать — это получить доступ к трехмерному принтеру, напечатать детали и собрать все это вместе. Мы рекомендуем обратиться к оккупациональному терапевту за помощью с пластиковыми рукавом и перчаткой. Однако, если вы решились сделать все своими силами, от начала до конца, это также возможно. — Я очень рад, что теперь у меня есть рука Robohand. Мне не терпится попробовать играть в крикет и гольф, и даже поплавать в ней. Во вторник мы будем играть в крикет, и теперь я смогу ловить мяч моей правой рукой. — Когда я вижу, как лицо Дилана озаряется радостью, мое сердце замирает от счастья. В такие моменты я чувствую и гордость, и печаль… весь спектр эмоций одновременно. Это изумительно! — Возможно, Robohand и стал и неожиданностью для мира трехмерной печати, однако, если Вы серьезно зададитесь вопросом что может нам дать возможность самостоятельно печатать механические части, Вы поймете, что замещение утерянных пальцев — всего лишь одно из огромного множества применений. Технология трехмерной печати дает невероятно широкие возможности. — Я всегда буду благодарна Ричарду, Makerbot и Robohand за шанс на нормальную жизнь и за все, что они для нас сделали. — Я просто не могу выразить словами своих чувств… Что все еще есть люди, помогающие другим. И да, я просто ошеломлена возможностями этого принтера. — Я могу поднимать вещи. — Раньше я не мог себе и представить, каково это будет — иметь такую руку. — Я могу кинуть мяч. — Мои друзья говорят, что это круто. — Я люблю мою руку Robohand. Благодарим за просмотр! Будем рады обсуждениям в комментариях Технологии растут потрясающими темпами. Недавно мы публиковали ролик об изобретении для доставки лекарственного средства непосредственно в определенное место организма. Что будет дальше — даже сложно загадывать.Механический дровокол своими руками: чертежи, фото, инструкция
Изготовить механический дровокол своими руками хотят многие. Однако, с чего начать, знают далеко не все. Интересно прочитать о конструкции того или иного устройства. На фотографиях они выглядят довольно привлекательно.
В торговой сети предлагают желающим целый арсенал машин для раскалывания чурбаков. Для некоторых из них сняты довольно интересные видеоролики, года демонстрируются особенности работы. На стендах около предлагаемых моделей присутствуют результаты измельчения дров на отдельные полена.
Зачем нужны дрова – повышение качества топлива
В современном мире довольно много источников энергии:
- Природный газ доступен на обширных территориях. Достаточно открыть горелку и зажечь, как появляется синеватый огонек, который выделяет значительный тепловой поток.
- Жидкое топливо, подаваемое через форсунки, горит ярким красным или желтоватым пламенем. Даже в тепловых машинах применяют разные виды жидких энергоносителей.
- Уголь и продукты его переработки имеют продолжительный цикл горения. Красноватое пламя долго отдает тепло не только конвекцией, мощный поток теплового излучения поступает на все окружающие предметы.
- Дрова – были первыми доступными источниками тепла. Актуальными они остаются и в настоящее время.
Во многих домах используется печное отопление. Бани и сауны, рекламируя свои услуги, указывают, что в качестве источника тепла используют дрова определенных пород деревьев. Приготовление пищи на открытом воздухе традиционно предусматривает использование древесины в технологии тепловой обработки продуктов.
Теоретические основы теплотехники – сгорание твердого топлива
Чтобы легче поджечь дерево, его нужно расщепить на сравнительно небольшие фрагменты. После раскалывания чурбаков на отдельные поленья увеличивают поверхность контакта горючего материала с воздухом. В результате мгновенная теплоотдача внутри топки возрастает пропорционально площади горения. Поэтому процедура колки дров – это прием, позволяющий повысить эффективность использования топлива.
Внимание! Расколотые на поленья дрова укладывают в поленницы. В них происходит их высушивание. Влага, находящаяся внутри древесины, интенсивно испаряется. Видимая теплота сгорания повышается, так как не нужно тратить энергию на испарение жидкости, располагающейся в межклеточном пространстве.
В теплотехнике для характеристики топлива введены понятия:
- Высшая теплота сгорания, подразумевающая суммарную теплоту, выделяемую при сгорании конкретного типа горючего вещества.
- Низшая теплота сгорания – фактическое количество теплоты, в котором учитываются затраты энергии на нагрев топлива, удаления из него в процессе горения ингредиентов, не участвующих в самом процессе.
Поэтому сушка дров – это прием, улучшающий характеристики топливного элемента. Предварительное измельчение повышает эффективность высушивания дров, а в дальнейшем и горения в печи или ином устройстве для сжигания твердого топлива.
Процесс раскалывания древесины
Колоть дрова можно разными способами. Традиционно принято производить удары топором, стараясь расщепить отпиленный фрагмент бревна, нанося удар по торцевой части.
Тяжелый клин (топор имеет клиновидную форму) внедряется в тело чурбака. Если попадается древесина без сучков и рыхлой структурой, то даже при сравнительно небольших физических затратах произойдет внедрение клина внутрь. Тангенциальные усилия раздвинут волокна, произойдет раскалывание тела на две составляющие.
Если угол при вершине сделать небольшим, то клиновидное тело будет глубоко проникать внутрь, но величина тангенциальных сил окажется небольшой. Разрушающего усилия окажется недостаточно. Топор будет заклинивать в образующейся щели.
При образовании менее острого угла, касательные силы окажутся более значимыми. Они сумеют расколоть древесину.
В лабораториях проводится изучение реологических свойств разных пород дерева. Вязкость зависит от многих факторов. Установлено, что для большинства видов древесины желательно иметь клин с углом при вершине 25…30 °. У подобного режущего инструмента рубящие свойства оказываются наилучшими по раскалывающим свойствам.
При медленном проникновении клина определяющими становятся не накопленная в результате замаха и последующего удара кинетическая энергия. Процесс происходит внедрением в пластическое тело, где при достижении определенных значений происходит разрыв связей между волокнами.
Исследования показали, что для дровоколов угол при вершине должен быть 30…38 °. Тогда проникновение клина будет сопровождаться разрыванием связей при меньших усилиях. Только некоторые породы будут оказывать сопротивление: вяз, клен, яблоня, вишня.
Для сосны, дуба, ясеня и ряда других пород достаточно небольшого внедрения в тело. Разрыв связей происходит довольно легко.
На величину сил влияет и длина чурбака. Чем он короче, тем меньшее сопротивление оказывает дерево при раскалывании. Обычно длину определяет глубина топки – дрова должны помещаться внутри печи так, чтобы можно закрывать дверку.
Механические помощники для раскалывания дров
Ряд предприятий металлообработки изготавливают дровоколы. По принципу действия их делят на несколько типов:
- Колуны – установки рубящего действия. Осуществляется постановка чурбаков на специальные опоры, а затем наносятся удары утяжеленным долотом.
- Клин для рубки ставят неподвижно, на них опирают раскалываемые предметы. Удары наносят тяжелыми кувалдами, раскалывание выполняется при прохождении через пассивный рабочий орган.
- Давилки – это установки с механическим приводом толкателя. Бревно укладывается на ложе, а потом его проталкивают через плоский или крестообразный нож.
- Винтовые разрушители внедряются внутрь слоистого материала. Проникая глубже, расщепляют даже прочную и свилеватую древесину.
Рубка древесины клиновыми устройствами
Клинья являются самыми простыми устройствами для рубки дерева. В них уровень механизации труда минимальный. Основная задача приспособления – это ориентированная фиксация чурбака относительно режущих кромок. Удары наносит сам пользователь, размахивая тяжелым молотком или кувалдой.
В колунах движение клинового топора выполняется по постоянной траектории. Объект обработки ставят на неподвижную площадку. Чтобы сила удара была максимальной, массу исполнительного механизма увеличивают.
Для смягчения работы устройства его комплектуют мощными пружинами. Они смягчают удар в конечной точке, не позволяя клину касаться опор (предотвращают притупление клина). Попутно пружины помогают пользователю поднимать тяжелый нож для нанесения очередного удара.
В стабильном положении вся система находится в уравновешенном состоянии. Момент, создаваемый весом груза G, расположенном на плече L₁, уравновешивается силой пружины F на плече L₂.
G·L₁ = F·L₂
Удобнее всего использовать пружины от автомобиля. Для стандартных авто начальная величина сжатия составляет F = 8 кН (800 кГ). Плечо L₁ = 2,0 м. Приняв плечо L₂ = 0,3 м, получится вес груза G = 300 кН (30 кГ). Пружинный механизм работает довольно мягко, хотя действие дровокола основано на ударах по разрубаемым чурбакам.
Человек приподнимает груз от уровня пояса на 0,5…0,6 м. В дальнейшем производится отпускание клина. Он падет и разбивает чурбак. Если полного разрушения не произошло, то приходится поднимать колун и чурбан. При последующих ударах действует вес всей системы, удар получается сильнее. Даже сучковатые обрезки разбиваются при многократном ударении.
Механизмы подачи бревна на расщепление
Дровоколы, в которых реализуется принцип продавливания через неподвижные ножи, механизируют основной технологический процесс: раскалывание чурбаков на отдельные фрагменты. По типу привода толкателя принято определять:
- Гидравлические, в них толкатели связаны со штоками гидроцилиндров. Насосом создается давление в масле, которое передается внутрь механизма. Это самые простые конструкции, так как гидроприводные устройства не имеют дополнительных преобразователей энергии.
- Инерционные используют вращающиеся массы. Накопленная маховиками энергия преобразуется в поступательное движение толкателя. Устройства используют специальные муфты сцепления, включаемые оператором после установке на ложе фрагмента бревна.
- Реечные механизмы используют преобразователь из вращательного в поступательное движение с использованием зубчатого колеса и рейки с зубьями. В нужный момент шестерня поворачивается до зацепления с зубьями исполнительного устройства. Толкатель передвигает чурбан на неподвижные ножи. Он раскалывается на меньшие по размеру элементы.
- Кривошипно-шатунный механизм из редуктора получает крутящий момент. Он преобразуется в поступательное перемещение толкателя. Включение (выключение) регулируется постоянно разомкнутой муфтой сцепления. В нужный момент оператор включает сцепление, кривошип начинает вращаться, заставляя шатун перемещаться поступательно. Цикл завершается возвращением кривошипа и шатуна в исходное положение.
- Разъемной гайкой и ходовым винтом. Включается двигатель, вращение вала передается на ходовой винт. В нужный момент разъемная гайка соединяется, вращающийся вал перемещает ее, действуя на толкатель. Для возврата меняют направление вращения вала (используется зубчатая передача обратного вращения).
Винтовой дровокол
Подобные устройства не обладают высокой производительностью, но они занимают сравнительно немного места. Их устанавливают в дровяниках (помещениях для хранения дров). Там же производят раскалывание брусков на небольшие поленья и щепу.
В состав станка входят:
- Электродвигатель, от него крутящий момент передается на исполнительный механизм.
- Ведущий и ведомый шкивы с клиновым ремнем, понижающая клиноременная передача помогает увеличить крутящий момент, а также снизить частоту вращения на основной детали устройства.
- Конус является основным рабочим органом. На конической поверхности нарезана упорная коническая резьба. При вращении внутри разрушаемого тела коническая винтовая часть врезается глубже, подтягивая полено к опоре.
- Клин – это вспомогательное приспособление, которое помогает разрушить притянутую деталь.
Механизм простой, управляет им один человек. В процессе работы приходится подавать чурбак на конус. Его конструкция сложнее. Нарезается упорная резьба с шагом 7 мм.
Самостоятельное изготовление дровокола
У многих жителей сельской местности, а также у дачников возникают вопросы: «Как сделать механический дровокол своими руками? Насколько сложно изготовить станок для колки дров?»
Еще больше вопросов возникает в процессе изготовления. Начинать можно с самого простого устройства. Освоив приемы работы на нем, можно переходить к изготовлению более сложных дровоколов и не только.
Пошаговое руководство по изготовлению пружинного дровокола
Для выполнения работы потребуются инструменты:
- УШМ (болгарка) с набором отрезных дисков и зачистных лепестковых кругов.
- Сварочный аппарат, современные бытовые устройства инверторного типа для сварки стальных конструкций сравнительно небольшие по массе. Процесс выполняется на постоянном токе, поэтому сварные швы получаются аккуратными, расплавленный металл электрода полностью заполняет стыки между деталями.
- Струбцины помогут соединять свариваемые детали.
- Мерительный и разметочный инструменты помогут изготавливать заготовки будущей конструкции.
Нужны материалы:
- Швеллер №№ 10…16 (номер определяет высоты выраженную в сантиметрах).
- Профильная труба 40·60 мм (30·60 мм).
- Рельс длиной 300…400 мм.
- Двутавр №№ 12…16.
- Уголок № 30…50.
- Втулка от подвески автомобиля (она может иметь износ).
- Трубы диаметром 40…70 мм.
- Пружина подвески легкового автомобиля, например, от ВАЗ.
Перед началом работы прорисовывается эскизный проект. Некоторые умельцы освоили программы инженерного проектирования, с помощью которых могут проработать детали будущего изделия. Подробности изготовления показаны ниже.
Примерная схема поможет сориентироваться в процессе изготовления установки.
Из швеллера изготавливается опора. К ней приваривают стойку. Для стойки лучше всего использовать двутавр. У этого вида проката высока жесткость. При длительных нагрузках изогнуть такой элемент довольно сложно.
Чтобы обеспечить устойчивость основанию, к нему приваривают укосины. Дополнительно из имеющихся труб создают упоры, они предотвратят возможное падение всего изделия.
Из швеллера вырезается опора для пружины. В ней пропиливается квадратное отверстие. Оно позволит в дальнейшем надежно зафиксировать элемент на стойке.
Высоту установки опоры определяют по длине имеющейся пружины. Попутно ориентируются на высоту всего дровокола, а также удобство использования его для человека. Удобно приподнимать груз, расположенный на высоте пояса. Приподнимать придется немного выше уровня груди.
Все эти размышления позволят выбрать высоту установки опоры для пружины на стойке.
Из уголков изготавливают укосины. Они будут удерживать опору. Тогда при динамическом нагружении дровокола не будут происходить смещения опорной поверхности.
Чтобы зафиксировать нижний конец пружины, нужно изготовить цилиндрический фиксатор. Для его изготовления используется небольшой отрезок трубы. Желательно, подобрать трубу по внутреннему диаметру пружины. Тогда она не будет смещаться в процессе работы.
В верхней части стойки выполняется прорезь. В нее устанавливают втулку. Затем ее проваривают. При монтаже нужно выдержать перпендикулярность к стойке. Ось втулки должна быть параллельной земле. Для сварки используют кондуктор, который позволит выполнить указанные условия.
Во втулку устанавливают вал. К нему приваривают коромысло (используется швеллер). На нижней части коромысла монтируют небольшой фрагмент трубы. В нем будет фиксироваться верхняя часть пружины.
Чтобы коромысло перемещалось свободно, в нем прорезается окно, его размеры зависят от параметров стойки.
К коромыслу приваривается профильная труба. На ее конец устанавливают зубило. Эти инструменты изготавливают из углеродистой стали У9…У10. Твердость такого металла составляет HRC 60…63. Такой инструмент прослужит долго. В процессе эксплуатации его несложно заточить с помощью УШМ и заточного круга.
Дровокол обретает рабочий вид. Выше зубила приваривают груз (часть рельса). Для удобства использования приваривается рукоятка. Чтобы меньше повреждать руки, надевают резиновые элементы. Они погасят вибрацию при ударах.
Для работы потребуется установить обрезок бревна большого размера. На него будут устанавливать поленья, которые придется разрубить.
Чурбак придерживают одной рукой. Приподнимают колун, а потом наносят удар.
Колун опускается вниз. Находящийся снизу фрагмент раскалывается. Зубило опускается ниже. Если происходит полное раскалывание, то острие ударяется в деревянную опору и не тупится.
Организация производственного процесса
После изготовления дровокола придется заниматься колкой дров. Чтобы работа выполнялась легко, необходимо правильно организовать производственный процесс.
Напиленные фрагменты нужно расположить с одной стороны. Чтобы меньше уставать, расстояние должно быть всего два-три шага.
Нарубленные поленья желательно укладывать на тележку. Объем тележки небольшой, в нее поместится не более 30…40 кг дров.
После наполнения их нужно отвозить и укладывать на поленницу. Пока нарубленные дрова перевозятся к месту хранения, можно отдохнуть от основной работы. Смена занятий – это тоже отдых.
Видео: механический дровокол своими руками или как собрать дровокол.
Заключение
- Облегчить заготовку дров можно использованием дровоколов. Простейшие виды этих устройств можно изготовить своими руками.
- Выполняя пошаговые действия при самостоятельном изготовлении пружинного устройства, несложно самостоятельно изготовить удобный дровокол ударного действия.