Пайка bga микросхем: подробная инструкция
Пайка bga микросхем
Выпаивание чипаУдаление компаунда
Последовательность демонтажа
Пайка bga чипов
Нижний подогрев для пайки bga
Флюс для пайки bga
Термовоздушная паяльная станция
Паяльник для пайки
Микроскоп бинокулярный
Шарики bga
Качество пайки
Пайка bga микросхем
Как паять платы? Как расшифровывается BGA? На эти два часто задаваемых вопроса, во время прохождения курсов пайки, отвечают мастера Bgacenter. От английского – ball grid arrey, то есть массив шариков, своим видом похожий на сетку. Шарики из припоя наносятся на микросхему через трафарет, затем потоком горячего воздуха, расплавляется сам припой и формируются контакты правильной формы.
Процесс пайки BGA состоит из определенной последовательности действий, соблюдая которую получаем качественное соединение. Но существует большое количество нюансов, ради которых и приезжают на обучение.
Начиная с того под каким углом и на каком расстоянии от платы держать сопло фена, температурные режимы демонтажа и монтажа микросхем, с какой стороны заводить лопатку. А при проведении диагностики, и наличии межслойного короткого замыкания ничего не нагревается.
Как в этом случае найти неисправный элемент или цепь? И много других тонкостей которые может знать действующий мастер сервисного центра. И тот кто может подтвердить свой уровень выполненными ремонтами.
Ремонт iPhone в Bgacenter
Выпаивание чипа
90 % успешности ремонта зависит от правильно выполненного демонтажа микросхем. Именно на этом этапе важно не оторвать пятаки и не повредить микросхему высокой температурой. А начинают выпаивание чипа, с удаления компаунда.
Удаление компаунда
Компаунд – полимерная смола, обычно черного или коричневого цвета, применяемая при изготовлении системных плат телефонов. Назначение компаунда:
- Дополнительная фиксация радио компонентов и bga микросхем на плате
- Защита не изолированных контактов от попадания влаги
- Повышение прочности платы
Наиболее ответственные микросхемы, такие как: CPU, BB_RF, EPROM, NAND Flash, Wi-Fi в заводских условиях после установки, заливаются компаундом. И перед тем как выполнять демонтаж, необходимо очистить периметр от смолы.
Снятие компаунда
Последовательность демонтажа
- Внимательно осмотреть плату, на предмет ранее выполнявшихся ремонтов.
- Выполнить диагностику, произвести необходимые измерения.
- Подготовить плату к пайке, удалить защитные экраны, наклейки. Отключить и убрать коаксиальный кабель.
- Закрепить motherboard в соответствующем держателе.
- Удалить компаунд вокруг демонтируемого чипа. Температура на фене при этом 210 – 240 градусов Цельсия.
- Установить теплоотводы. Место установки теплоотводов зависит от месторасположения выпаиваемой микросхемы.
- Феном прогреть плату в течение нескольких секунд. Тем самым повышаем температуру платы, для того чтобы флюс растекался равномерно.
- Для выпаивания чипа, нанести флюс Martin, или любой другой безотмывочный флюс, на поверхность микросхемы.
- Направить поток горячего воздуха на выпаиваемый элемент. Температура при демонтаже 340 градусов Цельсия. Как понять, что припой расплавился и настало время убирать микросхему с платы? Для этого существует несколько способов:
- Отслеживать время по секундомеру.
- Отсчитывать секунды про себя.
- “Толкать” зондом или пинцетом саму микросхему или рядом расположенную обвязку (конденсаторы, резисторы или катушки). Как только отпаиваемый чип начнет сдвигаться, на доли миллиметра, настало время заводить лопатку под или воспользоваться пинцетом.
- Подготовить контактную площадку. Для этого:
- специальной лопаткой убрать остатки компаунда;
- залудить сплавом Розе (температура плавления 94 градуса Цельсия) все без исключения контакты;
- оплеткой собрать остатки припоя с рабочей поверхности;
- после остывания motherboard до комнатной температуры, отмыть контактную площадку спиртом, БР-2 или DEAGREASER.
- Для изменения состава заводского припоя могут использоваться легкоплавкие (низкотемпературные припои)
- Плата подготовлена для установки исправной микросхемы.
Пайка bga чипов
Общий принцип пайки следующий, благодаря создаваемому поверхностному натяжению при расплавлении припоя, происходит фиксация микросхемы относительно контактной площадки на системной плате. Температура пайки bga микросхем на платах iPhone 290 – 340 градусов Цельсия.
Подготовка микросхемы:
- Специальным ножом очистить компаунд.
- Медной оплеткой 1 или 2 мм (зависит от геометрических размеров чипа) удалить остатки припоя.
- Восстановить шариковые выводы. Существует два способа формирования выводов:
- Паста bga через трафарет наносится на поверхность микросхемы (приоритетный метод) Используется в большинстве случаев.
- Вручную, шариками BGA. Этот вариант подходит для чипов с малым количеством выводов, до 50.
Хотя несколько лет назад, когда качество трафаретов оставляло желать лучшего) модемы на iPhone 5S накатывались вручную. То есть каждый шарик, зондом или пинцетом, устанавливался отдельно. А это 383 контакта, посчитали в ZXW. Если при распределении шариков на микросхеме присоединенной к трафарету, шары не фиксируются в отверстиях трафарета; это значит нанесено не достаточное количество флюса на микросхему.
- Если работаем с пастой, обязательно после того как убрали трафарет, термовоздушной станцией прогреть микросхему, для формирования контактов правильной формы. Дополнительно для этих целей может использоваться мелкозернистая наждачная бумага, Р500 ГОСТ Р 52381-2005.
- Спиртом и зубной щеткой очистить микросхему.
- Припаять чип на контактную площадку, установив его по ключу и зазорам.
- При установки новой микросхемы (приобретенной у поставщика), обязательная процедура – перекатать чип на свинец содержащий припой. Это необходимо, для понижения температуры плавления припоя и уменьшения времени воздействия на плату высокой температурой.
Нижний подогрев для пайки bga
Для уменьшения времени воздействия на плату высоких температур используется подогревать плат. Рекомендуем моноблочный подогреватель печатных плат СТМ 10-6. Стабильное поддержание заданной температуры на всей площади нагревательного элемента способствует равномерному прогреву всей motherboard (зависит от модели подогревателя). И ещё одно из преимуществ перед другими термостолами, это удобная универсальная система креплений.
Термостол СТМ 10-6
Флюс для пайки bga
В интернете представлено огромное количество производителей флюсов. В Bgacenter применяется профессиональный безотмывочный флюс Martin. Следует обращать внимание на дату изготовления и срок годности флюса. Преимущества флюс-геля:
- безотмывочный (мы рекомендуем всё равно отмывать)
- удобный дозатор, отсюда высокая точность дозирования во время паяльных работ
- не выделяет неприятных запахов
- обеспечивает хорошее растекание припоя по основному металлу
Флюс Martin
Термовоздушная паяльная станция
Назначение станции Quick 861DE ESD Lead – пайка (демонтаж и монтаж) BGA микросхем и SMD компонентов. Преимущества этой станции:
- три режима памяти СН1, СН2, СН3;
- высокая производительность “по воздуху”, Quick 861DE подойдет для пайки плат и телефонов и ноутбуков;
- стабильность температуры.
Что бы можно улучшить в конструкции станции, это регулировка температуры не кнопками, а вращающимися регуляторами, как на Quick 857D (W)+.
Quick 861DE ESD Lead
Паяльник для пайки
PS-900 METCAL – индукционная паяльная система. Мощности паяльника 60 Вт вполне достаточно для работы с многослойными платами современной электроники. Опыт работы инженеров по ремонту телефонов именно с этим паяльником – 4 года. Какие отличительные особенности у PS-900:
- нет необходимости в калибровке,
- большой выбор наконечников,
- надежность станции, расходным материалом является индуктор. При ежедневной интенсивной пайке, замена индуктора в среднем 1 раз в 10 месяцев.
Паяльник индукционный
Микроскоп бинокулярный
Для начинающего мастера по ремонту телефонов хорошим вариантом будет микроскоп СМ0745. Бинокулярный микроскоп с фокусным расстоянием 145 мм (при установке рассеивающей линзы). Назначение системы линз, увеличение фокусного расстояния при сохранении рабочей зоны.
Преимущество СМ0745:
- Плавное увеличение, достигается использованием кремальеры.
- Линзовая система изготовлена из стекла, а не из пластика.
- Возможность укомплектовать голову микроскопа разными столиками и штативами.
- Увеличение до 45Х.
Микроскоп для пайки плат
Шарики bga
Для пайки плат iPhone в основном применяются шарики припоя диаметр 0,2 мм. Обычно поставляются в стеклянной таре, по 10000 шаров в каждой банке.
Состав шариков из припоя:
- олово 63%,
- свинец 37%.
Шарики bga
Качество пайки
После выполнения паяльных работ необходимо убедиться, что пайка bga выполнена качественно. Контроль осуществляется несколькими способами:
- Визуальный.
- Измерительный.
- Включением устройства.
- Подключением к ноутбуку и проверке в 3uTools.
Подробно о методиках проверки, читайте в следующем материале. Например при диагностике цепи заряда iPad Air, подключением платы к ЛБП, при исправном TRISTAR потребление тока должно быть не более 0,07 Ампер.
Технологии — корпуса BGA-типа, пластик и космос / Хабр
В обсуждениях к предыдущей статье proton17 написал, что в космос обычные BGA не летают, дав ссылки на корпуса CCGA-типа как образец надёжности. Я решил разобраться в этом вопросе и нашёл много интересной информации (во многом благодаря вот этому ↓ человеку).Несмотря на свои преимущества (максимальное количество выводов по отношению к габаритам при заданном шаге, низкая индуктивность выводов, самовыравнивание при пайке) корпуса BGA-типа имеют серьезный для надёжных применений недостаток – невозможность достоверного визуального контроля качества паяных соединений.
Вопрос применимости BGA-компонентов в надёжных приложения не является новым, ещё в 1995 году JPL проводила исследования их надёжности в различных условиях. Результаты работ были последовательно представлены в многочисленных публикациях настоящего гуру этой темы, Р. Джафэриана [1-5]. Сначала керамические и «обычные» пластиковые корпуса исследовались на плоскостность поверхности с помощью лазерного сканирования. За меру плоскостности была выбрана разница между самым низким и самым высоким шариком. Чем меньше эта разница, тем меньше вероятность дефектов при пайке. Керамические корпуса обладали большей плоскостностью, она также улучшалась с уменьшением количества выводов. Этот параметр тем более критичен, чем более высокотемпературный припой используется при пайке. Второй этап – монтаж на печатные платы (FR-4 и полиимид) и термоциклирование. Электрические соединения на плате и внутри тестового BGA-корпуса были организованы таким образом, чтобы образовать несколько групп последовательных соединений (англ. daisy chain). В каждой из этих групп контролировалось наличие нарушения соединений по критерию превышения сопротивления в 1 кОм на более чем 1 мкс.
Данный критерий определён в IPC-SM-785, однако он не является достаточным, так как даже полностью треснувшее соединение может не выходить за указанное пороговое значение из-за поджима контакта за счёт соседних выводов [4].
Из-за большой разницы КТР керамики и FR-4/полиимида CBGA-корпуса давали сбой раньше, чем пластиковые. Также более ранние сбои показывали пластиковые корпуса с полным заполнением массива выводов, в отличие от корпусов с периферическим заполнением, так как под кристаллом возникает локальный рост несоответствия КТР корпуса и платы и именно там возникали первые сбои в соединениях.
Среди результатов отмечается влияние температуры стеклования материала печатной платы на надёжность для расширенного температурного диапазона. FR-4 показывал в среднем более слабые результаты, чем полиамид. Подтверждение данного результата есть и в статье [6]: использование печатной платы FR-5 (с Tg ~ 170 oC и КТР ~ 13 ∙ 10−6 K−1) обеспечивает четырёхкратное увеличение надёжности по сравнению обычным FR-4 для корпуса SON-типа.
Стоит отметить, что КТР печатной платы может отличаться даже в пределах платы и зависит от её топологии. В статье [6] приводится широкий диапазон значений от 12 до 24 ∙ 10−6 K−1. Там же есть интересные данные (таблица 1) по зависимости надёжности PBGA от диаметра шарика, контактных площадок (КП) на плате (NSMD-типа) и основании микросхемы (SMD-типа). Их анализ выявляет следующие закономерности:
- Увеличение диаметра шарика при прочих равных увеличивало количество выдерживаемых термоциклов на ~20-30%.
- Увеличение диаметра КП только на стороне печатной платы снижает надёжность, так как уменьшается высота шарика. Однако при одновременном увеличении диаметра площадки на основании PBGA потери надёжности, связанные с уменьшением высоты, компенсируются улучшением площади связи, и общий эффект становится положительным.
- Максимальная надёжность была получена, когда диаметр КП на плате был несколько меньше, чем на основании микросхемы.
Автор ссылается на аналогичный результат, полученный в другой работе. К сожалению, нет сравнительных для случая с большим диаметром шарика.
В статье [7] экспериментально показано увеличение количества выдерживаемых термоциклов с уменьшением толщины керамического основания корпуса. Ознакомиться с предшествующей статьей одного из авторов с описанием модели процесса мне не удалось, но общие соображения такие: чем тоньше корпус, тем меньше он сопротивляется растягивающей силе, тем меньше нагрузка на выводы.
Скорость смены температуры влияет на преимущественное место возникновения дефектов в соединений – при быстром (когда возникают локальные напряжения) это со стороны корпуса, при медленном (когда система успевает прийти в тепловое равновесие) – со стороны печатной платы. Для расширенного температурного диапазона наибольшее количество отказов керамических корпусов CBGA было в соединении корпуса (63Sn37Pb) и шарика (90Pb10Sn).
Итак, основные очевидные закономерности, экспериментально подтверждённые ещё в 1995 году, для надёжности BGA-компонентов определяются тепловым расширением и заключаются в следующем:
- Чем больше корпус и количество выводов, тем меньше надёжность.
- Выводы, максимально удалённые от центра, наиболее уязвимы к разрушению. Для пластиковых BGA-корпусов, кроме того, уязвимы выводы в зоне расположения кристалла
- Керамические корпуса на печатной плате из текстолита показывают низкую надёжность. Кроме того, они не так хорошо выравниваются при пайке (так как обладают большей массой) и более чувствительны к количеству и качеству нанесения паяльной пасты, что усложняет постановку процесс надёжного монтажа компонентов.
Лирическое отступление. Использование печатных плат на основе LTCС-керамики сняло бы проблему несоответствия КТР. Возможно, это одно из направлений развития РЭА для космоса, которое приведёт к снижению стоимости таких печатных плат.Зачем использовать керамические корпуса? Этого вопроса касался BarsMonster в одной из статей. Про то, что в пластике перемычки поддерживаются по всей длине компаундом, с одной стороны, логично, но с другой несоответствие КТР материалов пластикового корпуса (компаунд, кремний, текстолит, металлическая перемычка) создаёт большое количество проблем в расширенном диапазоне температур.

На Spirit и Opportunity использовались именно керамические корпуса, но не CBGA-типа, а CCGA-типа (рис. 1): в них шарики заменены на столбики (иногда армированные медной спиралью), которые способны выдерживать большие нагрузки (вот здесь приводятся данные, что увеличение высоты в 2 раза снижает механическое напряжение и деформации на 30%). Несмотря на то, что эти миссии с успехом выполнили и даже перевыполнили свои задачи, стоит отметить, что производительные процессоры в CCGA-корпусах находились в блоке с контролируемой температурой. В статьях [8, 9] представлено сравнение CCGA и соответствующего ему PBGA в различных условиях. У CCGA-560 после 1075 термоциклов –50/75°C произошло первое разрушение контакта на стороне корпуса (для монтажа использовалось повышенное количество паяльной пасты, что улучшило надёжность соединения на стороне платы, см. рис. 2 и 3), в то время как в PBGA-560 за 2000 циклов сбоев не было обнаружено.
Интересно подумать над тем, почему крайние выводы смещены в сторону центра на стороне платы. КТР печатной платы больше, чем КТР керамики, и тогда это означает, что разрушение происходит на сжатии, в области отрицательных температур. Это меня привело к таким рассуждениям: спайка и фиксация взаимного положения происходит около температуры плавления паяльной пасты, то есть ~183 oC для 63Sn37Pb, поэтому весь диапазон рабочих температур находится в области сжатия печатной платы относительно керамического основания корпуса. И тогда температура нейтральной точки – это не 25 oC, это температура плавления паяльной пасты.
Для того, чтобы уменьшить нагрузку на выводы BGA-корпусов (в том числе в результате воздействий механических факторов), применяется несколько методов: фиксация по углам (англ. corner-staking), компаундирование пространства между корпусом и платой (англ. underfill). Однако результаты испытаний в [9] показывают, что такая технология не только не устраняет проблему, но может, наоборот, только ухудшать устойчивость конструкции к воздействию смены температур (рис. 4).
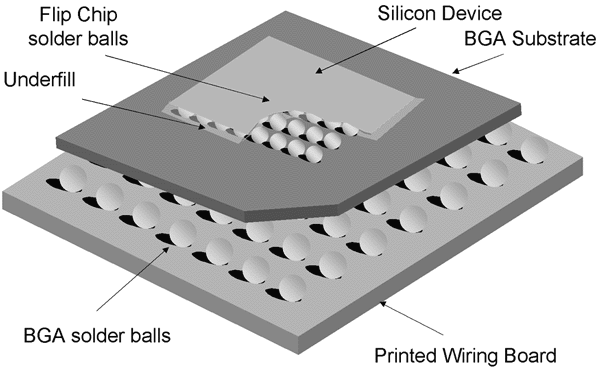
В таблице 2 сведены данные экспериментов по исследованию надёжности компонентов BGA-типа, анализ которых указывает на наличие некоторых закономерностей (например, снижение толщины керамического основания значительно снижает нагрузку на выводы). Эти данные могут выступать лишь как ориентир при проектировании, критерий надёжности – эксперимент для конкретной конструкции и технологии сборки. В конце статьи [9] даются ценные рекомендации по использованию BGA-компонентов на основе обобщения опыта NASA от человека, который занимается надёжностью BGA-компонентов с 1995 года. Вот некоторые тезисы:
- Большинство PBGA-корпусов обеспечивают достаточную надёжность для миссий с ограниченными перепадами температур (например, контролируемая температура в корпусе модуля). При большой длительности миссии корпуса с большим количеством выводов (более 500) должны подвергаться испытаниям.
- Керамические BGA-корпуса с небольшим количеством выводов (менее 400) могут удовлетворять требованиям надёжности для краткосрочных миссий с ограниченными перепадами температур, но для долгосрочных миссий должны проходить квалификационные испытания даже в случае пониженных требований к перепаду температур. Для корпусов с большим количеством выводов (более 500) необходимы испытания во всех случаях.
- Использование компаунда типа «underfill» не рекомендуется для CCGA из-за высокого зазора между корпусом и печатной платой. В случае же использования, КТР компаунда должен быть близким к КТР печатной платы (нагрузки в плоскости) и выводов (нагрузки в направлении оси Z), кроме того необходимы индивидуальные испытания для каждого случая применения.
- В случае необходимости повышения устойчивости к механическим воздействиям фиксация по углам (англ. corner staking, edge bonding) более предпочтительна для CCGA- и CBGA-корпусов по сравнению с технологией «underfill». Однако и тут можно ухудшить надёжность неправильно подобранными материалами.

Важно понимать, что дело не в технологии корпусирования в общем, а в том, соответствует ли конкретная микросхема требованиям надёжности и стойкости к воздействующим факторам.Запрос на снижение массы космических аппаратов (прежде всего, развитие малоразмерных КА) толкает производителей выпускать надёжные ЭКБ в пластиковых корпусов, на рынке уже есть решения (кроме того, они заявляются и как бюджетные).Можно использовать и коммерческую микросхему в пластиковом корпусе, если она пройдёт полный цикл испытаний. При этом успешные испытания не будут означать, что «такая же» микросхема с другого завода-изготовителя или даже из другой партии будет удовлетворять требованиям надёжности. В этом отличие надёжной ЭКБ, которое и заложено в цене — изготовитель берёт на себя затраты на испытания. Тот же 3D PLUS проводит отбор микросхем в пластике для некоторых своих микросборок, но стоят такие изделия уже на порядок дороже. Другой путь — это выполнение испытаний и отбора на стороне потребителя. Это может быть оправдано, если нужная функциональность не реализована в надёжном исполнении, или если если модель внешних воздействий и требования надёжности для целевой миссии значительно ниже, чем типовые на рынке надёжной ЭКБ.
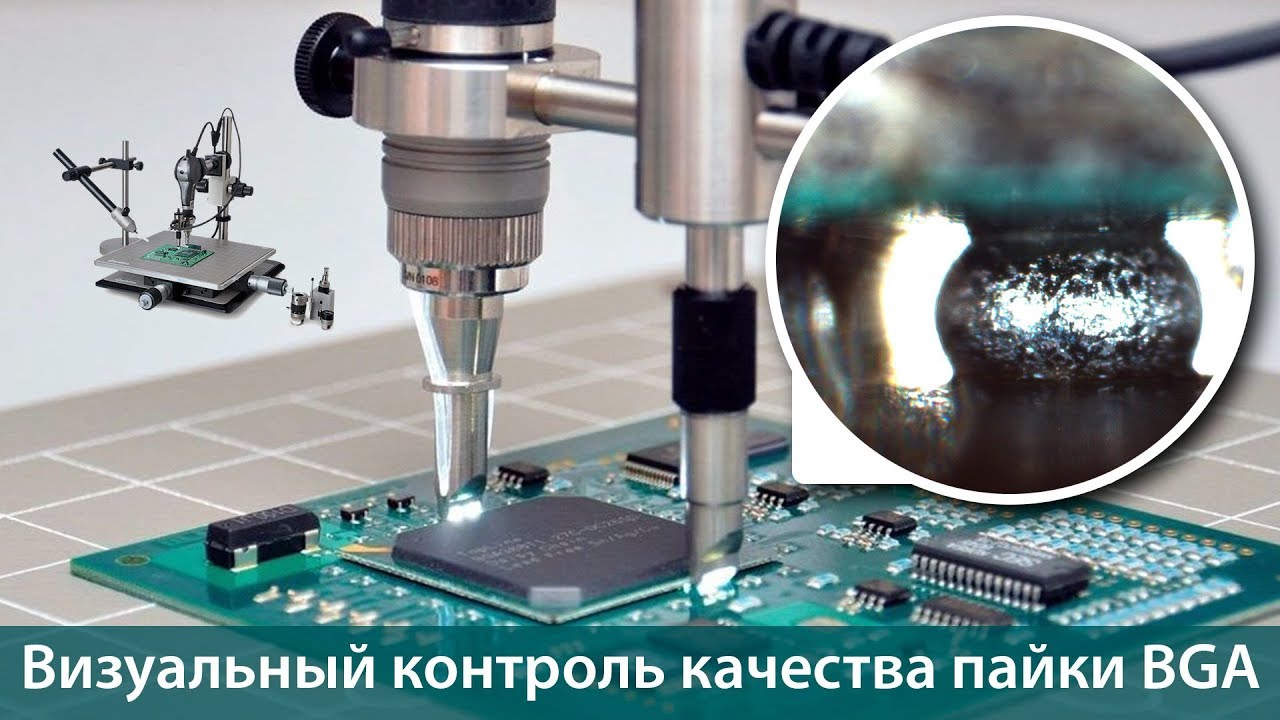
Литература
[1] Reza Ghaffarian, “BGAs for High Reliability Applications”, 1998.[2] Reza Ghaffarian, “Ball Grid Array Reliability Assessment for Aerospace Applications”, 1997
[3] Reza Ghaffarian, “Reliability and Failure Analyses of Thermally Cycled Ball Grid Array Assemblies”, 1998
[4] Reza Ghaffarian, “Reliability of BGA Packages for Highly Reliable Applications and Chip Scale Package Board Level Reliability”, 1997
[5] Reza Ghaffarian, “Assembly Reliability Of BGAs And Effects Of Boards Finish”, 1998
[6] Jean-Paul Clech, ”Solder Joint Reliability Of CSP Versus BGA Assemblies”, 2000
[7] Raj N.Master, Gregory B. Martin, etc. “Ceramic Ball Grid Array for AMD K6 Microprocessors Applications”, 1998
[8] Reza Ghaffarian, “Effect of Area Array Package Types on Assembly Reliability And Comments on IPC-9701A”, 2005
[9] Reza Ghaffarian, “CCGA packages for space applications», 2006
[10] F.
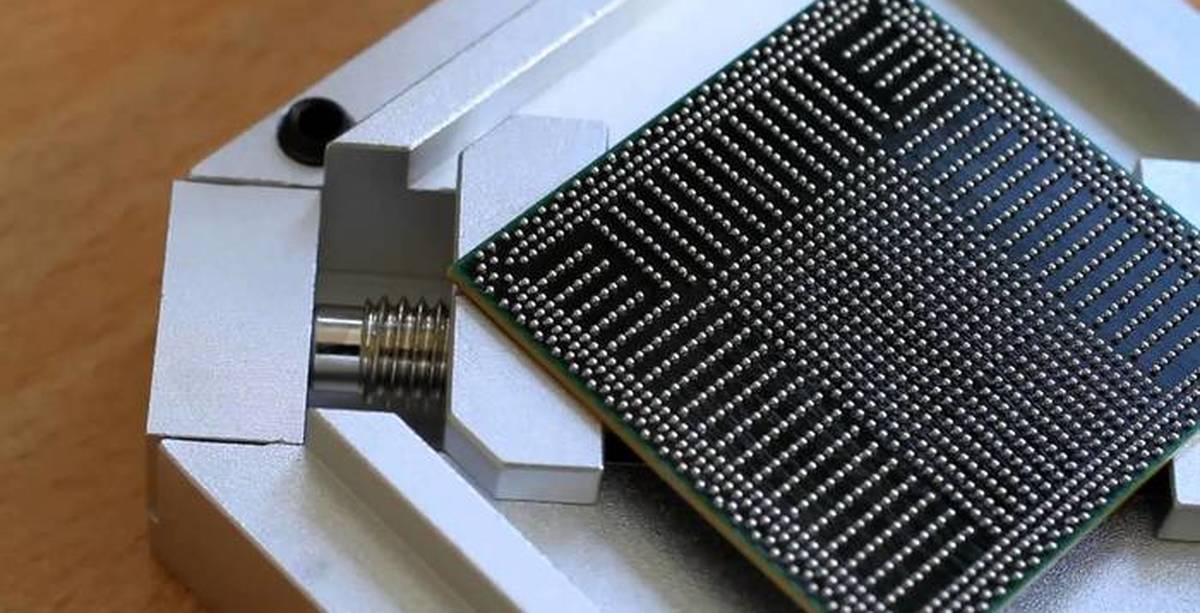
[11] F.D.Bruce Houghton. “Solving the ENIG Black Pad Problem: An ITRI Report on Round 2”, 1999
Пайка и ремонт BGA | Как припаять шариковую решетку (BGA SMD)
Руководство по пайке и ремонту BGA и учебное пособие.
Пайка и ремонт массива шариковых решеток BGA отличается от пайки и демонтажа SMD и является сложной задачей.
Электронные устройства и гаджеты с каждым днем становятся все меньше и тоньше. Все это возможно благодаря техническому прогрессу и развитию электроники. Ведущие электронные компании мира соревнуются в создании самых маленьких и тонких гаджетов.
SMD или устройства для поверхностного монтажа и BGA или матрица Ball Grid — это два электронных компонента, благодаря которым электронные устройства, гаджеты и мобильные телефоны становятся меньше и тоньше.
Что такое BGA (Ball Grid Array) и зачем нужен BGA? BGA или Ball Grid Array — это один из типов упаковки для технологии поверхностного монтажа (когда электронные компоненты SMD фактически монтируются или прикрепляются к поверхности печатной платы SMT). Корпус BGA не имеет выводов или контактов. Массив шариковых сеток получил свое название потому, что представляет собой массив шариков из металлического сплава, расположенных в виде сетки. Эти шарики BGA обычно изготовлены из олова/свинца ( Sn/Pb 63/37 ) или олово/серебро/медь (без свинца).
Печатная плата или печатная плата в современных электронных устройствах и гаджетах плотно заполнена электронными компонентами. Размер печатной платы будет увеличиваться с увеличением количества электронных компонентов. Чтобы уменьшить размер печатной платы, используются SMD и BGA-корпуса, поскольку как SMD, так и BGA меньше и тоньше по размеру и занимают очень мало места на печатной плате.
Компоненты BGA обеспечивают лучшее решение для многих типов печатных плат, но при пайке компонентов BGA требуется осторожность, чтобы гарантировать правильность и надежность процесса пайки BGA.
BGA предлагает следующие преимущества по сравнению с компонентами SMD:
- Улучшенная конструкция печатной платы в результате меньшей плотности дорожек.
- Прочный корпус BGA.
- Пониженное тепловое сопротивление.
- Улучшена производительность и возможности подключения.
На начальных этапах технология BGA вызывала озабоченность. У людей были сомнения в паяемости и надежности компонентов BGA. В BGA контактные площадки находятся под устройством и не видны, поэтому необходимо обеспечить правильный процесс пайки и проверки.
Сегодня методы пайки BGA проверены и протестированы, а их надежность подтверждена доверием. Также стало известно, что после правильной настройки процесса надежность пайки BGA намного выше, чем у четырехъядерных плоских корпусов (9).0015 QFP ) или любой другой пакет SMD.
Пайка оплавлением BGA
Метод пайки оплавлением обычно используется для пайки BGA, поскольку он помогает довести всю сборку печатной платы до фиксированной температуры, чтобы расплавить припой или шарики припоя под компонентами BGA.
Для любой пайки BGA шарики припоя на упаковке содержат контролируемое количество припоя. Доступны шарики припоя различных размеров: 18 мил, 24 мил, 30 мил, и т. д. Когда плата с шариками припоя и корпусом BGA помещается в печь оплавления, она нагревается и припой плавится. Поверхностное натяжение заставляет расплавленный припой удерживать корпус в правильном положении относительно печатной платы. Важно позаботиться о составе припоя и температуре пайки, чтобы припой не расплавился полностью, а оставался полутвердым, чтобы шарики припоя оставались отдельными друг от друга и не образовывали перемычек.
BGA Package
Проверка паяного соединения BGA Проверка BGA и поверхностного монтажа — одна из самых сложных работ. Становится чрезвычайно трудно осматривать соединения BGA, так как припой находится под корпусом BGA и не виден. Единственным удовлетворительным средством проверки паяных соединений BGA является рентгеновское излучение. Рентгеновский снимок помогает увидеть стыки под упаковкой и, таким образом, помогает при осмотре.
Переделка и ручная пайка корпусов BGA — самая сложная часть. Для работы нужна практика. Давайте разберемся Отпайка и пайка корпусов BGA вручную
Отпайка BGA вручнуюНаиболее распространенная практика отпайки BGA — горячий воздух. Вот шаги по отпайке корпуса BGA с помощью горячего воздуха:
- Нанесите жидкий флюс на боковые стороны корпуса.
- Предварительно нагрейте упаковку сверху и снизу. Тепло может подаваться снизу с помощью предварительного нагревателя, а тепло сверху может подаваться с помощью системы ремонта горячим воздухом. Здесь можно использовать ремонтную систему Goot Hot Air SMD / BGA.
- Теперь, используя правильное сопло BGA, нагрейте корпус BGA.
- Шарики припоя под корпусом BGA расплавятся.
Возьмите пакет с помощью пинцета ИЛИ с помощью вакуумного захвата.
Опять же, наиболее распространенной практикой пайки BGA является пайка горячим воздухом. Вот шаги для пайки корпуса BGA с помощью горячего воздуха:
После извлечения корпуса BGA очистите контактную площадку и удалите лишний припой с платы.
- Нанесите Flux Paste ( Not Liquid Flux ) на подушку. Паста-флюс поможет приклеить шарики припоя, чтобы они не падали и не меняли положение.
- Очень осторожно поместите шарики припоя на контактную площадку.
- Нанесите пастообразный флюс на дно ( сторона пайки ) корпуса BGA.
- Аккуратно поместите корпус BGA на шарики припоя.
- Предварительно нагрейте, а затем подайте горячий воздух с помощью нагнетателя горячего воздуха сверху и снизу.
- Шарики припоя расплавятся и спаются.
Технология BGA и пайка BGA очень надежны, если они выполняются с использованием правильной процедуры. BGA имеет меньшую устойчивость к нагреву и, следовательно, меньше или совсем не повреждается из-за перегрева.
Видео: Как восстановить BGA IC
Похожие сообщения:
- Методы пайки и сборки печатных плат SMT
- Электронные компоненты, детали и их функции
- Паяльная паста и ее применение в поверхностном монтаже
- Как работает полупроводник
- Руководство по ограничению использования опасных веществ в электронике: RoHS, WEEE и часто задаваемые вопросы о бессвинцовой продукции
- Печатная плата и печатная плата — в чем разница
- Машины и инструменты для сборки печатных плат
- Лучшая машина для селективной пайки и процесс селективной пайки
- Машины для поверхностного монтажа и производители машин для поверхностного монтажа
7 типов корпусов BGA (Ball Grid Array)
Когда речь идет о чрезвычайно чувствительных компонентах компьютера. Понятно, что соединение интегральных схем с помощью проводов затруднено, когда речь идет о поверхностных компонентах. Лучшим решением для этого является массив шариковых сеток. Эти BGA можно легко идентифицировать в нижней части микропроцессоров. Поскольку он напрямую соединяет клеммы, BGA широко используется при разработке компьютерных компонентов и других высокопроизводительных вычислительных машин. BGA использует всю площадь всего компонента, предоставляя больше места для соединений и хорошей связи.
Введение в BGA
Что такое массив шариковых решеток?
BGA — это аббревиатура от Ball Grid Array. В общем, это набор маленьких, крошечных металлических шариков-проводников, которые гармонично размещаются на плате по мере того, как мы движемся к созданию печатной платы (PCB).
Массив с шариковой решеткой, или BGA, имеет другую стратегию подключения, чем типичные разъемы для поверхностного монтажа. В другой упаковке, такой как четырехъярусная плоская упаковка (QFP), разъемы расположены по бокам упаковки. Это означало, что для контактов было мало места, которые должны были быть расположены близко друг к другу и значительно уменьшены, чтобы обеспечить необходимое количество связи. BGA использует нижнюю часть упаковки, где достаточно места для соединений.
Причина использования BGA
Массив шариковых решеток набирает популярность среди ИС SMD, требующих плотных соединений. Использование нижней части корпуса ИС вместо соединений по краям позволяет снизить плотность соединений и, следовательно, упростить компоновку печатной платы.
Использование нижней части микросхемы препятствует прямому доступу к соединениям, что усложняет пайку, отпайку и проверку. Однако с помощью основного оборудования для производства печатных плат эти проблемы легко преодолеваются, а общая надежность и производительность могут повышаться.
Где его можно идентифицировать?
Превосходные характеристики рассеивания тепла BGA обеспечивают охлаждение ядра во время работы, что продлевает срок службы изделия. Тепло является наиболее важным фактором, который следует учитывать, и BGA является причиной того, что технологические товары работают так эффективно, поддерживая нормальную температуру даже при работе на полную мощность.
Вторым по важности фактором являются электрические характеристики. Соединения с наименьшими расстояниями и минимально допустимыми резистивными путями повышают ценность и важность BGA.
Третий по важности фактор — совместимость. Возможность использовать кратчайшее пространство при работе с большим количеством мячей позволяет производителю включать все большее количество рабочих вариантов. Таким образом, повышается ценность и желательность продукта.
Различные типы BGA-компонентов
BGA-компоненты — это основа изделий, которые вы хотите производить. Это зависит не только от того, какую продукцию вы хотите производить. А также на общую стоимость производства, вес конечного продукта, качество продукта, количество выделяемого тепла и множество других факторов.
Керамический BGA (CBGA)
Это керамический тип BGA. В этом типе соотношение между оловом и свинцом составляет 10:90. Этот тип BGA требует подхода C4 (Контролируемое сжатие чипа) для построения моста между BGA и печатными платами. Это связано с его чрезвычайно высокой температурой плавления. Этот тип BGA дороже, чем PBGA, но он невероятно надежен благодаря улучшенным электрическим характеристикам и теплопроводности.
Пластиковый ламинат BGA (PBGA)
Аббревиатура от Plastic Ball Grid Array — PBGA. Это наиболее распространенный тип двухсторонних печатных плат, используемых в настоящее время. Компании MOTOROLA приписывают ее новаторство, хотя в настоящее время ее используют практически все производители. В качестве материала подложки сердцевину образует бисмалеимид-триазиновая (БТ) смола. Это, вместе с применением технологии герметика формованного носителя массива прокладок (OMPAC) или держателя массива прокладок (GTPAC), подтверждено JEDEC как высоконадежное (уровень 3). Эти BGA содержат от 200 до 500 массивов шариков.
Лента BGA
Единственным недостатком TBGA является то, что она всегда дороже, чем PBGA. Тем не менее, TBGA — лучший выбор для тонких изделий. Для этого требуются прочные материалы сердечника, превосходное рассеивание тепла и превосходное электрическое соединение. Независимо от того, должны ли микросхемы / микросхемы быть обращены вверх или вниз, это стратегия максимизации ценности продукта при минимизации затрат. В этой форме BGA обычно предпочтительнее соединение проводами, если микросхемы обращены вверх, но метод перевернутой микросхемы кажется подходящим, если микросхемы обращены вниз.
Типы корпусов PoP
Пакет на корпусе (PoP) — это подход к компоновке интегральных схем, который сочетает в себе вертикально дискретную логику и блоки памяти BGA. Стекирование означает установку двух или более пакетов друг над другом со стандартным интерфейсом для передачи сигналов между ними.
Технология PoP предназначена для удовлетворения постоянных потребностей электронной промышленности в отношении малого шага, меньшего размера, высокой скорости обработки сигнала и меньшего монтажного пространства в электронных продуктах, таких как смартфоны и цифровые камеры. Используя этот метод в процессе сборки печатной платы, устройства памяти в верхнем корпусе и логические устройства в нижнем корпусе электрически соединяются, проверяются и заменяются по отдельности. Все эти качества снижают стоимость и сложность конструкции печатной платы.
Типы корпусов LGA
Массив Land Grid, или LGA, представляет собой корпус, в котором используются металлические площадки вместо выводов (как в массиве штыревой сетки) или шарики припоя для внешнего электрического соединения (как в массиве шариковой сетки). Эти металлические площадки, известные как «площадки», обычно организованы в виде сетки или массива в основании упаковки, отсюда и название «решетка площадок». Сетчатый дизайн площадок корпуса LGA позволяет иметь большое количество площадок, что делает его распространенным вариантом упаковки для устройств с обширными потребностями ввода-вывода.
Количество земель для типичных LGA варьируется от 8 до 1681. LGA с наименьшим количеством земель по сути являются QFN, поскольку земли этих пакетов ограничены периферией тела. Типичные значения шага контактных площадок LGA (расстояние между контактными площадками) варьируются от 1,0 мм до 1,27 мм .
Тип корпуса QFN
Соединение ASCIC с печатной платой представляет собой полупроводниковый корпус QFN. Более того, это достигается с помощью технологии поверхностного монтажа. Кроме того, QFN представляет собой упаковку с выводным каркасом, известную как Chip Scale Package (CSP). И это связано с тем, что он позволяет вам наблюдать и связываться с лидами после сборки. Как правило, соединение с печатной платой и сборка кристалла корпусов QFN, как правило, состоят из медного выводного каркаса. Кроме того, этот пакет может иметь один или несколько рядов контактов.
Упаковка QFN имеет штамп, обернутый выводной рамкой. Выводная рамка состоит из медного сплава с матовым оловянным покрытием.
Проволочное соединение обычно используется для соединения матрицы и рамы. Медь/золото обычно предпочтительнее для соединения проводов. Некоторые производители реализуют этот интерфейс, используя технологию флип-чипа. Метод флип-чипа обеспечивает превосходные электрические характеристики по сравнению с традиционным методом.
На нижней стороне устройства находятся металлические клеммные колодки. Вдоль четырех краев нижней поверхности эти клеммные колодки обеспечивают электрическое подключение к печатной плате.
На дне упаковки открыта прокладка. Эта площадка обеспечивает теплопроводящий канал к печатной плате. Открытая площадка также позволяет выполнить заземление. На открытой площадке корпус QFN припаивается к печатной плате. Прикрепление штампа относится к эпоксидной смоле, используемой для крепления штампа к открытой площадке.
Flip-Chip
Аналогичен CBGA, за исключением керамической подложки. Вместо этого в этом FC-BGA используется смола BT. Таким образом, дополнительные расходы для этого типа минимизируются. Основное преимущество заключается в более коротких электрических путях по сравнению с другими разновидностями BGA, что приводит к превосходной электропроводности и повышенной скорости работы. Соотношение олова и свинца в этом типе BGA составляет 63:37. Чипы, используемые на подложке, можно легко переставить в нужное место без использования машины для выравнивания с переворотом, что является еще одним преимуществом этого типа BGA.
Преимущества BGA
Массив шариковых решеток изначально создавался для предоставления ряда преимуществ производителям интегральных схем и оборудования, а также пользователям оборудования. Среди преимуществ BGA по сравнению с другими технологиями можно выделить следующие:
- Эффективное использование пространства на печатной плате, позволяющее выполнять соединения под корпусом SMD, а не только по его периметру.
- Улучшения тепловых и электрических характеристик. Корпуса BGA могут обеспечивать плоскости питания и заземления с низкой индуктивностью, дорожки с регулируемым импедансом для трасс сигналов, а также возможность отводить тепло через контактные площадки и т. д.
- Повышение производительности за счет улучшенной пайки.
BGA обеспечивают более широкое разделение соединений и улучшенную способность к пайке.
- Уменьшенная толщина упаковки, что является преимуществом, когда составные части, такие как мобильные телефоны, делаются только значительно тоньше; Улучшенная возможность повторной обработки благодаря большим размерам колодок и т. д.
Final Word
Существует множество причин, по которым современная технология в значительной степени зависит от BGA. Наиболее важным является то, что BGA обеспечивает превосходное рассеивание тепла. Это позволяет ядру оставаться прохладным во время работы и, таким образом, продлевает срок службы продукта. Тепло является наиболее важным фактором, который следует учитывать, и BGA является причиной того, что технологические товары работают так эффективно, поддерживая нормальную температуру даже при работе на полную мощность.
Вторым по важности фактором являются электрические характеристики. Соединения с наименьшими расстояниями и минимально допустимыми резистивными путями повышают ценность и важность BGA.