ООО «Кондор-электро» — АСКПЗ
ГОСТ 839-80
1. Преимущественная область применения
Провода предназначены для передачи электрической энергии в воздушных электрических сетях на суше всех макроклиматических районов по ГОСТ 15150 исполнения УХЛ, провода АСК, АСКС, АСКП — на побережьях морей, соленых озер, в промышленных районах и районах засолоненных песков, провода АС, кроме исполнения ТВ и ТС, провода АСК и АСКС, кроме исполнения ТВ.
2. Конструкция
Провода состоят из стального сердечника и алюминиевых проволок.
В проводе марки АСК стальной сердечник покрыт нейтральной смазкой повышенной нагревостойкости и изолирован двумя лентами полиэтилентерефталатной пленки. В проводе марки АСКС межпроволочное пространство стального сердечника, включая его наружную поверхность, заполнено нейтральной смазкой повышенной нагревостойкости. В проводе марки АСКП межпроволочное пространство всего провода, за исключением наружной поверхности, заполнено нейтральной смазкой повышенной нагревостойкости.
Материалы:
— алюминий содержания 99,5; 99,7%;
— проволока стальная оцинкованная 1 или 2 группы по качеству цинкового покрытия — ГОСТ 9850;
— в проводах марок АСК, АСКС, АСКП нейтральная нагревостойкая смазка с температурой каплепадения не менее 105°С и стальная проволока 2-ой группы. При применении проволоки с цинковым покрытием 2 группы марка провода обозначается «АС2».
3. Указания по монтажу и эксплуатации
Длительно допустимая температура проводов в процессе эксплуатации не должна превышать 90°С.
4. Основные характеристики материалов:
Параметры | Проволока алюминиевая | Проволока стальная |
Удельное электрическое сопротивление постоянному току при 20 °С, ОМ·мм2/м не более |
0,028264 | — |
Температурный коэффициент электросопротивления при неизменной массе, на 1 °С | 0,00403 | — |
Временное сопротивление разрыву, МПа (Н/ мм2) | 160-195 | 1290-1450 |
Напряжение при 1%-ном удлинении, МПа (Н/ мм2) | — | 1100-1310 |
5. Характеристики материалов
Номинальное сечение, мм2 |
Диаметр провода, мм |
Электрическое сопротивление 1 км провода постоянному току при 20°С, 0м, не более | Разрывное усилие провода, Н, не менее |
Масса 1 км провода, |
16/2,7 | 5,6 | 1,7818 | 6220 | 64,9 |
25/4,2 | 6,9 | 1,1521 | 9296 | 100,3 |
35/6,2 | 8,4 | 0,7774 | 13524 | 148 |
50/8,0 | 9,6 | 0,5951 | 17112 | 195 |
70/11 | 11,4 | 0,4218 | 24130 | 276 |
70/72 | 15,4 | 0,4194 | 96826 | 755 |
95/16 | 13,5 | 0,3007 | 33369 | 385 |
95/141 | 19,8 | 0,3146 | 180775 | 1357 |
120/19 | 15,2 | 0,244 | 471 | |
120/27 | 15,4 | 0,2531 | 49465 | 528 |
150/19 | 16,8 | 0,2046 | 46307 | 554 |
150/24 | 17,1 | 0,2039 | 52279 | 599 |
150/34 | 17,5 | 0,2061 | 62643 | 675 |
185/24 | 0,154 | 58075 | 705 | |
185/29 | 18,8 | 0,1591 | 62055 | 728 |
185/43 | 19,6 | 0,1559 | 77767 | 846 |
185/128 | 23,1 | 0,1543 | 183816 | 1525 |
205/27 | 19,8 | 0,1407 | 63740 | 774 |
240/32 | 21,6 | 0,1182 | 75050 | 921 |
240/39 | 21,6 | 0,1222 | 80895 | 952 |
240/56 | 22,4 | 0,1197 | 98253 | 1106 |
300/39 | 24 | 0,0958 | 90574 | 1132 |
300/48 | 24,1 | 0,0978 | 100623 | 1186 |
300/66 | 24,5 | 0,1 | 117520 | 1313 |
300/67 | 24,5 | 0,1 | 126270 | 1323 |
300/204 | 29,2 | 0,0968 | 284579 | 2428 |
330/30 | 24,8 | 0,0861 | 88848 | 1152 |
330/43 | 25,2 | 0,0869 | 103784 | 1255 |
400/18 | 26 | 0,0758 | 85600 | 1199 |
400/22 | 26,6 | 0,0733 | 95115 | 1261 |
400/51 | 27,5 | 0,0733 | 120481 | 1490 |
400/64 | 27,7 | 0,0741 | 129183 | 1572 |
400/93 | 29,1 | 0,0711 | 173715 | 1851 |
450/56 | 28,8 | 0,0666 | 131370 | 1640 |
500/26 | 30 | 0,0575 | 112548 | 1592 |
500/27 | 29,4 | 0,06 | 112188 | 1537 |
500/64 | 30,6 | 0,0588 | 148257 | 1852 |
500/204 | 34,5 | 0,058 | 319609 | 2979 |
500/336 | 37,5 | 0,0588 | 466649 | 4005 |
550/71 | 32,4 | 0,0526 | 166164 | 2076 |
600/72 | 33,2 | 0,0498 | 183835 | 2170 |
605/79 | 34,7 | 0,0456 | 200451 | 2372 |
700/86 | 36,2 | 0,042 | 217775 | 2575 |
750/93 | 37,7 | 0,0386 | 234450 | 2800 |
800/105 | 39,7 | 0,0352 | 260073 | 3092 |
1000/56 | 42,4 | 0,0288 | 224047 | 3210 |
Каталог:
| Главная / Нихром, фехраль / Сопротивление нихромовой проволоки Номинальное значение сопротивления нихромовой проволоки
Удельное значение электрического сопротивления
Обрашаем Ваше внимание на то, что в формуле расчета электронагревательных элементов используем номинальное значение электрического сопротивления нихромовой проволоки из верхней таблицы. |
8 (800) 200-52-75 (495) 366-00-24 (495) 504-95-54 (495) 642-41-95 | |||||||||||||||||||||||||||||||||||||||||||||||||||||||||||||||||||||||||||||||||||||||||||||||||||||||||||||||||||||||||||||||||||||||||||||||||||||||||||||||||||||||||||||||||||||||||||||||||||||||||||||||||||||||||||||||||||||||||||||||||||||||||||||||||||||||||||||||||||||||||||||||||||||||||||||||||||||||||||||||||||||||||||||||||||||||||||||||||||||||||||||||||||||||||||||||||||||||||||||||||||||||||||||||||||||||||||||||||||||||||||||||||||||||||||||||||||||||||||||||||||||||||||||||||||||||||||||||||||||||||||||||||||||||||||||||||||||||||||||||||||
e-mail: [email protected] | e-mail: [email protected] | ||||||||||||||||||||||||||||||||||||||||||||||||||||||||||||||||||||||||||||||||||||||||||||||||||||||||||||||||||||||||||||||||||||||||||||||||||||||||||||||||||||||||||||||||||||||||||||||||||||||||||||||||||||||||||||||||||||||||||||||||||||||||||||||||||||||||||||||||||||||||||||||||||||||||||||||||||||||||||||||||||||||||||||||||||||||||||||||||||||||||||||||||||||||||||||||||||||||||||||||||||||||||||||||||||||||||||||||||||||||||||||||||||||||||||||||||||||||||||||||||||||||||||||||||||||||||||||||||||||||||||||||||||||||||||||||||||||||||||||||||||
Рассчитать нагреватели электрической печи Калькулятор нагревателей электрических печейПараметры электрической печи Мощность печи, Вт
?
Тип электросети
?
Напряжение на концах нагревателя, Вольт
Материал нагревателя
Температура нагревателя, °C
?
Температура нагреваемого изделия, °C
?
Тип нагревателей
Конструкция и размещение нагревателей
?
Параметры нагревателя Диаметр нагревателя, мм
Размеры нагревателей (толщина x ширина), мм Выбрать из стандартных размеров (толщина х ширина), мм
?
Толщина нагревателя, мм
Ширина нагревателя, мм
Длина нагревателя, м
Масса нагревателя, кг
Общая длина нагревателей, м
Общая масса нагревателей, кг
*Результаты расчета нагревателей электрических печей, выполненного с помощью данного калькулятора, носят информативный характер. Расчет основан на подходе, рассмотренном в книге «Типовые расчеты по электрооборудованию», Дьяков В.И., а также в статье «Нагреватели. Методика и примеры расчета», Никонов Н. В., и содержит ряд допущений. В каждом конкретном случае могут появиться дополнительные условия, связанные с конструктивными особенностями печи, а также условиями эксплуатации. Очень часто при желании сделать или отремонтировать нагреватель электропечи своими руками у человека появляется много вопросов. Например, какого диаметра взять проволоку, какова должна быть ее длина или какую мощность можно получить, используя проволоку или ленту с заданными параметрами и т.д. При правильном подходе к решению данного вопроса необходимо учитывать достаточно много параметров, например, силу тока, проходящего через нагреватель, рабочую температуру, тип электрической сети и другие. В данной статье приводятся справочные данные о материалах, наиболее распространенных при изготовлении нагревателей электрических печей, а также методика и примеры их расчета (расчета нагревателей электрических печей). Непосредственно нагреватель – один из самых важных элементов печи, именно он осуществляет нагрев, имеет наибольшую температуру и определяет работоспособность нагревательной установки в целом. Поэтому нагреватели должны соответствовать ряду требований, которые приведены ниже. Требования к нагревателямОсновные требования к нагревателям (материалам нагревателей):
Материалы для изготовления нагревателей Наиболее подходящими и самыми используемыми в производстве нагревателей для электропечей являются прецизионные сплавы с высоким электрическим сопротивлением. К ним относятся сплавы на основе хрома и никеля (хромоникелевые), железа, хрома и алюминия (железохромоалюминиевые). Марки и свойства данных сплавов рассмотрены в ГОСТ 10994-74 «Сплавы прецизионные. Марки». Представителями хромоникелевых сплавов является нихром марок Х20Н80, Х20Н80-Н (950-1200 °С), Х15Н60, Х15Н60-Н (900-1125 °С), железохромоалюминиевых – фехраль марок Х23Ю5Т (950-1400 °С), Х27Ю5Т (950-1350 °С), Х23Ю5 (950-1200 °С), Х15Ю5 (750-1000 °С). Также существуют железохромоникелевые сплавы — Х15Н60Ю3, Х27Н70ЮЗ. Перечисленные выше сплавы обладают хорошими свойствами жаропрочности и жаростойкости, поэтому они могут работать при высоких температурах. Хорошую жаростойкость обеспечивает защитная пленка из окиси хрома, которая образуется на поверхности материала. Температура плавления пленки выше температуры плавления непосредственно сплава, она не растрескивается при нагреве и охлаждении. Приведем сравнительную характеристику нихрома и фехрали.
Недостатки нихрома:
Достоинства фехрали:
Недостатки фехрали:
Также сравнение сплавов фехраль и нихром производится в статье Сравнение сплавов фехраль и нихром. В последнее время разработаны сплавы типа Х15Н60Ю3 и Х27Н70ЮЗ, т.е. с добавлением 3% алюминия, что значительно улучшило жаростойкость сплавов, а наличие никеля практически исключило имеющиеся у железохромоалюминиевых сплавов недостатки. Сплавы Х15Н60ЮЗ, Х27Н60ЮЗ не взаимодействуют с шамотом и окислами железа, достаточно хорошо обрабатываются, механически прочны, нехрупки. Максимальная рабочая температура сплава Х15Н60ЮЗ составляет 1200 °С. Помимо перечисленных выше сплавов на основе никеля, хрома, железа, алюминия для изготовления нагревателей применяют и другие материалы: тугоплавкие металлы, а также неметаллы. Среди неметаллов для изготовления нагревателей используют карборунд, дисилицид молибдена, уголь, графит. Нагреватели из карборунда и дисилицида молибдена используют в высокотемпературных печах. Среди тугоплавких материалов в качестве нагревателей могут использоваться вольфрам, молибден, тантал и ниобий. В высокотемпературных вакуумных печах и печах с защитной атмосферой применяются нагреватели из молибдена и вольфрама. Молибденовые нагреватели могут работать до температуры 1700 °С в вакууме и до 2200 °С – в защитной атмосфере. Такая разница температур обусловлена испарением молибдена при температурах выше 1700 °С в вакууме. Вольфрамовые нагреватели могут работать до 3000 °С. В особых случаях применяют нагреватели из тантала и ниобия. Обычно в качестве исходных данных для расчета нагревателей электрических печей выступают мощность, которую должны обеспечивать нагреватели, максимальная температура, которая требуется для осуществления соответствующего технологического процесса (отпуска, закалки, спекания и т. . В ходе расчета нагревателей требуется получить диаметр и длину (для проволоки) или площадь сечения и длину (для ленты), которые необходимы для изготовления нагревателей. Также необходимо определить материал, из которого следует делать нагреватели (данный пункт в статье не рассматривается). В данной статье в качестве материала для нагревателей рассматривается хромоникелевый прецизионный сплав с высоким электрическим сопротивлением нихром Х20Н80, который является одним из самых популярных при изготовлении нагревательных элементов. Определение диаметра и длины нагревателя (нихромовой проволоки) для заданной мощности печи (простой расчет) Пожалуй, наиболее простым вариантом расчета нагревателей из нихрома является выбор диаметра и длины нихромовой проволоки при заданной мощности нагревателя, питающего напряжения сети, а также температуры, которую будет иметь нагреватель. Пример расчета диаметра и длины нагревательного элемента Исходные данные: 1. Сначала необходимо определить силу тока, которая будет проходить через нагревательный элемент: 2. Теперь нужно найти сопротивление нагревателя: 3. Исходя из значения полученной в п. 1 силы тока, проходящего через нихромовый нагреватель, нужно выбрать диаметр проволоки. И этот момент является важным. Если, например, при силе тока в 6 А использовать нихромовую проволоку диаметром 0,4 мм, то она сгорит. Общее правило выбора диаметра проволоки можно сформулировать следующим образом: необходимо выбрать проволоку, у которой допустимая сила тока не меньше, чем расчетная сила тока, проходящего через нагреватель. С целью экономии материала нагревателя следует выбирать проволоку с ближайшей большей (чем расчетная) допустимой силой тока. Таблица 1
Примечание:
4. Далее определим длину нихромовой проволоки. Таким образом, получим длину нагревателя: В данном примере в качестве нагревателя используется нихромовая проволока Ø 0,35 мм. В соответствии с ГОСТ 12766.1-90 «Проволока из прецизионных сплавов с высоким электрическим сопротивлением. Технические условия» номинальное значение удельного электрического сопротивления нихромовой проволоки марки Х20Н80 составляет 1,1 Ом · мм2 / м (ρ = 1,1 Ом · мм2 / м), см. Итогом расчетов является необходимая длина нихромовой проволоки, которая составляет 5,3 м, диаметр — 0,35 мм. Таблица 2
Определение диаметра и длины нагревателя (нихромовой проволоки) для заданной печи (подробный расчет) Расчет, представленный в данном пункте, является более сложным, чем выше. 1. Первое, что необходимо сделать — посчитать объем камеры внутри печи. В данном случае возьмем h = 490 мм, d = 350 мм и l = 350 мм (высота, ширина и глубина соответственно). Таким образом, получаем объем V = h · d · l = 490· 350 · 350 = 60 · 10 6 мм3 = 60 л (мера объема). 2. Далее необходимо определить мощность, которую должна выдавать печь. Мощность измеряется в Ваттах (Вт) и определяется по эмпирическому правилу: для электрической печи объемом 10 — 50 литров удельная мощность составляет 100 Вт/л (Ватт на литр объема), объемом 100 — 500 литров — 50 — 70 Вт/л. Возьмем для рассматриваемой печи удельную мощность 100 Вт/л. Стоит отметить, что при мощности 5-10 кВт нагреватели изготовляют, обычно, однофазными. При больших мощностях для равномерной загрузки сети нагреватели делают трехфазными. 3. Затем нужно найти силу тока, проходящего через нагреватель I = P / U, где P — мощность нагревателя, U — напряжение на нагревателе (между его концами), и сопротивление нагревателя R = U / I. Здесь может быть два варианта подключения к электрической сети:
Далее расчет будет проведен отдельно для однофазного и трехфазного подключения. Бытовая сеть однофазного тока I = P / U = 6000 / 220 = 27,3 А — ток проходящий через нагреватель. Рисунок 1 Проволочный нагреватель в сети однофазного тока Искомые значения диаметра проволоки и ее длины будут определены в п. 5 данного параграфа. Промышленная сеть трехфазного тока При данном типе подключения нагрузка распределяется равномерно на три фазы, т.е. по 6 / 3 = 2 КВт на фазу. Таким образом, нам требуется 3 нагревателя. Далее необходимо выбрать способ подключения непосредственно нагревателей (нагрузки). Способов может быть 2: “ЗВЕЗДА” или “ТРЕУГОЛЬНИК”. Стоит заметить, что в данной статье формулы для расчета силы тока (I) и сопротивления (R) для трехфазной сети записаны не в классическом виде. Это сделано для того, чтобы не усложнять изложение материала по расчету нагревателей электротехническими терминами и определениями (например, не упоминаются фазные и линейные напряжения и токи и соотношения между ними). При подключении типа “ЗВЕЗДА” нагреватель подключается между фазой и нулем (см. рис. 2). Соответственно, напряжение на концах нагревателя будет U = 220 В. Рисунок 2 Проволочный нагреватель в сети трехфазного тока. Подключение по схеме «ЗВЕЗДА» При подключении типа “ТРЕУГОЛЬНИК” нагреватель подключается между двумя фазами (см. рис. 3). Соответственно, напряжение на концах нагревателя будет U = 380 В. Рисунок 3 Проволочный нагреватель в сети трехфазного тока. Подключение по схеме «ТРЕУГОЛЬНИК» 4. После определения сопротивления нагревателя при соответствующем подключении к электрической сети необходимо подобрать диаметр и длину проволоки. При определении указанных выше параметров необходимо анализировать удельную поверхностную мощность нагревателя, т.е. мощность, которая выделяется с единицы площади. Поверхностная мощность нагревателя зависит от температуры нагреваемого материала и от конструктивного выполнения нагревателей. Пример Полученная поверхностная мощность слишком велика. Приведенный пример является демонстрацией неправильного выбора диаметра проволоки, которая будет использоваться для изготовления нагревателя. В п. 5 данного параграфа будет приведен пример с правильным подбором диаметра. Для каждого материала в зависимости от требуемой температуры нагрева определено допустимое значение поверхностной мощности. Оно может определяться с помощью специальных таблиц или графиков. В данных расчетах используются таблицы. Для высокотемпературных печей (при температуре более 700 – 800 °С) допустимая поверхностная мощность, Вт/м2, равна βдоп = βэф · α, где βэф – поверхностная мощность нагревателей в зависимости от температуры тепловоспринимающей среды [Вт / м2], α – коэффициент эффективности излучения. Если печь низкотемпературная (температура менее 200 – 300 °С), то допустимую поверхностную мощность можно считать равной (4 — 6) · 104 Вт/м2. Таблица 3
Таблица 4
Предположим, что температура нагревателя 1000 °С, и хотим нагреть заготовку до температуры 700 °С. 5. После определения допустимой поверхностной мощности нагревателя необходимо найти его диаметр (для проволочных нагревателей) или ширину и толщину (для ленточных нагревателей), а также длину. Диаметр проволоки можно определить по следующей формуле: , где d — диаметр проволоки, [м]; P — мощность нагревателя, [Вт]; U — напряжение на концах нагревателя, [В]; βдоп — допустимая поверхностная мощность нагревателя, [Вт/м2]; ρt — удельное сопротивление материала нагревателя при заданной температуре, [Ом·м]. Длину проволоки можно определить по следующей формуле: , где l — длина проволоки, [м]. Подберем диаметр и длину проволоки из нихрома Х20Н80. Удельное электрическое сопротивление материала нагревателя составляет Бытовая сеть однофазного тока Полученный размер необходимо округлить до ближайшего большего стандартного. Длина нагревателя l = 43 м. Также иногда требуется определить массу необходимого количества проволоки. В нашем случае масса нагревателя m = l · μ = 43 · 0,052 = 2,3 кг. Данный расчет дает минимальный диаметр проволоки, при котором она может быть использована в качестве нагревателя при заданных условиях. С точки зрения экономии материала такой расчет является оптимальным. При этом также может быть использована проволока большего диаметра, но тогда ее количество возрастет. Проверка Теперь необходимо проверить, не превысит ли поверхностная мощность выбранного нами нагревателя допустимую поверхностную мощность, которая была найдена в п. 4. β = P / S = 6000 / (3,14 · 4300 · 0,28) = 1,59 Вт/см2. Полученное значение β = 1,59 Вт/см2 не превышает βдоп = 1,6 Вт/см2. Итоги Промышленная сеть трехфазного тока Как описано в п. 3, на каждый из трех нагревателей приходится по 2 КВт мощности. Найдем диаметр, длину и массу одного нагревателя. Подключение типа “ЗВЕЗДА” (см. рис. 2) В данном случае, ближайшим большим стандартным размером является Ø 1,4 мм. Диаметр нагревателя d = 1,4 мм. Длина одного нагревателя l = 30 м. Проверка Поверхностная мощность составит β = P / S = 2000 / (3,14 · 3000 · 0,14) = 1,52 Вт/см2, она не превышает допустимую. Итоги Подключение типа “ТРЕУГОЛЬНИК” (см. рис. 3) В данном случае, ближайшим большим стандартным размером является Ø 0,95 мм. Диаметр нагревателя d = 0,95 мм. Длина одного нагревателя l = 43 м. Проверка Данное значение практически совпадает со значением, полученным в результате другого расчета. Поверхностная мощность составит β = P / S = 2000 / (3,14 · 4300 · 0,095) = 1,56 Вт/см2, она не превышает допустимую. Итоги Если сравнить 2 рассмотренных выше варианта подключения нагревателей к сети трехфазного тока, то можно заметить, что для “ЗВЕЗДЫ” требуется проволока большего диаметра, чем для “ТРЕУГОЛЬНИКА” (1,4 мм против 0,95 мм), чтобы обеспечить заданную мощность печи 6 кВт. При этом требуемая длина нихромовой проволоки при подключении по схеме “ЗВЕЗДА” меньше длины проволоки при подключении типа “ТРЕУГОЛЬНИК” (90 м против 129 м), а требуемая масса, наоборот, больше (1,2 кг против 0,8 кг). Расчет спиралиПри эксплуатации основная задача — это разместить нагреватель расчетной длины в ограниченном пространстве печи. Нихромовая и фехралевая проволока подвергаются навивке в виде спиралей или сгибанию в форме зигзагов, лента сгибается в форме зигзагов, что позволяет вместить большее количество материала (по длине) в рабочую камеру. Наиболее распространенным вариантом является спираль. Соотношения между шагом спирали и ее диаметром и диаметром проволоки выбирают таким образом, чтобы облегчить размещение нагревателей в печи, обеспечить достаточную их жесткость, в максимально возможной степени исключить локальный перегрев витков самой спирали и в то же время не затруднить теплоотдачу от них к изделиям. Чем больше диаметр спирали и чем меньше ее шаг, тем легче разместить в печи нагреватели, но с увеличением диаметра уменьшается прочность спирали, увеличивается склонность ее витков лечь друг на друга. Практика установила вполне определенные, рекомендуемые соотношения между диаметром проволоки (d), шагом (t) и диаметром спирали (D) для проволоки Ø от 3 до 7 мм. Эти соотношения следующие: t ≥ 2d и D = (7÷10)·d для нихрома и D = (4÷6)·d — для менее прочных железохромоалюминиевых сплавов, таких как фехраль и т.п. Для более тонких проволок отношение D и d, а также t обычно берутся больше. В статье были рассмотрены различные аспекты, касающиеся расчета нагревателей электрических печей — материалы, примеры расчета с необходимыми справочными данными, ссылками на стандарты, иллюстрациями. В примерах были рассмотрены методики расчета только проволочных нагревателей. Помимо проволоки из прецизионных сплавов для изготовления нагревателей может применяться и лента. Расчет нагревателей не ограничивается выбором их размеров. Также необходимо определить материал, из которого должен быть сделан нагреватель, тип нагревателя (проволочный или ленточный), тип расположения нагревателей и другие особенности. Если нагреватель изготавливается в виде спирали, то необходимо определить количество витков и шаг между ними. Надеемся, что статья оказалась Вам полезной. Мы допускаем её свободное распространение при условии сохранения ссылки на наш сайт http://www.metotech.ru В случае обнаружения неточностей, просим сообщить нам на адрес электронной почты [email protected] или с помощью системы «Орфус», выделив текст с ошибкой и нажав Ctrl+Enter.
|
Провод АС 95/16 — Цены, диаметр, вес и др. характеристики
Кабельная энциклопедия → Провода неизолированные → Провод АС
ГОСТ 839-80
АС 150/24
АС 70/11
Расшифровка
А
С
95
/
16
алюминиевые проволоки
сердечник из стальных проволок
номинальное сечение алюминиевых проволок 95 мм2
номинальное сечение стальных проволок 16 мм2
Конструкция
1. Сердечник из одной стальной проволоки номинальным диаметром 4,5 мм.
2. Токопроводящая часть из одного повива из 6 алюминиевых проволок номинальным диаметром 4,5 мм.
Технические характеристики
Электрическое сопротивление провода | не более 0,3007 Ом/км |
Разрывное усилие провода | не менее 33 369 Н |
Строительная длина | не менее 1 500 м |
Маломеры в партии | не более 5% кусками от 250 м |
Допустимая температура нагрева провода | 90 °C |
Минимальный радиус изгиба | не регламентируется |
Срок службы | не менее 45 лет |
Массо-габаритные характеристики
Расчетная масса (вес) | 385,0 кг/км |
Наружный диаметр | 13,5 мм |
Макс.![]() | 129 м |
Калькулятор массы | км → 0 кг |
Купить из наличия
АС 95/16 | Санкт-Петербург | 15,810 | км |
АС 95/16 | Екатеринбург | 15,796 | км |
АС 95/16 | Самара | 12,984 | км |
АС 95/16 | Новосибирск | 12,977 | км |
АС 95/16 | Пермь | 12,683 | км |
показать ещё 14 ↓ | |||
АС 95/16 | Хабаровск | 8,000 | км |
АС 95/16 | Красноярск | 5,728 | км |
АС 95/16 | Алматы | 3,756 | км |
АС 95/16 | Нижний Новгород | 3,539 | км |
АС 95/16 | Томск | 2,746 | км |
АС 95/16 | Омск | 2,048 | км |
АС 95/16 | Казань | 1,976 | км |
АС 95/16 | Челябинск | 1,500 | км |
АС 95/16 | Москва | 1,023 | км |
АС 95/16 | Павлодар | 0,151 | км |
АС 95/16 | Волгоград | 2,716 | тн |
АС 95/16 | Пермь | 1,594 | тн |
АС 95/16 | Ростов-на-Дону | 0,100 | тн |
АС 95/16 | Псков | 0,078 | тн |
Производители
ТОО «K.![]() |
ООО «Завод Агрокабель», Великий Новгород |
ООО «АлтайКабель», Барнаул |
ООО «Балткабель», Санкт-Петербург |
СЗАО «Белтелекабель», Минск |
показать ещё 14 ↓ |
ТОО «КазЭлектроМаш», Семипалатинск |
АО «Казэнергокабель», Павлодар |
ООО «Камский кабель», Пермь |
АО «Людиновокабель», Людиново |
ООО «Рыбинсккабель», Рыбинск |
АО «Сибкабель», ООО «ХКА», Томск |
ООО «СКТ Групп», Псков |
АО «Тверьэнергокабель», Тверь |
ООО ТД «Ункомтех», Иркутск |
АО «Уралкабель», ООО «ХКА», Екатеринбург |
АО «Электрокабель» Кольчугинский завод», ООО «ХКА», Кольчугино |
ООО «ЭМ-Кабель», Саранск |
ООО «Энергокомплект МФ», Домодедово |
ТОО «Юг-ЭлектроКомплект», Алматы |
Цены из заявок
Уже 30 дней нет предложений на АС 95/16.
Кабельные муфты
Мы не знаем муфты для АС 95/16. Попробуйте подобрать муфту по характеристикам.
Удельное сопротивление нержавеющей стали
AISI 304
Обозначение по международным стандартам
Международный стандарт | Американский ASTM A240 | Европейский ЕN 10088-2 | Российский ГОСТ 5632-72 |
Обозначение марки | AISI 304 | 1.4301 | 08Х18Н10 |
12Х18Н9 |
Применяемые стандарты и одобрения
AMS 5513 ASTM A 240 ASTM A 666
Классификация
сталь коррозионно-стойкая жаропрочная
Применение
- Предметы домашнего обихода
- Раковины
- Каркасы для металлоконструкций в строительной промышленности
- Кухонная утварь и оборудование для общепита
- Молочное оборудование, пивоварение
- Сварные конструкции
- Резервуары судовые и наземные танкеры для продовольствия, напитков и некоторых химических веществ
Обычно производители стали разделяют марку на три основных класса (сорта) по способности к волочению:
- AISI 304 – Основной сорт
- AISI 304 DDQ (Normal and deep drawing) – Сорт глубокой вытяжки
- AISI 304 DDS (Extra deep drawing) – Сорт особо глубокой вытяжки
Основные характеристики
- хорошее общее сопротивление коррозии
- хорошая пластичность
- превосходная свариваемость
Химический состав (% к массе)
стандарт | марка | C | Si | Mn | P | S | Cr | Ni |
ASTM A240 | AISI 304 | ≤0.![]() | ≤0.75 | ≤2.0 | ≤0.045 | ≤0.030 | 18.00 – 20.00 | 8.00 – 10.50 |
Механические свойства
AISI 304 | Сопротивление на разрыв (σв), Н/мм² | Предел текучести(σ0,2), Н/мм² | Предел текучести(σ1,0), Н/мм² | Относительное удлинение (σ), % | Твердость по Бринеллю (HB) | Твердость по Роквеллу (HRB) |
В соответствии с EN 10088-2 | ≥520 | ≥210 | ≥250 | ≥45 | – | – |
В соответствии с ASTM A 240 | ≥515 | ≥205 | – | ≥40 | 202 | 85 |
Механические свойства при высоких температурах
Все эти значения относятся к только AISI 304
.
Физические свойства
Физические свойства | Условные обозначения | Единица измерения | Температура | Значение |
Плотность | d | – | 4°C | 7.![]() |
Температура плавления | °C | 1450 | ||
Удельная теплоемкость | c | J/kg.K | 20°C | 500 |
Тепловое расширение | k | W/m.K | 20°C | 15 |
Средний коэффициент теплового расширения | α | 10 -6 .K -1 | 0-100°C 0-200°C | 17.5 18 |
Электрическое удельное сопротивление | ρ | Ωmm 2 /m | 20°C | 0.80 |
Магнитная проницаемость | μ | в 0.80 kA/m DC или в/ч AC | 20°C μ μ разряж.возд. | 1.02 |
Модуль упругости | E | MPa x 10 3 | 20°C | 200 |
Сопротивление коррозии
304-е стали имеют хорошее сопротивление к общим коррозийным средам, но не рекомендованы там, где есть риск межкристаллитной коррозии. Они хорошо приспособлены для эксплуатации в пресной воде и городской и сельской среде. Во всех случаях необходима регулярная очистка внешних поверхностей для сохранения их первоначального состояния.
304-е стали имеют хорошее сопротивление различным кислотам:
- фосфорной кислоте во всех концентрациях при температуре окружающей среды,
- азотной кислоте до 65 % при температуре 20°C – 50°C,
- муравьиной и молочной кислоте при комнатной температуре,
- уксусной кислоте при температуре 20°C – 50°C.
Их рекомендуют для производства оборудования, контактирующего с холодными или горячими пищевыми продуктами: вино, пиво, молоко (кисломолочные продукты), спирт, натуральные плодовые соки, сиропы, патока, и т.д.
Кислотные среды
Температура, °C | 20 | 80 | ||||||||||
Концентрация, % к массе | 10 | 20 | 40 | 60 | 80 | 100 | 10 | 20 | 40 | 60 | 80 | 100 |
Серная кислота | 2 | 2 | 2 | 2 | 1 | 2 | 2 | 2 | 2 | 2 | 2 | |
Азотная кислота | 2 | 1 | 2 | |||||||||
Фосфорная кислота | 2 | 1 | 2 | |||||||||
Муравьиная кислота | 1 | 2 | 2 | 1 |
Код: 0 = высокая степень защиты – Скорость коррозии менее чем 100мкм/год 1 = частичная защита – Скорость коррозии от 100 до 1000мкм/год 2 = нет защиты – Скорость коррозии более чем 1000мкм/год
Атмосферные воздействия
Сравнение 304-й
марки с другими металлами в различных окружающих средах (Скорость коррозии расчитана при 10-летнем воздействии).
Окружающая среда | Скорость коррозии (мкм/год) | ||
AISI 304 | Алюминий-3S | Углеродистая сталь | |
Сельская | 0.0025 | 0.025 | 5.8 |
Морская | 0.0076 | 0.432 | 34.0 |
Индустриальная Морская | 0.0076 | 0.686 | 46.2 |
Устойчивость к коррозии в кипящих химикалиях
Кипящая среда | Состояние металла | Скорость коррозии (мм/год) |
20%-ая уксусная кислота | Обычный металл Сваренный | * (При толщине образца 0.8 мм и диаметре пресса равном 20 мм) |
AISI 430 | 2.05 мм | |
AISI 304 | 2.0 мм |
*Limiting drawing ratio – предельный коэффициент вытяжки
youtube.com/embed/DNVKOfpMStQ?feature=oembed» frameborder=»0″ allow=»accelerometer; autoplay; encrypted-media; gyroscope; picture-in-picture» allowfullscreen=»»/>
Удельное сопротивление металлов и сплавов (при 20° C)
Вещество | Удельное сопротивление мкОм • мм 2 /м |
Алюминий | 0,028 |
Вольфрам | 0,055 |
Железо | 0,098 |
Золото | 0,023 |
Константан | 0,44−0,52 |
Латунь | 0,025−0,06 |
Манганин | 0,42−0,48 |
Медь | 0,0175 |
Молибден | 0,057 |
Никелин | 0,39−0,45 |
Никель | 0,100 |
Олово | 0,115 |
Ртуть | 0,958 |
Свинец | 0,221 |
Серебро | 0,016 |
Тантал | 0,155 |
Фехраль | 1,1−1,3 |
Хром | 0,027 |
Цинк | 0,059 |
Вещество | К | Вещество | К |
Алюминий | 0,0042 | Олово | 0,0042 |
Вольфрам | 0,0048 | Платина | 0,004 |
Константан | 0,00002 | Ртуть | 0,0009 |
Латунь | 0,001 | Свинец | 0,004 |
Медь | 0,0043 | Серебро | 0,0036 |
Манганин | 0,00003 | Сталь | 0,006 |
Молибден | 0,0033 | Тантал | 0,0031 |
Никель | 0,005 | Хром | 0,006 |
Никелин | 0,0001 | Фехраль | 0,0002 |
Нихром | 0,0001 | Цинк | 0,004 |
Сплавы (состав в %):
- Константан (58,8 Cu, 40 Ni, 1,2 Mn)
- Манганин (85 Cu, 12 Mn, 3 Ni)
- Нейзильбер (65 Cu, 20 Zn, 15 Ni)
- Никелин (54 Cu, 20 Zn, 26 Ni)
- Нихром (67,5 Ni, 15 Cr, 16 Fe, 1,5 Mn)
- Реонат (84Cu, 12Mn, 4 Zn)
- Фехраль (80 Fe, 14 Cr, 6 Al)
Удельное сопротивление нихрома
Каждое тело, через которое пропускается электрический ток, автоматически оказывает ему определенное сопротивление. Свойство проводника противостоять электрическому току принято называть электрическим сопротивлением.
Рассмотрим электронную теорию данного явления. При движении по проводнику свободные электроны постоянно встречают на своем пути другие электроны и атомы. Взаимодействуя с ними, свободный электрон теряет часть своего заряда. Таким образом, электроны сталкиваются с сопротивлением со стороны материала проводника. Каждое тело имеет свою атомную структуру, которая оказывает электрическому току разное сопротивление. Единицей сопротивления принято считать Ом. Обозначается сопротивление материалов — R или r.
Чем меньше сопротивление проводника, тем легче электрическому току пройти через это тело. И наоборот: чем выше сопротивление, тем хуже тело проводит электрический ток.
Сопротивление каждого отдельно взятого проводника зависит от свойств материала, из которого он изготовлен. Для точной характеристики электрического сопротивления того или иного материала было введено понятие — удельное сопротивление (нихрома, алюминия ). Удельным считается сопротивление проводника длиной до 1 м, сечение которого — 1 кв. мм. Этот показатель обозначается буквой p. Каждый материал, использующийся в производстве проводника, обладает своим удельным сопротивлением. Для примера рассмотрим удельное сопротивление нихрома и фехрали (более 3 мм):
- Х15Н60 — 1.13 Ом*мм/м
- Х23Ю5Т — 1.39 Ом*мм/м
- Х20Н80 — 1.12 Ом*мм/м
- ХН70Ю — 1.30 Ом*мм/м
- ХН20ЮС — 1.02 Ом*мм/м
Удельное сопротивление нихрома, фехрали указывает на основную сферу их применения: изготовление аппаратов теплового действия, бытовых приборов и электронагревательных элементов промышленных печей.
Поскольку нихром и фехраль преимущественно используются в производстве нагревательных элементов, то самая распространенная продукция — нихромовая нить, лента, полоса Х15Н60 и Х20Н80, а также фехралевая проволока Х23Ю5Т.
Удельное сопротивление нержавеющей стали
- Свойства
- Таблица технических характеристик
В современном мире нержавейка является незаменимым материалом при производстве разных разновидностей изделий. Она применяется в пищевой, медицинской, металлургической и военной промышленности.
Свойства нержавейки
Сегодня такой материала, как нержавейка является достаточно популярным при производстве многих изделий промышленного и бытового назначения. Нержавеющая сталь представляет собой материал, который производится из стали с добавлением отдельных примесей, которые замедляют или делают процесс образования коррозии на металле невозможным.
Основным достоинством нержавеющей стали является то, что она обладает высоким уровнем устойчивости к появлению ржавчины.
В зависимости от добавленных к стали элементов нержавейка может обладать разными внешними качествами и свойствами. Если каких-либо примесей будет больше или меньше, то процесс коррозии либо будет вообще невозможен, либо он появится спустя длительное время использования предметов, созданных из данного материала.
Нержавеющая сталь применяется для производства промышленного и бытового оборудования, посуды и многих других вещей, которые сталкиваются с влиянием агрессивной среды.
На промышленных предприятиях нержавейку получают путем добавления к стали таких элементов, как:
- медь,
- никель,
- хром,
- марганец.
В зависимости от того, какие виды стали производятся, определяется количество тех или иных элементов в нержавейке. Благодаря данным веществам сталь меняет свои физические и химические свойства, что позволяет использовать этот, материал для изготовления разного рода продукции.
Все добавляемые к стали элементы влияют на ее качества. Для того чтобы получить материал, устойчивый к появлению коррозии и обладающий высоким уровнем прочности, добавляется:
- молибден,
- марганец,
- титан,
- никель.
В стали также не обойтись и без таких элементов, как
- марганец,
- фосфор,
- сера,
- кремний,
которые являются частью железной руды. Они являются верными спутниками этого материала для производства нержавейки. На ее качества они практически не влияют.
Нержавейка сама по себе является уникальным материалом. Она не только обладает рядом преимуществ, но и отличными внешними качествами. Ее сияющая поверхность позволяет использовать этот материал в качестве декоративной отделки зданий и ограждений. Нержавеющая сталь чаще всего становится основной для создания перил для лестниц.
Таблица. Технические характеристики нержавейки
Сталь хромоникелеваяХромистая никелевая молибденоваяЖароупорнаяХромистаяМеханические свойства при 20 градусовМеханические свойства при нагреванииТермическая обработкаДругие свойства
Тип ASTM (AISI) | 304 | 304L | 321 | 316 | 316L | 316 Ti | 310S | 430 | ||
Удельный вес (гр/см) | 7,95 | 7,95 | 7,95 | 7,95 | 7,95 | 7,95 | 7,95 | 7,7 | ||
Структура | Аустенитная | Ферритная | ||||||||
Способность электрического сопротивления при 20 | 0,72 | 0,72 | 0,72 | 0,74 | 0,74 | 0,75 | 0,79 | 0,60 | ||
Твердость по Бринеллю — НВ | отжиг НВ | 130-150 | 125-145 | 130-185 | 130-185 | 120-170 | 130-190 | 145-210 | 135-180 | |
с деформацией в холодном состоянии НВ | 180-330 | 180-230 | ||||||||
Твердость По Роквеллу — HRB / HRC | Отжиг НRВ | 70-88 | 70-85 | 70-88 | 70-85 | 70-85 | 70-85 | 70-85 | 75-88 | |
с деформацией в холодном состоянии HRC | 10-35 | |||||||||
Rm(N/mm2) — Сопротивление рястяжению c деформацией (Предел прочности) | Отжиг | 500-700 | 500-680 | 520-700 | 540-690 | 520-670 | 540-690 | 520-670 | 440-590 | |
в холодном состоянии | 700-1180 | 610-900 | ||||||||
Rp(0,2) (N/mm2) — Предел упругости | Отжиг | 195-340 | 175-300 | 205-340 | 205-410 | 195-370 | 215-380 | 205-370 | 250-400 | |
с деформацией в холодном состоянии | 340-900 | 400-860 | ||||||||
Отжиг Rp(1) (N/mm2) минимальный | 235 | 215 | 245 | 245 | 235 | 255 | 255 | 275 | ||
Удлинение 50мм А(%) | 65-50 50-10 | 65-50 | 60-40 | 60-40 | 60-40 | 60-40 | 60-40 | 30-22 20-2 | ||
Сжатие отжиг Z(%) | 75-60 | 75-60 | 65-50 | 75-60 | 75-65 | 75-60 | 70-55 | 70-60 | ||
Ударная Вязкость | KCUL (Дж/см2) | 160 | 160 | 120 | 160 | 160 | 120 | 160 | 50 | |
KVL (Дж/см2) | 180 | 180 | 130 | 180 | 180 | 130 | 180 | 65 | ||
Упругость при различных температурах | Rp(0,2) (N/mm2) | при 300 С | 125 | 115 | 150 | 140 | 138 | 145 | 165 | 245 |
при 400 С | 97 | 98 | 135 | 125 | 115 | 135 | 156 | 215 | ||
при 500 С | 93 | 88 | 120 | 105 | 95 | 125 | 147 | 155 | ||
Rp(1) (N/mm2) | при 300 С | 147 | 137 | 186 | 166 | 161 | 176 | 181 | ||
при 400 С | 127 | 117 | 161 | 147 | 137 | 166 | 171 | |||
при 500 С | 107 | 108 | 152 | 127 | 117 | 156 | 137 | |||
температура образование окалины | непрерывное обслуживание | 925 | 925 | 900 | 925 | 925 | 925 | 1120 | 840 | |
прерывистое обслуживание | 840 | 840 | 810 | 840 | 840 | 840 | 1030 | 890 | ||
Свариваемость | очень хорошая | очень хорошая | хорошая | очень хорошая | очень хорошая | хорошая | хорошая | достат.![]() | ||
Вытяжка | очень хорошая | очень хорошая | хорошая | хорошая | хорошая | хорошая | хорошая | достаточно хорошая |
Углеродистые стали
Углеродистые стали при комнатной температуре, как уже было сказано, имеют низкое удельное электросопротивление за счет высокого содержания железа. При 20°С значение их удельного сопротивления находится в диапазоне от 13·10-8 (для стали 08КП) до 20·10-8 Ом·м (для У12).
При нагревании до температур более 1000°С способность углеродистых сталей проводить электрический ток сильно снижается. Величина сопротивления возрастает на порядок и может достигать значения 130·10-8 Ом·м.
Удельное электрическое сопротивление углеродистых сталей ρэ·108, Ом·мТемпература, °ССталь 08КПСталь 08Сталь 20Сталь 40Сталь У8Сталь У12
12 | 13,2 | 15,9 | 16 | 17 | 18,4 | |
20 | 13 | 14,2 | 16,9 | 17,1 | 18 | 19,6 |
50 | 14,7 | 15,9 | 18,7 | 18,9 | 19,8 | 21,6 |
100 | 17,8 | 19 | 21,9 | 22,1 | 23,2 | 25,2 |
150 | 21,3 | 22,4 | 25,4 | 25,7 | 26,8 | 29 |
200 | 25,2 | 26,3 | 29,2 | 29,6 | 30,8 | 33,3 |
250 | 29,5 | 30,5 | 33,4 | 33,9 | 35,1 | 37,9 |
300 | 34,1 | 35,2 | 38,1 | 38,7 | 39,8 | 43 |
350 | 39,3 | 40,2 | 43,2 | 43,8 | 45 | 48,3 |
400 | 44,8 | 45,8 | 48,7 | 49,3 | 50,5 | 54 |
450 | 50,9 | 51,8 | 54,6 | 55,3 | 56,5 | 60 |
500 | 57,5 | 58,4 | 60,1 | 61,9 | 62,8 | 66,5 |
550 | 64,8 | 65,7 | 68,2 | 68,9 | 69,9 | 73,4 |
600 | 72,5 | 73,4 | 75,8 | 76,6 | 77,2 | 80,2 |
650 | 80,7 | 81,6 | 83,7 | 84,4 | 85,2 | 87,8 |
700 | 89,8 | 90,5 | 92,5 | 93,2 | 93,5 | 96,4 |
750 | 100,3 | 101,1 | 105 | 107,9 | 110,5 | 113 |
800 | 107,3 | 108,1 | 109,4 | 111,1 | 112,9 | 115 |
850 | 110,4 | 111,1 | 111,8 | 113,1 | 114,8 | 117,6 |
900 | 112,4 | 113 | 113,6 | 114,9 | 116,4 | 119,6 |
950 | 114,2 | 114,8 | 115,2 | 116,6 | 117,8 | 121,2 |
1000 | 116 | 116,5 | 116,7 | 117,9 | 119,1 | 122,6 |
1050 | 117,5 | 117,9 | 118,1 | 119,3 | 120,4 | 123,8 |
1100 | 118,9 | 119,3 | 119,4 | 120,7 | 121,4 | 124,9 |
1150 | 120,3 | 120,7 | 120,7 | 122 | 122,3 | 126 |
1200 | 121,7 | 122 | 121,9 | 123 | 123,1 | 127,1 |
1250 | 123 | 123,3 | 122,9 | 124 | 123,8 | 128,2 |
1300 | 124,1 | 124,4 | 123,9 | — | 124,6 | 128,7 |
1350 | 125,2 | 125,3 | 125,1 | — | 125 | 129,5 |
Низколегированные стали
Низколегированные стали способны чуть более сильно сопротивляться прохождению электричества, чем углеродистые. Их удельное электросопротивление составляет (20…43)·10-8 Ом·м при комнатной температуре.
Следует отметить марки стали этого типа, которые наиболее плохо проводят электрический ток — это 18Х2Н4ВА и 50С2Г. Однако при высоких температурах, способность проводить электрический ток у сталей, приведенных в таблице, практически не различается.
Удельное электрическое сопротивление низколегированных сталей ρэ·108, Ом·мМарка стали2010030050070090011001300
15ХФ | — | 28,1 | 42,1 | 60,6 | 83,3 | — | — | — |
30Х | 21 | 25,9 | 41,7 | 63,6 | 93,4 | 114,5 | 120,5 | 125,1 |
12ХН2 | 33 | 36 | 52 | 67 | — | 112 | — | — |
12ХН3 | 29,6 | — | — | 67 | — | 116 | — | — |
20ХН3 | 24 | 29 | 46 | 66 | — | 123 | — | — |
30ХН3 | 26,8 | 31,7 | 46,9 | 68,1 | 98,1 | 114,8 | 120,1 | 124,6 |
20ХН4Ф | 36 | 41 | 56 | 72 | 102 | 118 | — | — |
18Х2Н4ВА | 41 | 44 | 58 | 73 | 97 | 115 | — | — |
30Г2 | 20,8 | 25,9 | 42,1 | 64,5 | 94,6 | 114,3 | 120,2 | 125 |
12МХ | 24,6 | 27,4 | 40,6 | 59,8 | — | — | — | — |
40Х3М | — | 33,1 | 48,2 | 69,5 | 96,2 | — | — | — |
20Х3ФВМ | — | 39,8 | 54,4 | 74,3 | 98,2 | — | — | — |
50С2Г | 42,9 | 47 | 60,1 | 78,8 | 105,7 | 119,7 | 124,9 | 128,9 |
30Н3 | 27,1 | 32 | 47 | 67,9 | 99,2 | 114,9 | 120,4 | 124,8 |
Высоколегированные стали
Высоколегированные стали имеют удельное электрическое сопротивление в несколько раз выше чем углеродистые и низколегированные. По данным таблицы видно, что при температуре 20°С его величина составляет (30…86)·10-8 Ом·м.
При температуре 1300°С сопротивление высоко- и низко- легированных сталей становится почти одинаковым и не превышает 131·10-8 Ом·м.
Удельное электрическое сопротивление высоколегированных сталей ρэ·108, Ом·мМарка стали2010030050070090011001300
Г13 | 68,3 | 75,6 | 93,1 | 95,2 | 114,7 | 123,8 | 127 | 130,8 |
Г20Х12Ф | 72,3 | 79,2 | 91,2 | 101,5 | 109,2 | — | — | — |
Г21Х15Т | — | 82,4 | 95,6 | 104,5 | 112 | 119,2 | — | — |
Х13Н13К10 | — | 90 | 100,8 | 109,6 | 115,4 | 119,6 | — | — |
Х19Н10К47 | — | 90,5 | 98,6 | 105,2 | 110,8 | — | — | — |
Р18 | 41,9 | 47,2 | 62,7 | 81,5 | 103,7 | 117,3 | 123,6 | 128,1 |
ЭХ12 | 31 | 36 | 53 | 75 | 97 | 119 | — | — |
40Х10С2М (ЭИ107) | 86 | 91 | 101 | 112 | 122 | — | — | — |
Хромистые нержавеющие стали
Хромистые нержавеющие стали имеют высокую концентрацию атомов хрома, что увеличивает их удельное сопротивление — электропроводность такой нержавеющей стали не высока. При обычных температурах ее сопротивление составляет (50…60)·10-8 Ом·м.
Удельное электрическое сопротивление хромистых нержавеющих сталей ρэ·108, Ом·мМарка стали2010030050070090011001300
Х13 | 50,6 | 58,4 | 76,9 | 93,8 | 110,3 | 115 | 119 | 125,3 |
2Х13 | 58,8 | 65,3 | 80 | 95,2 | 110,2 | — | — | — |
3Х13 | 52,2 | 59,5 | 76,9 | 93,5 | 109,9 | 114,6 | 120,9 | 125 |
4Х13 | 59,1 | 64,6 | 78,8 | 94 | 108 | — | — | — |
Хромоникелевые аустенитные стали
Хромоникелевые аустенитные стали также являются нержавеющими, но за счет добавки никеля имеют удельное сопротивление почти в полтора раза выше, чем у хромистых — оно достигает величины (70…90)·10-8 Ом·м.
Удельное электрическое сопротивление хромоникелевых нержавеющих сталей ρэ·108, Ом·мМарка стали201003005007009001100
12Х18Н9 | — | 74,3 | 89,1 | 100,1 | 109,4 | 114 | — |
12Х18Н9Т | 72,3 | 79,2 | 91,2 | 101,5 | 109,2 | — | — |
17Х18Н9 | 72 | 73,5 | 92,5 | 103 | 111,5 | 118,5 | — |
Х18Н11Б | — | 84,6 | 97,6 | 107,8 | 115 | — | — |
Х18Н9В | 71 | 77,6 | 91,6 | 102,6 | 111,1 | 117,1 | 122 |
4Х14НВ2М (ЭИ69) | 81,5 | 87,5 | 100 | 110 | 117,5 | — | — |
1Х14Н14В2М (ЭИ257) | — | 82,4 | 95,6 | 104,5 | 112 | 119,2 | — |
1х14Н18М3Т | — | 89 | 100 | 107,5 | 115 | — | — |
36Х18Н25С2 (ЭЯ3С) | — | 98,5 | 105,5 | 110 | 117,5 | — | — |
Х13Н25М2В2 | — | 103 | 112,1 | 118,1 | 121 | — | — |
Х7Н25 (ЭИ25) | — | — | 109 | 115 | 121 | 127 | — |
Х2Н35 (ЭИ36) | 87,5 | 92,5 | 103 | 110 | 116 | 120,5 | — |
Н28 | 84,2 | 89,1 | 99,6 | 107,7 | 114,2 | 118,4 | 122,5 |
Жаропрочные и жаростойкие стали
По своим электропроводящим свойствам жаропрочные и жаростойкие стали близки к хромоникелевым. Высокое содержание в этих сплавах хрома и никеля не позволяет им проводить электрический ток, подобно обычным углеродистым с высокой концентрацией железа.
Значительное удельное электросопротивление и высокая рабочая температура таких сталей делают возможным их применение в качестве рабочих элементов электрических нагревателей. В частности, сталь 20Х23Н18 по своему сопротивлению и жаростойкости в некоторых случаях способна заменить такой популярный сплав для нагревателей, как нихром Х20Н80.
Удельное электрическое сопротивление жаропрочных и жаростойких сталей ρэ·108, Ом·мТемпература, °С15Х25Т (ЭИ439)15Х28 (ЭИ349)40Х9С2 (ЭСХ8)Х25С3Н (ЭИ261)20Х23Н18 (ЭИ 417)Х20Н35
— | — | — | — | — | 106 | |
20 | — | — | 75 | 80 | — | — |
100 | — | — | — | — | 97 | — |
200 | — | — | — | — | 98 | 113 |
400 | 102 | — | — | — | 105 | 120 |
600 | 113 | — | — | — | 115 | 124 |
800 | — | 122 | — | — | 121 | 128 |
900 | — | — | — | — | 123 | — |
1000 | — | 127 | — | — | — | 132 |
Технические характеристики стали
Прежде чем подробно рассматривать удельное сопротивление стали, следует ознакомиться с ее основными физико-механическими свойствами. Благодаря своим качествам, этот материал получил широкое распространение в производственной сфере и других областях жизни и деятельности людей.
Сталь представляет собой сплав железа и углерода, содержащегося в количестве, не превышающем 1,7%. Кроме углерода, сталь содержит определенное количество примесей – кремния, марганца, серы и фосфора. По своим качествам она значительно лучше чугуна, легко поддается закаливанию, ковке, прокату и другим видам обработки. Все виды сталей отличаются высокой прочностью и пластичностью.
По своему назначению сталь подразделяется на конструкционную, инструментальную, а также с особыми физическими свойствами. В каждой из них содержится различное количество углерода, благодаря которому материал приобретает те или иные специфические качества, например, жаропрочность, жаростойкость, устойчивость к действию ржавчины и коррозии.
Особое место занимают электротехнические стали, выпускаемые в листовом формате и применяющиеся в производстве электротехнических изделий. Для получения этого материала производится легирование кремнием, способным улучшить его магнитные и электрические свойства.
Для того чтобы электротехническая сталь приобрела необходимые характеристики, необходимо соблюдение определенных требований и условий. Материал должен легко намагничиваться и перемагничиваться, то есть, обладать высокой магнитной проницаемостью. Такие стали имеют хорошую магнитную индукцию, а их перемагничивание осуществляется с минимальными потерями.
От соблюдения этих требований зависят габариты и масса магнитных сердечников и обмоток, а также коэффициент полезного действия трансформаторов и величина их рабочей температуры. На выполнение условий оказывают влияние многие факторы, в том числе и удельное сопротивление стали.
Материалы высокой проводимости
К наиболее широкораспрстраненным материалам высокой проводимости следует отнести медь и алюминий (Сверхпроводящие материалы, имеющие типичное сопротивление в 10-20 раз ниже обычных проводящих материалов (металлов) рассматриваются в разделе Сверхпроводимость).
Медь
Преимущества меди, обеспечивающие ей широкое применение в качестве проводникового материала, следующие:
- малое удельное сопротивление;
- достаточно высокая механическая прочность;
- удовлетворительная в большинстве случаев применения стойкость по отношению к коррозии;
- хорошая обрабатываемость: медь прокатывается в листы, ленты и протягивается в проволоку, толщина которой может быть доведена до тысячных долей миллиметра;
- относительная легкость пайки и сварки.
Медь получают чаще всего путем переработки сульфидных руд. После ряда плавок руды и обжигов с интенсивным дутьем медь, предназначенная для электротехнических целей, обязательно проходит процесс электролитической очистки.
В качестве проводникового материала чаще всего используется медь марок М1 и М0. Медь марки М1 содержит 99.9% Cu, а в общем количестве примесей (0.1%) кислорода должно быть не более 0,08%. Присутствие в меди кислорода ухудшает ее механические свойства. Лучшими механическими свойствами обладает медь марки М0, в которой содержится не более 0.05% примесей, в том числе не свыше 0.02% кислорода.
Медь является сравнительно дорогим и дефицитным материалом, поэтому она все шире заменяется другими металлами, особенно алюминием.
В отдельных случаях применяются сплавы меди с оловом, кремнием, фосфором, бериллием, хромом, магнием, кадмием. Такие сплавы, носящие название бронз, при правильно подобранном составе имеют значительно более высокие механические свойства, чем чистая медь.
Алюминий
Алюминий является вторым по значению после меди проводниковым материалом. Это важнейший представитель так называемых легких металлов: плотность литого алюминия около 2.6, а прокатанного — 2.7 Мг/м3. Т.о., алюминий примерно в 3.5 раза легче меди. Температурный коэффициент расширения, удельная теплоемкость и теплота плавления алюминия больше, чем меди. Вследствие высоких значений удельной теплоемкости и теплоты плавления для нагрева алюминия до температуры плавления и перевода в расплавленное состояние требуется большая затрата тепла, чем для нагрева и расплавления такого же количества меди, хотя температура плавления алюминия ниже, чем меди.
Алюминий обладает пониженными по сравнению с медью свойствами — как механическими, так и электрическими. При одинаковом сечении и длине электрическое сопротивление алюминиевого провода в 1.63 раза больше, чем медного. Весьма важно, что алюминий менее дефицитен, чем медь.
Для электротехнических целей используют алюминий, содержащий не более 0.5% примесей, марки А1. Еще более чистый алюминий марки АВ00 (не более 0.03% примесей) применяют для изготовления алюминиевой фольги, электродов и корпусов электролитических конденсаторов. Алюминий наивысшей чистоты АВ0000 имеет содержание примесей не более 0ю004%. Добавки Ni, Si, Zn или Fe при содержании их 0.5% снижают γ отожженного алюминия не более, чем на 2-3%. Более заметное действие оказывают примеси Cu, Ag и Mg, при том же массовом содержании снижающие γ алюминия на 5-10%. Очень сильно снижают электропроводность алюминия Ti и Mn.
Алюминий весьма активно окисляется и покрывается тонкой оксидной пленкой с большим электрическим сопротивлением. Эта пленка предохраняет металл от дальнейшей коррозии.
Алюминиевые сплавы обладают повышенной механической прочностью. Примером такого сплава является альдрей, содержащий 0.3-0.5% Mg, 0.4-0.7% Si и 0.2-0.3% Fe. В альдрее образуется соединение Mg2Si, которое сообщает высокие механические свойства сплаву.
Железо и сталь
Железо (сталь) как наиболее дешевый и доступный металл, обладающий к тому же высокой механической прочностью, представляет большой интерес для использования в качестве проводникового материала. Однако даже чистое железо имеет значительно более высокое сравнительно с медью и алюминием удельное сопротивление; ρ стали, т.е. железа с примесью углерода и других элементов, еще выше. Обычная сталь обладает малой стойкостью коррозии: даже при нормальной температуре, особенно в условиях повышенной влажности, она быстро ржавеет; при повышении температуры скорость коррозии резко возрастает. Поэтому поверхность стальных проводов должна быть защищена слоем более стойкого материала. Обычно для этой цели применяют покрытие цинком.
В ряде случаев для уменьшения расхода цветных металлов применяют так называемый биметалл. Это сталь, покрытая снаружи слоем меди, причем оба металла соединены друг с другом прочно и непрерывно.
Натрий
Весьма перспективным проводниковым материалом является металлический натрий. Натрий может быть получен электролизом расплавленного хлористого натрия NaCl в практически неограниченных количествах. Из сравнения свойств натрия со свойствами других проводниковых металлов видно, что удельное сопротивление натрия примерно в 2.8 раза больше ρ меди и в 1.7 раз больше ρ алюминия, но благодаря чрезвычайно малой плотности натрия (плотность его почти в 9 раз меньше плотности меди), провод из натрия при данной проводимости на единицу длины должен быть значительно легче, чем провод из любого другого металла. Однако натрий чрезвычайно активен химически (он интенсивно окисляется на воздухе, бурно реагирует с водой), почему натриевый провод должен быть защищен герметизирующей оболочкой. Оболочка должна придавать проводу необходимую механическую прочность, так как натрий весьма мягок и имеет малый предел прочности при деформациях.
Литература по удельному сопротивлению проводников
- Кузнецов М. И., «Основы электротехники» – 9-е издание, исправленное – Москва: Высшая школа, 1964 – 560с.
- Бачелис Д. С., Белоруссов Н. И., Саакян А. Е. Электрические кабели, провода и шнуры. Справочник. — М.: Энергия, 1971.
- Гершун А. Л. Кабель // Энциклопедический словарь Брокгауза и Ефрона : в 86 т. (82 т. и 4 доп.). — СПб., 1890—1907.
- Р. Лакерник, Д. Шарле. От меди к стеклу // Наука и жизнь. — 1986. — Вып. 08. — С. 50—54, 2-3 стр. цветной вкладки.
ТОЭЭ ТЭЦ РиЭКТ Метрология Реальная физика Сверхпроводимость Теория проводимости
Знаете ли Вы,
низкочастотные электромагнитные волны частотой менее 100 КГц коренным образом отличаются от более высоких частот падением скорости электромагнитных волн пропорционально корню квадратному их частоты от 300 тыс. км/с при 100 кГц до примерно 7 тыс км/с при 50 Гц.
Mr Toogood Physics — Удельное сопротивление
Что такое удельное сопротивление?
Чем длиннее проводник, тем больше число столкновений между электронами и ионами металла. Как обсуждалось на предыдущей странице, столкновения между этими ионами и электронами вызывают сопротивление проводников, поэтому чем длиннее проводник, тем больше его сопротивление.
Рисунок 1: Сопротивление проводника увеличивается с увеличением его длины.Если длину проводника удвоить, его сопротивление удвоится, поэтому сопротивление прямо пропорционально длине:
$$R\propto l$$
И наоборот, если разность потенциалов приложить к толстому проводу, а затем к тонкому, так как в толстом проводе больше носителей заряда на метр, будет протекать больший ток. Больший ток от того же сопротивления предполагает меньшее сопротивление. Отсюда можно сделать вывод, что чем больше диаметр проводника, тем меньше его сопротивление.
На самом деле сопротивление проводника уменьшится вдвое, если площадь его поперечного сечения удвоится:
$$R\propto\frac{1}{A}$$
Имея два пропорциональных соотношения, мы можем построить уравнение, которое их связывает, введя постоянную, называемую удельным сопротивлением, и оно выглядит следующим образом:
$$\большой R=\frac{ρl}{A}$$
Если мы переформулируем приведенное выше уравнение, чтобы сделать ρ предметом, мы увидим, что единицами удельного сопротивления являются $\units{Ωm}$. 9{2}}} {\ единиц {м}} \\ \\ ρ&=\единицы{Ом\,м} \end{выравнивание}
Удельное сопротивление материала остается постоянным при постоянной температуре и обычно дается при комнатной температуре ($\quantity{2}{° C}$). Ниже приведены удельные сопротивления некоторых распространенных проводников:
Проводник | Удельное сопротивление /$\units{Ом·м}$ |
---|---|
Медь | 1,7×10 -8 (1) |
Золото | 2,4×10 -8 (1) |
Углерод (графит) | 1×10 -5 (1) |
Константин | 4,9×10 -7 (2) |
Алюминий | 2,7×10 -8 (2) |
Серебро | 1,6×10 -8 (1) |
Кремний | 6,4×10 2 (2) |
Чем ниже удельное сопротивление материала, тем лучше он проводит электричество. Инженерам часто приходится принимать решения об использовании материалов в качестве проводников на основе значения их удельного сопротивления, а также других соображений, таких как модуль Юнга и реактивность.
Например, медь имеет более низкое удельное сопротивление, чем алюминий, поэтому она является лучшим проводником, но у нее более высокий модуль Юнга, поэтому она меньше растягивается, чем алюминий. Таким образом, при рассмотрении материалов для линий электропередач большой протяженности, где кабели могут растягиваться и сжиматься из-за колебаний температуры и растягиваться ветром, алюминий является лучшим выбором.
Многие высококачественные аудиоразъемы покрыты золотом, опять же, медь является лучшим проводником, но со временем тускнеет, в то время как золото крайне неактивно, поэтому обеспечивает хороший электрический контакт в течение очень долгого времени. Серебро, несмотря на то, что оно является лучшим проводником, также тускнеет, поэтому не является хорошим выбором для этой функции.
Вы проведете CAP для исследования удельного сопротивления константиновой проволоки.
Вернуться к началу
Кабель, используемый для передачи электроэнергии высокого напряжения, состоит из шести алюминиевых проволок, окружающих стальную проволоку. Поперечное сечение показано ниже.
Рисунок 3: Поперечное сечение кабеля электропередачи.Сопротивление стальной проволоки длиной $\quantity{1,0}{км}$ составляет $\quantity{3,3}{Ом}$. Сопротивление одного из алюминиевых проводов на длине $\quantity{1,0}{км}$ равно $\quantity{1,1}{Ом}$. 9{2}}$$
Хорошей практикой является записывать как можно большую часть дисплея вашего калькулятора для этого промежуточного шага, чтобы избежать ошибок округления в окончательном расчете. Если ваш калькулятор имеет функцию памяти, вы можете сохранить в ней значение и извлечь его при необходимости.
Теперь нужно просто правильно подставить данные в уравнение для удельного сопротивления, как оно дано в вашем листе уравнений:
\начать{выравнивать} ρ&=\frac{RA}{l}\\ \\ & = \ гидроразрыва {\ количество {3,3} {Ω} \ раз \ количество {4,3008403} {м ^ {2}}} {\ количество {1000} {м}} \\ \\ &=\количество{1,4\умножить на 10^{-7}}{Ом·м} \end{выравнивание}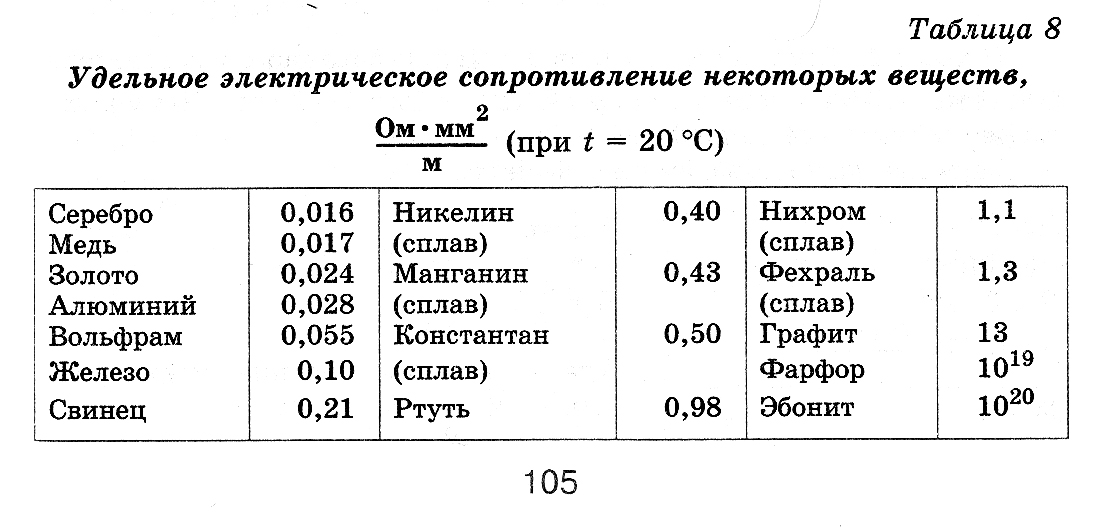
Стальная проволока имеет более высокое удельное сопротивление, поэтому является худшим проводником, чем алюминиевая проволока, фактически сопротивление алюминия составляет одну треть сопротивления стали, поэтому через каждую алюминиевую проволоку будет протекать в три раза больше тока. На каждый стальной провод приходится шесть алюминиевых проводов, поэтому общая площадь алюминиевых проводов в шесть раз больше, чем у стальных, и они фактически ведут себя как параллельные резисторы.
Вернуться к началу
Полупроводники и термисторы
Полупроводники — это материалы, которые не проводят электричество, как обычные проводники, такие как металлы, но будут проводить электричество только при определенных условиях, либо если им передается энергия через тепло или свет, либо если приложено электрическое поле. Полупроводники имеют фундаментальное значение для современной электроники, поскольку транзисторы и диоды, которые используются для создания компьютеров, сделаны из них. Единственные полупроводники, которые вы будете использовать на уровне A, — это термисторы, светозависимые резисторы (LDR), диоды и светодиоды.
Термисторы — это резисторы, удельное сопротивление которых зависит от температуры. Конечно, все резисторы и проводники увеличивают свое удельное сопротивление по мере повышения их температуры, но эффект в термисторах гораздо более драматичен. Термисторы бывают двух видов: с положительным температурным коэффициентом (PTC) и с отрицательным температурным коэффициентом (NTC). Термисторы с положительным температурным коэффициентом увеличивают свое удельное сопротивление при повышении температуры, тогда как термисторы с отрицательным температурным коэффициентом уменьшают свое удельное сопротивление с температурой. Мы будем исследовать термисторы NTC только на уровне A. Обычно термистор NTC изменяет свое сопротивление в диапазоне около $\quantity{200}{Ω}$ в течение $\quantity{100}{°C}$. Это делает их очень полезными в цепях с регулируемой температурой и в качестве датчиков температуры. Различные термисторы имеют разные значения сопротивления и разные рабочие температуры, поэтому инженеры-электронщики могут выбрать наиболее подходящий для своего конкретного применения. Если изменение температуры требуется измерить с высокой степенью точности, термистор, значение которого быстро меняется при интересующей температуре.
Из термисторов получаются очень хорошие термометры, так как они очень чувствительны, они быстро меняются при изменении температуры, однако они не самые надежные, и для проведения измерений им требуются вспомогательные схемы и измерительные приборы.
Термисторы представляют собой собственные полупроводники , что означает, что материалы, из которых они изготовлены, нелегированные , они сделаны из чистых материалов, таких как кремний или германий, или соединений, таких как арсенид галлия, которые могут быть термически возбуждены электронов из валентной зоны , где они присоединены к внешним слоям атомов к проводимости полоса , где они ведут себя как свободные электроны в проводнике. Чем больше энергии передается либо за счет тепла, как для термистора, либо света для LDR, тем больше электронов продвигается из валентной зоны в зону проводимости, тем больше количество доступных носителей заряда и тем ниже сопротивление. Когда электрон пересекает энергетическую щель, он оставляет после себя отверстие . Собственный полупроводник имеет равное количество дырок и электронов проводимости, и хотя дырки — это отсутствие частиц, они ведут себя так, как если бы они были положительно заряженными частицами, и при разработке полупроводников рассматриваются как таковые.
Диоды и светодиоды являются внешними полупроводниками и изготовлены из материалов, легированных . Это означает, что полупроводниковый материал (обычно кремний или германий) имеет смешанные с ним дополнительные материалы, которые либо отдают, либо принимают электроны, обеспечивая либо больше электронов проводимости, либо больше дырок. Полупроводники с дополнительными свободными электронами называются N-типом, а с дополнительными дырками — P-типа. Диод представляет собой простую комбинацию полупроводников N-типа и P-типа, когда к нему приложена разность потенциалов, превышающая минимальное значение (около $\quantity{0,7}{V}$), электроны перемещаются из N полупроводника через обедненную область к полупроводнику P-типа, создающему дырку. Когда это происходит в светодиоде, энергия, выделяемая электроном при рекомбинации с дыркой, больше, чем разница между энергией электрона и энергией дырки, разница высвобождается в виде фотона.
Хотя детали работы полупроводников выходят за рамки изучения уровня A, стоит подумать о том, как их функцию можно объяснить тем, что вы изучали в других модулях.
Вернуться к началу
Сверхпроводники
Сверхпроводники представляют собой особую группу разработанных материалов с нулевым удельным сопротивлением. Это означает, что они проводят без какого-либо электрического сопротивления. Ясно, что это отличная разработка для мощных электрических цепей, однако есть и недостаток. Явление сверхпроводимости возникает только при очень низких температурах. Первым открытым сверхпроводником была ртуть, которая становится сверхпроводником при температуре $\quantity{4,2}{K}$ или около $\quantity{-269.{°C}$. Температура, при которой материал становится сверхпроводником, известна как критическая температура . Мы можем определить сверхпроводник как материал с нулевым сопротивлением ниже (или ниже) его критической температуры .
Большинство материалов становятся сверхпроводниками только при очень низких температурах, и этот эффект разрушается в присутствии сильных магнитных полей, поэтому они могут проводить только небольшие токи. Разрабатывается новое поколение керамических высокотемпературных сверхпроводников, и в настоящее время материалом с самой высокой критической температурой является сероводород (H 2 S), который становится сверхпроводящим при $\quantity{203}{K}$ или $\quantity{-70}{° C}$, хотя он становится сверхпроводящим только при очень высоких давлениях. Эти материалы охлаждаются жидким гелием или жидким азотом, а наиболее пригодные сверхпроводники изготавливаются из керамических материалов, таких как иттрий-барий-оксид меди или YBCO, критическая температура которых составляет $\quantity{92}{K}$ или $\количество{-181}{° C}$.
Сверхпроводники также проявляют некоторые странные эффекты, такие как исключение магнитных полей, что позволяет им левитировать, когда они находятся рядом с сильным магнитом. Это называется эффектом Мейснера, он используется в современных поездах MAGLEV и наглядно демонстрируется на видео ниже. Сверхпроводники имеют много потенциальных применений, некоторые из них уже реализованы. Они особенно полезны в ситуациях, когда требуется передача больших токов, поскольку в них нет потерь энергии или мощности из-за нулевого сопротивления. Они уже используются в сканерах МРТ и ускорителях частиц, где требуются сильные магнитные поля и очень низкое рассеивание энергии. Они были бы полезны при разработке современных микрочипов и суперкомпьютеров, поскольку они обеспечивают более высокие скорости обработки, меньшие размеры конструкции и все это без потерь энергии. Если бы удалось разработать сверхпроводники при комнатной температуре, то их можно было бы использовать для передачи энергии без потери мощности по сети, и их можно было бы использовать для очень эффективных небольших трансформаторов.
Вернуться к началу
Ресурсы
- Презентация — неделя 1
- Домашнее задание
- Рабочий набор CAP
- Пример данных CAP
Предыдущая тема
Следующая тема
Сталь плакированная медью (40%) | Fisk Alloy
Сталь с медным покрытием (CCS) представляет собой композитный проводящий материал, содержащий сердечник из низкоуглеродистой стали, окруженный медью. Медь обеспечивает электропроводность, а сталь придает проводнику прочность. Наиболее распространенный сорт CCS, используемый для электрических проводников, имеет номинальную электропроводность 40% по IACS. CCS подходит для применений, где требуется высокая прочность и средняя проводимость. Сталь, плакированная медью, также подходит для приложений с высокочастотными сигналами, поскольку токи высокой частоты проходят в основном по внешней оболочке проводника.
CCS может поставляться без покрытия или с покрытием из серебра, никеля или олова.
Английские единицы Метрические единицы
Физические свойства
Жестко вытянутый | Мягкий | |
Растяжение | 110 тыс.фунтов/кв.дюйм | 45 тысяч фунтов на квадратный дюйм |
Удлинение | 1% | 10% |
Электропроводность | 39% IACS* при 68°F | 39% IACS* при 68°F |
Удельное электрическое сопротивление | 26,45 мил Ом/фут при 68°F | 26,45 мил Ом/фут при 68°F |
Точка плавления | — | — |
Плотность | 0,294 фунта/дюйм³ | 0,294 фунта/дюйм³ |
Тепловой коэффициент сопротивления | 0,00210 На °F | 0,00210 на °F |
19-рядные концентрические конструкции
Чистый CCS (40%) — Закалка | ||||||
AWG | Константа | Диаметр (дюйм) | Сопротивление (Ом/м²) | Вес (фунт/метр) | Перерыв СТРГ (фунт) | |
Мин.![]() | Максимум | Максимум | Максимум | Мин. | ||
18 | 19/30 | 0,0495 | 0,0505 | 14,5 | 5,47 | 160,9 |
20 | 19/32 | 0,0395 | 0,0405 | 22,7 | 3,51 | 102,4 |
22 | 19/34 | 0,0310 | 0,0320 | 37,0 | 2,20 | 63,1 |
24 | 19/36 | 0,0245 | 0,0255 | 58,8 | 1,39 | 39,4 |
26 | 19/38 | 0,0195 | 0,0205 | 92,9 | 0,899 | 25,0 |
28 | 19/40 | 0,0150 | 0,0160 | 157,1 | 0,548 | 14,8 |
CCS без покрытия (40%) — Soft Temper | ||||||
AWG | Константа | Диаметр (дюйм) | Сопротивление (Ом/м²) | Вес (фунт/метр) | Перерыв StrG (фунт) | |
Мин.![]() | Максимум | Максимум | Максимум | Мин. | ||
18 | 19/30 | 0,0495 | 0,0505 | 14,5 | 5,47 | 65,8 |
20 | 19/32 | 0,0395 | 0,0405 | 22,7 | 3,51 | 41,9 |
22 | 19/34 | 0,0310 | 0,0320 | 37,0 | 2,20 | 25,8 |
24 | 19/36 | 0,0245 | 0,0255 | 58,8 | 1,39 | 16,1 |
26 | 19/38 | 0,0195 | 0,0205 | 92,9 | 0,899 | 10,2 |
28 | 19/40 | 0,0150 | 0,0160 | 157,1 | 0,548 | 6,04 |
7-рядные конструкции
Чистый CCS (40%) — Закалка | ||||||
AWG | Постоянная | Диаметр (дюйм) | Сопротивление (Ом/м²) | Вес (фунт/метр) | Перерыв StrG (фунт) | |
Мин.![]() | Максимум | Максимум | Максимум | Мин. | ||
22 | 30.07 | 0,0297 | 0,0303 | 39,1 | 2.01 | 59,2 |
24 | 7/32 | 0,0237 | 0,0243 | 61,1 | 1,28 | 37,7 |
26 | 7/34 | 0,0186 | 0,0192 | 99,3 | 0,803 | 23,2 |
28 | 7/36 | 0,0147 | 0,0153 | 159.0 | 0,510 | 14,5 |
30 | 7/38 | 0,0117 | 0,0123 | 250,1 | 0,328 | 9,20 |
32 | 7/40 | 0,0090 | 0,0096 | 424.1 | 0,201 | 5,44 |
ГЛУБОКИЙ CCS (40%) — МЯГКИЙ ЗАКАЛ | ||||||
AWG | Константа | Диаметр (дюйм) | Сопротивление (Ом/м²) | Вес (фунт/метр) | Перерыв StrG (фунт) | |
Мин.![]() | Максимум | Максимум | Максимум | Мин. | ||
22 | 30.07 | 0,0297 | 0,0303 | 39,1 | 2.01 | 24,2 |
24 | 7/32 | 0,0237 | 0,0243 | 61,1 | 1,28 | 15,4 |
26 | 7/34 | 0,0186 | 0,0192 | 99,3 | 0,803 | 9,50 |
28 | 7/36 | 0,0147 | 0,0153 | 159,0 | 0,510 | 5,94 |
30 | 7/38 | 0,0117 | 0,0123 | 250,1 | 0,328 | 3,76 |
32 | 7/40 | 0,0090 | 0,0096 | 424.1 | 0,201 | 2,23 |
Односторонние конструкции
CCS с никелированным покрытием (40%) — твердый/мягкий | ||||||||
AWG | СТД Пластина % | Диаметр (дюйм) | Сопротивление (Ом/м²) | Вес (фунт/метр) | Перерыв StrG Жесткий (фунт) | Сломать Силу Мягкий (фунт) | ||
№ | Мин.![]() | Максимум | Максимум | Максимум | Мин. | Мин. | ||
30 | 2 | 0,0101 | 0,0099 | 0,0103 | 281,1 | 0,298 | 8,47 | 3,46 |
31 | 4 | 0,0090 | 0,0088 | 0,0092 | 363,4 | 0,238 | 6,69 | 2,74 |
32 | 4 | 0,0081 | 0,0079 | 0,0083 | 450,9 | 0,194 | 5,39 | 2,21 |
33 | 4 | 0,0071 | 0,0069 | 0,0073 | 574,2 | 0,154 | 4,23 | 1,73 |
34 | 4 | 0,0064 | 0,0062 | 0,0066 | 732,0 | 0,121 | 3,32 | 1,36 |
35 | 4 | 0,0057 | 0,0055 | 0,0059 | 930,2 | 0,0966 | 2,61 | 1,07 |
36 | 4 | 0,0051 | 0,0049 | 0,0053 | 1 172 | 0,0779 | 2,07 | 0,849 |
37 | 7 | 0,0046 | 0,0044 | 0,0048 | 1 501 | 0,0639 | 1,67 | 0,684 |
38 | 7 | 0,0041 | 0,0039 | 0,0043 | 1 911 | 0,0513 | 1,31 | 0,538 |
39 | 7 | 0,0036 | 0,0034 | 0,0038 | 2 514 | 0,0401 | 0,999 | 0,409 |
40 | 7 | 0,0032 | 0,0030 | 0,0034 | 3 230 | 0,0321 | 0,778 | 0,318 |
Посеребренный CCS (40%) | ||||||||
AWG | СТД Пластина % | Диаметр (дюйм) | Сопротивление (Ом/м²) | Вес (фунт/метр) | Перерыв StrG Жесткий (фунт) | Усил.![]() Мягкий (фунт) | ||
№ | Мин. | Максимум | Максимум | Максимум | Мин. | Мин. | ||
30 | 3 | 0,0100 | 0,0099 | 0,0101 | 269,9 | 0,288 | 8,47 | 3,46 |
31 | 3 | 0,0089 | 0,0088 | 0,0090 | 341,6 | 0,229 | 6,69 | 2,74 |
32 | 4 | 0,0080 | 0,0079 | 0,0081 | 423,8 | 0,185 | 5,39 | 2,21 |
33 | 4 | 0,0071 | 0,0070 | 0,0072 | 539,8 | 0,147 | 4,23 | 1,73 |
34 | 4 | 0,0063 | 0,0062 | 0,0064 | 688,1 | 0,116 | 3,32 | 1,36 |
35 | 5 | 0,0056 | 0,0055 | 0,0057 | 874,4 | 0,0921 | 2,61 | 1,07 |
36 | 5 | 0,0050 | 0,0049 | 0,0051 | 1 102 | 0,0739 | 2,07 | 0,849 |
37 | 6.![]() | 0,0045 | 0,0044 | 0,0046 | 1 366 | 0,0602 | 1,67 | 0,684 |
38 | 6.1 | 0,0040 | 0,0039 | 0,0041 | 1 739 | 0,0479 | 1,31 | 0,538 |
39 | 8 | 0,0035 | 0,0034 | 0,0036 | 2 288 | 0,0370 | 0,999 | 0,409 |
40 | 8 | 0,0031 | 0,0030 | 0,0032 | 2 939 | 0,0293 | 0,778 | 0,318 |
Для получения полной версии технических характеристик продукта, включая химический состав в американских и метрических единицах, загрузите PDF-файл.
Артикул № 7#8, Стальная проволока с медным покрытием на American Wire Group
Информация о запросе
ПРИМЕНЕНИЕ
Стальная проволока и прядь, плакированные медью, сочетают электрические характеристики меди с механическими свойствами стали. Часто используемый для систем подземных заземляющих сетей, воздушных заземляющих проводов и несущих проводов, он может противостоять механическим повреждениям во время установки, а также электрическим повреждениям во время неисправности. Сталь с медным покрытием практически не имеет стоимости лома, и ее чрезвычайно трудно разрезать традиционными инструментами для резки проволоки и кабеля, что значительно снижает вероятность кражи.
КОНСТРУКЦИЯ
Мягко отожженные (DSA) стальные плакированные медью (CCS) проводники имеют концентрическую многопроволочную конструкцию. Пряди CCS представляют собой материал с классом проводимости 40%, в котором используется сердечник из низкоуглеродистой стали, обеспечивающий большую гибкость, что упрощает обращение во время установки.
СТАНДАРТЫ
- ASTM B193 — Стандартный метод испытания удельного сопротивления материалов электрических проводников
- ASTM B227 — Стандартные технические условия для жесткотянутой стальной проволоки с медным покрытием
- ASTM B228 — Стандартные технические условия для концентрически-скрученных стальных проводов, плакированных медью
- ASTM B258 — Стандартные технические условия для стандартных номинальных диаметров и площадей поперечного сечения размеров AWG сплошных круглых
- ASTM B910 — Стандартные технические условия для отожженной медной стальной проволоки
ПРИМЕЧАНИЯ
Размеры и вес являются номинальными значениями с учетом стандартных производственных допусков. Номинальная токовая нагрузка и сопротивление постоянному и переменному току стального провода с медным покрытием не эквивалентны таковым у медного проводника.
Для выбора правильного эквивалента см. «Подходящий размер продукта: сравнение диаметров для медного эквивалентного тока плавления для заземления».
Обновлено 06.12.2021
- Технические характеристики
Номинальный Поперечный Секционный Площадь (дюйм²) | Н/Д 0,09078 |
Номинальный Поперечный Сегментный Площадь (мм²) | Н/Д 58,57 |
Номер из Провода | Н/Д 7 |
Диаметр из Проволоки (дюймы) | Н/Д 0,1285 |
Диаметр Габаритные размеры (дюймы) | Н/Д 0,385 |
Масса (фунт/1000 футов) | Н/Д 0,327 |
Минимум Разрушение Прочность (фунты) | Н/Д 3350 |
Максимум Сопротивление Постоянный ток при 20 °C Ом/1000 футов | Н/Д 0,2311 |
Взаимосвязь между электрическим сопротивлением и пределом прочности на растяжение в термообработанных проводниках из алюминиевого сплава
Материалы (Базель). 2021 окт.; 14(19): 5738.
Published online 2021 Oct 1. doi: 10.3390/ma14195738
, 1, * , 2 , 1 , 2 , 2 and 2
Чао Сюй, академический редактор
Информация об авторе Примечания к статье Информация об авторских правах и лицензиях Отказ от ответственности
- Заявление о доступности данных
Термическая обработка всех проводников из алюминиевого сплава (AAAC) является важным этапом, который выполняется для улучшения электрических и механических свойств после процесса вытягивания. В этих сплавах 6ххх механическая прочность и электропроводность обычно являются двумя взаимоисключающими свойствами. В связи с повышенным спросом на высокоэффективные силовые проводники важно понимать и контролировать процессы эволюции микроструктуры (например, восстановление и образование наноразмерных осадков) в этих сплавах для улучшения электрических и механических характеристик. В этом исследовании термообработке подвергались проволочные проводники 6201 AAAC после волочения. Количественно изучались изменения предела прочности при растяжении и удельного электрического сопротивления в зависимости как от температуры обработки, так и от времени выдержки. Были использованы два диаметра проволоки, обычно используемые в производстве силовых кабелей среднего и высокого напряжения: 1,7 мм и 3,5 мм. Из полученных данных следует, что с увеличением времени обработки наблюдались значительные изменения удельного электрического сопротивления и прочности на растяжение. Было обнаружено, что для обоих диаметров проволоки корреляция между прочностью и удельным сопротивлением может быть описана простой экспоненциальной зависимостью. Эта связь может быть полезна для прогнозирования механической прочности путем отслеживания изменений удельного электрического сопротивления во время промышленной термической обработки проводов из AAAC.
Ключевые слова: термическая обработка, дисперсионное твердение, удельное электрическое сопротивление, все проводники из алюминиевых сплавов, сплавы Al–Mg–Si
Помимо широкого применения в автомобильной промышленности, алюминиевые сплавы широко используются в качестве среды для передачи электроэнергии. благодаря их высокой электропроводности, превосходной устойчивости к коррозии и привлекательному соотношению прочности и веса. В связи с растущим спросом на электроэнергию разработка эффективных и долговечных проводников становится важной задачей. Это может быть достигнуто за счет изменения микроструктуры сплава путем термической обработки с целью получения проволоки с высокой электропроводностью и превосходной механической прочностью [1,2,3,4,5]. Высокая электропроводность необходима для снижения потерь мощности при передаче, в то время как для выдерживания эксплуатационных и сезонных механических нагрузок требуется значительная механическая прочность.
Все проводники из алюминиевого сплава (AAAC) изготавливаются методом холодного волочения до желаемого конечного диаметра. В литературе имеется множество исследований, направленных на оптимизацию механических и электрических свойств AAAC [6,7,8,9,10]. Поскольку типичное уменьшение поперечного сечения может превышать 85 %, прочность на разрыв этих металлических сплавов увеличивается за счет деформационного упрочнения. Кроме того, влияние волочения на электропроводность можно объяснить тем фактом, что металлические сплавы чувствительны к деталям микроструктуры, включая плотность дислокаций, границы зерен и присутствие атомов растворенных веществ. Таким образом, после волочения обычно требуется специальный этап термообработки для оптимизации как электрических, так и механических свойств. При этом при разработке сценария термообработки необходимо учитывать несколько параметров (например, исходный состав сплава и уровень холодной обработки) [7,11,12]. Хорошо известно, что при термической обработке и искусственном старении металлических сплавов могут происходить процессы эволюции микроструктуры, включая восстановление, рекристаллизацию, рост зерен и выделение второй фазы. При восстановлении происходит частичная аннигиляция дислокаций, что приводит к некоторому механическому разупрочнению. При рекристаллизации новые бездислокационные зерна образуются и растут на пространстве деформированных зерен, что приводит к повышению пластичности и снижению механической прочности.
Рост зерна обычно следует за рекристаллизацией и приводит к увеличению среднего размера зерна и уменьшению плотности границ зерен.
Термообрабатываемый алюминиевый сплав 6201 в настоящее время широко используется для производства силовых кабелей. В тройном сплаве Al-Mg-Si происходит последовательность событий осаждения, когда атомы Mg и Si диффундируют из насыщенного твердого раствора с образованием несвязных выделений Mg 2 Si [2,13]. Этот процесс влияет на электропроводность, уменьшая вклад растворенных атомов в общее рассеяние электронов [14,15]. Это также влияет на механическую прочность, поскольку наноразмерные выделения могут существенно препятствовать подвижности дислокаций. В алюминиевых сплавах дисперсионное твердение может происходить при комнатной температуре (естественное старение) и ускоряться при относительно повышенной температуре (искусственное старение). В литературе имеются сообщения о влиянии холодного волочения на предел прочности при растяжении и удельное электрическое сопротивление алюминиевых сплавов. Например, Quainoo и Yannacopolos [16] заметили, что объем предварительной холодной обработки AA6111 оказывает сильное влияние на энергию активации образования осадка, что приводит к ускоренной кинетике осаждения. К аналогичному выводу пришли Lan et al. [14] на алюминиевом сплаве 2А14. Кроме того, оказывается, что на кинетику фазового превращения при искусственном старении может влиять предшествующее естественное старение [17,18,19].,20]. В связи с этим Xin et al. В работе [4] изучалось влияние предварительного естественного старения на свойства образцов после искусственного старения. Исследования показали, что предшествующее естественное старение после обработки раствором оказывает разрушительное воздействие на механические свойства. В недавнем исследовании [21] было установлено, что химический состав по количеству Mg и Si играет важную роль в определении механических и электрических свойств катанки 6101. Кроме того, сделан вывод, что наилучшие температура и время искусственного старения составляют 150 °С и 4–10 ч соответственно.
В литературе обычно используются несколько методов характеризации для количественной оценки кинетики образования осадка и его влияния на механические свойства. Исследование образования осадка и эволюции микроструктуры является сложным процессом и обычно требует использования комбинации методов характеризации, включая дифференциальную сканирующую калориметрию (ДСК) [22, 23], атомный зонд [12, 24], спектроскопию времени жизни аннигиляции позитронов [17, 18]. ], дифракция обратного рассеяния электронов [8,25], просвечивающая электронная микроскопия [2,4,5] и измерение удельного электрического сопротивления [26,27,28,29]. Хотя эти методы могут выявить различные аспекты процессов эволюции микроструктуры и деталей выделения, измерение удельного электрического сопротивления имеет много преимуществ по сравнению с этими методами. Во-первых, измерение удельного электрического сопротивления относительно легко выполнить и не требует сложной настройки. Во-вторых, время измерения и пробоподготовки минимальны, что может быть преимуществом с практической точки зрения. Хотя DSC может определить начало и завершение процесса осаждения, объем пробы часто слишком мал. С другой стороны, измерения удельного электрического сопротивления могут предоставить более репрезентативную информацию по относительно большему объему образца, что повышает точность данных [29].,30]. Более того, удельное электрическое сопротивление очень чувствительно к любым изменениям концентрации растворенных атомов, которые могут возникнуть в сплаве в результате реакции осаждения. В случае проводов AAAC удельное электрическое сопротивление является не только «датчиком» кинетики осаждения, но также представляет собой важный параметр, который необходимо минимизировать для высококачественных силовых проводов [15,28].
В промышленных условиях, где термическая обработка силовых проводов часто выполняется внутри очень больших печей, важен точный контроль электрических и механических свойств, особенно когда не всегда поддерживается равномерное распределение температуры в печи. В этом исследовании было изучено влияние параметров отжига с точки зрения температуры и времени выдержки на предел прочности при растяжении и удельное электрическое сопротивление волоченных проводников 6201 Al-Mg-Si. Идея заключалась в том, чтобы изучить связь между двумя свойствами после волочения и термической обработки в моделировании реальной производственной практики. На основании полученных результатов была проанализирована корреляция между удельным электрическим сопротивлением и пределом прочности. Кроме того, взаимосвязь между измеренными параметрами была исследована на двух широко используемых диаметрах проволоки при производстве силовых электрических кабелей (т. е. 1,7 мм и 3,5 мм).
Проволока диаметром 1,7 мм и 3,5 мм была получена методом холодного волочения, при котором стержень диаметром 9,5 мм пропускали через ряд конвергентных фильер. Эти стержни 9,5 выпускались серийно, их химический состав указан в . Средний предел прочности при растяжении этих стержней составил 212 МПа, а их удельное электрическое сопротивление составило 50% по шкале IACS, оба значения были измерены при комнатной температуре. Для диаметра 3,5 мм стержни волочили в семь этапов, в результате чего площадь поперечного сечения уменьшилась на 86,4%. С другой стороны, для диаметра 1,7 мм стержни вытягивались в 14 этапов, что привело к уменьшению площади поперечного сечения на 96,8%. Волоченные проволоки разрезали на образцы длиной 20 см, а затем испытывали их механические и электрические свойства. Это проводили при комнатной температуре (25 °С) и после термообработки (130–250 °С в течение 10–360 мин). Термообработку проводили в печи с регулируемой температурой с замкнутым контуром (Heratherm OGS60, Thermo Fisher Scientific, Уолтем, Массачусетс, США). В цикле термообработки температуру повышали с 25 °C до желаемой температуры в течение заданного времени отжига. В этих экспериментах и для обеспечения точности электрических и механических измерений три образца из разных сечений тянутой проволоки подвергались термообработке при одинаковых условиях. После завершения термической обработки все образцы охлаждались на воздухе вне печи в течение одного часа. Затем была измерена средняя прочность на растяжение этих образцов при комнатной температуре с использованием универсальной машины для испытаний материалов (Testometric FS300CT, Рочдейл, Великобритания), оснащенной датчиком нагрузки 2500 кг (тип DBBMTCL) при скорости деформации 80 мм/мин.
Средняя расчетная длина испытанных образцов составила 60 мм и 80 мм для проволоки диаметром 1,7 и 3,5 мм соответственно.
Таблица 1
Химический состав исследуемых проволок из алюминиевого сплава (в мас. %).
Al | Mg | Si | Fe | Cu | B |
---|---|---|---|---|---|
98.48 | 0.670 | 0.578 | 0.![]() | 0.014 | 0.009 |
Открыть в отдельном окне
Измерения удельного электрического сопротивления выполнены четырехточечным методом с использованием источника постоянного тока Keithly 6221 и нановольтметра Keithly 2182A. Чтобы подавить термоэлектрический шум, два прибора были соединены в дельта-режиме, когда полярность тока чередуется, а нановольтметр измеряет падение потенциала при каждой полярности. Затем из значений тока и напряжения было получено удельное электрическое сопротивление (ρ) с учетом поперечного сечения и длины образца, где:
ρ=VAIL
(1)
здесь V представляет собой измеренное напряжение, A представляет собой площадь поперечного сечения, I передает введенный ток, а L представляет собой длину образца. Во время всех измерений удельного сопротивления ток, проходящий через каждый образец, был установлен равным 5 мА. Данные измерений были получены с помощью кода LabVIEW, который записывает среднее значение 10 измерений в дельта-режиме на образец. Установки для испытаний на растяжение и сопротивление показаны на рис.
Открыть в отдельном окне
( a ) Установка для испытания на растяжение, показывающая зажатую проволоку диаметром 3,5 мм. Тест проводился при комнатной температуре с помощью программного обеспечения для управления скоростью траверсы; ( b ) Внутренняя установка удельного электрического сопротивления с использованием источника тока и нановольтметра, подключенных в дельта-режиме. Тест сопротивления, управляемый LabVIEW, был выполнен с использованием четырехточечного метода.
3.1. Прочность на растяжение
показывает влияние времени отжига на прочность на растяжение для проволоки диаметром 1,7 мм, обработанной при различных температурах. В то время как средняя прочность на растяжение образцов после волочения составляла 327 МПа, термическая обработка может резко снизить это значение. Основными параметрами термической обработки, влияющими на механические свойства металлов и сплавов, являются температура обработки и время выдержки. Здесь не было значительного изменения прочности на растяжение для образцов, обработанных при 130 °C в течение всего шестичасового периода обработки. Однако при температурах выше 130 °C наблюдается значительное падение значений прочности на растяжение. Можно показать, что по мере увеличения времени отжига предел прочности при растяжении обычно снижается. С образцом после вытягивания в качестве эталона было измерено снижение прочности на разрыв примерно на 13% для образцов, состаренных при 150 °C после шести часов обработки. По мере повышения температуры процентное снижение предела прочности при растяжении в конце термической обработки увеличивалось. Окончательная прочность на растяжение около 120 МПа была достигнута для образцов, обработанных при 230 °C и 250 °C, что привело к общему падению примерно на 63%. В то время как постепенное снижение предела прочности образцов, состаренных при 150 °С, 170 °С и 190 °С, зафиксировано резкое падение прочности в течение первых 10 мин термообработки при 230 °С и 250 °С.
После этого быстрого падения образцы, обработанные при 250 °C, не претерпели каких-либо значительных изменений прочности на растяжение примерно через один час в печи.
Открыть в отдельном окне
Изменение предела прочности при растяжении в зависимости от времени отжига для образцов толщиной 1,7 мм при заданной температуре.
показывает данные по прочности на растяжение для проволоки диаметром 3,5 мм, обработанной при различных температурах. Образцы после вытяжки имели среднюю прочность на растяжение примерно такую же, как у образцов толщиной 1,7 мм (333 МПа). Из представленных данных видно, что проволока, обработанная при 130 °C, испытала увеличение прочности на растяжение, достигнув 365 МПа после трех часов пребывания в печи. В течение оставшегося времени лечения дальнейшего увеличения не наблюдалось. С другой стороны, и аналогично поведению, изображенному на , наблюдались заметные изменения в профилях зависимости прочности от времени, когда температура превышала 130 °C. Здесь процентное снижение предела прочности при растяжении в конце обработки увеличивалось с температурой старения (150–250 °C). Замечено, что образцы, обработанные при 150°С и 170°С, достигли пика прочности на разрыв на ранней стадии термической обработки. Этот пик не был обнаружен в других образцах, обработанных при более высоких температурах (190–250 °С). Подобно поведению проволоки диаметром 1,7 мм, быстрое падение предела прочности при растяжении для образцов, обработанных при 230 °С и 250 °С, было обнаружено в течение первых 10 мин термообработки. По сравнению с соответствующими данными, представленными в , имеются некоторые отличия в профилях прочность-время в течение первого часа обработки при температурах выше 190 °С. В то время как проволока диаметром 1,7 мм испытывала при этих температурах резкое и непрерывное падение прочности, прочность образцов диаметром 3,5 мм практически не изменялась в течение 10–30 мин отжига. После этого прочность на растяжение возобновила свое падение со временем.
Относительное изменение предела прочности при растяжении для образцов диаметром 3,5 мм и 1,7 мм после шестичасовой обработки при 250 °С было примерно одинаковым (67 % и 63 % соответственно).
Открыть в отдельном окне
Изменение предела прочности при растяжении в зависимости от времени отжига для образцов диаметром 3,5 мм при заданной температуре.
3.2. Удельное электрическое сопротивление
показывает влияние температуры отжига и времени выдержки на удельное электрическое сопротивление проволоки диаметром 1,7 мм. Среднее удельное сопротивление вытянутых образцов составляло около 35 нОм·м. Образцы, обработанные при температуре 130 °C, испытали снижение удельного электрического сопротивления примерно на 7% в конце обработки по сравнению с образцами после вытягивания. Подобно поведению, наблюдаемому в приведенных выше данных по прочности на разрыв, удельное электрическое сопротивление проволоки, отожженной при 230 °C и 250 °C, резко упало в течение первых 10 мин. Наименьшее конечное значение удельного электрического сопротивления (≈290,5 нОм·м) было достигнуто для образцов, обработанных при 190 °С, 230 °С и 250 °С. Для образцов, отожженных при 150 °C, после постепенного падения удельного сопротивления примерно до 32,7 нОм·м удельное сопротивление увеличилось до 33,5 нОм·м, прежде чем возобновить падение до конечного значения 31,3 нОм·м. Аналогичный рост удельного сопротивления в середине обработки наблюдался и для образцов, обработанных при температуре 170 °С и выше. Однако имело место относительное конечное падение удельного сопротивления в конце обработки, составляющее от 7% до 16%.
Открыть в отдельном окне
Изменение удельного электросопротивления в зависимости от времени отжига образцов толщиной 1,7 мм при заданной температуре.
Влияние температуры отжига и времени выдержки на удельное электрическое сопротивление проволоки диаметром 3,5 мм показано на рис. Среднее электрическое сопротивление вытянутых образцов не сильно отличалось от такового для образцов толщиной 1,7 мм. Для образцов, обработанных при 130 °С, 150 °С и 190 °С, наблюдалось постепенное снижение удельного электрического сопротивления со временем отжига. По мере повышения температуры отжига процент падения удельного электрического сопротивления в конце обработки обычно увеличивался. В то время как конечное удельное сопротивление около 29нОм.м достигается у образцов, отожженных при 170 °С, 190 °С и 210 °С, наибольшее снижение удельного электросопротивления получено у образцов, отожженных при 250 °С (около 22 % по сравнению с необработанными образцами). Подобно данным по удельному электрическому сопротивлению 1,7 мм, представленным в , данные также показали, что провода, отожженные при 210 ° C, 230 ° C и 250 ° C, испытали быстрое падение значений электрического сопротивления в течение первых 10 минут термической обработки.
Открыть в отдельном окне
Изменение удельного электрического сопротивления в зависимости от времени отжига образцов диаметром 3,5 мм при заданной температуре.
На наблюдаемые изменения прочности на растяжение и удельного электрического сопротивления проволоки 6201 AAAC повлияла комбинация двух процессов: дисперсионного твердения и отжига. При дисперсионном твердении сплавов Al–Mg–Si области в пересыщенном твердом растворе α превращаются в кластеры растворенных атомов (сферические по форме и известные как зоны GP), а затем в мелкие игольчатые метастабильные когерентные выделения β″. Реакция полного превращения хорошо описана в литературе [23,31] и может быть представлена следующим образом:
α → Г.П. зоны → β″ → β′ → β
здесь выделения β″ трансформируются в стержнеобразные β′ и, в конечном счете, в равновесную фазу некогерентного β (Mg 2 Si). Некоторые сообщения в литературе указывают на возможность образования равновесной фазы Si в конце последовательности, которая, по-видимому, контролируется соотношением Mg и Si [7,11,12]. Последовательность реакции также зависит от состава сплава и может зависеть от присутствия Cu в количестве, сравнимом с количеством Mg и Si. При этом образуются Cu-содержащие выделения типа реечных Q ′ , который появляется после β″ и сопровождается образованием равновесных фаз Q + Mg 2 Si [31]. Общеизвестно, что укрепление начинается, как только Г.П. зоны формируются в образцах после закалки, обработанных раствором. Однако нанопреципитаты β″ ответственны за достижение максимальной механической прочности (условия пикового старения). Поскольку в данном исследовании термообработка проводилась на образцах после вытяжки без обработки раствором, упрочнения большинства образцов в течение всего времени обработки не наблюдалось. Это означает, что наблюдаемое снижение предела прочности при растяжении при старении было вызвано возможным сочетанием процессов статического восстановления, осаждения β’ и укрупнения β″ в дополнение к любому возможному образованию равновесной фазы. Во время восстановления часть внутренней энергии, запасенной в результате холодной обработки, высвобождается после частичной аннигиляции дислокаций.
Поскольку восстановление представляет собой термически активируемый процесс, обусловленный плотностью дислокаций, температура оказывает значительное влияние на микроструктуру и результирующие механические свойства. Кроме того, температура старения влияет на диффузию атомов растворенного вещества, происходящую при образовании различных осадков. Предполагается, что дислокации, возникшие в результате холодной обработки, могут усиливать истощение растворенных атомов посредством механизма, известного как трубчатая диффузия [24]. Этот механизм влияет на вклад растворенных атомов в общую прочность сплава. С точки зрения электрических свойств и на основе правила Маттиссена полное удельное электрическое сопротивление можно описать совместным влиянием колебаний решетки и несовершенств на рассеяние электронов. Таким образом, удельное электрическое сопротивление (ρ) можно записать как:
ρ=ρT+ρgb+ρd+ρi+ρp
(2)
где ρT, ρgb, ρd, ρi и ρp представляют вклад температуры, границ зерен, дислокаций и вакансий, растворенных атомов и выделений в общее удельное электрическое сопротивление в объемных поликристаллических материалах соответственно. Поскольку дисперсионное твердение включает диффузию атомов растворенных веществ, а восстановление приводит к уменьшению плотности дислокаций, измерение удельного электрического сопротивления может предоставить ценную информацию о кинетике этих процессов эволюции микроструктуры в термообработанных проволоках из AAAC. Хорошо известно, что длина свободного пробега (СПП) электронов при комнатной температуре в алюминии меньше 20 нм [32]. Это означает, что когда расстояние между выделениями становится больше МФП, их влияние на электропроводность становится незначительным. Кроме того, зерна в алюминиевых сплавах обладают термической стабильностью при типичных температурах старения, что снижает влияние границ зерен на рассеяние электронов. Таким образом, любые изменения значений электропроводности в основном связаны с вариациями концентрации растворенных атомов, доступных в матрице. Как поясняется в литературе [24], дислокации, по-видимому, вносят вклад второго порядка в электропроводность в сплавах Al–Mg–Si.
Образцы толщиной 3,5 мм, обработанные при 130 °C, 150 °C и 170 °C, достигли пика прочности на разрыв через 180, 60 и 30 мин соответственно. Это указывает на то, что сырье перед волочением не находилось в условиях пикового старения и в алюминиевой матрице существовало избыточное количество атомов растворенных веществ. Затем увеличение прочности приписывают зарождению и росту β-выделений в дополнение к тем, которые могли образоваться во время естественного старения и обработки перед вытяжкой. По-видимому, дисперсионное твердение оказало здесь большее влияние на прочность, чем любое возможное разупрочнение, возникающее в результате процесса восстановления. Тот факт, что проволока, обработанная при 130 °C, не претерпела изменений в прочности на растяжение после достижения 360 МПа, можно объяснить возможным балансом между зарождением и ростом как β″, так и реечных полусвязных β’-преципитатов. Для образцов, обработанных при 150 °С и 170 °С, падение прочности можно объяснить комбинированным эффектом восстановления, укрупнения выделений β″ и образования β’. Здесь падение предела прочности связано с изменением характера взаимодействия дислокаций и выделений. Эффект последовательности восстановления и осаждения более заметен в образцах, отожженных при 19от 0 °C до 250 °C, на что указывает резкое падение удельного электрического сопротивления в течение первых 10 минут отжига. Здесь величина этого падения увеличивалась с температурой, что привело к прочности на разрыв 180 МПа для проволоки, отожженной при 250 ° C. Между 10 и 30 минутами отжига наблюдалось плато прочности на разрыв, после чего снова падало. Это может быть признаком осаждения β″ при этих температурах, что, по-видимому, уравновешивает эффект восстановления и образования β’. После 30 мин отжига гашение дислокаций через восстановление, по-видимому, происходит параллельно с увеличением объемной доли выделений β’. Эти микроструктурные изменения (снижение упрочнения твердого раствора, образование и трансформация выделений, аннигиляция дислокаций после отжига) могут объяснить значительное падение предела прочности при растяжении после шести часов обработки, достигающее значений ниже 120 МПа для образцов, обработанных при максимальной применяемой температуре.
в этом исследовании (250 ° C). Аналогичное падение механической прочности наблюдалось и для состаренных проволок диаметром 1,7 мм. Хотя проволока диаметром 1,7 мм и 3,5 мм после волочения имела одинаковые значения предела прочности при растяжении, оказалось, что на скорость снижения предела прочности при растяжении влиял процент холодной обработки. Например, падение прочности на растяжение после одного часа старения при 210°С составило около 45% и 31% для образцов толщиной 1,7 мм и 3,5 мм соответственно. Это можно объяснить более высокой плотностью дислокаций, доступной в микроструктуре толщиной 1,7 мм, которая, по-видимому, ускоряет диффузию растворенных атомов по трубе, как объяснялось ранее. Этим также можно объяснить отсутствие участков плато в профилях зависимости прочности от времени для состаренных проволок диаметром 1,7 мм. Здесь, а также поскольку энергия активации выделения меньше при наличии высокой плотности дислокаций, образование β’ ускоряется наряду с более быстрым укрупнением выделений β″ и более высокой скоростью восстановления.
Изменения прочности на растяжение были связаны с изменениями удельного электрического сопротивления, как указано в и . Для проволоки диаметром 3,5 мм начальное падение удельного сопротивления образцов, отожженных при температуре от 130 °C до 170 °C, указывает на то, что атомы растворенного вещества диффундируют из алюминиевой матрицы с образованием β-выделений. В то время как предел прочности при растяжении образца при 130 °C оставался постоянным в течение времени отжига свыше трех часов, удельное сопротивление продолжало снижаться до пяти часов, что подтверждает возможность одновременного образования выделений β″ и β’. Однако образцы, отожженные при 190 °C наблюдалось непрерывное снижение удельного сопротивления в течение всех шести часов. В этом случае большая часть падения происходила в течение первых двух часов лечения. Во всех обработанных образцах падение удельного сопротивления оказалось резким в течение первых 30 мин термической обработки, причем масштаб этого падения увеличивался по мере увеличения температуры отжига со 130 °С до 230 °С. Аналогичное падение удельного сопротивления наблюдалось для проволоки диаметром 1,7 мм, что свидетельствует об аналогичном механизме осаждения. Небольшие изменения тренда удельного сопротивления примерно через час обработки неясны, но они могут быть связаны с локальным перераспределением атомов растворенного вещества во время термической обработки. Обычно требуемая минимальная прочность на растяжение для проволочных жил составляет около 195 МПа при максимальном удельном электрическом сопротивлении около 30,5 нОм·м. Для 1,7 мм наилучший результат был достигнут при температуре и времени обработки 190 °С и трех часах соответственно. С другой стороны, есть больше возможностей для получения нужных характеристик проводов 3,5 мм. Например, время термообработки в течение примерно 300 минут при 150°С было подходящим, в то время как только 10 минут при 210°С оказалось достаточным.
показывает взаимосвязь между удельным электрическим сопротивлением и пределом прочности на растяжение для проводов диаметром 1,7 мм. 64 точки на графике были получены путем объединения данных прочности на растяжение с данными удельного сопротивления, представленными на (всего 64 точки включены, где каждая точка представляет среднее значение измерения трех образцов). Когда предел прочности при растяжении увеличился с примерно 140 МПа до примерно 350 МПа, удельное электрическое сопротивление увеличилось примерно с 29от 0,5 нОм·м до примерно 34 нОм·м. Оказывается, что связь между удельным сопротивлением и пределом прочности при растяжении может быть выражена простой экспоненциальной функцией. Исходя из подгонки измеренных данных, удельное электрическое сопротивление (в нОм·м) может быть выражено математически как:
ρ=aeTSb+c
(3)
где TS — предел прочности при растяжении в МПа, а a, b и c — константы. Для этого случая a = 0,054, b = 72,62 и c = 29,20. показывает тот же анализ для проводов диаметром 3,5 мм. Представляется, что зависимость между прочностью и удельным сопротивлением также следует форме, описываемой уравнением (3). Однако константы в уравнении отличались от констант, полученных при подгонке данных 1,7 мм (a = 0,177, b = 107,11 и c = 27,47). Полученное соотношение может быть полезно при прогнозировании значений удельного электрического сопротивления по данным о прочности на растяжение или наоборот. Это может уменьшить количество образцов, необходимых для рутинной проверки качества в процессе производства. Результаты этого исследования также показывают, что это соотношение справедливо для двух наиболее распространенных диаметров (1,7 мм и 3,5 мм). Таким образом, взаимосвязь может помочь технологам в оценке влияния отжига и старения в сплавах AAAC при уменьшенном количестве испытаний. Возможно, что некоторые условия, такие как химический состав сплава и длительные периоды естественного старения, могут повлиять на подгоночные константы в полученной модели. Необходимо провести подробное исследование для количественной оценки влияния этих параметров и подтверждения полученной взаимосвязи между удельным электрическим сопротивлением и пределом прочности на разрыв образцов термически обработанного алюминиевого сплава.
Открыть в отдельном окне
Зависимость между удельным электрическим сопротивлением и пределом прочности при растяжении проволоки диаметром 1,7 мм.
Открыть в отдельном окне
Зависимость между удельным электрическим сопротивлением и пределом прочности при растяжении проволоки диаметром 3,5 мм.
Проанализировано влияние температуры отжига и времени выдержки на предел прочности при растяжении и удельное электрическое сопротивление проводников из алюминиевого сплава 6201. Исследование было сосредоточено на проволоках диаметром 1,7 мм и 3,5 мм, которые были подвергнуты холодной вытяжке и отжигу без обработки на твердый раствор после процесса волочения. После испытаний более 380 образцов было обнаружено, что как предел прочности при растяжении, так и удельное электрическое сопротивление чувствительны к изменениям параметров процесса старения. Как правило, при температурах выше 150 °C оказывается, что по мере увеличения времени старения как предел прочности при растяжении, так и удельное электрическое сопротивление уменьшаются. Было установлено, что наилучший сценарий обработки проволоки диаметром 1,7 мм – нагрев при 19°С.0°С в течение трех часов. С другой стороны, провода диаметром 3,5 мм могут успешно подвергаться термообработке при различных температурах в диапазоне от 150 °C до 230 °C. По полученным данным был определен характер корреляции между удельным электрическим сопротивлением и пределом прочности проволоки после отжига. Было доказано, что два свойства могут быть связаны с помощью простой экспоненциальной зависимости. Таким образом, удельное электрическое сопротивление можно обоснованно прогнозировать по значениям предела прочности при растяжении независимо от сценария термообработки. Причем такая же тенденция наблюдалась как для проволоки 1,7 мм, так и для проволоки 3,5 мм. Это исследование может быть полезно производителям электрических проводов для прогнозирования прочности на растяжение по удельному электрическому сопротивлению, которое является неразрушающим испытанием и относительно легко выполняется.
Требуется дальнейшая работа, чтобы исследовать достоверность полученной модели для других диаметров проволоки (например, 4,5 мм) и различных химических составов сплавов.
Концептуализация, Н.Д.; методология, NA и QA; программное обеспечение, NA и BA; формальный анализ, Н.А.; расследования, Б.А., С.Б., С.К. и О.А.; ресурсы, S.Q. и О.А.; курирование данных, N.A., B.A. и QA; написание — подготовка первоначального проекта, Н.А. и С.Б.; написание — обзор и редактирование, нет данных; визуализация, контроль качества; авторский надзор, Н.А. Все авторы прочитали и согласились с опубликованной версией рукописи.
Это исследование не получило внешнего финансирования.
Неприменимо.
Неприменимо.
Данные, представленные в этом исследовании, доступны по запросу у соответствующего автора.
Авторы заявляют об отсутствии конфликта интересов.
Примечание издателя: MDPI сохраняет нейтралитет в отношении юрисдикционных претензий в опубликованных картах и институциональной принадлежности.
1. Cui L.-X., Liu Z.-X., Zhao X.-G., Tang J.-G., Liu K., Liu X.-X., Qian C. Осаждение метастабильных фаз и его влияние на удельное электрическое сопротивление Al-0,9Сплав 6Mg2Si в процессе старения. Транс. Цветные металлы. соц. Китай. 2014; 24:2266–2274. doi: 10.1016/S1003-6326(14)63343-4. [CrossRef] [Google Scholar]
2. Hou J.P., Wang Q., Zhang Z.J., Tian Y.Z., Wu X.M., Yang HJ, Li XW, Zhang Z.F. Наноразмерные осадки: ключ к высокой прочности и высокой проводимости проволоки из алюминиевого сплава. Матер. Дес. 2017; 132:148–157. doi: 10.1016/j.matdes.2017.06.062. [CrossRef] [Google Scholar]
3. Jin S., Ngai T., Zhang G., Zhai T., Jia S., Li L. Механизмы усиления осаждения во время естественного старения и последующего искусственного старения в Al-Mg- Si-Cu сплав. Матер. науч. англ. А. 2018; 724: 53–59. doi: 10.1016/j.msea.2018.03.006. [CrossRef] [Google Scholar]
4. He X., Pan Q., Li H., Huang Z., Liu S., Li K., Li X. Влияние искусственного старения, замедленного старения и преждевременного старения по микроструктуре и свойствам алюминиевого сплава 6082. Металлы. 2019;9:173. doi: 10.3390/met73. [CrossRef] [Google Scholar]
5. Ян М., Чен Х., Орехов А., Лу К., Лан С., Ли К., Чжан С., Сонг М., Конг Ю., Шрайверс Д. , и другие. Количественный вклад выделений β″ и β′ в упрочнение состаренного сплава Al–Mg–Si. Матер. науч. англ. А. 2020; 774:138776. doi: 10.1016/j.msea.2019.138776. [CrossRef] [Google Scholar]
6. Ji X., Zhang H., Luo S., Jiang F., Fu D. Микроструктура и свойства контактного провода из сплава Al–Mg–SI методом горизонтального непрерывного литья и непрерывного формования методом экструзии. процесс. Матер. науч. англ. А. 2016; 649: 128–134. doi: 10.1016/j.msea.2015.09.114. [CrossRef] [Google Scholar]
7. Xu X., Yang Z., Ye Y., Wang G., He X. Влияние различных соотношений Mg/Si на микроструктуру и рабочие характеристики кабелей из сплава Al-Mg-Si . Матер. Характер. 2016;119: 114–119. doi: 10.1016/j.matchar.2016.07.011. [CrossRef] [Google Scholar]
8. Zhang J., Ma M., Shen F., Yi D., Wang B. Влияние деформации и отжига на электропроводность, механические свойства и текстуру сплава Al-Mg-Si. кабели. Матер. науч. англ. А. 2018; 710:27–37. doi: 10.1016/j.msea.2017.10.065. [CrossRef] [Google Scholar]
9. Рейнке Г., Каломбо Бадибанга Р., Пестана М.С., де Алмейда Феррейра Дж.Л., Александр Араужо Дж., да Силва С.Р.М. Анализ отказов алюминиевых проводов во всех проводах из алюминиевого сплава -AAAC. англ. Потерпеть неудачу. Анальный. 2020;107:104197. doi: 10.1016/j.engfailanal.2019.104197. [CrossRef] [Google Scholar]
10. Hou J.P., Li R., Wang Q., Yu H.Y., Zhang Z.J., Chen Q.Y., Ma H., Wu X.M., Li XW, Zhang Z.F. Три принципа изготовления алюминиевой проволоки с высокой прочностью и высокой электропроводностью. Дж. Матер. науч. Технол. 2019; 35: 742–751. doi: 10.1016/j.jmst.2018.11.013. [CrossRef] [Google Scholar]
11. Цзян С., Ван Р. Влияние соотношения Mg/Si в зависимости от размера зерна на микроструктуру и механические/электрические свойства сплавов Al-Mg-Si-Sc. Дж. Матер. науч. Технол. 2019;35:1354–1363. doi: 10.1016/j.jmst.2019.03.011. [CrossRef] [Google Scholar]
12. Meyruey G., Massardier V., Lefebvre W., Perez M. Перестаривание сплава Al-Mg-Si с избытком кремния. Матер. науч. англ. А. 2018; 730:92–105. doi: 10.1016/j.msea.2018.05.094. [CrossRef] [Google Scholar]
13. Пакиела З., Людвичовска К., Ференц Дж., Кульчик М. Механические свойства и электропроводность сплавов Al 6101 и 6201, обработанных методом гидроэкструзии. ИОП конф. сер. Матер. науч. англ. 2014;63:012120. дои: 10.1088/1757-899Х/63/1/012120. [CrossRef] [Google Scholar]
14. Lan J., Shen X., Liu J., Hua L. Механизмы упрочнения алюминиевого сплава 2А14 холодной деформацией перед искусственным старением. Матер. науч. англ. А. 2019; 745: 517–535. doi: 10.1016/j.msea.2018.12.051. [CrossRef] [Google Scholar]
15. Цзян Ф., Зуроб Х.С., Пурди Г.Р., Чжан Х. Характеристика выделения осадка в коммерческом сплаве на основе Al–Zn–Mg–Cu в процессе искусственного старения и неизотермической термообработки с помощью полевой контроль удельного электрического сопротивления. Матер. Характер. 2016; 117:47–56. doi: 10.1016/j.matchar.2016.04.014. [Перекрестная ссылка] [Академия Google]
16. Quainoo G.K., Yannacopoulos S. Влияние холодной обработки на кинетику осаждения алюминия AA6111. Дж. Матер. науч. 2004; 39: 6495–6502. doi: 10.1023/B:JMSC.0000044888.01854.e1. [CrossRef] [Google Scholar]
17. Yang Z., Jiang X., Zhang X., Liu M., Liang Z., Leyvraz D., Banhart J. Кластеризация естественного старения при различных условиях закалки в Al-Mg -Si сплав. Скр. Матер. 2021; 190: 179–182. doi: 10.1016/j.scriptamat.2020.08.046. [CrossRef] [Академия Google]
18. Маданат М., Лю М., Банхарт Дж. Реверсия естественного старения в сплавах Al-Mg-Si. Acta Mater. 2018; 159: 163–172. doi: 10.1016/j.actamat.2018.07.066. [CrossRef] [Google Scholar]
19. Liu C.H., Lai Y.X., Chen J.H., Tao G.H., Liu L.M., Ma P.P., Wu C.L. Обращение путей осаждения в сплаве Al–Mg–Si, вызванное естественным старением. Скр. Матер. 2016; 115:150–154. doi: 10.1016/j.scriptamat.2015. 12.027. [CrossRef] [Google Scholar]
20. Engler O., Marioara C.D., Aruga Y., Kozuka M., Myhr O.R. Влияние естественного старения или предварительного старения на эволюцию структуры и прочности выделений при старении сплава Al–Mg–Si АА 6016. Матер. науч. англ. А. 2019 г.;759:520–529. doi: 10.1016/j.msea.2019.05.073. [CrossRef] [Google Scholar]
21. Смырак Б., Юркевич Б., Засадзинская М., Гнелчик М., Яловы П. Влияние термической обработки катанки Al-Mg-Si на ее электропроводность и прочность. Металлы. 2020;10:1027. doi: 10.3390/met10081027. [CrossRef] [Google Scholar]
22. Афшар М., Мао Ф., Цзян Х., Молес В., Шик М., Хак К., Корте-Керзель С., Барралес-Мора Л.А. Моделирование дифференциальной сканирующей калориметрии кривые нагрева для осаждения и растворения в Al-Mg-Si. вычисл. Матер. науч. 2019;158:235–242. doi: 10.1016/j.commatsci.2018.11.023. [CrossRef] [Google Scholar]
23. Fang X., Song M., Li K., Du Y. Последовательность осаждения состаренного сплава Al-Mg-Si. Дж. Мин. Металл. Разд. Б Металл. 2010;46:171–180. doi: 10.2298/JMMB1002171F. [CrossRef] [Google Scholar]
24. Sunde J.K., Marioara C.D., Wenner S., Holmestad R. О микроструктурных причинах улучшения проводимости в результате сильной деформации и старения сплава Al-Mg-Si 6101. Mater. Характер. 2021;176:111073. doi: 10.1016/j.matchar.2021.111073. [Перекрестная ссылка] [Академия Google]
25. He Y., Jia Z., Sanders R.E., Liu Y., Ding L., Xing Y., Liu Q. Количественное исследование растворения Mg2Si во время обработки на твердый раствор в сплаве AA6014. Дж. Эллой. комп. 2017; 703: 272–279. doi: 10.1016/j.jallcom.2017.01.336. [CrossRef] [Google Scholar]
26. Эйвани А.Р., Ахмед Х., Чжоу Дж., Душчик Дж. Корреляция между удельным электрическим сопротивлением, растворением частиц, осаждением дисперсоидов и поведением при рекристаллизации алюминиевого сплава AA7020. Металл. Матер. Транс. А. 2009 г.;40:2435–2446. doi: 10.1007/s11661-009-9917-y. [CrossRef] [Google Scholar]
27. Raeisinia B., Poole W.J., Lloyd D.J. Исследование выделений в алюминиевом сплаве АА6111 с помощью измерений удельного электрического сопротивления. Матер. науч. англ. А. 2006; 420: 245–249. doi: 10.1016/j.msea.2006.01.042. [CrossRef] [Google Scholar]
28. Kao Y.-F., Chen S.-R., Ruan J. Мониторинг удельного электрического сопротивления на месте процесса отжига листа из алюминиевого сплава Al-Mg-Mn. Дж. Эллой. комп. 2018; 740:1046–1050. doi: 10.1016/j.jallcom.2018.01.028. [Перекрестная ссылка] [Академия Google]
29. He H., Zhang L., Li S., Wu X., Zhang H., Li L. Стадии осаждения и кинетика реакции сплавов AlMgSi в процессе искусственного старения, контролируемая методом измерения удельного электрического сопротивления на месте. Металлы. 2018;8:39. doi: 10.3390/met8010039. [CrossRef] [Google Scholar]
30. Esmaeili S., Vaumousse D., Zandbergen M.W., Poole W.J., Cerezo A., Lloyd D.J. Исследование ранней стадии распада в сплаве Al–Mg–Si–Cu АА6111 методами удельного электрического сопротивления и трехмерного атомного зонда. Филос. Маг. 2007;87:3797–3816. doi: 10.1080/14786430701408312. [CrossRef] [Google Scholar]
31. Esmaeili S., Wang X., Lloyd D.J., Poole WJ О дисперсионно-упрочняющем поведении сплава Al-Mg-Si-Cu AA6111. Металл. Матер. Транс. А. 2003; 34: 751–763. doi: 10.1007/s11661-003-0110-4. [CrossRef] [Google Scholar]
32. Галл Д. Длина свободного пробега электрона в элементарных металлах. Дж. Заявл. физ. 2016;119:085101. doi: 10.1063/1.4942216. [CrossRef] [Google Scholar]
Стандартные технические условия для жесткотянутой стальной проволоки с алюминиевым покрытием
Лицензионное соглашение ASTM
ВАЖНО — ВНИМАТЕЛЬНО ПРОЧИТАЙТЕ ЭТИ УСЛОВИЯ ПЕРЕД ВХОДОМ В ЭТОТ ПРОДУКТ ASTM.
Приобретая подписку и нажимая на это соглашение, вы вступаете в
контракт, и подтверждаете, что прочитали настоящее Лицензионное соглашение, что вы понимаете
его и соглашаетесь соблюдать его условия. Если вы не согласны с условиями настоящего Лицензионного соглашения,
немедленно покиньте эту страницу, не входя в продукт ASTM.
1. Право собственности:
Этот продукт защищен авторским правом как
компиляции и в виде отдельных стандартов, статей и/или документов («Документы») ASTM
(«ASTM»), 100 Barr Harbour Drive, West Conshohocken, PA 19428-2959 USA, за исключением случаев, когда
прямо указано в тексте отдельных документов. Все права защищены. Ты
(Лицензиат) не имеет прав собственности или иных прав на Продукт ASTM или Документы.
Это не продажа; все права, право собственности и интерес к продукту или документам ASTM
(как в электронном, так и в печатном виде) принадлежат ASTM. Вы не можете удалять или скрывать
уведомление об авторских правах или другое уведомление, содержащееся в Продукте или Документах ASTM.
2. Определения.
A. Типы лицензиатов:
(i) Индивидуальный пользователь:
один уникальный компьютер с индивидуальным IP-адресом;
(ii) Одноместный:
одно географическое местоположение или несколько
объекты в пределах одного города, входящие в состав единой организационной единицы, управляемой централизованно;
например, разные кампусы одного и того же университета в одном городе управляются централизованно.
(iii) Multi-Site:
организация или компания с
независимое управление несколькими точками в одном городе; или организация или
компания, расположенная более чем в одном городе, штате или стране, с центральным управлением для всех местоположений.
B. Авторизованные пользователи:
любое лицо, подписавшееся
к этому Продукту; если Site License также включает зарегистрированных студентов, преподавателей или сотрудников,
или сотрудник Лицензиата на Одном или Множественном Сайте.
3. Ограниченная лицензия.
ASTM предоставляет Лицензиату ограниченное,
отзывная, неисключительная, непередаваемая лицензия на доступ посредством одного или нескольких
авторизованные IP-адреса и в соответствии с условиями настоящего Соглашения использовать
разрешенных и описанных ниже, каждого Продукта ASTM, на который Лицензиат подписался.
A. Конкретные лицензии:
(i) Индивидуальный пользователь:
(a) право просматривать, искать, извлекать, отображать и просматривать Продукт;
(b) право скачивать, хранить или распечатывать отдельные копии
отдельных Документов или частей таких Документов исключительно для собственного использования Лицензиатом.
То есть Лицензиат может получить доступ к электронному файлу Документа (или его части) и загрузить его. Документа) для временного хранения на одном компьютере в целях просмотра и/или
печать одной копии документа для личного пользования. Ни электронный файл, ни
единственный печатный отпечаток может быть воспроизведен в любом случае. Кроме того, электронный
файл не может распространяться где-либо еще по компьютерным сетям или иным образом. Это
электронный файл нельзя отправить по электронной почте, загрузить на диск, скопировать на другой жесткий диск или
в противном случае разделены. Одна печатная копия может быть распространена среди других только для их
внутреннее использование в вашей организации; его нельзя копировать. Индивидуальный загруженный документ
иным образом не может быть продана или перепродана, сдана в аренду, сдана в аренду, одолжена или сублицензирована.
(ii) Односайтовые и многосайтовые лицензии:
(a) право просматривать, искать, извлекать, отображать и просматривать Продукт;
(b) право скачивать, хранить или распечатывать отдельные копии
отдельных Документов или частей таких Документов для личных целей Авторизованного пользователя. использовать и передавать такие копии другим Авторизованным пользователям Лицензиата в компьютерной сети Лицензиата;
(c) если образовательное учреждение, Лицензиату разрешается предоставлять печатная копия отдельных Документов отдельным учащимся (Авторизованные пользователи) в классе по месту нахождения Лицензиата;
(d) право на отображение, загрузку и распространение печатных копий Документов для обучения Авторизованных пользователей или групп Авторизованных пользователей.
(e) Лицензиат проведет всю необходимую аутентификацию и процессы проверки, чтобы гарантировать, что только авторизованные пользователи могут получить доступ к продукту ASTM.
(f) Лицензиат предоставит ASTM список авторизованных
IP-адреса (числовые IP-адреса домена) и, если многосайтовый, список авторизованных сайтов.
B. Запрещенное использование.
(i) Настоящая Лицензия описывает все разрешенные виды использования. Любой другой использование запрещено, является нарушением настоящего Соглашения и может привести к немедленному прекращению действия настоящей Лицензии.
(ii) Авторизованный пользователь не может производить этот Продукт, или Документы, доступные любому, кроме другого Авторизованного Пользователя, будь то по интернет-ссылке, или разрешив доступ через его или ее терминал или компьютер; или другими подобными или отличными средствами или договоренностями.
(iii) В частности, никто не имеет права передавать, копировать,
или распространять любой Документ любым способом и с любой целью, за исключением случаев, описанных в Разделе
3 настоящей Лицензии без предварительного письменного разрешения ASTM. Особенно,
за исключением случаев, описанных в Разделе 3, никто не может без предварительного письменного разрешения
ASTM: (a) распространять или пересылать копию (электронную или иную) любой статьи, файла,
или материал, полученный из любого продукта или документа ASTM; (b) воспроизводить или фотокопировать любые
стандарт, статья, файл или материал из любого продукта ASTM; в) изменять, видоизменять, приспосабливать,
или переводить любой стандарт, статью, файл или материал, полученный из любого продукта ASTM;
(d) включать любой стандарт, статью, файл или материал, полученный из любого продукта ASTM или
Документировать в других произведениях или иным образом создавать любые производные работы на основе любых материалов.
получено из любого продукта или документа ASTM; (e) взимать плату за копию (электронную или
иным образом) любого стандарта, статьи, файла или материала, полученного из любого продукта ASTM или
Документ, за исключением обычных расходов на печать/копирование, если такое воспроизведение разрешено
по разделу 3; или (f) систематически загружать, архивировать или централизованно хранить существенные
части стандартов, статей, файлов или материалов, полученных из любого продукта ASTM или
Документ.
Включение печатных или электронных копий в пакеты курсов или электронные резервы,
или для использования в дистанционном обучении, не разрешено настоящей Лицензией и запрещено без
Предварительное письменное разрешение ASTM.
(iv) Лицензиат не может использовать Продукт или доступ к Продукт в коммерческих целях, включая, помимо прочего, продажу Документов, материалы, платное использование Продукта или массовое воспроизведение или распространение Документов в любой форме; а также Лицензиат не может взимать с Авторизованных пользователей специальные сборы за использование Продукт сверх разумных расходов на печать или административные расходы.
C. Уведомление об авторских правах . Все копии материала из ASTM
Продукт должен иметь надлежащее уведомление об авторских правах от имени ASTM, как показано на начальной странице. каждого стандарта, статьи, файла или материала. Сокрытие, удаление или изменение
уведомление об авторских правах не допускается.
4. Обнаружение запрещенного использования.
A. Лицензиат несет ответственность за принятие разумных мер для предотвращения запрещенного использования и незамедлительного уведомления ASTM о любых нарушениях авторских прав или запрещенное использование, о котором Лицензиату стало известно. Лицензиат будет сотрудничать с ASTM при расследовании любого такого запрещенного использования и предпримет разумные шаги для обеспечения прекращение такой деятельности и предотвращение ее повторения.
B. Лицензиат должен приложить все разумные усилия для защиты
Продукт от любого использования, не разрешенного настоящим Соглашением, и уведомляет
ASTM о любом использовании, о котором стало известно или о котором было сообщено.
5. Постоянный доступ к продукту.
ASTM резервирует
право прекратить действие настоящей Лицензии после письменного уведомления, если Лицензиат существенно нарушит
условия настоящего Соглашения. Если Лицензиат не оплачивает ASTM какую-либо лицензию или
абонентской платы в установленный срок, ASTM предоставит Лицензиату 30-дневный период в течение
что бы вылечить такое нарушение. Для существенных нарушений период устранения не предоставляется
связанные с нарушениями Раздела 3 или любыми другими нарушениями, которые могут привести к непоправимым последствиям ASTM.
вред. Если подписка Лицензиата на Продукт ASTM прекращается, дальнейший доступ к
онлайн-база данных будет отклонена. Если Лицензиат или Авторизованные пользователи существенно нарушают
настоящую Лицензию или запрещать использование материалов в любом продукте ASTM, ASTM оставляет за собой право
право отказать Лицензиату в любом доступе к Продукту ASTM по собственному усмотрению ASTM.
6. Форматы доставки и услуги.
A. Некоторые продукты ASTM используют стандартный интернет-формат HTML. ASTM оставляет за собой право изменить такой формат с уведомлением Лицензиата за три [3] месяца, хотя ASTM приложит разумные усилия для использования общедоступных форматов. Лицензиат и Авторизованные пользователи несут ответственность за получение за свой счет подходящие подключения к Интернету, веб-браузеры и лицензии на любое необходимое программное обеспечение для просмотра продуктов ASTM.
B. Продукты ASTM также доступны в Adobe Acrobat.
(PDF) Лицензиату и его Авторизованным пользователям, которые несут единоличную ответственность за установку
и настройка соответствующего программного обеспечения Adobe Acrobat Reader.
C. ASTM приложит разумные усилия для обеспечения онлайн-доступа доступны на постоянной основе. Доступность будет зависеть от периодического перерывы и простои для обслуживания сервера, установки или тестирования программного обеспечения, загрузка новых файлов и причины, не зависящие от ASTM. ASTM не гарантирует доступ, и не несет ответственности за ущерб или возврат средств, если Продукт временно недоступен, или если доступ становится медленным или неполным из-за процедур резервного копирования системы, объем трафика, апгрейды, перегрузка запросов к серверам, общие сбои сети или задержки, или любая другая причина, которая может время от времени делать продукт недоступным для Лицензиата или Авторизованных пользователей Лицензиата.
7. Условия и стоимость.
A. Срок действия настоящего Соглашения _____________ («Период подписки»). Доступ к Продукту предоставляется только на Период Подписки. Настоящее Соглашение останется в силе после этого для последовательных Периодов подписки при условии, что ежегодная абонентская плата, как таковая, может меняются время от времени, оплачиваются. Лицензиат и/или ASTM имеют право расторгнуть настоящее Соглашение. в конце Периода подписки путем письменного уведомления, направленного не менее чем за 30 дней.
B. Сборы:
8. Проверка.
ASTM имеет право проверять соответствие
с настоящим Соглашением, за свой счет и в любое время в ходе обычной деятельности
часы. Для этого ASTM привлечет независимого консультанта при соблюдении конфиденциальности. соглашение, для проверки использования Лицензиатом Продукта и/или Документов ASTM. Лицензиат соглашается
разрешить доступ к своей информации и компьютерным системам для этой цели. Проверка
состоится после уведомления не менее чем за 15 дней, в обычные рабочие часы и в
таким образом, чтобы не создавать необоснованного вмешательства в деятельность Лицензиата. Если
проверка выявляет нелицензионное или запрещенное использование продуктов или документов ASTM,
Лицензиат соглашается возместить ASTM расходы, понесенные при проверке и возмещении
ASTM для любого нелицензированного/запрещенного использования. Применяя эту процедуру, ASTM не отказывается от
любое из своих прав на обеспечение соблюдения настоящего Соглашения или на защиту своей интеллектуальной собственности путем
любым другим способом, разрешенным законом.
Лицензиат признает и соглашается с тем, что ASTM может внедрять
определенная идентифицирующая или отслеживающая информация в продуктах ASTM, доступных на Портале.
9. Пароли:
Лицензиат должен немедленно уведомить ASTM
о любом известном или предполагаемом несанкционированном использовании(ях) своего пароля(ей) или о любом известном или предполагаемом
нарушение безопасности, включая утерю, кражу, несанкционированное раскрытие такого пароля
или любой несанкционированный доступ или использование Продукта ASTM. Лицензиат несет исключительную ответственность
для сохранения конфиденциальности своего пароля (паролей) и для обеспечения авторизованного
доступ и использование Продукта ASTM. Личные учетные записи/пароли не могут быть переданы.
10. Отказ от гарантии:
Если не указано иное в настоящем Соглашении,
все явные или подразумеваемые условия, заверения и гарантии, включая любые подразумеваемые
гарантия товарного состояния, пригодности для определенной цели или ненарушения прав
отказываются от ответственности, за исключением случаев, когда такие отказы признаются юридически недействительными.
11. Ограничение ответственности:
В пределах, не запрещенных законом,
ни при каких обстоятельствах ASTM не несет ответственности за любые потери, повреждения, потерю данных или за особые, косвенные,
косвенные или штрафные убытки, независимо от теории ответственности,
возникающие в результате или в связи с использованием продукта ASTM или загрузкой документов ASTM.
Ни при каких обстоятельствах ответственность ASTM не будет превышать сумму, уплаченную Лицензиатом по настоящему Лицензионному соглашению.
12. Общие.
A. Прекращение действия:
Настоящее Соглашение действует до
прекращено. Лицензиат может расторгнуть настоящее Соглашение в любое время, уничтожив все копии
(на бумажном, цифровом или любом носителе) Документов ASTM и прекращении любого доступа к Продукту ASTM.
B. Применимое право, место проведения и юрисдикция:
Это
Соглашение должно толковаться и толковаться в соответствии с законодательством
Содружество Пенсильвании. Лицензиат соглашается подчиняться юрисдикции и месту проведения
в суды штата и федеральные суды Пенсильвании по любому спору, который может возникнуть в соответствии с настоящим
Соглашение. Лицензиат также соглашается отказаться от любых претензий на неприкосновенность, которыми он может обладать.
C. Интеграция:
Настоящее Соглашение представляет собой полное соглашение
между Лицензиатом и ASTM в отношении его предмета. Он заменяет все предыдущие или
одновременные устные или письменные сообщения, предложения, заверения и гарантии
и имеет преимущественную силу над любыми противоречащими или дополнительными условиями любой цитаты, заказа, подтверждения,
или другое сообщение между сторонами, относящееся к его предмету в течение срока действия
настоящего Соглашения. Никакие изменения настоящего Соглашения не будут иметь обязательной силы, если они не будут в письменной форме
и подписан уполномоченным представителем каждой стороны.
D. Уступка:
Лицензиат не может уступать или передавать
свои права по настоящему Соглашению без предварительного письменного разрешения ASTM.
E. Налоги.
Лицензиат должен платить любые применимые налоги,
за исключением налогов на чистый доход ASTM, возникающий в результате использования Лицензиатом Продукта ASTM.
и/или права, предоставленные по настоящему Соглашению.
Металлы | Бесплатный полнотекстовый | Экспериментальное определение пределов сопротивления металлических газов платины и железа с помощью взрывающейся проволоки
1. Введение
Транспортные свойства металлов, удельное электрическое сопротивление и теплопроводность представляют значительный интерес для физики, поскольку они, например, являются важными параметрами для моделирования ядер планет и их структуры. Для удельного сопротивления твердых и жидких фаз металлов имеется набор данных, хорошо обобщенных в [1]. Эти результаты основаны на работах для конкретных металлов, таких как эксперименты Матулы с медью и другими металлами [2]. Имеются также данные о платине и железе, металлах, использованных в этой работе.
Действительно, измерения в различных работах [3,4] дают диапазон объемного удельного сопротивления платины от 10 до 60 × 10–8 Ом·м при повышении ее температуры от стандартных значений до разжижения. Эти измерения являются продолжением измерений, опубликованных Powell et al. [5] в диапазоне от -200 до 100 градусов Цельсия, где они сообщают значения от 10 до 20 × 10-8 Ом·м.
Результаты по удельному сопротивлению твердой и жидкой фаз железа также существуют и опубликованы. В работе Пауэлла [6] приводится значение удельного сопротивления железа в жидкой фазе 125 × 10–8 Ом·м, достигнутое после исходного значения для твердого железа ниже 25 × 10–8 Ом·м, что согласуется с расчетами. и экспериментальные данные, показанные другими группами, как недавно, так и годы назад [7,8].
Плазма различных металлов также изучалась и имеются некоторые работы. Например, обзорная статья Лебедева и соавт. [9] приведены данные по жидким металлам при высоких давлениях, до 4×104 атм. С другой стороны, Milchberg et al. В работе [10] измерено удельное сопротивление алюминия до температуры 106 К без значительных изменений плотности из-за нагрева образца лазерным лучом, препятствующим расширению металла во время измерения. Де Сильва и другие сотрудники [11,12] экспериментально изучили удельное сопротивление плотной медной и алюминиевой плазмы, также оцененное Мики и др. [13] в другом диапазоне параметров с помощью взрывающейся проволочной установки с проволокой, окруженной водяными или стеклянными капиллярами. Позже Шефтман и Красик [14] использовали аналогичную установку для дальнейшего расширения результатов по меди, алюминию и вольфраму. Таким образом, среди методов создания плазмы лазеры могут достигать температуры и давления в больших значениях, вплоть до килоэлектронвольт и мегабаров, соответственно, до которых не может дотянуться взрывающаяся проволока. И наоборот, более низкие значения давления и плотности плазмы можно получить с помощью взрывающихся проволочных установок.
Напротив, насколько известно авторам, нет опубликованных экспериментальных данных по удельному сопротивлению металлических газов, таких как железо и платина. В этой работе, следуя методу, разработанному авторами для взрываемой проволочной установки [15] и ранее использовавшемуся для измерения пределов удельного сопротивления газообразной металлической меди [16], представлены дальнейшие измерения пределов удельного сопротивления для газов железа и платины.
В экспериментальных условиях, описанных в [15,16], образуется нейтральный классический газ с плотностью энергии несколько сотен кДж на моль и давлением ниже 100 атм, который расширяется относительно окружающего воздуха. При этом условии газовая фаза растет за счет саморазогревающегося твердожидкого ядра, процесс хорошо описан в предыдущих работах [17,18]. Подобно другим газам, удельное электрическое сопротивление металлических газов больше, чем в их твердой фазе.
Нелегко настроить эксперимент со взрывающейся проволокой, чтобы получить вышеупомянутую эволюцию. Во-первых, должен быть баланс между временем испарения проволоки и временем нарастания тока, чтобы избежать дуги и коротких замыканий, которые могут быть вызваны достаточно быстрыми разрядами. Следовательно, подача электроэнергии и время, в течение которого эта энергия доставляется, являются одними из основных параметров для контроля этого баланса. В этих экспериментах максимальная обеспечиваемая энергия составляла порядка 100 Дж, а время подачи энергии составляло порядка 2 мкс.
Во-вторых, геометрия и масса проволоки являются важными факторами, так как если бы проволока была слишком короткой, газовая фаза была бы настолько короткой, что ее было бы нелегко измерить (по крайней мере, с доступной диагностикой). С другой стороны, если проволока имеет слишком большой диаметр, то джоулев электрический ток, нагревающий твердую и жидкую фазы, не будет радиально однородным.
Наконец, в соответствии с предыдущими рассуждениями, время подачи электрического тока не может быть слишком быстрым, опять же, чтобы получить металлический газ в масштабе времени, достаточном для их измерения. Таким образом, типичные значения электрического тока для взрывных проволочных установок составляют от 50 до 100 А/нс и выше [19].], слишком быстры для представленных здесь экспериментов и требуют гораздо более медленного тока, максимум ≈10 А/нс. В результате непросто добиться электрического разряда на проволоке, чтобы иметь относительно длительный газовый переход (темновую паузу). Тогда для каждого материала существует лишь узкий диапазон параметров, при которых это может быть достигнуто.
Как более ясно объяснено в нашей предыдущей работе [15], газовая фаза металла не является полностью гомогенной по разным причинам. Одним из важнейших источников неоднородностей в расширяющейся фазе является то, что распределение тока не является радиально однородным, а динамически изменяющимся. С другой стороны, центральная часть расширяющейся проволоки могла находиться в совершенно иной фазе, являясь горячей жидкостью, превращающейся в расширяющийся газ, по крайней мере, в первые моменты расширения газа. Кроме того, стоит еще раз упомянуть, что пределы удельного сопротивления, представленные в этой работе, основаны на измерениях внешнего слоя расширяющегося газа, поэтому внутренний состав этой фазы или ее различные плотности не влияют на представленные здесь измерения.
Кроме того, хотя это и менее вероятно, возможно, что часть газа вступает в реакцию с кислородом воздуха с образованием оксидов металлов. Чтобы устранить этот последний эффект, следует проводить опыты в инертной атмосфере, например, с аргоном. Подобные эксперименты в настоящее время выходят за рамки данной работы. В наших экспериментах мы используем три напряжения для зарядки конденсаторной батареи, описанной в предыдущем разделе, поэтому процентное содержание окисленного металлического газа должно зависеть от напряжения из-за его зависимости от общей энергии, передаваемой металлическому газу. Наши эксперименты показывают небольшой эффект или его отсутствие в полученных значениях; в противном случае дисперсия ошибки была бы пропорциональна зарядному напряжению, чего в наших экспериментах не наблюдается.
2. Экспериментальная установка
Эксперименты, описанные здесь, были проведены в системе взрывающихся проводов ALEX (ALambre EXplosivo, по-испански «взрывная проволока»), расположенной в INEI, Университет Кастилия-Ла-Манча, Испания, в соответствии с предыдущими работами, которые уже комментировались в введение. Использовались металлические проволоки из железа и платины фиксированного диаметра и длины 125 мкм и 56,9 ± 0,1 мм соответственно. Для измерения пределов удельного сопротивления в различных экспериментальных ситуациях напряжение в конденсаторной батарее изменялось между 10, 15 и 20 кВ.
Для получения интенсивных токов, необходимых в экспериментах, ALEX использует конденсаторную батарею с двумя параллельно подключенными конденсаторами емкостью 1,1 мкФ каждый и максимальным напряжением порядка 60 кВ. Конденсаторная батарея, соединенная последовательно с источником высокого напряжения через синхронизированный блок искрового разрядника, разряжает электрический ток через металлическую проволоку. Этот разряд синхронизирован с блоком стрик-камеры, как показано на рис. 1.
Делители напряжения («зонд 3» и «зонд 4») и пояс Роговского, как указано на рисунке, регистрируют напряжение и ток во времени в осциллографы, помещенные в комнату с клеткой Фарадея вдали от эксперимента. Это и другое электронное управляющее оборудование размещено внутри этой клетки Фарадея, чтобы предотвратить проблемы, связанные с шумом электромагнитных волн, возникающим при взрыве провода на открытом воздухе.
Данные этих зондов калибруются для получения фактических измерений напряжения и тока, протекающих по проводу, и позже используются для расчета пределов удельного сопротивления металла провода, как описано в следующем разделе этой работы. Измерения тока, использованные в данной работе, представляют собой аналоговое интегрирование с помощью пассивной RC-цепи сигнала пояса Роговского до его регистрации на осциллографе. Следовательно, токовые сигналы не нуждаются в какой-либо численной обработке, кроме умножения на калибровочный коэффициент.
Следует отметить, что для получения пределов удельного сопротивления измерения тока должны быть очень точными на стадии темновой паузы. Таким образом, выбранный датчик тока должен работать либо в больших масштабах, от ампер до килоампер в наших экспериментах, либо отбрасывать самые большие значения тока, появляющиеся из темновой паузы; этот последний подход использовался в этой работе, как показано на рисунке 2. С другой стороны, поскольку пояс Роговского обеспечивает производную тока, обычной экспериментальной практикой является численное интегрирование результата для получения тока, который обычно должен быть корректируется из-за постоянного смещения в текущем сигнале. Такой подход не может работать в этих экспериментах, потому что текущее смещение сигнала не является постоянным и имеет случайные изменения. Поэтому использовалось аналоговое интегрирование текущего сигнала пассивной RL-схемой перед входом прицела.
Для расчета пределов удельного сопротивления металлических газов также необходимо измерить (с большой точностью) динамическое поведение радиального расширения газа. В данной работе такая задача выполняется с ретро-освещенными штриховыми изображениями. Непрерывный лазерный луч с длиной волны 532 нм, изображенный на рисунке 1, использовался в качестве источника света, создавая штриховые изображения, подобные показанному на рисунке 3. Как видно из этой фотографии, благодаря одновременной регистрации расширения диаметра, вертикальный размер , и время, в которое появляется такой размер диаметра, горизонтальный размер, радиальное расширение газовой фазы металлов можно рассматривать как функцию времени, тем самым синхронизируя его с электрической энергией, пропорциональной проволоке и другими величинами. Как видно на упомянутом штриховом изображении, ударная волна в воздухе создается расширением газа и отделяется от металлического газа в более поздние моменты времени, зафиксированные камерой. Учитываемые значения радиального расширения металлического газа брались только из внутренней более темной части изображения, соответствующей металлическому газу.
Поскольку штриховые изображения фиксируют поведение расширения металлического газа во времени, на изображениях возникают различия из-за зарядного напряжения в батарее конденсаторов. Наиболее заметной особенностью является то, что время газовой фазы сокращается по мере увеличения зарядного напряжения, что приводит к различным временным шкалам, показанным на рисунке 4 для платиновых проводов.
Сигналы датчиков напряжения, пояса Роговского и их аналогового интегрирования записываются с той же временной базой, что и осциллографы, поэтому для их синхронизации с штриховыми изображениями используется сигнал фотодиода Ph2.
3. Модель пределов удельного сопротивления и результаты
Хотя детали модели и гипотезы, которые приводят к пределам удельного сопротивления, были ранее опубликованы авторами [15], полезно включить краткий обзор модели.
Обычные системы взрывающихся проводов могут быть классифицированы, среди прочих параметров, по мощности, которая может быть отдана, полностью зависящей от батареи конденсаторов и внешней цепи. Вообще говоря, они делятся на медленные и быстрые системы; медленный при производной тока менее 50 А/нс и быстрый при токе выше 100 А/нс соответственно [20]. Когда электрический разряд в цепи даже медленнее, чем ранее упомянутый предел, тогда фазовое преобразование металлической проволоки из твердого состояния в плазменное можно настроить так, чтобы оно выдерживалось в течение микросекунд. В этих экспериментальных условиях промежуточное газовое состояние металла длится достаточно долго, чтобы его можно было изучить.
Когда большая часть материала провода находится в газообразном состоянии и из-за большего удельного сопротивления этой фазы, ток, проходящий через провод, прекращается и достигает минимума: ситуация, часто описываемая в литературе как темная пауза [21,22] . Как упоминалось ранее, этот этап является объектом данной работы.
Общие условия Получение большой темновой паузы, достаточной для проведения измерений предельных значений удельного сопротивления металла, – непростая задача. Производная тока накладывает сильные ограничения: она не может быть настолько медленной, чтобы избежать фазовых превращений металла, и одновременно не может быть настолько высокой, чтобы паровая фаза была слишком короткой, что затрудняло измерения. Поэтому в этих экспериментах использовалось максимальное значение ≈10 А/нс.
С другой стороны, геометрия проволоки также должна быть тщательно настроена, так как она связана с массой проволоки через объем проволоки, который должен в большом процентном соотношении преобразовываться в пар, чтобы уменьшить разницу между верхним и более низкие пределы удельного сопротивления, как объяснено последним в этом разделе. Поэтому в первом приближении размеры проволоки должны быть больше, чем обычно во взрывающихся проволочных системах для проведения этих экспериментов; например, длина порядка 10 сантиметров. Кроме того, диаметр не может быть очень тонким, ≈ 10 мкм, так как тогда темновая пауза будет слишком короткой, или слишком толстой, ≈ 250 мкм, чтобы минимизировать неоднородности расширения проволоки после начала ее превращения в металлическую газовую фазу. Из практических соображений диаметры менее 100 мкм в данном эксперименте не используются, а длина проволоки зафиксирована на указанном выше значении (56,9± 0,1 мм).
Следуя нашим предыдущим работам, нижнюю границу удельного сопротивления металлического газа можно записать в виде [16]:
где Vres — резистивное напряжение на проводе, rb2 — радиус расширения, измеряемый полосой, а I — электрический ток, протекающий по системе проводов. Чтобы прийти к этому уравнению, необходимо рассматривать расширение проволоки как неоднородное, при этом газ, образующийся из внутреннего жидкого ядра, уносится электрическим током. Тогда общее удельное сопротивление цепи можно рассматривать как параллель двух очень разных состояний одного и того же металла: внешнего газа и внутреннего жидкого ядра или эквивалентной фазы. Следовательно, (1) дает нижний предел удельного сопротивления металлического газа.
Чтобы получить верхний предел удельного сопротивления на основе измерений радиального расширения и сопротивления, необходимо использовать термодинамику системы. Как объяснялось в ранее цитируемой статье, полная внутренняя энергия, сообщаемая материалу, не может быть больше, чем поглощаемая им электрическая энергия, и, принимая во внимание, что газ испытывает расширение при постоянном атмосферном давлении, верхний предел удельного сопротивления можно записать как:
где tкип — момент начала кипения проволоки, n — число молей в газовом состоянии, l — длина системы (постоянная и равная начальной длине проволоки, так как расширение проволоки можно считать цилиндрическим), Cp молярная теплоемкость при постоянном давлении, Tкип — температура кипения металла, а Qvap — скрытая теплота парообразования. Учитывая, что как температура, так и количество молей газа монотонно увеличиваются со временем во время темной паузы, первый подход к оценке верхнего предела удельного сопротивления, определяемого формулой (2), заключается в допущении линейной зависимости со временем. Согласно численному моделированию [16], это приближение выполняется с точностью до 20 %.
Результат измерения пределов удельного сопротивления железа и платины представлен на рис. 5 и рис. 6. Максимальное значение удельного сопротивления, которое было измерено для железа, достигает 0,03 Ом·м, в то время как в случае платины максимальные достигнутые значения примерно в двадцать раз меньше этого (порядка 1,4 × 10–3 Ом·м). На обоих рисунках можно увидеть, что полученное удельное газовое сопротивление обоих металлов намного больше, на несколько порядков, чем их твердые и жидкие аналоги. Такую разницу следовало ожидать, так как газ является гораздо лучшим изолятором, чем твердая или жидкая фаза проводника. Твердое железо имеет удельное сопротивление порядка 10-7 Ом·м по сравнению с максимальным значением ≈0,03 Ом·м, зарегистрированным для газа. Аналогичная тенденция наблюдается и с платиной; его удельное сопротивление в твердом состоянии того же порядка, что и у железа, но его удельное сопротивление в газе достигает максимума ≈1,4×10–3 Ом·м. Поэтому даже для наиболее благоприятного случая платины удельное сопротивление газа на три порядка больше, чем в твердом состоянии.
В конце темной паузы большую часть ее энергии можно считать внутренней энергией, так как расширение происходит намного медленнее (или даже остановилось) по сравнению с началом. Это приводит к тому, что верхний предел приближается к фактическому значению удельного сопротивления. В то же время, учитывая, что в это время жидкая фаза значительно уменьшилась (или исчезла), это также приводит к приближению нижнего предела к реальному значению удельного сопротивления. Это видно на графиках, где различия между кривыми верхнего и нижнего пределов уменьшаются со временем. Приведенные графики также показывают, что приведенные выше гипотезы о линейных зависимостях от времени вполне обоснованы, так как, например, завышение количества молей в газообразном состоянии может сделать верхний предел ниже нижнего, а занижение может привести к очень высокому верхнему пределу.
Стоит обсудить энергетические шкалы полученного удельного сопротивления, так как они дают полезную информацию о достигнутой конечной стадии паров металла. Энтальпия плавления и испарения железа составляет 343 кДж/моль, что близко к конечному значению измеренной энергии, поглощенной проволокой в наших опытах. Таким образом, измеренные значения удельного сопротивления, представленные здесь, являются репрезентативными для всей газовой фазы материала. Это не относится к платине, так как ее энтальпии плавления и испарения достигают значения ≈532 кДж/моль. Измерения удельного сопротивления, представленные в данной работе, останавливаются на уровне ≈330 кДж/моль, поэтому эти значения не включают весь диапазон энергий, которых может достичь платина [23].
4. Выводы
С помощью ранее разработанного авторами метода измерения пределов удельного электрического сопротивления газообразных металлов [15] были исследованы металлические газы железа и платины.
Измеренное удельное сопротивление металлических газов железа и платины показывает разницу в четыре порядка с жидкой и твердой фазами. Газообразные медь и железо достигают максимального удельного сопротивления того же порядка (10-2 Ом·м), а газообразная платина имеет на порядок меньшее сопротивление при аналогичном уровне энергии.
Газы не обладают коллективным эффектом, как конденсированные состояния, поэтому удельное сопротивление будет зависеть от размера и электронной структуры атомов и, конечно же, от ионизирующих агентов, которые могут присутствовать в эксперименте и, следовательно, от геометрии и могут быть важны материалы электродов, и в дальнейшем мы планируем изучить этот тип зависимости.
Измерение других термодинамических переменных, таких как давление, помимо других свойств этих металлических газов, имеет свои преимущества. Например, что касается свойств металлического газа, связанных с его взаимодействием с электромагнитными полями, его диэлектрическая проницаемость и оптическая непрозрачность могут быть измерены с помощью полосовых изображений, аналогичных представленным здесь. Для того, чтобы составить более определенное представление об атомарных свойствах металлических газов, эти две представленные здесь величины и измерения удельного сопротивления необходимы, и мы планируем изучить их в дальнейших экспериментах.
Вклад авторов
Концептуализация, Л.Б. и ВРП; Формальный анализ, Л.Б. и ВРП; Расследование, Л.Б. и ВРП; Написание — первоначальный вариант, Л.Б. и ВРП; Написание — обзор и редактирование, L.B. и G.R.P. Все авторы прочитали и согласились с опубликованной версией рукописи.
Финансирование
Это исследование финансировалось проектами «MATERIA CON ALTA DENSIDAD DE ENERGIA EN FUSION POR CONFINAMIENTO INERCIAL», номер ссылки ENE2016-75703-R Министерства науки, инноваций и университетов Испании и «HIDRODINAMICA DE LA MATERIA». CON ALTA DENSIDAD DE ENERGIA», регистрационный номер SBPLY/17/180501/000264 от Хунты общин Кастилии-ла-Манча.
Благодарности
Авторы благодарят Roberto Piriz за комментарии и предложения по этой работе.
Конфликт интересов
Авторы заявляют об отсутствии конфликта интересов. Спонсоры не участвовали в разработке исследования; при сборе, анализе или интерпретации данных; в написании рукописи или в решении опубликовать результаты.
Ссылки
- Dyos, G.T. Справочник по удельному электрическому сопротивлению. Новые материалы и эффекты давления; Том 13 из серии «Материалы и устройства»; Инженерно-технологический институт: Лондон, Великобритания, 2012 г. [Google Scholar]
- Матула Р.А. Удельное электрическое сопротивление меди, золота, палладия и серебра. Дж. Физ. хим. Ссылка Данные 1979 , 8, 1147–1298. [Google Scholar] [CrossRef][Зеленая версия]
- Уилтан, Б.; Кагран, К.; Бруннер, К.; Pottlacher, G. Теплофизические свойства твердой и жидкой платины. Термохим. Acta 2004 , 415, 47–54. [Google Scholar] [CrossRef]
- Абадлия, Л.; Гассер, Ф.; Халук, К .; Маюфи, М .; Гассер, Дж.Г. Новая экспериментальная методология, установка и программа лабораторного просмотра для точных измерений абсолютной термоэлектрической мощности и удельного электрического сопротивления в диапазоне от 25 до 1600 К: Применение к чистой меди, платине, вольфраму и никелю при очень высоких температурах.
преподобный наук. Инструм. 2014 , 85, 095121. [Google Scholar] [CrossRef]
- Powell, R.W.; Тай, Р.П.; Вудман Маргарет, Дж. Теплопроводность и удельное электрическое сопротивление платиновых металлов. платина. Встретились. Ред. 1962 , 6, 138–143. [Google Scholar]
- Пауэлл, Р. В. Lxxx. электрическое сопротивление жидкого железа. Лонд. Эдинб. Дублин Филос. Маг. J. Sci. 1953 , 44, 772–775. [Google Scholar] [CrossRef]
- Sha, X.; Коэн, Р.Э. Первопринципные исследования электросопротивления железа под давлением. Дж. Физ. Конденс. Материя 2011 , 23, 075401. [Google Scholar] [CrossRef] [PubMed]
- Арайс, С.; Колвин, Р.В. Удельное электрическое сопротивление железа высокой чистоты от 300 до 1300 °К. Physica Status Solidi (B) 1964 , 6, 797–802. [Google Scholar] [CrossRef]
- Лебедев С.В.; Савватимский С.А. Металлы при быстром нагреве плотными токами.
сов. физ. Успехи 1984 , 27, 749–771. [Google Scholar] [CrossRef]
- Milchberg, H.M.; Фриман, Р.Р.; Дэйви, Южная Каролина; Мор, Р.М. Удельное сопротивление простого металла от комнатной температуры до 10 6 к. физ. Преподобный Летт. 1988 , 61, 2634. [Google Scholar] [CrossRef]
- DeSilva, A.W.; Кунце, Х.-Й. Экспериментальное исследование электропроводности сильно связанной медной плазмы. физ. Ред. E 1994 , 49, 4448–4454. [Google Scholar] [CrossRef]
- ДеСильва, А.В.; Кацурос, Дж. Д. Электропроводность плотной плазмы меди и алюминия. физ. Ред. E 1998 , 57, 5945–5951. [Google Scholar] [CrossRef]
- Мики Ю.; Амано, Ю.; Сасаки, Т .; Кикучи, Т .; Харада, Н. Оценка электропроводности теплого плотного вещества меди и золота, генерируемого импульсным разрядом мощности с изохорным нагревом; МАГАТЭ: Вена, Австрия, 2003 г. [Google Scholar] «> Шефтман Д.; Красик, Ю.Е. Оценка электропроводности и уравнения состояния неидеальной плазмы при микросекундном масштабе подводного взрыва электрического провода. физ. Plasmas 2011 , 18, 092704. [Google Scholar] [CrossRef]
- Bilbao, L.; Родригес Прието, Г. Об измерении удельного сопротивления в эксперименте с взрывающейся проволокой. IEEE транс. Плазменные науки. 2018 , 46, 466–473. [Google Scholar] [CrossRef]
- Bilbao, L.; Родригес Прието, Г. Измерение удельного сопротивления газа нейтральной меди с помощью взрываемой проволоки в воздухе. заявл. науч. 2017 , 7, 829. [Google Scholar] [CrossRef][Green Version]
- Калантар, Д.Х.; Хаммер, Д.А. Наблюдение стабильного плотного ядра в нестабильной корональной плазме в экспериментах с плотным z-пинчем, инициированным проволокой. физ. Преподобный Летт. 1993 , 71, 3806–3809. [Google Scholar] [CrossRef] «> Иваненков Г.В.; Мингалеев, А.Р.; Пикуз, С.А.; Романова В.М.; Шелковенко Т.А.; Лебедев, П.Н.; Степневский, В .; Хаммер, Д.А. Динамика тонкой проволочной плазмы с холодной плотной сердцевиной. Дж. Эксп. Теор. физ. 1998 , 87, 663–671. [Google Scholar] [CrossRef]
- Саркисов Г.С.; Струве, К.В.; Макдэниел, Д.Х. Влияние силы тока на выделение энергии при взрывах металлических проводов в вакууме. физ. Plasmas 2004 , 11, 4573. [Google Scholar] [CrossRef]
- Саркисов Г.С.; Сасоров, П.В.; Струве, К.В.; Макдэниел, Д.Х. Состояние металлического сердечника в наносекундных взрывающихся проводах и связанные с ними явления. Дж. Заявл. физ. 2004 , 96, 1674–1686. [Академия Google] [CrossRef]
- Нэш, Ч.П.; Макмиллан В. Г. О механизме взрыва проводов. физ. Жидкости 1961 , 4, 911–917. [Google Scholar] [CrossRef]
- Ткаченко С.И.; Пикуз, С.А.; Романова В.М.; Тер-Оганесян, А.
Э.; Мингалеев, А.Р.; Шелковенко, Т.А. Развитие импульса перенапряжения при электрическом взрыве тонких проводов. Дж. Физ. Д заявл. физ. 2007 , 40, 1742–1750. [Google Scholar] [CrossRef]
- На основе термодинамических баз данных Горного управления США и Геологической службы США. Доступно в Интернете: http://www.thermart.net/freed-thermodynamic-database/ (по состоянию на 3 марта 2019 г.).).
Рисунок 1. (В цвете онлайн) Экспериментальная установка. «Щуп 3» и «Щуп 4» — это делители напряжения, Ph2 сигнализирует о фотодиоде, C — о блоке конденсаторов, а L0 и R0 — о сосредоточенных индуктивности и сопротивлении электрической цепи соответственно.
Рисунок 1. (В цвете онлайн) Экспериментальная установка. «Щуп 3» и «Щуп 4» — это делители напряжения, Ph2 сигнализирует о фотодиоде, C — о блоке конденсаторов, а L0 и R0 — о сосредоточенных индуктивности и сопротивлении электрической цепи соответственно.
Рисунок 2. Токовый сигнал разряда ALEX через железную проволоку при номинальном заряде батареи конденсаторов до 20 кВ. Другие экспериментальные ситуации имеют сходные формы. Насыщение сигнала является побочным эффектом усиления, необходимого для измерения слабого сигнала темновой паузы, в данном случае от 2 до 5 мкс, как более подробно поясняется в тексте.
Рисунок 2. Токовый сигнал разряда ALEX через железную проволоку при номинальном заряде батареи конденсаторов до 20 кВ. Другие экспериментальные ситуации имеют сходные формы. Насыщение сигнала является побочным эффектом усиления, необходимого для измерения слабого сигнала темновой паузы, в данном случае от 2 до 5 мкс, как более подробно поясняется в тексте.
Рисунок 3. Типичная полоса изображения в искусственных цветах. В этом эксперименте был взорван железный провод при зарядном напряжении 10 кВ в конденсаторной батарее. Общее время развертки составляет 20 мкс. Темная часть изображения соответствует расширению металлического газа, а более светлая часть в конце — началу образования плазмы. Горизонтальное измерение – это время, когда происходит радиальное расширение, вертикальное измерение.
Рисунок 3. Типичная полоса изображения в искусственных цветах. В этом эксперименте был взорван железный провод при зарядном напряжении 10 кВ в конденсаторной батарее. Общее время развертки составляет 20 мкс. Темная часть изображения соответствует расширению металлического газа, а более светлая часть в конце — началу образования плазмы. Горизонтальное измерение — это время, когда происходит радиальное расширение, вертикальное измерение.
Рисунок 4. Типичные штриховые изображения расширения газообразного платинового металла при различных зарядных напряжениях. Пространственный масштаб такой же, как и в предыдущих случаях, рис. 3, но обратите внимание на временной масштаб последнего эксперимента. Как и на предыдущем рисунке, линия слева — это провод перед электрическим разрядом.
Рисунок 4. Типичные штриховые изображения расширения газообразного платинового металла при различных зарядных напряжениях.