Пайка и ремонт BGA: инструменты, материалы, приспособления
Отличительной особенностью электронных технологий последнего времени является всё большее уплотнение монтажа компонентов и микросхем, что стало причиной появления корпусов типа BGA (англ. Ball grid array — массив шариков). Этот самый массив находится под корпусом микросхемы, что позволяет разместить большое количество выводов в малом объеме (корпуса).
Подобная микроминиатюризация зачастую оборачивается известными неудобствами, вызванными сложностью ремонта (пайки) элементов, размещённых в таком корпусе.
При их пайке обрабатывается сразу несколько контактных ножек и площадок, располагаемых под нижней частью цифрового контроллера или небольшого по размерам чипа. Действовать с ними следует очень аккуратно, пайка требует специализированного оборудования, навыков, знания технологий и профессионализма.
Технология ремонта BGA
Пайка BGA микросхем или реболлинг (reballing) – это процесс восстановления массива из шариков на нижней площадке платы. У нас данный термин не очень прижился и сами специалисты этот процесс ремонта называют просто «перекаткой» контактных шариков. Необходимость в этой процедуре возникает в случаях, когда требуется заменить сгоревшую микросхему, предварительно выпаяв её с посадочного места. Саму процедуру можно разделить на основные этапы:
- демонтаж неисправного микроэлемента после предварительного нагрева;
- очистка несущей платы от остатков старого припоя;
- накатывание новых контактных выводов;
- установка компонента на место.
Следует отметить, что качество пайки значительно отличается при работе на профессиональных паяльных станциях и в домашних условиях на кустарных приспособлениях. К тому же, BGA пайка требует опыта, знания элементной базы, хорошего глазомера и качественных расходных элементов. Имея профессиональную станцию, ремонт станет значительно проще и пройдет в полуавтоматическом режиме.
Для работы с BGA чипами потребуются следующие инструменты, материалы и приспособления:
- паяльная станция с термофеном;
- удобный пинцет;
- специальная паяльная паста и фирменный флюс;
- нужный трафарет для нанесения паяльной пасты;
- липкая лента или экранная оплётка для удаления припоя;
Порядок действий
- Для качественной пайки BGA-корпусов очень важна предварительная подготовка посадочного места (его ещё называют «рабочей областью»). Ремонтируемая плата помещается на горизонтальную платформу, имеющую нижний подогрев инфракрасным излучателем локального действия. Этот излучатель направляется на отпаиваемый BGA чип. При нижнем нагреве станция следит за температурой. Она не должна превышать 200°С, так как требуется только подогрев припоя для облегчения демонтажа элемента. Сверху нагрев осуществляется горячим воздухом целенаправленного действия. Обычно для чипов средних размеров температуру выставляют в пределах 330–360°С.
- После этого можно производить демонтаж микросхемы. Для этого используется «подъемник» чипа, который входит в комплект станции. Данное приспособление необходимо для отделения ремонтируемой микросхемы от печатной платы. Этап очень ответственный. При недостаточном нагреве существует риск оборвать дорожки.
- Следующим этапом необходимо очистить электронную плату и чип от остатков припоя. Здесь очень важно не испортить паяльную маску, в противном случае возможно растекание припоя по дорожкам. Для удаления используется паяльник с насадкой типа «волна». Его использование эффективно и позволяет добиться максимально качественного результата.
- Далее технология BGA пайки предусматривает накатывание новых контактных выводов на чипе. Возможно применение готовых шаров. Но зачастую контактная площадка состоит из сотни выводов. Поэтому в промышленном случае используются специализированные трафаретные площадки, в которых закрепляется микросхема. При реболлинге важный элемент – высококачественная паяльная паста. Такие экземпляры при нагревании дают ровный и гладкий шарик. А некачественные пасты распадаются на большое количество мелких шариков.
- Заключительная процедура пайки BGA микросхемы — установка ее на место. Элемент устанавливается, исходя из шелкографии, нанесенной на саму плату или монтажных меток. Затем микросхема прогревается горячим воздухом и за счет сил поверхностного натяжения от действия расплавленного припоя фиксируется на первоначальном участке демонтажа, занимая «удобную позицию».
Подробнее об особенностях BGA монтажа читайте:
BGA-пайка корпусов в домашних условиях
В современной электронике наблюдается устойчивая тенденция к тому, что монтаж становится всё более уплотненным. Следствием этого стало возникновение корпусов BGA. Пайка этих конструкций в домашних условиях и будет нами рассмотрена в рамках данной статьи.
Общая информация
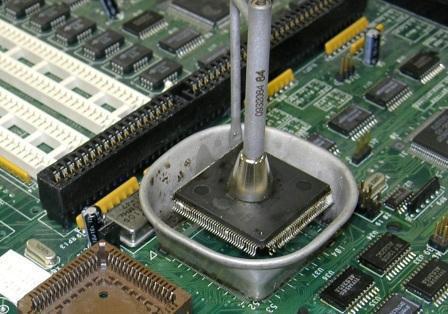
Что нужно для работы?
Необходимо запастись:
- Паяльной станцией, где есть термофен.
- Пинцетом.
- Паяльной пастой.
- Изолентой.
- Оплеткой для снятия припоя.
- Флюс (желательно сосновый).
- Трафарет (чтобы наносить паяльную пасту на микросхему) или шпатель (но остановиться лучше на первом варианте).
Пайка BGA-корпусов не является сложным делом. Но чтобы она успешно осуществлялась, необходимо провести подготовку рабочей области. Также для возможности повторения описанных в статье действий необходимо рассказать про особенности. Тогда технология пайки микросхем в корпусе BGA не составит труда (при наличии понимания процесса).
Особенности
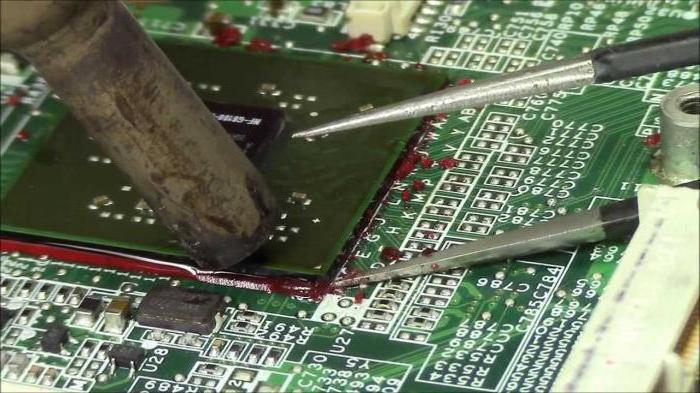
Подготовка
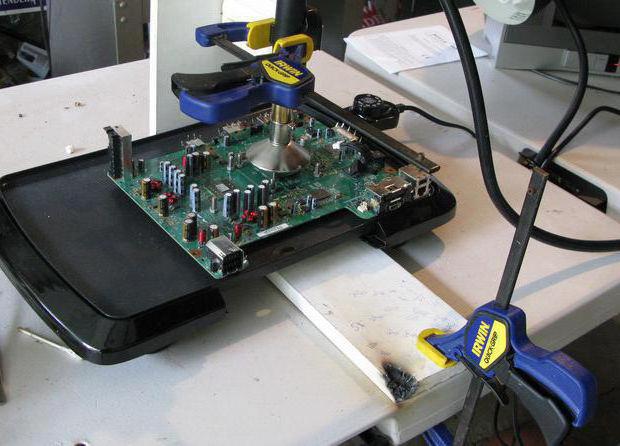
Очистка
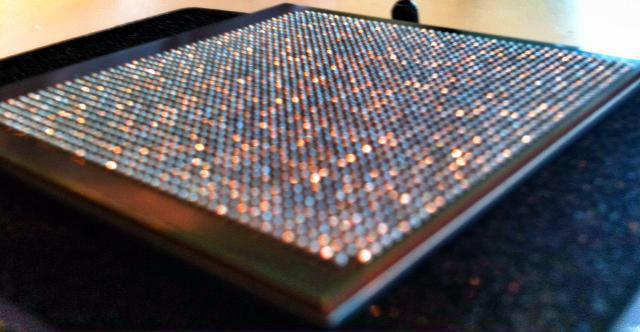
Накатка новых шаров
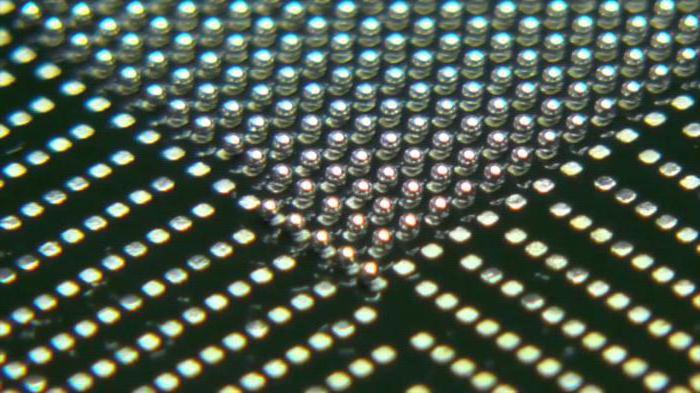
Можно применять уже подготовленные заготовки. Их в таком случае необходимо просто разложить по контактным площадкам и расплавить. Но такое подходит только при небольшом количестве выводов (можете себе представить микросхему с 250 «ножками»?). Поэтому в качестве более легкого способа используется трафаретная технология. Благодаря ей работа ведётся быстрее и с таким же качеством. Важным здесь является использование качественной паяльной пасты. Она сразу же будет превращаться в блестящий гладкий шарик. Некачественный экземпляр же распадётся на большое количество мелких круглых «осколков». И в этом случае даже не факт, что нагрев до 400 градусов тепла и смешивание с флюсом смогут помочь. Для удобства работы микросхему закрепляют в трафарете. Затем с использованием шпателя наносится паяльная паста (хотя можно использовать и свой палец). Затем, поддерживая трафарет пинцетом, необходимо расплавить пасту. Температура фена не должна превышать 300 градусов Цельсия. При этом само устройство должно находиться перпендикулярно пасте. Трафарет следует поддерживать, пока припой полностью не застынет. После этого можно снять крепежную изолирующую ленту и феном, который будет подогревать воздух до 150 градусов Цельсия, аккуратно его нагреть, пока не начнёт плавиться флюс. После этого можно отсоединять от трафарета микросхему. В конечном результате будут получены ровные шарики. Микросхема же является полностью готовой для того, чтобы установить её на плату. Как видите, пайка BGA-корпусов не сложна и в домашних условиях.
Крепёж
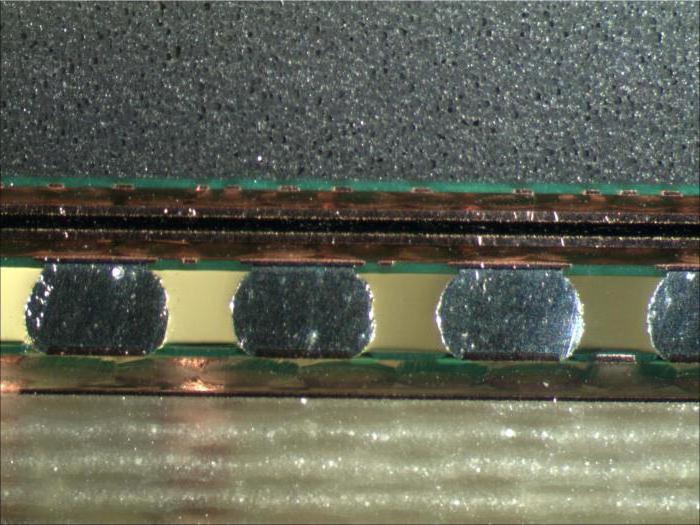
- Переверните микросхему так, чтобы она была выводами вверх.
- Приложите краем к пятакам таким образом, чтобы они совпадали с шарами.
- Фиксируем, где должны находиться края микросхемы (для этого можно нанести небольшие царапинки иголкой).
- Закрепляем сначала одну сторону, затем перпендикулярную ей. Таким образом, достаточно будет двух царапин.
- Ставим микросхему по обозначениям и стараемся шарами на ощупь поймать пятаки на максимальной высоте.
- Следует прогреть рабочую область, пока припой не будет в расплавленном состоянии. Если предыдущие пункты исполнялись точно, то микросхема должна без проблем стать на своё место. Ей в этом поможет сила поверхностного натяжения, которой обладает припой. При этом необходимо наносить совсем немножко флюса.
Заключение
Вот это всё и называется «технология пайки микросхем в корпусе BGA». Следует отметить, что здесь применяется не привычный большинству радиолюбителей паяльник, а фен. Но, несмотря на это, BGA-пайка показывает хороший результат. Поэтому ею продолжают пользовать и делают это весьма успешно. Хотя новое всегда отпугивало многих, но с практическим опытом эта технология становится привычным инструментом.
Выбираем лучший флюс для пайки BGA (Ball grid array) чипов.
В данной статье мы попытаемся ответить на вопросы, связанные с подбором паяльного флюса в случае пайки интегральных BGA микросхем и их реболлинга (накатки шариковых выводов).
О BGA микросхемах
Использование корпусов с выводами в виде шариков, вместо привычных пинов, в настоящее время стало безальтернативным в микро и радиоэлектронике.
Чип с выводами BGA
Из основных преимуществ в использовании микросхем данной конфигурации, отметим:
- экономию места на плате;
- малые наводки;
- теплопроводность, за исключением элементов материнских плат и видеокарт компьютеров.
Из недостатков выделяют: негибкость выводов, сложность установки и необходимость дополнительного рентген контроля после монтажа данных микросхем.
Требования к флюсу при пайке bga
Основной задачей данного паяльного материала в процессе пайки, в частности, bga элементов — это удаление оксидов металлов и оксидных плёнок на этапе подготовки участка пайки.
Качественный флюс должен обеспечивать лучшее растекание припоя (снижение поверхностного натяжения) и предотвращать повторное окисление подготовленной поверхности.
Рабочая температура флюса должна быть ниже, чем температура плавления припоя, из которого состоят выводы микросхемы.
В случае использования чипа с оловянно-свинцовыми выводами, ликвидус (температура полного расплавления) в большинстве своём начинается от 179ºC.
Паяльный флюс нанесённый на плату
Флюс же должен начать работать при температуре на порядок ниже. Чтобы во время полного расплавления припоя с участка пайки были удалены все оксиды.
К принципиальным требованиям стоит добавить и то, что флюс не должен закипать и выделять канцерогенных испарений.
Лёгкое удаление остатков флюса или отсутствие необходимости в отмывке — свойство которое специалисты считают “must have”, в последнее время, при пайке микросхем с шариковыми выводами.
В идеале флюс должен полностью испаряться к моменту пайки микросхемы, в крайнем случае быть диэлектриком и химически инертным по своему составу.
В случае реболлинга требования к лёгкости смытия обычно менее строгие, поскольку смыть флюс с помощью отмывочной жидкости гораздо легче, при открытом доступе к месту пайки.
Примеры флюсов предназначенные для пайки чипов BGA
Как же выбрать паяльный флюс для монтажа и реболлинга bga микросхем? Ниже мы приведём примеры материалов, которые отвечают большинству характеристик перечисленных в статье. А также прошли испытания в боевом режиме и на практике доказали свою пригодность.
Флюс KOKI TF-M955 (NO-CLEAN) «Классический»
Высококачественный флюс для ремонта и пайки. Имеет прозрачные остатки, не мешающие контролю качества. Не содержит галогенов. Для дозаторов или нанесения кисточкой.
Представляет собой желтоватую пасту с вязкостью — 6600±10 % мПа.с. Заявленный срок хранения без потери свойств — 12 месяцев при температуре ниже 10ºС.
Флюс KOKI TF-A254 (NO-CLEAN) «Легко отмывной»
Клейкий флюс TF-A254 незаменим при пайке и реболлинге BGA микросхем в телефонах, ноутбуках и других электронно-цифровых приборах, а также при работе с другими SMD-компонентами.
Флюс TF-A254 необходимо отмывать с использованием отмывочных жидкостей. Рекомендуется Vigon®.
Уникальные технологические свойства флюса TF-A254 позволяют осуществлять пайку даже в условиях, когда предварительный прогрев был коротким, ввиду чего требуемый уровень нагрева не был достигнут.
Надеемся нам удалось осветить все наиболее важные нюансы при выборе флюса при пайке BGA корпусов. Отметим, что в настоящее время все большую популярность и востребованность набирает технология microBGA. Где расстояние между выводами ещё меньше и требования к флюсам, так же как и к другим паяльным материалам, будут выше.
Вы всегда можете проконсультироваться при подборе флюса для решения задач Вашего производства, позвонив по телефону
8 (495) 135-13-11.
Технологии — корпуса BGA-типа, пластик и космос / Habr
В обсуждениях к предыдущей статье proton17 написал, что в космос обычные BGA не летают, дав ссылки на корпуса CCGA-типа как образец надёжности. Я решил разобраться в этом вопросе и нашёл много интересной информации (во многом благодаря вот этому ↓ человеку).Вопрос применимости BGA-компонентов в надёжных приложения не является новым, ещё в 1995 году JPL проводила исследования их надёжности в различных условиях. Результаты работ были последовательно представлены в многочисленных публикациях настоящего гуру этой темы, Р. Джафэриана [1-5]. Сначала керамические и «обычные» пластиковые корпуса исследовались на плоскостность поверхности с помощью лазерного сканирования. За меру плоскостности была выбрана разница между самым низким и самым высоким шариком. Чем меньше эта разница, тем меньше вероятность дефектов при пайке. Керамические корпуса обладали большей плоскостностью, она также улучшалась с уменьшением количества выводов. Этот параметр тем более критичен, чем более высокотемпературный припой используется при пайке. Второй этап – монтаж на печатные платы (FR-4 и полиимид) и термоциклирование. Электрические соединения на плате и внутри тестового BGA-корпуса были организованы таким образом, чтобы образовать несколько групп последовательных соединений (англ. daisy chain). В каждой из этих групп контролировалось наличие нарушения соединений по критерию превышения сопротивления в 1 кОм на более чем 1 мкс. Данный критерий определён в IPC-SM-785, однако он не является достаточным, так как даже полностью треснувшее соединение может не выходить за указанное пороговое значение из-за поджима контакта за счёт соседних выводов [4].
Из-за большой разницы КТР керамики и FR-4/полиимида CBGA-корпуса давали сбой раньше, чем пластиковые. Также более ранние сбои показывали пластиковые корпуса с полным заполнением массива выводов, в отличие от корпусов с периферическим заполнением, так как под кристаллом возникает локальный рост несоответствия КТР корпуса и платы и именно там возникали первые сбои в соединениях.
Среди результатов отмечается влияние температуры стеклования материала печатной платы на надёжность для расширенного температурного диапазона. FR-4 показывал в среднем более слабые результаты, чем полиамид. Подтверждение данного результата есть и в статье [6]: использование печатной платы FR-5 (с Tg ~ 170 oC и КТР ~ 13 ∙ 10−6 K−1) обеспечивает четырёхкратное увеличение надёжности по сравнению обычным FR-4 для корпуса SON-типа.
Стоит отметить, что КТР печатной платы может отличаться даже в пределах платы и зависит от её топологии. В статье [6] приводится широкий диапазон значений от 12 до 24 ∙ 10−6 K−1. Там же есть интересные данные (таблица 1) по зависимости надёжности PBGA от диаметра шарика, контактных площадок (КП) на плате (NSMD-типа) и основании микросхемы (SMD-типа). Их анализ выявляет следующие закономерности:
- Увеличение диаметра шарика при прочих равных увеличивало количество выдерживаемых термоциклов на ~20-30%.
- Увеличение диаметра КП только на стороне печатной платы снижает надёжность, так как уменьшается высота шарика. Однако при одновременном увеличении диаметра площадки на основании PBGA потери надёжности, связанные с уменьшением высоты, компенсируются улучшением площади связи, и общий эффект становится положительным.
- Максимальная надёжность была получена, когда диаметр КП на плате был несколько меньше, чем на основании микросхемы. Автор ссылается на аналогичный результат, полученный в другой работе. К сожалению, нет сравнительных для случая с большим диаметром шарика.
В статье [7] экспериментально показано увеличение количества выдерживаемых термоциклов с уменьшением толщины керамического основания корпуса. Ознакомиться с предшествующей статьей одного из авторов с описанием модели процесса мне не удалось, но общие соображения такие: чем тоньше корпус, тем меньше он сопротивляется растягивающей силе, тем меньше нагрузка на выводы.
Скорость смены температуры влияет на преимущественное место возникновения дефектов в соединений – при быстром (когда возникают локальные напряжения) это со стороны корпуса, при медленном (когда система успевает прийти в тепловое равновесие) – со стороны печатной платы. Для расширенного температурного диапазона наибольшее количество отказов керамических корпусов CBGA было в соединении корпуса (63Sn37Pb) и шарика (90Pb10Sn).
- Чем больше корпус и количество выводов, тем меньше надёжность.
- Выводы, максимально удалённые от центра, наиболее уязвимы к разрушению. Для пластиковых BGA-корпусов, кроме того, уязвимы выводы в зоне расположения кристалла
- Керамические корпуса на печатной плате из текстолита показывают низкую надёжность. Кроме того, они не так хорошо выравниваются при пайке (так как обладают большей массой) и более чувствительны к количеству и качеству нанесения паяльной пасты, что усложняет постановку процесс надёжного монтажа компонентов.
Лирическое отступление. Использование печатных плат на основе LTCС-керамики сняло бы проблему несоответствия КТР. Возможно, это одно из направлений развития РЭА для космоса, которое приведёт к снижению стоимости таких печатных плат.
Зачем использовать керамические корпуса? Этого вопроса касался BarsMonster в одной из статей. Про то, что в пластике перемычки поддерживаются по всей длине компаундом, с одной стороны, логично, но с другой несоответствие КТР материалов пластикового корпуса (компаунд, кремний, текстолит, металлическая перемычка) создаёт большое количество проблем в расширенном диапазоне температур. Дополнительными аргументами в сторону использования керамических корпусов являются близкое к кремнию значение КТР, высокая теплопроводность, широкой температурный диапазон (что важно и для процесса сборки), более высокая гидрофобность, более простой в освоении техпроцесс герметизации.
На Spirit и Opportunity использовались именно керамические корпуса, но не CBGA-типа, а CCGA-типа (рис. 1): в них шарики заменены на столбики (иногда армированные медной спиралью), которые способны выдерживать большие нагрузки (вот здесь приводятся данные, что увеличение высоты в 2 раза снижает механическое напряжение и деформации на 30%). Несмотря на то, что эти миссии с успехом выполнили и даже перевыполнили свои задачи, стоит отметить, что производительные процессоры в CCGA-корпусах находились в блоке с контролируемой температурой. В статьях [8, 9] представлено сравнение CCGA и соответствующего ему PBGA в различных условиях. У CCGA-560 после 1075 термоциклов –50/75°C произошло первое разрушение контакта на стороне корпуса (для монтажа использовалось повышенное количество паяльной пасты, что улучшило надёжность соединения на стороне платы, см. рис. 2 и 3), в то время как в PBGA-560 за 2000 циклов сбоев не было обнаружено.
Интересно подумать над тем, почему крайние выводы смещены в сторону центра на стороне платы. КТР печатной платы больше, чем КТР керамики, и тогда это означает, что разрушение происходит на сжатии, в области отрицательных температур. Это меня привело к таким рассуждениям: спайка и фиксация взаимного положения происходит около температуры плавления паяльной пасты, то есть ~183 oC для 63Sn37Pb, поэтому весь диапазон рабочих температур находится в области сжатия печатной платы относительно керамического основания корпуса. И тогда температура нейтральной точки – это не 25 oC, это температура плавления паяльной пасты.
Для того, чтобы уменьшить нагрузку на выводы BGA-корпусов (в том числе в результате воздействий механических факторов), применяется несколько методов: фиксация по углам (англ. corner-staking), компаундирование пространства между корпусом и платой (англ. underfill). Однако результаты испытаний в [9] показывают, что такая технология не только не устраняет проблему, но может, наоборот, только ухудшать устойчивость конструкции к воздействию смены температур (рис. 4).
Испытывался также корпус CCGA-717 с армированными столбиками меньшего диаметра [9]. По сравнению с CCGA-560 с неармированными выводами он показал большую устойчивость к термоциклированию: после 950 циклов -55/100 oC электрических отказов не было, но дефекты на выводах уже начали образовываться (рис. 5). В открытом доступе также есть результаты успешных испытаний CCGA-472 от лаборатории Aeroflex по стандартам NASA.
В статье [5] представлены результаты исследования влияния финишного покрытия печатной платы на надёжность BGA-компонентов. Было отмечено, что для ENIG, в отличие от HASL и OSP, для которых были характерно вязкое разрушение выводов, некоторые выводы демонстрировали хрупкое разрушение выводов. Стандарт IPC-9701A, описывающий методологию испытания надёжности паяных соединений, запрещает использование иных покрытий печатной платы, кроме HASL, OSP и IAg, во избежание влияний интерметаллидов (также, к слову, стандарт рекомендует использовать контактные площадки NSMD-типа с отступом маски). В рамках специальных исследований [10, 11] проблемы использования ENIG в качестве финишного покрытия не удалось обнаружить каких-либо закономерностей и, таким образом, снижение надёжности соединения является трудно предсказуемым событием. Видимо, по этой причине, в стандарте и не рекомендуется использовать такой финиш. К слову, в качестве альтернативного покрытия, среди прочих, рассматривалось покрытие ENEPIG, которое показало хорошие результаты (в оригинале – «performed very well and requires more testing»).
В таблице 2 сведены данные экспериментов по исследованию надёжности компонентов BGA-типа, анализ которых указывает на наличие некоторых закономерностей (например, снижение толщины керамического основания значительно снижает нагрузку на выводы). Эти данные могут выступать лишь как ориентир при проектировании, критерий надёжности – эксперимент для конкретной конструкции и технологии сборки. В конце статьи [9] даются ценные рекомендации по использованию BGA-компонентов на основе обобщения опыта NASA от человека, который занимается надёжностью BGA-компонентов с 1995 года. Вот некоторые тезисы:
- Большинство PBGA-корпусов обеспечивают достаточную надёжность для миссий с ограниченными перепадами температур (например, контролируемая температура в корпусе модуля). При большой длительности миссии корпуса с большим количеством выводов (более 500) должны подвергаться испытаниям.
- Керамические BGA-корпуса с небольшим количеством выводов (менее 400) могут удовлетворять требованиям надёжности для краткосрочных миссий с ограниченными перепадами температур, но для долгосрочных миссий должны проходить квалификационные испытания даже в случае пониженных требований к перепаду температур. Для корпусов с большим количеством выводов (более 500) необходимы испытания во всех случаях.
- Использование компаунда типа «underfill» не рекомендуется для CCGA из-за высокого зазора между корпусом и печатной платой. В случае же использования, КТР компаунда должен быть близким к КТР печатной платы (нагрузки в плоскости) и выводов (нагрузки в направлении оси Z), кроме того необходимы индивидуальные испытания для каждого случая применения.
- В случае необходимости повышения устойчивости к механическим воздействиям фиксация по углам (англ. corner staking, edge bonding) более предпочтительна для CCGA- и CBGA-корпусов по сравнению с технологией «underfill». Однако и тут можно ухудшить надёжность неправильно подобранными материалами.
Есть и другие данные: в одной из презентаций JAXA говорится, что его использование для CBGA-корпусов увеличивает количество циклов до возникновения сбоя в среднем в 1,7 раз. Чаще всего компаунды типа «underfill» применяется в корпусах CSP-типа, где основная задача – в габаритах, максимально близких к размеру кристалла, обеспечить переход между низким КТР кремния и КТР печатной платы. Для BGA-компонентов, как уже было сказано, необходимо проведение испытаний в каждом конкретном случае (без возможности переноса результатов даже при изменении одного из параметров, в том числе технологического) в соответствии с моделью внешних воздействующих факторов.
Какое количество термоциклов должен выдерживать корпус? Безусловно, это зависит от модели воздействующих факторов. При оптимизированной технологии сборки обобщенному критерию надёжности в отсутствии отказов в течение 500 циклов -60/125 оС удовлетворяют многие типы корпусов (см. таблицу 2). Однако «не термоциклированием единым», корпус не должен накапливать влагу, должен обеспечивать низкое тепловое сопротивление, должен обеспечивать стойкость к механическим воздействующим факторам и т.д. И по полному списку критериев у керамических корпусов надёжность статистически выше. Производители ЭКБ для космической аппаратуры, такие как Aeroflex и MSK, выпускают свои микросхемы именно в керамических и металлостеклянных корпусах. Да, для исполнения BGA-типа монтаж на текстолитовые печатные платы создаёт проблемы из-за несоответствия КТР, поэтому приходится изобретать способы повышения надёжности соединений – снижение толщины основания, использование столбиковых выводов, компаундирование и т.д.
Важно понимать, что дело не в технологии корпусирования в общем, а в том, соответствует ли конкретная микросхема требованиям надёжности и стойкости к воздействующим факторам. Можно использовать и коммерческую микросхему в пластиковом корпусе, если она пройдёт полный цикл испытаний. При этом успешные испытания не будут означать, что «такая же» микросхема с другого завода-изготовителя или даже из другой партии будет удовлетворять требованиям надёжности. В этом отличие надёжной ЭКБ, которое и заложено в цене — изготовитель берёт на себя затраты на испытания. Тот же 3D PLUS проводит отбор микросхем в пластике для некоторых своих микросборок, но стоят такие изделия уже на порядок дороже. Другой путь — это выполнение испытаний и отбора на стороне потребителя. Это может быть оправдано, если нужная функциональность не реализована в надёжном исполнении, или если если модель внешних воздействий и требования надёжности для целевой миссии значительно ниже, чем типовые на рынке надёжной ЭКБ.
Запрос на снижение массы космических аппаратов (прежде всего, развитие малоразмерных КА) толкает производителей выпускать надёжные ЭКБ в пластиковых корпусов, на рынке уже есть решения (кроме того, они заявляются и как бюджетные). Возможно, в ближайшем будущем количество надёжного, сертифицированного для космоса пластика будет расти, обеспечивая нужды околоземных миссий с низкими орбитами, а керамические корпуса пересядут на LTCC печатные платы для того, чтобы бороздить глубинный космос.
Литература
[1] Reza Ghaffarian, “BGAs for High Reliability Applications”, 1998.
[2] Reza Ghaffarian, “Ball Grid Array Reliability Assessment for Aerospace Applications”, 1997
[3] Reza Ghaffarian, “Reliability and Failure Analyses of Thermally Cycled Ball Grid Array Assemblies”, 1998
[4] Reza Ghaffarian, “Reliability of BGA Packages for Highly Reliable Applications and Chip Scale Package Board Level Reliability”, 1997
[5] Reza Ghaffarian, “Assembly Reliability Of BGAs And Effects Of Boards Finish”, 1998
[6] Jean-Paul Clech, ”Solder Joint Reliability Of CSP Versus BGA Assemblies”, 2000
[7] Raj N.Master, Gregory B. Martin, etc. “Ceramic Ball Grid Array for AMD K6 Microprocessors Applications”, 1998
[8] Reza Ghaffarian, “Effect of Area Array Package Types on Assembly Reliability And Comments on IPC-9701A”, 2005
[9] Reza Ghaffarian, “CCGA packages for space applications», 2006
[10] F.D.Bruce Houghton. “ITRI Project on Electroless Nickel / Immersion Gold Joint Cracking”, 2000
[11] F.D.Bruce Houghton. “Solving the ENIG Black Pad Problem: An ITRI Report on Round 2”, 1999
BGA пайка микросхем
Технология развития радиоэлектроники не стоит на месте и сегодня повсеместно на электронных платах используются BGA компоненты. Но что же из себя представляют эти элементы?
Со времен изобретения радио, электроника стремилась к малым габаритам и размерам. Сначала такие единицы были дискретными, то есть отдельными. Затем электронные компоненты стали собирать по несколько единиц в одни корпус. Это стало зарождением элементных сборок. Технологии постоянно развивались и относительно недавно мир перешел на наноструктуры (10-9 метра), позволяющие объединять огромное количество элементов в один корпус. А именно, миллионы транзисторов, резисторов, диодов, конденсаторов. Но появилась проблема колоссального количества выводов. Решением этого вопроса стала BGA микросхема или в переводе на русский – «массив из шариков». Этот самый массив располагается под корпусом микросхемы, что позволяет разместить большое количество выводов на малом объеме.
Из-за большой плотности расположения элементов на микросхеме и миниатюризации самих электронных компонентов усложнилась и технология BGA пайки. Пайка требует специализированного оборудования, знания технологий и профессионализма.
Технология ремонта
Пайка BGA микросхем или реболлинг (reballing) – это процесс восстановления массива из шариков на нижней площадке платы. В России данный термин не прижился и зачастую специалисты сам процесс ремонта называют «перекаткой» контактных шариков. Саму процедуру можно разделить на основные этапы:
- демонтаж неисправного микроэлемента после предварительного нагрева;
- очистка несущей платы от остатков старого припоя;
- накатывание новых контактных выводов;
- установка компонента на место.
Следует отметить, что качество пайки значительно отличается при работе на профессиональных паяльных станциях и в домашних условиях на кустарных приспособлениях. К тому же, BGA пайка требует обширного опыта работы, знания элементной базы, хорошего глазомера и качественных расходных элементов. Имея профессиональную станцию, ремонт станет значительно проще и пройдет в полуавтоматическом режиме.
Раскроем каждый шаг более подробно. Ремонтируемая плата помещается на горизонтальную платформу, имеющую нижний подогрев инфракрасным излучателем локального действия. Этот излучатель направляется на отпаиваемый BGA чип. При нижнем нагреве станция следит за температурой. Она не должна превышать 200 0С. Так как требуется только подогрев припоя, для облегчения демонтажа элемента. Сверху нагрев осуществляется горячим воздухом целенаправленного действия. Обычно температуру выставляют в пределах 330–360 0С для чипов средних размеров. Процедура занимает около минуты. Нагрев осуществляется по краям платы, исключая центр микросхемы. Это требуется для предотвращения перегрева кристалла. Следует учитывать время и интенсивность обработки микросхемы воздухом. Так как компоновка элементов очень плотная, то существует вероятность перегреть соседние элементы. Для этого их укрывают специальной защитной пленкой.
После этого происходит демонтаж микросхемы. Для этого используется «подъемник» чипа, который входит в комплект станции. Данное приспособление необходимо для отделения ремонтируемой микросхемы от печатной платы. Этап очень ответственный. При недостаточном нагреве существует риск оторвать дорожки.
Следующим этапом необходимо очистить электронную плату и чип от остатков припоя после пайки BGA микросхемы. Здесь очень важно не испортить паяльную маску, в противном случае возможно растекание припоя по дорожкам. Для удаления используется паяльник с насадкой типа «волна». Его использование эффективно, и позволяет добиться максимально качественного результата.
Далее технология BGA пайки предусматривает накатывание новых контактных выводов на чипе. Возможно применение готовых шаров. Но зачастую контактная площадка состоит из сотни выводов. Поэтому в промышленном случае используются специализированные трафаретные площадки, в которых закрепляется микросхема. При реболлинге важный элемент – высококачественная паяльная паста. Такие экземпляры при нагревании дают ровный и гладкий шарик. А некачественные пасты распадаются на большое количество мелких шариков.
Заключительной процедурой пайки BGA микросхемы является установка на место. Элемент устанавливается, исходя из шелкографии, нанесенной на саму плату или монтажных рисок. Затем микросхема прогревается горячим воздухом и за счет сил поверхностного натяжения от действия расплавленного припоя фиксируется на первоначальном участке демонтажа. По этой причине схема немного шевелится, занимая «удобную позицию».
На этом ремонтные процедуры завершены. Плата промывается аэрозолю flux-off и проверяется на работоспособность.
Компания «ЛионТех» реализует промышленные станции для пайки BGA компонентов и предлагает клиентам комплексное решение для ремонта любой сложности. Пример такого оборудования по ссылке http://liontech.ru/catalog/oborudovanie-dlya-proizvodstva-elektroniki/instrumenty-dlya-payki/. На сайте Вы можете оставить интересующий Вас вопрос и наши специалисты с удовольствием ответят на него или получить дополнительную консультацию по телефону +7(812) 309-27-37 или 8-800 555-68-89 (звонок по России бесплатный).