Марка | Внешний вид | Паяемый металл или металлическое покрытие | Применяемые припои | Назначение |
Канифоль марки А | Медь; серебряное, оловянное, цинковое, оловянно-свинцовое, оловянно-висмутовое, золотое покрытия | Оловянно-свинцовые, оловянно-свинцово-кадмиевые (при температуре пайки выше 220°С), серебряные ПСр1,5 и ПСр2 | Ручная и механизированная пайки и лужение монтажных элементов и других поверхностей. Консервация изделия для сохранения паяемости в условиях складского хранения. | |
Жидкость светло-коричневого цвета | То же | То же | То же, а также пайка проводников, имеющих изоляцию в виде трубок или эмалевую изоляцию, изделий с повышенными требованиями по сопротивлению изоляции | |
ФКДТ | Жидкость тёмно-коричневого цвета | Медь; серебряное, оловянное, оловянно-свинцовое, оловянно-висмутовое, золотое покрытия | Оловянно-кадмиево-индиевые, оловянно-свинцовые, оловянно-свинцово-висмутовые, оловянно-свинцово-кадмиевые, индиевые | Ручная и механизированная пайки и лужение монтажных элементов и других поверхностей. |
ЛТИ-120 | Жидкость тёмно-коричневого цвета с незначительным осадком | Сталь углеродистая, медь и её сплавы, никель и его сплавы; оловянное, серебряное, кадмиевое, цинковое, оловянно-свинцовое, оловянно-висмутовое покрытия | Оловянно-свинцовые, серебряные ПСр1,5 и ПСр2 | Ручная и механизированная пайки и лужение монтажных элементов, не имеющих на выводах изоляции в виде трубок, и других поверхностей в изделиях широкого применения. |
ФГСп, ФСкСп, ФСкПс | ФГСп, ФСкСп – бесцветная жидкость; ФСкПс – однородная паста светло-жёлтого цвета | Медь и её сплавы, никель и его сплавы; оловянное, серебряное, кадмиевое, цинковое, оловянно-свинцовое, оловянно-висмутовое покрытия | Оловянно-свинцовые, оловянно-свинцово-висмутовые, оловянно-свинцово-кадмиевые | Ручная (ФСкПс и ФСкСп) и механизированная пайки и лужение монтажных элементов, не имеющих на выводах изоляции в виде трубок и других металлических поверхностей в изделиях широкого применения |
ФТС | Жидкость жёлтого цвета | Медь; оловянное, серебряное, кадмиевое, цинковое, оловянно-свинцовое, оловянно-висмутовое покрытия | Оловянно-свинцовые, оловянно-свинцово-висмутовые, оловянно-свинцово-кадмиевые | Ручная и механизированная пайки и лужение монтажных элементов и других металлических поверхностей в изделиях широкого потребления |
ФДГл | То же | Оловянно-свинцовые | Ручная и механизированная пайки и лужение изделий широкого потребления. Групповая пайка методом погружения в паяльный флюс при температуре 220–250°С и оплавление электролитически оловянированных деталей перед пайкой | |
ФЦА | Бесцветная жидкость | Медь и её сплавы (в том числе БрБ), углеродистые и нержавеющие стали, никель и его сплавы | Оловянно-свинцовые и низкотемпературные серебряные | Предварительное лужение (механизированное и ручное) и пайка изделий при условии полного удаления (с применением нейтрализующих растворов) остатков флюса после пайки, кроме монтажных соединений |
ФДФс | Бесцветная жидкость | Сталь, хромоникелевые сплавы (нихром, пермаллой, суперинвар, ковар, инвар), медь и её сплавы | Оловянно-свинцовые | Ручная и механизированная пайки и лужение изделий, кроме монтажных соединений |
ЖЗ-2-АП |
Вязкая жидкость тёмно-коричневого цвета | Оловянно-свинцовые | Защита зеркала расплавленного припоя от окисления в механизированных установках пайки | |
284, 209 | Белый порошок | Медь и её сплавы, нержавеющие и конструкционные стали, жаропрочные сплавы | Серебряные | Пайка узлов РЭА и различных конструкций с применением газопламенного нагрева и в печах |
200 | Белый порошок | Нержавеющие и конструкционные стали, жаропрочные сплавы | Латунь и припои с температурой плавления 850–1000°С | Пайка узлов РЭА и различных конструкций с применением газопламенного нагрева и в печах |
34А, Ф370А | Белый порошок | Алюминий и его сплавы, кроме сплавов с содержанием магния выше 3% | Алюминиевые | Пайка узлов РЭА |
16ВК | Алюминий и его сплавы | Алюминиевые | Пайка узлов РЭА. Групповая пайка узлов методом погружения в соляную ванну |
Название | Описание и состав | Свойства | Чем отмывать остатки ? |
|
Один из самых старых материалов, используемых для флюсования при пайке. Этонатуральный продукт, который входит в состав смолы смолы сосновых деревьев. Канифоль представляет собой сложную смесь из эфиров органических смол и первичных одновалентных смоляных кислот (абиетиновая, нео-абиетиновая, пимаровая, палюстровая), которые могут присутствовать в ней в разных количествах. Твёрдая, хрупкая, стеклообразная прозрачная смола светло-жёлтого (реже тёмно-красного) цвета.
|
Не влияет на электрическое сопротивление изоляции. |
Водой не смывается. Остатки удаляются отмывкой спиртом, спирто-бензиновой смесью или жидкостями на основе растворителей (АКВЕН-12, АКВАЛИТ-Ультра, АКВЕН-16) |
ФКСп(ФКЭт) |
Канифоль сосновая 20-30% Одноатомный спирт(этиловый или изопропиловый) 80-70% |
Не коррозионный, не влияет на электрическое сопротивление изоляции. Отмывка рекомендуется. |
|
ФКТ
|
Канифоль сосновая 20-50 % Тетрабромид дипентена 0,05-0,1 % Спирт 79,95 – 49,9 % |
Не влияет на электрическое сопротивление изоляции. Отмывка рекомендуется. | |
ФТС |
Кислота салициловая 4 – 4,5 % Этиловый спирт 96 – 95,5 % |
Снижает сопротивление изоляции, слабокоррозионно активный. |
Остатки флюса могут быть удалены водой или жидкостями на водной основе (АКВЕН-16) |
ФГСп |
Гидразин солянокислый 2 — 4 % Глицерин 25 — 50 % Спирт этиловый 73 – 46 % |
Вызывает коррозию, снижает сопротивление изоляции. ОТМЫВКА ОБЯЗАТЕЛЬНА! |
|
ФСкСП |
Семикарбазид гидрохлорид 3 – 5 % Этиленгликоль(или глицерин) 25 – 50% Спирт этиловый 73 – 46 % |
Активный, вызывает коррозию и снижает сопротивление изоляции. Отмывка обязательна! |
|
ФКДТ |
Канифоль сосновая 10 – 20 % Диметилалкилбензиламмоний хлорид(кетами АБ) 0,1 – 3,0 % Трибутилфосфат 0,01 – 0,10 % Спирт этиловый 89,89 – 76,90 % |
Флюс нейтрален, остатки флюса после пайки не влияют на сопротивление изоляции диэлектриков. | Отмывка производится в спирте, спирто-бензиновой смеси. Или жидкостями на основе растворителей (АКВЕН-12, АКВЕН-16, АКВАЛИТ-Ультра) |
ЛТИ — 120 |
Канифоль сосновая 20 – 25 % Диэтиламин солянокислый 3 – 5 % Триэтаноламин 1 – 2 % Спирт этиловый 76 – 68 % |
Неактивен, не вызывает коррозии. |
Сварочные флюсы классификация и особенности
Содержание
1. Для чего нужен флюс при сварке
2. Условия использования сварочных флюсов
3. Недостатки
4. Как работают флюсы
5. Сварочные флюсы — классификация
6. Химический состав флюсов для сварки
7. Виды флюсов для сварки по назначению
8. Назначение сварочного флюса — примеры
9. Флюсы для газовой сварки
10. Флюсы для автоматической сварки
При электродуговой или газовой сварке в условиях высоких температур значительно увеличивается химическая активность обрабатываемой зоны. Металл усиленно окисляется под воздействием атмосферного воздуха, в результате шлаки и окислы попадают в него, снижая интенсивность металлургических процессов и в итоге ухудшая качество сварного шва. Для предотвращения этих процессов необходима защитная газовая или жидкая среда, которая изолирует зону сварки. Ее и создают флюсы — неметаллические композитные порошковые компоненты.
Таким образом, назначение флюсов при сварке — изоляция сварочной ванны от атмосферного воздуха, защита наплавляемого металла от интенсивных окислительных процессов, стабильное горение сварочной дуги и получение сварного шва необходимого качества.
Для чего нужен флюс при сварке
Использование флюсов обеспечивает следующие преимущества при сварке.

- Как при электродуговой, так и при газовой сварке флюс сварочный обеспечивает более интенсивное расплавление металла — (соответственно при больших токах или высокой концентрации кислорода). Благодаря этому нет необходимости заблаговременно разделывать кромки будущего сварного шва.
- В зоне шва и на прилегающих к нему поверхностях удается избежать угара металла — его потерь на окисление и испарение.
- Горение дуги имеет более высокую стабильность, что особенно важно при сложных конфигурациях шва
- Снижаются потери энергии источника тока на нагрев металла, соответственно увеличивается его КПД.
- Оптимизируется расход присадочного материала.
- Более удобное выполнение работ для сварщика, потому что флюс экранирует некоторую часть пламени дуги.
Условия использования сварочных флюсов
Задача флюса — стабилизация металлургических процессов при сохранении необходимой производительности электродов. Для этого в процессе сварки следует соблюдать определенные условия.
- Флюс не должен вступать в химическую реакцию с металлом стержня и основным металлом.
- Зона сварной ванны должна оставаться изолированной на протяжении всего сварочного процесса.
Остатки флюса, связанные со шлаковой коркой в результате сварки, по завершении работ должны легко удаляться. При этом до 80% материла после очистки можно использовать заново.
Недостатки
Условных минусов в использовании сварочных флюсов немного.
- Высокая стоимость, которая примерно сопоставима с ценой на сварочную проволоку.
- Yевозможность сразу осмотреть сварной шов. В силу этого, особенно в конструкциях сложной формы, место сварки предварительно тщательно подготавливается.
Как работают флюсы
- Перед сваркой на места соединений наносится толстый (40-60 мм) слой флюса.
- Электрод вводится в зону сварки, происходит поджиг дуги.
- Под воздействием высоких температур (до 6000 °C) флюс с его низкой плотностью быстро плавится в газовом пузыре, изолируя сверху сварную ванну, перекрывая к ней доступ газовых, водяных паров и других химических веществ.
- Имея высокое поверхностное натяжение, таким же образом расплав флюса предотвращает интенсивное разбрызгивание металла.
- Это позволяет значительно увеличить ток дуги (до 1000-2000 Ампер) без серьезных потер материала электрода и с сохранением хорошего качества шва.
- Под воздействием флюса в зоне дуги происходит концентрация тепловой мощности — в результате плавление металла происходит быстрее.
- При этом металлом заполняются все стыки, независимо от состояния кромок.
- Изменяется материальный баланс сварного шва — 60-65% процентов в нем составляет металл свариваемых деталей, и только остальное — это металл сварочного электрода.
Сварочные флюсы — классификация
Классификация флюсов чрезвычайно широка. Их различают по внешнему виду и физическому состоянию, химическому составу, способу получения, назначению. Так, например, для наплавки или дуговой сварки, как правило, используются гранулированные или порошковые флюсы с определенными показателями электропроводности, а для газовой — газы, порошки, пасты.
По способу получения композитов
Различают флюсы плавленые и неплавленые.
Флюс сварочный плавленый широко используют не только при сварке, но при наплавке. Он демонстрирует высокую эффективность в случаях, когда поверхность металла сварного шва путем добавления дополнительных химических элементов должна получить более высокие технические характеристики — например, повышенную стойкость к коррозии или очень ровный и гладкий шов.
Наплавка под флюсом

Получают плавленые флюсы следующим способом: компоненты размалывают, смешивают, затем расплавляют в пламенных или электропечах при полном отсутствии кислорода. Далее нагретые частицы пропускаются через непрерывный поток воды, затвердевая и превращаясь таким образом в гранулят. Размер частиц различен — чем тоньше сварочный пруток, тем меньше должны быть и гранулы.
Неплавленые флюсы (керамические) для сварки изготавливаются путем перемешивания измельченных частиц шихты из ферросплавов, минералов, шлакообразующих без последующего плавления. Частицы смешиваются со стеклом и далее спекаются.
В ряду их преимуществ:
- низкий расход,
- возможность многократного использования,
- высокое качество получаемого шва.

Пример — керамический сварочный флюс марки UF (UF-01, UF-02, UF-03) который используется в энергетике и гражданском строительстве для сварки металлоконструкций из низколегированных сталей повышенной прочности.
Химический состав флюсов для сварки
Химический состав — важная составляющая в характеристике флюсов. Материал должен быть химически инертен в условиях очень высоких температур. Помимо этого, он должен обеспечивать эффективную диффузию отдельных элементов (например, легирующих) в металл шва.
Наибольшую массовую долю (от 35…80% от общего объема) в сварочном флюсе обычно (но не во всех) составляет диоксид кремния (кремнезём) — кислотный оксид, бесцветный прозрачный кристаллический минерал. Кремний препятствует процессу образования углерода, тем самым снижая риски появления трещин и пор в металле шва.
Значительную часть составляет марганец. Как активный раскислитель, этот компонент флюсов для сварки снижает образование окислов в зоне сварочной ванны, вступая в реакцию вначале с кислородом в окислах железа, затем и с оксидом кремния. Результат сложной реакции — оксид марганца, нерастворяемый в стали и впоследствии легко удаляемый. Кроме того, марганец реагирует с вредной для металла шва серой — он связывается с ней в сульфид, который затем также удаляется с поверхности шва.
Также в ряду химических элементов флюсов — легирующие добавки — помимо кремния и марганца это молибден, хром, титан, вольфрам, ванадий и другие. Из задача — восстановить первичный химический состав металла, а в ряде случаев — путем легирования восполнить собой выгоревшие основные примеси стали и обеспечить металлу шва дополнительные специальные свойства. Обычно во флюсе они представлены соединениями с железом — ферросплавами (феррохром и т. д.).
Виды флюсов для сварки по назначению
От назначения сварочных флюсов напрямую зависит их выбор по химическому составу.
- Для сварки низкоуглеродистых сталей применяются флюсы с большим содержанием кремния и марганца в сочетании с проволокой из низкоуглеродистой стали без легирующих добавок. Второй вариант — малая доля марганца (или вообще его отсутствие) во флюсе, но легирующие добавки присутствуют в стали сварочного прутка.
- Для сварки низколегированных сталей используются флюсы с высокой химической инертностью, — выше, чем для низкоуглеродистых сталей. Благодаря этому получают более пластичный сварной шов. Пример — флюс для сварки стали АН-46.
- Для сварки высоколегированных металлов применяются флюсы с минимальной химической активностью. Кремний, как и марганец, практически не используется — его заменяет флюорит (плавиковый шпат), благодаря которому образуются легко отделяемые легкоплавкие шлаки. Также в таких флюсах обычно содержатся оксид алюминия, негашеная известь.
- Для сварки активных металлов (таких, как титан) используют солевые флюсы — как правило, это хлоридные и фторидные соли щелочных металлов. Примесь кислорода в них полностью отсутствует, поскольку она снижает пластичность шва.
Назначение сварочного флюса — примеры
Плавленые флюсы | Неплавленые флюсы | ||
АН-348-А, АН-348-АМ, АН-348-В, АН-348-ВМ, ОСЦ-45, ОСЦ-45М, АН-60, ФЦ-9 | Механическая сварка и наплавка низколегированных и углеродистых сталей низколегированной и углеродистой сварочной проволокой | АНК-35 | Сварка низкоуглеродистых сталей низкоуглеродистой проволокой Св-08 и Св-08А |
АН-8 | Электрошлаковая сварка углеродистых и низколегированных сталей; сварка низколегированных сталей углеродистой и низколегированной сварочной проволокой. | АНК-46 | Сварка низкоуглеродистых и низколегированных сталей |
АН-15М, АН-18, АН-20С, АН-20П, АН-20СМ | Дуговая автоматическая сварка и наплавка высоко- и среднелегированных сталей | АНК-30, АНК-47 | Сварка швов высокой хладостойкости |
АН-22 | Электрошлаковая сварка и дуговая автоматическая наплавка и сварка низко- и среднелегированных сталей | АНК-45 | Сварка высоколегированных сталей |
АН-26С, АН-26П, АН-26СП | Автоматическая и полуавтоматическая сварка нержавеющих, коррозионностойких и жаропрочных сталей | АНК-40, АНК-18, АНК-19 | Наплавка низкоуглеродистой сварочной проволокой Св-08 и Св-08А; |
АН-17М, АН-43 и АН-47 | Дуговая сварка и наплавка углеродистых, низко- и среднелегированных сталей высокой и повышенной прочности | АНК-3 | В качестве добавки к флюсам марок АН-348А, ОСЦ-45, АН-60 для повышения стойкости швов к образованию пор |
Флюсы для газовой сварки
Для сварки алюминия и других цветных металлов, чугуна, инструментальных сталей, отдельных марок тонколистовой стали используется защитная газовая атмосфера. Ее обеспечивают газообразные, пастообразные, а также порошковые флюсы. Они могут наносится:
- на кромки соединяемых деталей;
- напрямую в сварную ванну;
- на присадочный пруток.
В зависимости от физического состояния материала флюсы для сварки подают в рабочую зону по-разному. Некоторую сложность вызывают порошкообразные композиты — их необходимо равномерно и точно вносить в расплав, не позволяя потоку газа раздувать порошок. Составы в виде паст подают на участок соединения. Для подачи газообразных флюсов используют расходомеры — с их помощью газ дозированно подается в рабочую зону.
Электромагнитный расходомер

Важный момент: для газовой сварки флюс по составу подбирают в зависимости от образующихся в ходе сварки оксидов. Если они кислые, флюсы должны быть щелочными (основными), напротив, если щелочные оксиды — выбирают кислые флюсы.
Флюсы, применяемые при газовой сварке наиболее широко:
- медь, латунь, бронза — для их сварки используют кислые флюсы с включением борсодержащих соединений (борная кислота и т. д.) — например, такие марки, как МБ-2 или БМ-1;
- чугун — для его сварки обычно используются флюсы с включением различных соединений щелочных металлов — натрия и калия;
- алюминий — здесь используются составы с содержанием фторидов калия, лития и натрия, а также хлориды. В этом случае наиболее широко применяется сварочный флюс марки АФ-4А.
Флюсы для газовой сварки не используются для соединения деталей из низкоуглеродистых сталей, поскольку на поверхности расплавленного металла интенсивно скапливаются легкоплавкие оксиды железа.
Флюсы для автоматической сварки
Автоматическая и полуавтоматическая сварка наиболее широко применяется при работе с большими конструкциями. Благодаря высоким токам и флюсу возможно сваривание деталей значительной толщины, при этом — без предварительной разделки кромки. Области использования — сваривание труб, изготовление резервуаров, судостроение.

Для такого способа сварки характерно автоматическое поддержание стабильно горящей электродуги, необходимого количества флюса (с отсосом нерасплавившегося), а также непрерывное обновление расплавленного электрода. Чтобы поддерживать в сварочной зоне защитное газовое облако нужного состава, толщина слоя флюса должна быть 40-80 мм, ширина 50-100 мм. Марка флюса для автоматической сварки, как и для классической дуговой, также зависит от характеристик свариваемого металла. Сварка осуществляется в нижнем пространственном положении.
Выгодно купить флюс для сварки различных типов и марок вы можете в компании «Центр Метиз».
Приготовление флюса ФКЭт, ФКСп — Gostost.ru
Приготовление флюса ФКЭт, ФКСп — Gostost.ruТехнологическая инструкция
Определение и назначение.
- Настоящая инструкция устанавливает порядок приготовления и применения флюса ФКЭт, ФКСп.
- Инструкция распространяется на работников цеха и является обязательной для вязальщиков, монтажников и приготовителя флюсов.
Техника безопасности.
- При выполнении работ по приготовлению флюса необходимо соблюдать требования «Инструкции по охране труда для работающих с ЛВЖ и ГЖ».
- Исполнитель должен проходить периодический медицинский осмотр.
- Приготовление флюса производить в отдельном изолированном помещении в вытяжном шкафу при включенной местной вытяжной и общей приточной вентиляции.
- При попадании компонентов флюса на кожу необходимо вымыть руки горячей водой с мылом.
- При попадании компонентов флюса на пол или поверхность приспособления его необходимо собрать лоскутом холстопрошивного полотна или ватой.
- Материалы, загрязненные флюсом, необходимо собирать в специальные емкости с крышкой и после работы вынести из рабочего помещения в специально отведенное место.
- Запрещается хранение и прием пищи на рабочем месте.
- Работник должен быть одет в чистую производственную одежду и использовать следующие средства индивидуальной защиты:
- Халат белый х/б ГОСТ 12.4.131-83
- Косынка (шапочка) ГОСТ 29298-92
- Перчатки резиновые хирургические ГОСТ 3-88
- Перчатки х/б трикотажные ГОСТ 5007-87
- Респиратор ШБ-1 «Лепесток» ГОСТ 12.4.028-76
- Защитные очки ГОСТ Р.12.4.013
Технические требования.
- К работе по приготовлению флюса должны допускаться исполнители, изучившие данную инструкцию, требования по охране труда, правила противопожарной безопасности и аттестованные на данные работы.
- Рабочее место приготовителя компаундов, клеев и флюсов должно отвечать нормам чистоты. Под нормами чистоты понимается отсутствие пыли, грязи, посторонних предметов, оснастки и инструмента, не участвующих в данных операциях.
- Рабочее место приготовителя компаундов, клеев и флюсов должно отвечать нормам противопожарной безопасности, то есть количество ЛВЖ не должно превышать суточных норм расхода и храниться в вытяжном шкафу в таре цеховой.
- При измерении времени пользоваться бытовыми часами.
- Ежедневно, в начале смены контролировать температуру и влажность в помещении заливки при помощи гигрометра психрометрического ВИТ-1(ВИТ-2) с записью результатов в журнале.
- Приготовление флюса производить в помещении с температурой среды (15 ÷ 30)°С и относительной влажностью воздуха (40-80)%.
- Материалы, используемые при приготовлении флюса, должны иметь ярлыки хранения, содержащие в себе следующие данные:
- — название материала;
- — номер партии;
- — ТУ, ГОСТ, ОСТ;
- — дата изготовления;
- — гарантийный срок хранения;
- — номер заключения ОТК о качестве.
- Материалы должны применяться с учетом гарантийного срока хранения.
- По истечении гарантийного срока хранения материалы должны дентифицироваться ярлыками на несоответствующую продукцию и в работу не выдаваться до получения протокола перепроверки.
- После получения протокола перепроверки, с материалом поступают в соответствие с результатом переиспытаний: перемещают в изолятор брака и утилизируют, если качество не подтвердилось, или заносят дату очередной проверки в ярлык хранения и выдают в работу, если материал соответствует НД
- Срок хранения ФКЭт, ФКСп – 2 недели при температуре от 15 ºС до 30º С, относительной влажности воздуха (65±10)% в месте, защищенном от прямого попадания солнечных лучей.
- Флюсы ФКЭт, ФКСп готовить в начале рабочей недели по требованию бригадира (мастера). Количество флюса определяется потребностью цеха на одну рабочую неделю, при необходимости, флюс готовят дополнительно.
- Приготовленный флюс ФКЭт на электропроводность контролируется приготовителем. Флюс ФКЭТ на рабочих местах монтажников и вязальщиков контролируется технологом цеха, контролером ОТК летучим контролем.
- Контроль осуществляется прибором ПКФ-1.
- Приготовленный флюс должен храниться в таре цеховой из стекла или полимерного материала с плотно закрывающейся крышкой. Тара должна иметь этикетку с информацией о дате приготовления флюса и фамилией приготовителя, сроке хранения, отметку о проверке на электропроводность.
- На рабочем месте монтажника флюс должен находиться в количестве не превышающем норму на одну рабочую неделю в маркированной таре (флюснице).
- После окончания рабочей недели флюс слить в отдельно отведенную тару с крышкой, после работы вынести в специально отведенное место. Тару под флюс тщательно промыть ацетоном после чего ополоснуть теплой водой. Не допускается наливать вновь приготовленный флюс в грязную тару.
Общие сведения
- Паяльные флюсы предназначены для использования в технологических процессах пайки и горячего лужения с целью удален
Качество сварного шва определяется не только способностями мастера правильно организовать дугу, но и специальной защитой рабочей зоны от внешних воздействий. Главным врагом на пути к созданию прочного и долговечного металлического соединения является естественная воздушная среда. Изоляцию шва от кислорода обеспечивает флюс для сварки, но не только в этом заключается его задача. Различные конфигурации состава этой добавки с сочетанием защитной газовой среды позволяют по-разному управлять параметрами шовного соединения.
Назначение флюса
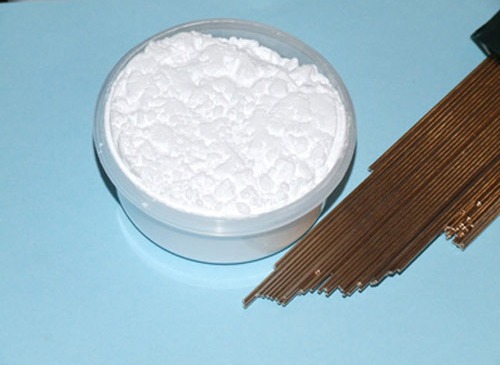
Сварочный расходник данного типа направляется в зону горения и в зависимости от характеристик своего расплава оказывает защитно-модифицирующее воздействие на участок формирования шва. В частности, материал может выполнять следующие функции:
- Создание шлаковой и газовой изоляции для сварочной ванны.
- Наделение сварного соединения определенными технико-физическими свойствами.
- Поддержание стабильности горения дуги.
- Перенос электродного металла (или проволочного расплава) в зону сварки.
- Устранение нежелательных примесей в шлаковой прослойке.
Если говорить о совместимости разных флюсов для сварки с металлами, то наиболее распространенные марки имеют следующие назначения:
- ФЦ-9 – стальные углеродистые сплавы с низким легированием.
- АН-18 – стальные сплавы высокого легирования.
- АН-47 – низко- и среднелегированные стали, характеризующиеся высокими прочностными показателями.
- АН-60 – стали низкого легирования, используемые в трубопроводах.
- ФЦ-7 – используется при сварке низкоуглеродистой стали на токе большой силы.
- ФЦ-17 – гранецентрированное высокотемпературное железо.
- ФЦ-19 – сплавы с повышенным содержанием хрома.
- ФЦ-22 – применяется для выполнения углового шовного соединения в работе с легированными углеродистыми сталями.
- 48-ОФ-6 – задействуется в техниках сварки с подключением высоколегированной электродной проволоки.
Составы флюса
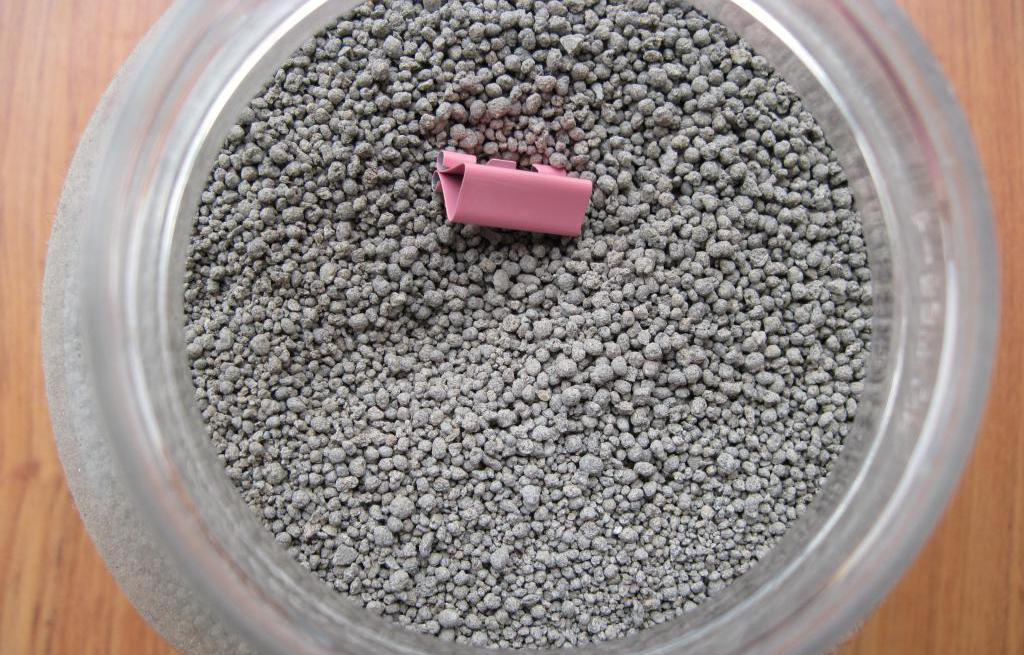
Сам по себе флюс, как правило, выпускается в виде гранулированного порошка с фракцией порядка 0,2–4 мм. Но наполнение и происхождение данного продукта может быть очень разным и не всегда однородным. В связи с этим выделяют следующие виды флюса для сварки:
- Оксидные. Большую часть в содержании составляют металлические оксиды и примерно на 10% приходится доля фторидных элементов. Такой флюс используется для работы с низколегированными и фтористыми стальными сплавами. Также в зависимости от содержания оксидные флюсовые составы делятся на бескремнистые, низкокремнистые и высококремнистые.
- Солеоксидные. Еще такие порошки называют смешанными, так как наполнение может в равной степени формироваться оксидами и солевыми соединениями. Используется такой флюс для обработки легированной стали.
- Солевые. Вовсе исключается наличие оксидов, а основу состава образуют фториды и хлориды. Целевое назначение солевого флюса – электрошлаковый переплав и сварка активных металлов.
Технология изготовления флюса
В процессе изготовления основа для флюса (шихта) подвергается нескольким процедурам переработки, в числе которых выплавка, грануляция, формовка и проверка на качество. Сырье шихты перед производственным процессом сегментируется на мелкое, среднее и крупное. Каждая партия проходит тщательную мойку и сушку, так как чистота и точность в параметрах будущего флюса поддерживаются изначально. Затем выполняют взвешивание, дозировку и смешивание с другими технологическими компонентами. Выплавка и грануляция флюса для сварки производится на специальном оборудовании – задействуются газопламенные или электродуговые печи, бассейны для обливки холодной водой и металлические поддоны. На финальных этапах обработки выполняется сушка с просеиванием. Прошедший контроль флюс упаковывается в специальные мешки или ящики с огнеупорными свойствами.
Требования ГОСТа к флюсу
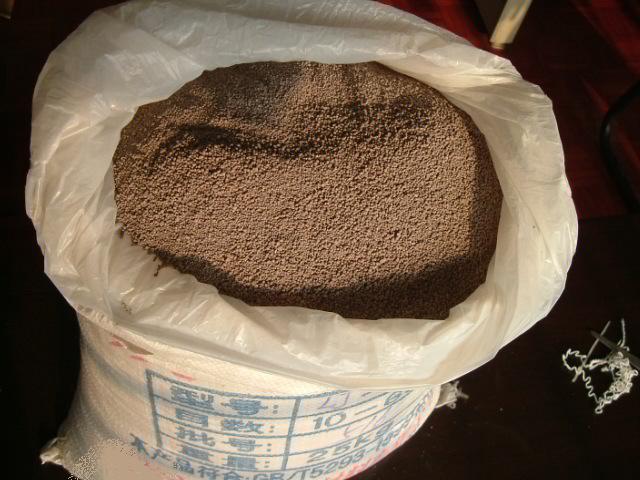
Нормативные требования затрагивают несколько направлений оценки качества флюса, а также регулируют правила обеспечения безопасности при обращении с материалом и методы проведения его испытаний. Что касается основных параметров, то к ним предъявляются следующие требования:
- Исключаются во флюсовом порошке зерна, размер которых превышает 1,6 мм. Процент их содержания не должен составлять более 3% от всей массы.
- Допускается производство флюса с фракцией до 0,25 мм, если это условие изначально было оговорено с потребителем.
- Также по соглашению с потребителем допустимо изготовление материала фракцией зерен от 0,35 до 2,8 мм, но только применительно к марке АН-348-А.
- Влажность флюсов в зависимости от марки не должна превышать коэффициент от 0,05 до 0,1%.
Что касается требований безопасности, то меры индивидуальной защиты являются главным предметом регуляции ГОСТа. Сварка под флюсом должна выполняться в соответствии с мерами противопожарной безопасности. Отдельно должна контролироваться концентрация применяемого флюсового порошка, который по умолчанию считается химически опасным и производственно вредным.
Плавленый и неплавленный флюс
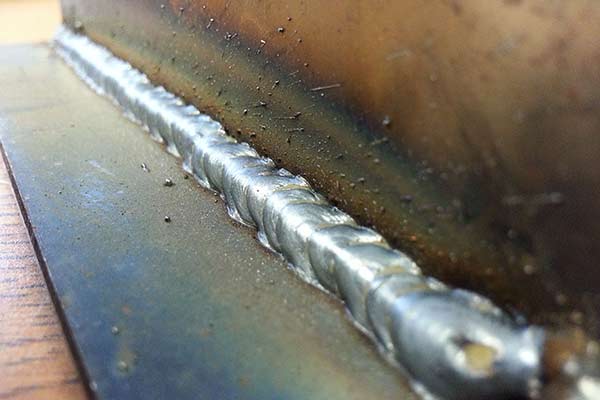
Содержание плавленого порошка в основном формируют шлакообразующие компоненты. Их вырабатывают в результате сплавления составляющих элементов, среди которых кварцевый песок, марганцевая руда и мел. Путем их смешивания в определенных пропорциях с последующей плавкой в печах можно получить модификатор для шва с определенным набором характеристик. Более функциональна дуговая сварка под флюсом, произведенным неплавленным способом. Это смесь зернистых и порошковых материалов, которые помимо шлакообразующей основы также включают в состав легирующие элементы и раскислители. Отсутствие операции плавления дает возможность вводить в состав флюса металлическую пыль и ферросплавы, которые расшифруют возможности улучшения соединений.
Виды сварки под слоем флюса
С применением флюса может выполняться как ручная, так и автоматическая сварка – принципиальная разница будет зависеть от выбранного оборудования. Электродуговая сварка выполняется в режиме саморегуляции или при поддержке автоматического контроля напряжения. Оптимально использовать инверторные установки, дополненные барабанами для подачи проволоки. Также распространена сварка с флюсом без газа, который по умолчанию выступает в качестве защитной среды от кислорода и азота. Чем же хороша техника, исключающая этот барьер перед негативными факторами воздействия? Во-первых, при условии выбора подходящего флюса он сможет выполнить весь перечень защитных и вспомогательных задач применительно к формируемому шву. Во-вторых, отсутствие газовой среды облегчает саму организацию процесса. Не нужно подготавливать баллон с аргонно-углекислотная смесью, а также защищать зону сварки от избыточного термического воздействия при использовании горелки.
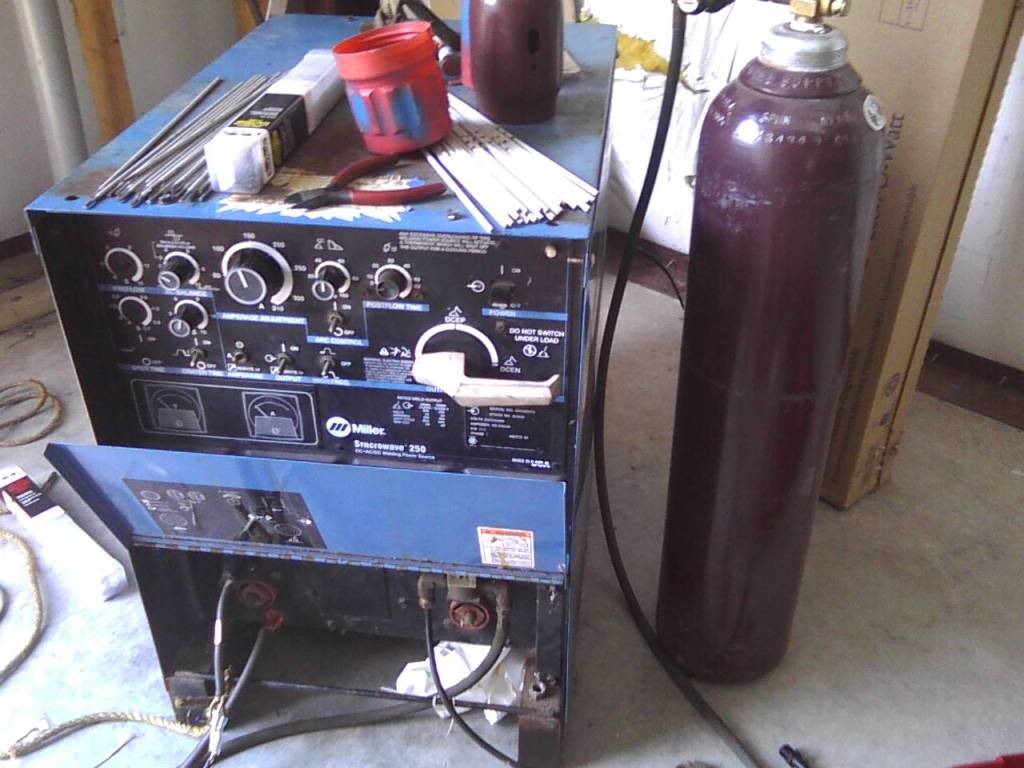
Техника применения флюса
После розжига дуги оператор должен ее поддерживать между окончанием электрода и заготовкой именно под слоем флюса. Порошок насыпается слоем 55-60 мм, после чего дугу следует буквально утопить в этой массе, пока она будет плавиться. При среднем весе флюса его статическое давление на металл может составлять порядка 8-9 г/см кв. Этой величины достаточно для устранения нежелательных механических воздействий на сварочную ванну. При использовании проволоки для сварки с флюсом можно добиться и минимальных показателей разбрызгивания расплава. Это условие выполняется путем обеспечения стабильного контакта зоны расплава с плавящейся проволокой и флюсом, а также за счет регуляции силы тока. Защита со стороны газа в данном случае тоже не требуется, но контроль мощности будет особенно важен. Как правило, комбинация проволоки и флюса используется при сварке на токе высокой плотности, поэтому и автомат должен подбираться с учетом поддержки постоянной скорости направления электродной нити.
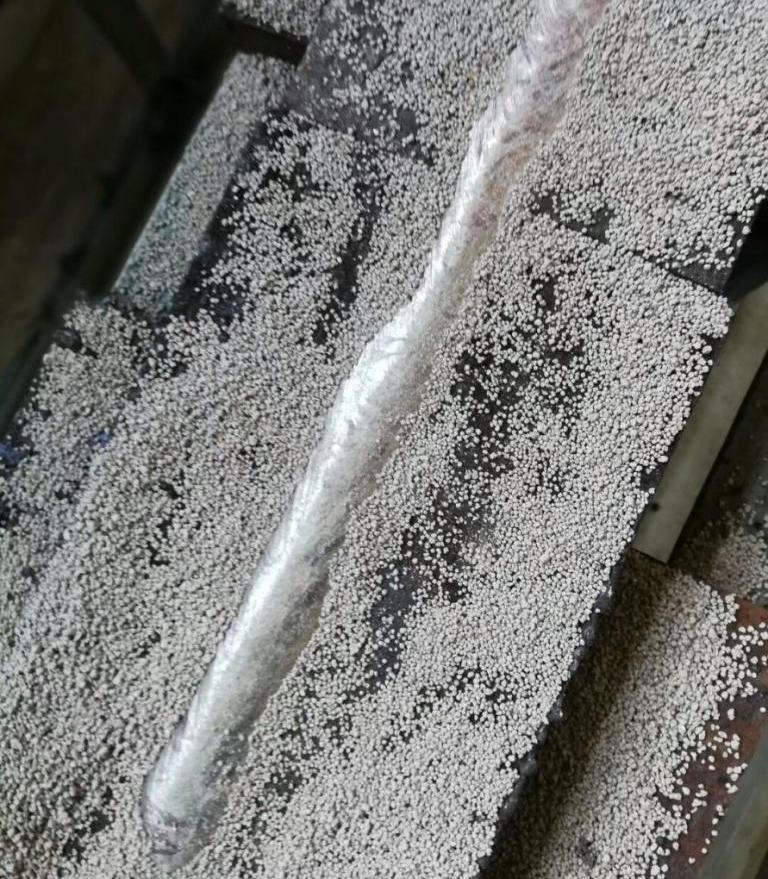
Плюсы от применения флюса
Использование флюса, безусловно, сказывается на формировании шва наилучшим образом, так как минимизируются негативные факторы рабочего процесса в условиях открытого воздуха. Из очевидных преимуществ можно отметить снижение дефектов в зоне соединения, минимизацию разбрызгивания и более эффективный контроль дуги со всеми возможностями автоматического регулирования. Что еще очень важно, участок сварка под флюсом всегда виден оператору. Это позволяет при необходимости своевременно вносить корректировки в процесс, а в некоторых случаях даже обходиться без специальной маски.
Недостатки от применения флюса
Слабые места данной технологии обуславливаются более высокими требованиями к оборудованию, так как для эффективного расплава флюса требуется большая мощность. Сегодня выпускаются специальные модификации аппаратов для аргонодуговой сварки в среде флюса, имеющие специальную оснастку для его подготовки и подачи. Логично, что такие модели стоят на 15-20% дороже. Еще один недостаток связан с увеличением зоны расплава. Хотя ее можно контролировать в определенных границах, мелкие элементы точечно обрабатывать в таких условиях проблематично.
Заключение
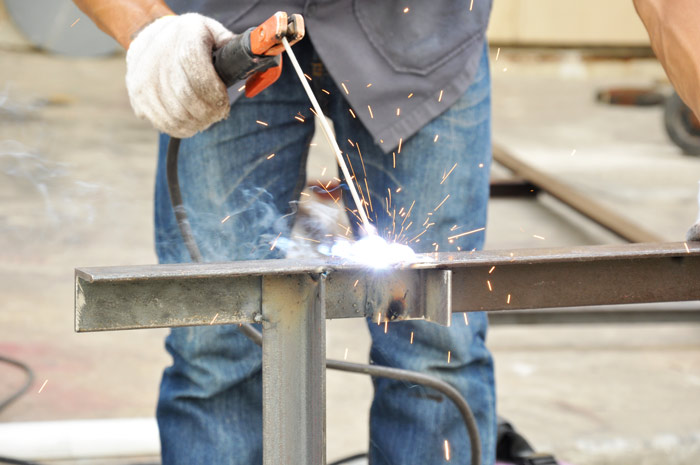
Флюс как расходный материал, улучшающий качество сварочного процесса, облегчает многие производственные и строительные мероприятия данного спектра. Но и в бытовых условиях его нередко используют на даче, в гараже или просто в ремонтных операциях. Выбирая данный материал для собственных нужд, очень важно не прогадать в оценке качества. Как отмечает тот же ГОСТ, флюс для сварки должен поставляться на рынке в плотных бумажных мешках от 20 до 50 кг с указанием транспортной маркировки. По специальному заказу можно оформлять и мелкую фасовку, но и для этого должны предусматриваться специальные контейнеры. Причем взвешивание должно производиться с максимальной погрешностью в 1% относительно общего веса тары.
Химический состав флюса?
Спросите экспертов 1 октября 2007 г.Химический состав флюса?
Каков реальный состав активатора потока? Имеет ли флюсующая способность кислот какую-либо связь с их кислотностью?
Питер Гонг
Ответы группы экспертов
Флюсы содержат широкий спектр компонентов, и особенно в случае паяльной пасты могут присутствовать определенные химические вещества на низких уровнях, чтобы обеспечить особые свойства в поведении продукта.Флюс существует для очистки металлических поверхностей от их естественного поверхностного оксидного слоя, так что расплавленный припой может смачивать нижележащий металл и образовывать прочную прочную связь. Конечно, флюсы предоставляют другие связанные с процессом характеристики (реология для печати паяльной пасты, липкость к компонентам и т. Д.), Но это, как правило, физические, а не химические свойства. Учитывая назначение флюса, следует использовать любое химическое вещество, которое удаляет оксиды металлов из обычных электронных материалов при температурах пайки, но на практике, особенно с флюсами No Clean, очень важно, чтобы флюс был не настолько агрессивным, чтобы он сильно растворялся металла, а также оксиды.Также важно, чтобы у fllux была очень низкая химическая активность ниже температур пайки. Разработчики достигают правильного баланса активности, используя мягкие карбоновые кислоты (одна из наиболее важных — канифоль и ее производные) и небольшое количество галогенидов и аминов. По существу (но очень сильно упрощенные) кислоты растворяют оксидные пленки, в то время как галогениды и амины разрушают их, ускоряя растворение. Существует некоторая связь между кислотностью и активностью флюса, но большинство систем флюса неводные, поэтому кислотность не всегда является значимым понятием.Активность, видимая пользователем, представляет собой сочетание собственной скорости реакции с оксидами (активаторы могут быть более эффективными для некоторых металлов и совсем не активными для других), устойчивостью (способность растворять большое количество оксидов металлов) и долговечностью (активаторы являются намеренно выбран иногда для разложения, чтобы обеспечить нейтральные остатки). Добавьте к этому тот факт, что разработчики часто «химически связывают» активаторы, поэтому они присутствуют во флюсе только при нагревании до температуры пайки, и я думаю, вы можете понять, почему нет простого ответа на этот вопрос.
Маркетинг
360-Biz
Дуглас Диксон — директор по маркетингу 360 BC Group, маркетингового агентства с офисами по всей территории США. 360 BC специализируется на консалтинге и реализации успешных маркетинговых программ, в которых используются новейшие стратегии маркетинга, продаж и технологий. Как ветеран электроники, Диксон проработал в отрасли более 30 лет в таких компаниях, как Henkel, Universal Instruments, Camelot Systems и Raytheon.Опыт электронной промышленности Dixon включает в себя широкий набор навыков, включая инженерные, полевые услуги, приложения, опыт управления продуктами и маркетинговые коммуникации.
,Flux используется для очистки металлических поверхностей перед их пайкой. Поскольку любые оксиды, которые остаются на металлической поверхности, могут привести к плохим соединениям припоя, основная функция флюса состоит в том, чтобы раскислять металлические поверхности без разложения. Поток припоя является важной частью электронного проектирования и ремонта. Давайте посмотрим на различные типы потока.
канифоль Flux
Поток канифоли, что неудивительно, состоит в основном из канифоли, которая извлекается из сока сосен и содержит активный ингредиент абиетиновую кислоту (также могут присутствовать другие кислоты).Существует три типа потока канифоли — канифоль (R), канифоль с мягкой активацией (RMA) и канифоль с активированной канифолью (RA) — каждый из которых имеет разный уровень активаторов, агентов, позволяющих потоку раскислять и очищать.
Флюс канифолииспользуется для очистки уже чистых поверхностей и имеет преимущество, не оставляя следов. Мягко активированный флюс канифоли используется на более грязных поверхностях и оставляет больше остатков, чем обычный флюс канифоли; после использования мягко активированного флюса канифоли вы используете очиститель флюса для очистки поверхности.Активированный канифоль флюс очищает лучше, но оставит после себя значительное количество остатков — из-за этого флюс, активированный канифолью, используется редко.
Водорастворимый флюс
Водорастворимый флюс, также называемый флюсом органической кислоты, обычно изготавливается из гликолевых оснований. Недостатком использования водорастворимого флюса является то, что он часто связывается с самой печатной платой или другими металлическими поверхностями, и в результате потребуется тщательная очистка. Кроме того, водорастворимый флюс имеет тенденцию быть более агрессивным окислителем, чем обычно требуется.Органический флюс является более реактивным, чем флюс, активированный канифолью, и, следовательно, является более сильным очистителем. (Примечание: Вы также можете найти неорганический водорастворимый флюс, который даже более мощный, чем водорастворимый флюс.)
No-Clean Flux
Неочищенный флюс — это смесь органических смол, за исключением канифоли, в смеси с некоторыми неорганическими агентами. Поведение и свойства неочищенных флюсов могут значительно различаться в зависимости от их химического состава; например, некоторые неочищенные флюсы оставляют огромное количество остатка, что непривлекательно, хотя и не представляет угрозы для поверхности.Однако вы можете найти неочищенные флюсы, которые не оставят следов. Основным преимуществом использования неочищенного флюса является то, что вам не нужно чистить поверхность после пайки, поскольку они не влияют на электропроводность.
,Что такое поток утечки и окантовка? — Circuit Globe
Поток утечки определяется как магнитный поток, который не следует по специально намеченному пути в магнитной цепи. Взяв пример соленоида, вы можете объяснить поток утечки и окантовку обоих.
Когда ток проходит через соленоид, он создает магнитный поток.
Большая часть потока устанавливается в сердечнике соленоида и проходит по определенному пути, который проходит через воздушный зазор и используется в магнитной цепи.Этот поток известен как Полезный поток φ u .
Поскольку практически невозможно, чтобы весь поток в цепи следовал по специально намеченному пути и устанавливался в магнитном сердечнике, и, таким образом, часть потока также настраивалась вокруг катушки или окружала сердечник катушки и не использовалась для любой работы в магнитопроводе. Этот тип флюса, который не используется для какой-либо работы, называется Leakage Flux и обозначается φ l .
Следовательно, общий поток Φ , создаваемый соленоидом в магнитной цепи, является суммой потока утечки и полезного потока и определяется уравнением, показанным ниже:
Коэффициент утечки
Отношение общего создаваемого потока к полезному потоку, установленному в воздушном зазоре магнитной цепи, называется коэффициентом утечки или коэффициентом утечки. Обозначается через (λ).
Окаймление
Полезный поток, когда он установлен в воздушном зазоре, он имеет тенденцию выпучиваться наружу в точке (b и b ‘), как показано на рисунке выше, из-за этого выпуклости эффективная площадь воздушного зазора увеличивается и плотность потока воздуха разрыв уменьшается.Этот эффект известен как Fringing.
Окаймление прямо пропорционально длине воздушного зазора, что означает, что если длина увеличивается, то эффект окантовки также будет больше, и наоборот.
,FLUX Defense
Сражайся как американец.
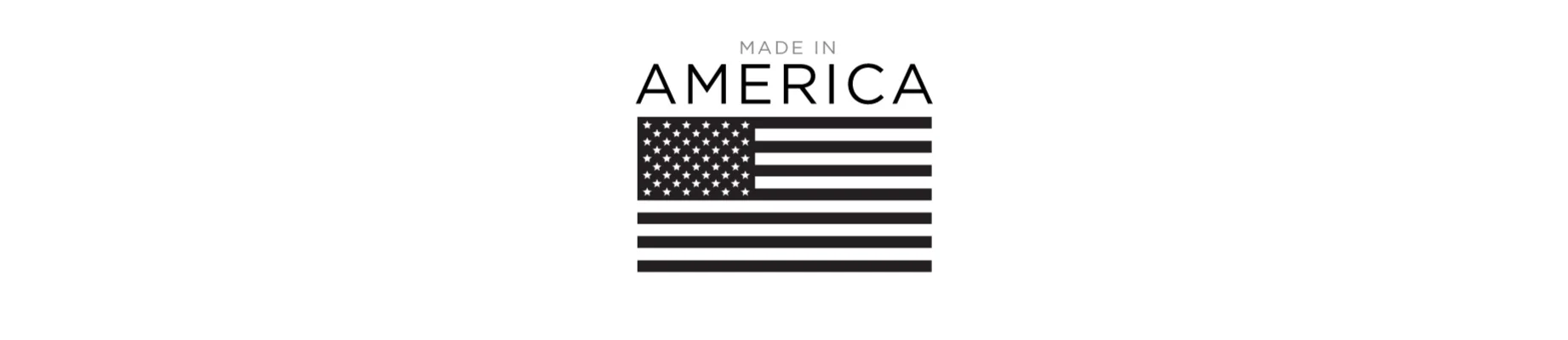
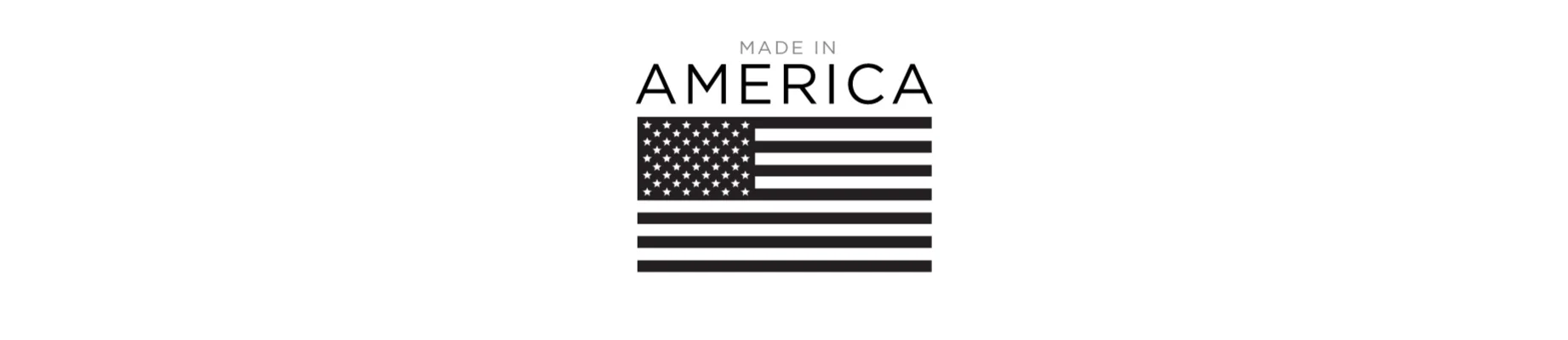
часов
Пн 9 утра — 5 вечера
Вт 9 утра — 5 вечера
Ср 9:00 — 17:00
Четверг 9:00 — 17:00
Пт 9 утра — 5 вечера
Сб 9.00 — 17.00
Солнце закрыто
,