Простое изготовление корпуса для радиолюбительских устройств
Автор: Прокофьев Алексей Александрович. “UA3060SWL”
Простая технология изготовления корпусов для радиолюбительских конструкций своими руками
Многие, особенно начинающие радиолюбители сталкиваются с такой проблемой, как подбор или изготовление корпуса для своей конструкции. Пытаются разместить собранную плату и другие компоненты будущей конструкции в корпуса от старых приемников или игрушек. В законченном виде этот прибор будет выглядеть не очень эстетично, лишние отверстия, видимые головки шурупов и т.д. Я хочу на примере показать и рассказать как я, буквально за пару часов, делаю корпус для собранного недавно SDR приемника.
Приступим!
Для начала нам нужно сделать приспособление для закрепления деталей будущего корпуса. У меня оно уже готово и я его с успехом использую уже десяток лет. Пригодится это нехитрое приспособление для точного склеивания боковых стенок корпуса и выдержки углов в 90 градусов. Для этого нужно выпилить из фанеры или дсп детали 1 и 2, толщиной не менее 10 мм , как на фото 1. Размеры конечно могут быть и другими, в зависимости от того, какие корпуса для конструкций вы планируете изготавливать в дальнейшем.
фото 1:
Корпус будет из пластмассы толщиной 1,5 мм. Для начала замеряем самые высокие детали конструкции, у меня это громоздкие конденсаторы на плате (фото 2). Получилось 20 мм, прибавим толщину текстолита 1,5 мм и добавим примерно 5 мм для стоек в которые будут вкручиваться саморезы, когда буду крепить плату в корпусе. Всего получается высота боковых стенок 26,5 мм, такая точность мне не нужна и я округлю это число до 30мм, небольшой запас не помешает. Запишем, что высота стенок равна 30 мм.
фото 2:
Размеры моей печатной платы 170х90 мм, к этому я прибавлю по 2 мм с каждой стороны и получу размеры 174х94 мм. Запишем, что дно корпуса равно 174х94 мм.
Практически все посчитано и приступаю к вырезанию заготовок. При работе с пластмассой удобно пользоваться монтажным ножом и линейкой. Буквально через 10 минут у меня получилась задняя стенка и заготовки боковых стенок (фото 3).
фото 3:
Далее зажимаем заднюю стенку в наше, ранее сделанное “устройство” и приклеиваем боковую стенку, которая в моем случае имеет размер 177х30 мм ( фото 4. а). Также как и первую стенку, приклеиваем вторую, повернув заготовки другой стороной (фото 4. б). Для склеивания стенок корпуса используется “Суперклей” (для большей прочности можно затем пройтись по уголкам клеевым пистолетом, также и все провода можно собирать в жгут и приклеивать к стенкам корпуса).
фото 4:
На фото 5 (а) виден результат моего труда. Когда правильно приклеены боковые стенки и выдержан угол 90 градусов, можно с легкостью вклеить оставшиеся 2 стеночки и монтажные стойки для крепления платы. В моем варианте одна стенка глухая, а вторая с отверстиями для подключения разъемов (фото 5 б).
фото 5:
После склеивания всего корпуса следует закруглить надфилем или наждачной бумагой все углы, это придаст корпусу плавные линии и он не будет похож на кирпич. После того как все будет готово, установлена плата, несколькими каплями клея приклеиваем крышку устройства (фото 6).
фото 6:
Ну и полностью собранный приемник в корпусе (фото 7) теперь установлен на стене, не мешает и не портит интерьер моего рабочего места.
фото 7:
Вот и все! На все слесарные работы я затратил пару часов и первый вопрос жены был: “что это у нас за сигнализация?” (шутка!)
Успехов в творчестве!
Самодельный корпус для электроники
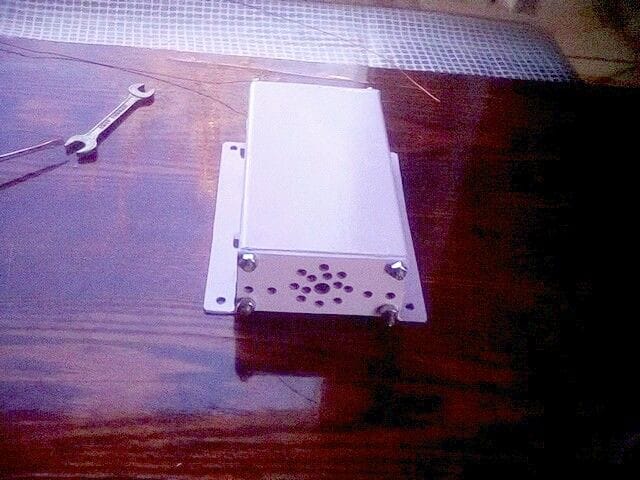
Сделать надёжные, качественные и долговечные корпуса для различного типа электроники можно своими руками. Это, конечно, потребует некоторых умений, навыков и усилий, однако поможет существенно сэкономить денежные средства (заводские корпуса из алюминия и даже обычные пластмассовые конструкции стоят весьма недёшево).
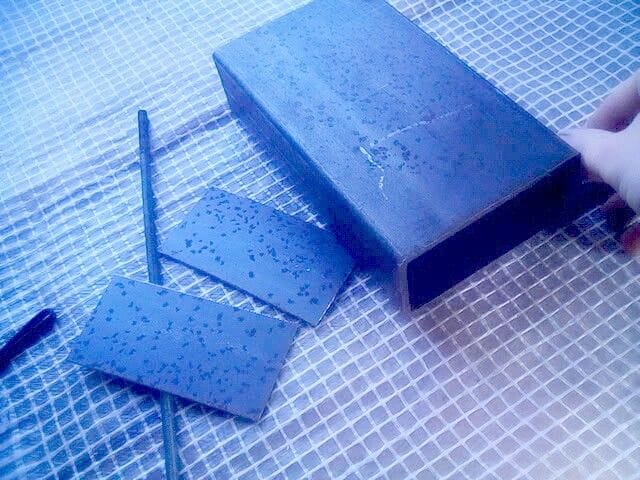
Чтобы изготовить самодельный аналог корпуса для электроники, возьмите 40-сантиметровый отрезок профильной оцинкованной трубы прямоугольного сечения 100х50 (подобные габариты позволят эффективно рассеивать тепло). Желательно, чтобы толщина стенки трубы при этом была не более 3 мм. Для мелкой электроники используемые размеры должны быть чуть меньшими – 40х20, а толщина стенки трубы 2 мм. Приобрести такие трубы можно в специализированных строительных магазинах. Инструментов вам понадобится самый минимум – только дрель или шуруповёрт (для сверления отверстий), а также болгарка (непосредственно для того чтобы разрезать трубу).
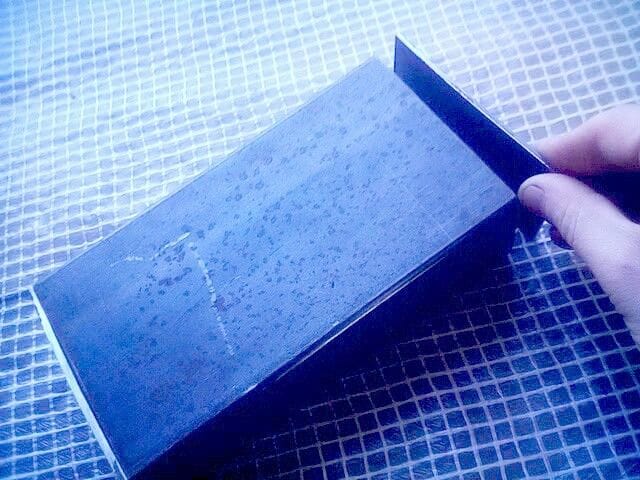
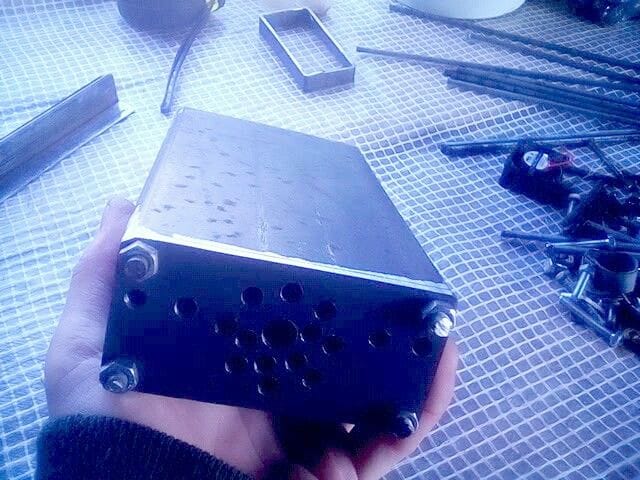
Отрежьте от профильной трубы 18 см – это будет сам корпус. Его боковые стенки, также полученные путём отрезания от трубы, необходимо скрепить 4-мя шпильками, проходящими через углы вдоль длины всего корпуса. В таком случае они не помешают размещению внутри всех нужных деталек. Для обеспечения оптимального зазора для быстрого охлаждения разрежьте профиль 20/20 мм так, чтобы получилось два уголка в форме буквы L. Их нужно прикрутить с боков – получится отличное настенное крепление.
Самодельный металлический корпус с достаточной теплопроводностью, который ввиду своего немалого веса больше подойдёт для стационарного использования, готов. Остаётся только придать ему привлекательный внешний вид, т.е. покрыть краской из баллончика, предварительно прогрунтовав и обезжирив поверхность, дабы краска легла ровнее и продержалась подольше.
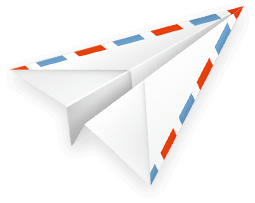
Получайте на почту подборку новых самоделок. Никакого спама, только полезные идеи!
*Заполняя форму вы соглашаетесь на обработку персональных данных
Становитесь автором сайта, публикуйте собственные статьи, описания самоделок с оплатой за текст. Подробнее здесь.Самый крутой системный блок для PC (сделай сам) / Habr
Добрый день, хабровчане. Большое спасибо за инвайт! И хотя начинать с перевода чужих постов — не самая хорошая идея, возможно, этот проект самоделки еще кому-то покажется мега-крутым.Это перевод поста с форума Оverclock.net. Пользователь Show4Pro решил вытащить все внутренности своего супер компа и повесить все на стену. Прекрасная идея прекрасно реализована. Кому интересно, как это собиралось и как это работает — велкам под кат.
Вступление
Последний раз я обновлял свою домашнюю машину 1,5 года назад. Ну и подумал апгрейдить тачку до i7 (до этого был Bloomfield), хотя на самом деле, более мощный процессор мне не был нужен. Хотел купить новый корпус — Corsair 900D, чтоб поменять 8 летний Super Armor. Но хотелось чего-то особенного, уникального. В Battlestations на Reddit-е я наткнулся на очень простое, но элегантное решение — настенный комп. И с этого начался весь проект.
Комплектующие:
Процессор: Intel Core i7 950
Материнская плата: Asus Rampage III Extreme
Видеокарты: 2 x AMD HD7970
Оперативка: 6 x 2GB Corsair Dominator
SSD диски: 4 x 120GB Corsair Force GT SSD
HDD диски: 2 x 1TB WD Caviar Black
2TB WD Caviar Green
1.5TB WD Caviar Green
Блок питания: Corsair AX1200i
Звук: Creative Sound Blaster Zx
Охлаждение:
Охлаждение для CPU:
Радиатор для CPU с водяным охлаждением EK Supreme HF Full Copper
Помпа Swiftech MCP655 /w Speed Control
Сам охладитель FrozenQ Liquid Fusion V Series 400 ml Reservoir — Blood Red
Радиатор XSPC RX360 Performance Triple 120mm Radiator
Охлаждение GPU
Радиатор для видеокарты EK FC7970 — Acetal+EN
Помпа и охладитель — те же, что и для проца.
Swiftech MCP655 /w Speed Control
FrozenQ Liquid Fusion V Series 400 ml Reservoir — Blood Red
Радиатор водяного охлаждения Watercool MO-RA3 9×120 LT Radiator
Другое:
Патрубки для системы охлаждения
Koolance QD4 Quick Discounnect No-Spill Coupling
Bitspower G1/4 Silver Triple Rotary 90deg Compression Fittings
Monsoon Free Center Compression Fittings
Сгибающая канавка для трубы Phobya Angled Clip 90° Tubing Guide
Холдер Phobya Terminal Strip Tubing Clip/Holder
Сами трубки охлаждения (красного цвета) PrimoChill Advanced LRT Tubing Bloodshed Red
Кабели:
Bitfenix Alchemy Premium Sleeved Extensions
Corsair Individually Sleeved Modular Cables
Создание.
Для начала, я сделал фотографии всех компонентов в их реальных размерах и скомпоновал все это в Фотошопе. Таким образом, я смог перемещать их по рабочей поверхности и решить, как это будет выглядеть. Ну и это нужно для разводки трубок охлаждения. Вот пара макетов:
От этого отказался, из-за пустого места в правом нижнем углу. А материнка оказалась слева, хотя должна быть в самом центре и притягивать внимание ко всей панели.
Тут тоже куча места справа, хотя блок питания и материнка уже ближе к центру. В финальной версии трубки охлаждения тянутся по всему правому краю, плюс там появились два термометра.
Переношу чертеж материнки на акриловый лист.
Так как видеоадаптеры будут далеко от материнской платы, я заказал удлинители для PCIe слота для каждой из карт на eBay. Это я тестирую, как они работают. Правда, потом у меня были огромные проблемы с перекрестной работой карт из-за дешевых неэкранированных проводов. Они оказались друг над другом и создавали серьезные помехи. Система висла на загрузке Биоса. Ее удалось запустить лишь с одной картой. В конце концов, мне пришлось раскошелится на очень дорогие кабели с хорошей защитой. Но об этом — позже.
Товар прибыл!
БОльшая часть водяного охлаждения — из Performance-PC. Они даже подарили мне футболку и целых два коврика для мышки!
Акриловая подложка для материнки.
Все акриловые панели обрезаны под 45°, чтоб достичь эффекта свечения края.
Отверстия просверлены, крепления установлены.
Та-да!!! Оказывается, мама Rampage III Extreme — формата eATX. А это — для АТХ формфактора.
Правильную eATX-подложку я сделал позже.
Пора выпотрошить мой старый пыльный корпус.
В старом компе диски вставлены в боксы Vantec HDCS, которые из 2-х 5.25″-х делают 3 бокса для HDD.
Видеокарты.
Подложки для всех компонентов.
Кастомные крепления для помпы из акрила.
Крупный план черновой отделки, сделанной с помощью настольной пилы. Позже их нужно будет отшлифовать.
В центре каждой пластины есть треугольный разрез. Он будет отражать свет, который проецируется перпендикулярно внутри пластины на краях. Без разреза края еле светятся.
Тест со включенным светом на панели с звуковухой.
Все панели отшлифованы влажной наждачкой на 120.
Крупный план шлифовки.
Все задние панели с готовыми отверстиями.
Под столом — акриловый снег.
Подготовка к покраске в красный цвет.
Удивительно, но Corsair сделал термопрокладки на лепестках, хотя они не нагреваются вообще.
Разметка всех компонентов на основной плате, чтоб отметить различные щели и отверстия. Доска — 1/4″ 48 х 30 ДВП.
Все щели и отверстия отмечены на своих местах.
Готовлюсь вырезать слоты лобзиком.
Приклеиваю рамку.
Внутренние края выкрашиваю в черный — под цвет карбоновой пленки.
Пайка светодиодных лент.
Рабочее место.
LED-ленты. Временное крепление.
Клею гигантскую виниловую пленку. Это была самая жестокая часть. Я чуть не получил инфаркт. Как наклеивать пленку на экран телефона, только х1000 больше.
Нет пузырей!
Использую алюминиевый скотч, чтоб скрыть LED на лицевой стороне панели для жестких дисков, между ними.
Мой помощник — Томми.
Все подложки установлены на свои места на общей плате на винтах №10. Их вкрутил в заранее подготовленные отверстия.
Проверка света.
Прибыла охлаждающая жидкость и кабели. Я использовал Bitfenix для компонентов и Сorsair — для блока питания.
Слева — Bitfenix, справа — Сorsair. У Bitfenix-а нет черной термоусадки на концах, поэтому Корсар выглядит круче.
Красные стяжки, чтоб подтянуть висячие провода.
Задняя сторона. Все кабели подсоединены.
Тестируем на герметичность, пока вся система лежит на полу — так проще устранять проблемы.
Первый запуск.
Не грузится. Подключился через iROG USB к ноутбуку, чтоб посмотреть лог загрузки. Оказалось — система застряла на VGA BIOS-е. Отключил одну из видеокарт — все заработало. Попробовал подключить другую — тоже работает. Обе карты — нет. Провел небольшое исследование и выяснил, что неэкранированные PCIe-удлинители с ленточными кабелями очень восприимчивы к электромагнитным помехам. Попробовал экранировать их, обернув в несколько слоев алюминиевой фольги.
После 4-х слоев фольги мне удалось запустить обе карты. Но машина сразу висла, как только запускал любую игру или какой-нибудь 3D редактор. Мало того, мой Soundblaster тоже каскадом связан шлейфом со слотом 3 x1 PCIe, и это также сильно мешало работе видюх и вешало систему.
В результате, с болью в сердце, пришлось заказать дорогие защищенные удлинители для слотов PCIe от 3М (ок. 100$ каждый)
Экранированные удлинители 3М на месте. Они оказались длиннее предыдущих и теперь обе видеокарты дотянулись до PCIe х16.
Поменял предыдущий звук на SoundBlaster Zx. Этот выглядит потрясающе!
И напоследок
На данный момент все работает гладко. Установка имеет всего 2 вентилятора. На БП он едва шевелится, и еще один я поставил на чипсет — очень тихий. Помпа работает на самой низкой мощности, так что комп вышел довольно тихим. Единственная штука, которая раздражает — оказалось, что вне корпуса слышна работа некоторых компонентов. В моем случае это — жужжание видюх и 1ТВ винчестера.
Хладагент EK UV очень чувствителен к ультрафиолету. Я знаю, что нельзя смешивать охлаждающие жидкости, чтоб сохранить их свойства, но черт возьми, если бы я использовал ее неразбавленной — не смог бы увидеть спирали в резервуаре. Для обеих контуров я взял примерно 1/8 от банки, остальное — дистиллированная вода.
От переводчика
Никак не претендую на хоть какое-нибудь авторство это невероятного проекта. Просто я — журналист, с образованием электронщика, и заниматься такими вещами — моя мечта. И если честно, я бы сделал стол, а не стену. Вот и решил, вдруг не все Хабровчане сидят на www.overclock.net
Вот ссылка на оригинал на английском: Тыц
Вот еще несколько фоточек:
Обзор материалов / Аудиомания corporate blog / Habr
Профессиональная активная акустика Denon DN-304S
Раньше колонки представляли собой обыкновенные рупорные громкоговорители и не имели корпуса как такового. Все изменилось, когда в 20-х годах XX века появились динамики с бумажными диффузорами.
Производители начали изготавливать крупные корпуса, которые вмещали в себя всю электронику. Однако вплоть до 50-х годов многие производители аудиоаппаратуры не закрывали корпуса колонок полностью – задняя часть оставалось открытой. Это было связано с необходимостью охлаждения электронных компонентов того времени (ламповое оборудование).
Задача корпуса колонок – контроль акустической среды и удержание динамиков и других компонентов системы. Уже тогда было замечено, что корпус способен оказывать серьезное влияние на звучание громкоговорителя. Поскольку передняя и задняя части динамика излучают звук с разными фазами, то возникала усиливающая или ослабляющая интерференция, что приводило к ухудшению звука и появлению эффекта гребенчатой фильтрации.
В связи с этим начались поиски способов улучшения качества звучания. Для этого многие стали исследовать естественные акустические свойства различных материалов, пригодных для изготовления корпусов.
Волны, отраженные от внутренней поверхности стенок корпуса колонок, накладываются на основной сигнал и создают искажения, интенсивность которых зависит от плотности используемых материалов. В связи с этим часто оказывается, что корпус стоит гораздо дороже компонентов, заключенных в нем.
При производстве корпусов на крупных фабриках, все решения касательно выбора формы и толщины материалов принимаются на основании расчетов и тестов, однако Юрий Фомин, звукоинженер и инженер-конструктор акустических систем, чьи разработки лежат в основе мультимедийных систем под брендами Defender, Jetbalance и Arslab, не исключает, что даже в отсутствие специальных музыкальных знаний и большого опыта работы в аудиоиндустрии можно сделать что-то, близкое по характеристикам к «серьезному» Hi-Fi.
«Надо брать готовые разработки, которыми инженеры делятся в сети, и повторять их. Это 90% успеха», – отмечает Юрий Фомин.
При создании корпуса акустической системы следует помнить, что, в идеале, звук должен поступать только из динамиков и специальных технологических отверстий в корпусе (фазоинвертор, трансмиссионная линия) – нужно позаботиться, чтобы он не проникал через стенки колонок. Для этого рекомендуется выполнять их из плотных материалов с высоким уровнем внутреннего звукопоглощения. Вот несколько примеров того, из чего можно собрать корпус для динамиков.
Древесно-стружечная плита (ДСП)
Это доски, сделанные из спрессованной древесной стружки и клея. Материал обладает гладкой поверхностью и неплотной рыхлой сердцевиной. ДСП хорошо гасит вибрации, однако пропускает через себя звук. Плиты легко скрепляются клеем для дерева или монтажным клеем, однако их края имеют тенденцию крошиться, что немного усложняет работу с материалом. Также он боится влаги – при нарушении производственных процессов легко её впитывает и разбухает.
В магазинах продают доски разной толщины: 10, 12, 16, 19, 22 мм и так далее. Для небольших корпусов (объемом меньше 10 литров) подойдет ДСП толщиной 16 мм, а для корпусов большего размера следует выбрать доски толщиной 19 мм. ДСП можно облицовывать: обклеивать пленкой или тканью, шпаклевать и красить.
Древесно-стружечная плита используется при создании акустической системы Denon DN-304S (на фото выше). Производитель выбрал ДСП потому, что этот материал является акустически инертным: колонки не резонируют и не окрашивают звук даже при высокой громкости.
Облицованная ДСП
Это ДСП, облицованная декоративными пластиками или шпоном с одной или с двух сторон. Плиты с деревянной облицовкой скрепляются обычным клеем для дерева, однако для ДСП, облицованной пластиком, придется покупать специальный клей. Для обработки срезов доски можно воспользоваться кромочной лентой.
Столярная плита
Популярный строительный материал из реек, брусков или других наполнителей, которые оклеены с двух сторон шпоном или фанерой. Плюсы столярной плиты: относительно малый вес и простота обработки краев.
Ориентированно-стружечная плита (ОСП)
ОСП – это доски, спрессованные из нескольких слоев тонкой фанеры и клея, узор на поверхности которых напоминает мозаику желтого и коричневого цветов. Сама поверхность материала неровная, но ее можно отшлифовать и покрыть лаком, поскольку текстура дерева придает этому материалу необычный вид. Такая плита обладает высоким коэффициентом звукопоглощения и устойчива к вибрациям.
Также стоит отметить, что благодаря своим свойствам ОСП используется для формирования акустических экранов. Экраны необходимы для создания комнат прослушивания, где пользователи могут оценить звучание акустических систем в практически идеальных условиях. Полосы из ОСП крепятся на определенном расстоянии друг от друга, образуя тем самым панель Шредера. Суть решения заключается в том, что закрепленная в определенных точках полоса под воздействием акустической волны расчетной длины начинает излучать в противофазе и гасит ее.
Древесноволокнистая плита средней плотности (МДФ)
Сделанный из древесной стружки и клея, этот материал более гладкий, чем ОСП. Благодаря своей структуре МДФ хорошо подходит для изготовления дизайнерских корпусов, поскольку легко поддается распилу, – это упрощает стыковку деталей, скрепляемых между собой при помощи монтажного клея.
МДФ можно облицовывать, шпаклевать и красить. Толщина плит варьируется от 10 до 22 мм: для корпусов колонок объемом до 3 литров будет достаточно доски толщиной 10 мм, до 10 литров – 16 мм. Для больших корпусов лучше выбрать 19 мм.
Если при выборе материала для изготовления корпусов акустических систем отбросить в сторону звуковые аспекты, то останутся три определяющих параметра: низкая стоимость, простота обработки, простота склеивания. МДФ как раз обладает всеми тремя. Именно невысокая стоимость и «податливость» МДФ делают его одним из самых популярных материалов для изготовления колонок.
Пример использования МДФ – полочная акустика Arslab Classic 1 SE, стенки корпуса которой изготовлены из толстых древесноволокнистых плит, препятствующих возникновению вибраций и окрашиванию звука.
Фанера
Этот материал сделан из спрессованного и склеенного тонкого шпона (около 1 мм). Для повышения прочности фанеры слои шпона накладываются так, чтобы волокна древесины были направлены перпендикулярно волокнам предыдущего листа. Фанера – лучший материал для подавления вибраций и удержания звука внутри корпуса. Склеить фанерные доски между собой можно обычным клеем по дереву.
Шлифовать фанеру сложнее, чем МДФ, поэтому выпиливать детали нужно как можно точнее. Среди достоинств фанеры стоит выделить её легкость. По этой причине из неё часто делают кейсы для музыкальных инструментов, ведь достаточно обидно отменять концерт из-за того, что музыкант надорвал спину.
Именно этот материал применяется компанией Penaudio для производства напольной акустики – она использует латвийскую фанеру, которая изготавливается из березы. Многим нравится то, как выглядит обработанная березовая фанера, особенно после покрытия лаком, – это придает корпусу уникальности. Этим и пользуется компания: поперечные слои фанеры стали своеобразной «визитной карточкой» Penaudio.
Напольная акустика Penaudio Rebel Three
Камень
Чаще всего используются мрамор, гранит и сланец. Сланец – самый подходящий материал для изготовления корпусов: с ним достаточно просто работать из-за его структуры, и он эффективно поглощает вибрации. Главный недостаток – необходимы специальные инструменты и навыки обработки камня. Чтобы как-то упростить работу, возможно, имеет смысл изготовить из камня только переднюю панель.
Стоит отметить, что для установки колонок из камня на полку, вам может понадобиться мини-кран, да и сами полки должны быть достаточно прочными: вес каменной аудиоколонки достигает 54 кг (для сравнения, колонка из ОСП весит около 6 килограмм). Такие корпусы серьезно улучшают качество звука, но их стоимость может оказаться «неподъемной».
Колонки из цельного куска камня делают ребята из компании Audiomasons. Корпусы вырезаются из известняка и весят порядка 18 килограмм. По заявлениям разработчиков, звучание их продукта придется по вкусу даже самым искушенным меломанам.
Оргстекло/стекло
Можно сделать корпус для динамиков из прозрачного материала – это действительно круто, когда видно «внутренности» колонки. Только здесь важно помнить, что без должной изоляции звук будет ужасным. С другой стороны, если вы добавите слой звукопоглощающего материала, прозрачный корпус перестанет быть прозрачным.
Неплохим примером акустической hi-end-аппаратуры из стекла может служить Crystal Cable Arabesque. Корпуса техники Crystal Cable изготавливаются в Германии из полос стекла толщиной 19 мм со шлифованными гранями. Детали скрепляются между собой невидимым клеем в вакуумной установке, дабы избежать появления пузырьков воздуха.
На выставке CES-2010, проходившей в Лас-Вегасе, обновлённые Arabesque завоевали все три награды в области Инноваций. «До сих пор ни одному производителю техники не удавалось добиться настоящего hi-end-звучания от акустики, изготовленной из такого сложного материала. – писали критики. – Компания Crystal Cable доказала, что это возможно».
Клееная древесина/дерево
Из дерева получаются хорошие корпуса, однако здесь нужно учитывать важный момент: дерево имеет свойство «дышать», то есть оно расширяется, если воздух влажный, и сжимается, если воздух сухой.
Так как деревянный брусок проклеивается со всех сторон, в нем создается напряжение, что может привести к растрескиванию древесины. В этом случае корпус потеряет свои акустические свойства.
Металл
Чаще всего для этих целей используется алюминий, точнее – его сплавы. Они легкие и жесткие. По мнению ряда специалистов, алюминий позволяет уменьшить резонанс и улучшить передачу высоких частот звукового спектра. Все эти качества способствуют росту интереса к алюминию со стороны фирм-производителей аудиоаппаратуры, и его используют для изготовления всепогодных акустических систем.
Существует мнение, что изготовление цельнометаллического корпуса – не самая хорошая идея. Однако стоит попробовать сделать из алюминия верхние и нижние панели, а также перегородки жесткости.
Наши материалы по теме:
Деревянный корпус для ПК своими руками
Автор:01 апреля 2016 20:40
У парня не было никакого опыта работы с деревом или компьютерами, но он все равно взялся за этот проект и остался доволен результатом. Отличный урок для тех, кто боится собственных идей – воплотить их в реальность иногда проще, чем кажется.
Вот так выглядит получившийся корпус, и вы можете сделать похожий самостоятельно


Начало проекта. Автор несколько недель работал в местной столярной мастерской, где ему изготовили эту деревянную раму (420X420мм).

Первым делом он подготовил раму для боковых панелей. Долотом и молотком он сделал выемки (5X15мм) и выровнял края дремелом.

Затем он установил кулеры 2×140мм сверху и снизу. Они держатся исключительно за счет силы трения. Автор шлифовал дерево напильником до тех пор, пока кулеры идеально не встали на место.

Установить контроллеры оказалось нелегко. Они оказались слишком большими, так что их пришлось подпилить дремелом и наждачкой. В итоге он установил RGB контроллер и регулятор оборотов кулера.

При помощи напильника автор обработал алюминиевые листы, чтобы они вошли в раму.

Затем он установил блок питания.

Следом за алюминиевыми листами, он обработал напильником заранее заказанные листы оргстекла (390x390x5мм), чтобы они тоже вошли в раму.

Затем при помощи крепежных уголков и болтов он приделал к корпусу «фальш-стену».

Кнопку включения автор установил ее на боковой стене, проделав в ней отверстие.

Как сделать корпус для ПК своими руками
Сейчас можно с легкостью купить корпус для компьютера в магазине. Бывают они горизонтальными или вертикальными – это самый распространённый тип. Однако, если не брать в расчёт некоторое разнообразие передней панели, все они выглядят одинаково, отличаясь разве что цветом. Скучная металлическая коробка с парой кнопок и парой светодиодов может не удовлетворять чувство прекрасного, и тогда хочется сделать корпус для своего ПК своими руками. Бывает и другая ситуация – имеющийся в наличии перестаёт устраивать в плане функционала – в нём становится мало места или недостаточная вентиляция, отчего компоненты компьютера перегреваются. Например, иногда требуется добавить вторую видеокарту или несколько винчестеров, и стандартный корпус становится малоподходящим для всего этого. Случаются и другие ситуации, когда корпус для компьютера приходится делать самому. Например, все деньги потрачены на топовые комплектующие, а на корпус бюджета не хватает. Или имеется ноутбук с неисправным дисплеем, и его хочется превратить в настольный. Случаи бывают разными, но объединяет их одно – нужно брать в руки инструменты и делать корпус для компьютера своими собственными руками.
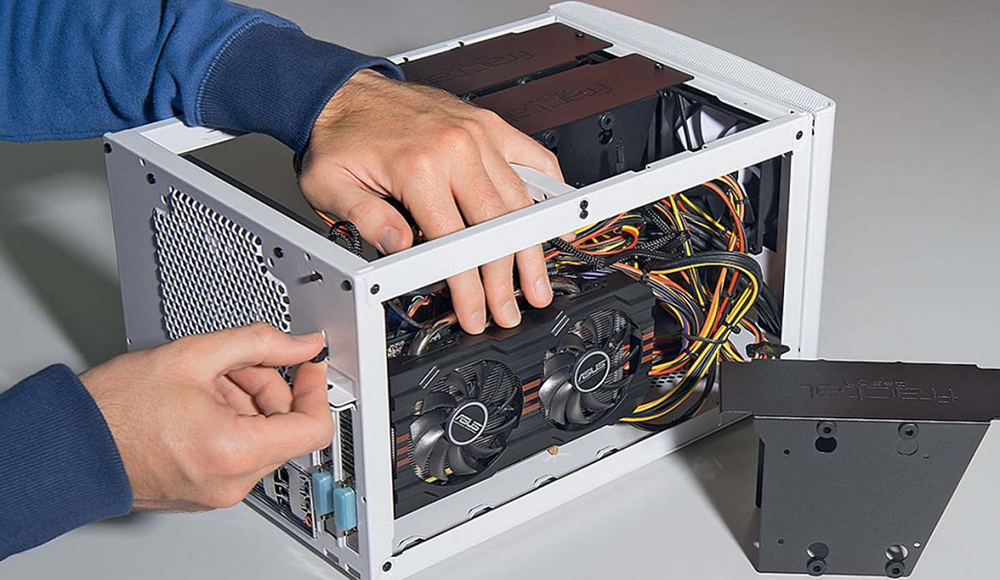
Создание корпуса для ПК самостоятельно.
Что нужно обязательно учитывать
Самое важное требование для любого компьютерного корпуса, в том числе и самодельного – достаточное пространство для вентиляции и охлаждения. В стандартных, самых распространённых корпусах типа Moddle-Tower Form не случайно имеется много пустого пространства. Это позволяет воздуху свободно циркулировать, а при установке энергоёмких компонентов есть возможность добавления дополнительных вентиляторов. Поэтому при разработке самодельной конструкции надо учитывать не только габариты всех комплектующих, но и предусмотреть свободное место для циркуляции воздушных потоков около каждого из них. Также надо решить, как будет установлен блок питания. Есть два варианта:
- Сверху. Это классическая схема, при которой сквозь блок питания наружу проходит теплый воздух. Так обеспечивается вентиляция и достигается небольшой уровень шума. Но есть и минус – блок питания может сам перегреваться, если других кулеров нет. Схему корпуса системника с верхним расположением блока питания обычно применяют и для создания своими руками.
- Снизу. В таком случае блок питания ставится на дно корпуса, и воздух в него поступает снизу, через решетку, и выдувается через другую стенку наружу. Плюс – блок питания хорошо охлаждается исключительно «забортным воздухом». Минус – он совсем не участвует в системе охлаждения системы в целом, поэтому обязательно нужны кулеры. Другой минус – приток воздуха к блоку питания происходит под днищем корпуса и может быть затруднённым. К тому же, будет повышен уровень шума – его создаёт движение воздуха внизу, плюс шум от вентилятора передаётся непосредственно на поверхность.
Если выбрать горизонтальный вариант – тип Desktop, то требования остаются теми же, разве что места для манёвров с блоком питания меньше. Однако вентиляцию надо обязательно обеспечить для всех узлов.
Какой материал выбрать
Корпус для компьютера, сделанный своими руками, должен быть не только красивым, но и прочным и функциональным. Хотя некоторые делают его даже из коробочного картона, это совсем несерьёзно. Обычно выбирают такие материалы:
- Дерево.
- Оргстекло.
- Алюминий.
- Сталь.
Каждый вариант имеет свои преимущества и недостатки. Рассмотрим их подробнее.
Дерево легко обрабатывается, можно использовать листовой материал – фанеру, ДСП и т.д. Корпус из дерева можно сделать, даже не имея большого опыта и дорогостоящих инструментов. Он обеспечит довольно низкий уровень шума. Однако у этого материала будет один недостаток – плохая теплопередача, поэтому внутри надо предусмотреть достаточное свободное пространство и хорошее охлаждение.
Оргстекло – легко пилится и режется, корпус при должной аккуратности получается довольно профессиональным. Такой вариант обычно выбирают любители моддинга – создатели красивых и оригинальных прозрачных корпусов с множеством подсветок внутри. Из недостатков – этот материал всё-таки требует умения с ним обращаться и навыков по его обработке. Неловкое движение – и длинная глубокая царапина обеспечена.
Алюминий имеет массу достоинств, н главные – он лёгкий и имеет хорошую теплоотдачу. Однако это сравнительно дорогой материал, к тому же из-за гибкости алюминия жесткость корпуса и внутренних перегородок будет слабовата. Да и царапается он легко, поэтому требуется обработка поверхности. Сталь отлично гасит вибрации, имеет хорошую теплопроводность, и прочная. Стальной корпус надёжно защитит внутренние узлы от любых воздействий. Но для обработки стали нужны разные инструменты, да и работа эта не из лёгких. Зато результат получается отличным.
Перед тем, как самому сделать корпус для компьютера, вопрос с материалом нужно обязательно решить. Если навыков работы с металлом нет, а хочется использовать именно его, можно сделать так – спроектировать все выкройки и сделать чертежи. Во многих городах есть мастерские и предприятия, где по чертежам на заказ точно вырежут и даже доставят все детали, из металла нужной толщины. Останется только собрать этот конструктор. С деревянными заготовками можно поступить так же.
Дизайн корпуса
Здесь трудно давать какие-то советы – всё строго индивидуально. Делать корпус со стандартным дизайном можно только от нужды, когда нет денег его купить, хотя стоит он не так уж много. Поэтому за эту работу берутся обычно люди творческие, чтобы сделать нечто оригинальное, чего нет ни у кого. Или чтобы решить какую-то техническую задачу – например, содержимое ноутбука поместить в отдельный корпус и закрепить это сзади телевизора. Любители моддинга – экспериментов с дизайном компьютерного корпуса, каких только вариантов не создали. Это и настенные варианты, в том числе в виде панели под стеклом. Это и многочисленные прозрачные корпуса с эффектной подсветкой кулеров и прочих узлов.
Некоторые даже устроили его из столешницы стола со стеклянной поверхностью. Формы тоже могут быть разными – от классических параллелепипедов до шарообразных или пирамидальных. Бывают и более сложные – в форме каких-нибудь персонажей, например, робота R2-D2 из «Звёздных войн». Неплохо выглядят корпуса, сделанные в стиле ретро. Например, эффектна модель, стилизованная под ламповую советскую аппаратуру, с множеством циферблатов и рукояток на передней панели – они, кстати, функционируют, и показывают загрузку процессора, памяти, и другие параметры. Футуристический и постапокалиптический дизайн тоже популярен. Множество компьютеров оформлено в стиле игры Fallout.
Корпус ПК, созданный своими руками, всегда имеет персональный дизайн, потому что существует в единственном экземпляре. Однако, прежде чем браться за это творческое дело, не забудьте просчитать и обеспечить все технические моменты, о которых шла речь в начале статьи. Как бы ни выглядел корпус вашего компьютера внешне, для внутренних устройств должны создаваться комфортные условия работы даже при максимальной нагрузке.
вырастить или фрезеровать? / Promwad corporate blog / Habr
Наша предыдущая статья об изготовлении рабочего прототипа электронного устройства вызвала много вопросов и обсуждений в комментариях, поэтому мы решили продолжить эту тему и сфокусироваться на создании прототипов корпусов и механизмов для электроники, чтобы вам было проще ориентироваться в различных материалах и технологиях прототипирования, которые предлагают современные производители.
Как всегда, уделим внимание самым актуальным вопросам и дадим полезные советы, исходя из нашей практики:
- Из каких материалов делается прототип корпус для электронных устройств?
- Обзор современных технологий прототипирования: что выбрать? Тут мы рассмотрим разные 3D-принтеры и сравним их с технологией фрезеровки на станках с ЧПУ.
- Как выбрать изготовителя прототипа, какие документы предоставить подрядчику?
1. Из чего делается прототип корпус для электронных устройств?
Оптимальные материалы для корпуса электроники подбирают с учетом требований дизайна, назначения прибора (условий работы), предпочтений заказчика и ценовой категории разработки. Современные технологии позволяют использовать следующие материалы для изготовления прототипов:
- Различных видов пластика: ABS, PC, PA, PP и т.д. Для корпусов, требующих повышенной ударопрочности или устойчивости к воздействию агрессивных сред, используются полиамиды и полиформальдегиды (PA, POM)
- Металлов: алюминий, различные марки нержавеющей стали, алюминиево-магниевые сплавы и др.
- Стекло
- Резина
- Древесина (различные породы) и прочие экзотические материалы
Не все материалы поддаются прототипированию. Например, некоторые виды пластиков, которые используются при массовом производстве электронных устройств. В этом случае для изготовления прототипов используются аналоги, которые наиболее полно передают свойства основных материалов.
При совмещении в одном корпусе различных типов материалов важно получить консультацию специалистов, они помогут грамотно реализовать места стыковки, обеспечат нужные параметры герметичности, прочности, гибкости, т.е. сопоставят желания клиента и дизайнера устройства с реальными производственными возможностями.
2. Обзор современных технологий прототипирования: что выбрать?
Прототипы корпуса могут создаваться на оборудовании для серийного производства, но при этом используются другие технологии. Например, пластик не отливается, а фрезеруется или выращивается, поскольку создание литьевой пресс-формы — это длительный и дорогостоящий процесс.
Самые распространенные на сегодня технологии прототипирования — это фрезерование и выращивание (SLA, FDM, SLS).
Особой популярностью пользуется выращивание прототипов в 3D-принтерах, эта модная технология стремительно развивается и даже наслаивается на массовое производство. Сегодня выращивают самые разные изделия, вплоть до металлических изделий и пищевых продуктов, но всё это имеет свои ограничения. Рассмотрим эти технологии более подробно, а в конце попробуем выбрать оптимальный вариант для создания прототипа корпуса:
SLA (Stereo Lithography Apparatus) — технология стереолитографии, позволяет «выращивать» модель в жидком фотополимере, который затвердевает под воздействием ультрафиолетового лазера. Преимущества: высокая точность и возможность создания крупногабаритных моделей. Качественная поверхность SLA-прототипов легко поддается финальной обработке (ее можно шлифовать и красить). Важный недостаток технологии — хрупкость модели, SLA-прототипы не годятся для вкручивания саморезов или проверки корпусов на защелках.
SLS (Selective Laser Sintering) — технология селективного лазерного спекания, позволяет создавать прототип за счет послойного оплавления порошка. Преимущества: высокая точность и прочность, возможность получить образцы из пластика и металлов. SLS-прототипы позволяют проводить сборочные испытания корпусов с использованием шарниров, защелок и сложных узлов. Недостаток: более сложная обработка поверхности.
FDM (Fused Deposition Modeling) — технология послойного выращивания полимерной нитью. Преимущества: максимальная приближенность полученного образца к заводской версии устройства (до 80% прочности по сравнению с литьем пластика). FDM-прототип можно испытывать на функциональность, собираемость и климатику. Детали такого корпуса поддаются склейке и ультразвуковой сварке, можно использовать материалы ABS+PC (АБС-пластик + поликарбонат). Недостатки: среднее качество поверхности, сложности при финальной обработке.
Как видно, ограничения различных технологий выращивания не позволяют точно воспроизвести и передать тактильные характеристики корпуса. На основании прототипа нельзя будет сделать выводы о реальном внешнем виде устройства без дополнительной обработки. Обычно при выращивании может использоваться ограниченное количество материалов, чаще всего от одного до трех типов пластика. Главное достоинство этих методов – относительная дешевизна, но тут важно учесть, что дополнительная обработка, которая требуется для качественного внешнего вида изделия, перекрывает это достоинство. Более того, на качество прототипа влияет и точность выращивания, которая недостаточна для создания корпусов небольшого размера. А после обработки и полировки поверхности становится еще ниже.
При этом фрезеровка на станках с числовым программным управлением (ЧПУ) позволяет достичь точности изготовления одного порядка с точностью массового производства. При этом можно использовать абсолютное большинство материалов, которые используются при массовом изготовлении корпусов. Основной недостаток фрезеровки — высокая трудоемкость и необходимость использования дорогостоящего оборудования, что обуславливает высокую стоимость этой технологии. Хотя эти затраты вполне сопоставимы с выращиванием корпуса, если учитывать длительную и дорогостоящую финальную обработку поверхности.
3. Как выбрать изготовителя прототипа, какие документы предоставить подрядчику?
При выборе подрядчика для изготовления прототипов стоит обратить внимание на следующие особенности:
- Готовые прототипы должны быть полнофункциональными, максимально приближенными к серийным изделиям, чтобы их можно было использовать для сертификации, демонстрации инвестору, на выставках и презентациях.
- Производитель должен работать с широким набором различных материалов и технологий, оказывать консультации по их выбору. Так вы сможете подобрать оптимальный вариант для вашего конкретного проекта.
- Желательно, чтобы у подрядчика была база проверенных производителей как в СНГ, так и в Юго-Восточной Азии, чтобы вы получили оценку различных вариантов по срокам и стоимости изготовления различных компонентов вашего устройства. Так будет проще выбрать оптимальный вариант.
Напомним, что для изготовления прототипа корпуса вам нужно будет передать подрядчику сборочный чертеж либо 3D-модель в виде файла в формате STEP.
Мы надеемся, что наши советы помогут вам создать собственный прототип корпуса для электроники! Вопросы и комментарии приветствуются.